ДСЕ — это… Что такое ДСЕ?
ДСЕ — детали и сборочные единицы; детале сборочная единица ДСЕ ДСК дворец спортивных единоборств спорт ДСЕ ДСЕ ЦСКА Источник: http://www.cska.ru/index.php?option=com content&task=view&id=16&Itemid=34 ДСК Источник: http://www.cska.ru/index.php?part=5 … Словарь сокращений и аббревиатур
ГОСТ Р 53374-2009: Двигатели ракетные жидкостные. Общие требования к изготовлению и контролю качества при поставках в эксплуатацию — Терминология ГОСТ Р 53374 2009: Двигатели ракетные жидкостные. Общие требования к изготовлению и контролю качества при поставках в эксплуатацию оригинал документа: 3.1.2 гарантийный срок: Общая календарная продолжительность хранения и… … Словарь-справочник терминов нормативно-технической документации
ДСК — Демократический союз Косово Косово Источник: http://lenta.ru/world/2004/10/24/rugova/ ДСК дачно строительный кооператив Словарь: С. Фадеев. Словарь сокращений современного русского языка. С. Пб.: Политехника, 1997. 527 с. ДСК Дом студента на… … Словарь сокращений и аббревиатур
СЕНЕГАЛ — Республика Сенегал, гос во на 3. Африки. Совр. название гос ва Сенегал и одноименной с ним реки, протекающей по его сев. границе, по видимому, восходят к названию королевства Сангана, которое упоминается араб, географом XI в. Аль Бакри. В основе… … Географическая энциклопедия
срок — 3.1 срок службы: Расчетное время работы труб при заданных параметрах эксплуатации трубопровода. Источник: ГОСТ Р 54468 2 … Словарь-справочник терминов нормативно-технической документации
срок годности — (expiry date or expiration date): Дата, указываемая на упаковке/этикетке АФС, обозначающая период времени, в течение которого гарантируется сохранение свойств АФС в рамках установленных спецификаций при хранении в определенных условиях и после… … Словарь-справочник терминов нормативно-технической документации
Андраник Маркарян — Андраник Нахапетович Маркарян родился 12 июня 1951 года в Ереване в семье учителя. С 14 ти лет занимался политической деятельностью. В 1968 году вступил в подпольную Национальную Объединенную партию. В 1972 году окончил факультет технической… … Энциклопедия ньюсмейкеров
Саркисян, Арам Завенович — Арам Завенович Саргсян арм. Արամ Զավէնի Սարգսյան Армянский политик Дата рождения: 2 января 1961(1961 01 02) (51 год) … Википедия
СГСЭУ — Саратовский государственный социально экономический университет (СГСЭУ) Год основания 1916 Ректор В.А. Динес … Википедия
Саркисян А. — Арам Завенович Саркисян арм. Արամ Զավէնի Սարգսյան Армянский политик Дата рождения: 2 января 1961 Место рождения: Арарат, Армянская ССР Арам Завенович Саркисян (арм … Википедия
Саркисян А. З. — Арам Завенович Саркисян арм. Արամ Զավէնի Սարգսյան Армянский политик Дата рождения: 2 января 1961 Место рождения: Арарат, Армянская ССР Арам Завенович Саркисян (арм … Википедия
universal_en_ru.academic.ru
ДСЕ — это… Что такое ДСЕ?
ДСЕ — детали и сборочные единицы; детале сборочная единица ДСЕ ДСК дворец спортивных единоборств спорт ДСЕ ДСЕ ЦСКА Источник: http://www.cska.ru/index.php?option=com content&task=view&id=16&Itemid=34 ДСК Источник: http://www.cska.ru/index.php?part=5 … Словарь сокращений и аббревиатур
ГОСТ Р 53374-2009: Двигатели ракетные жидкостные. Общие требования к изготовлению и контролю качества при поставках в эксплуатацию — Терминология ГОСТ Р 53374 2009: Двигатели ракетные жидкостные. Общие требования к изготовлению и контролю качества при поставках в эксплуатацию оригинал документа: 3.1.2 гарантийный срок: Общая календарная продолжительность хранения и… … Словарь-справочник терминов нормативно-технической документации
ДСК — Демократический союз Косово Косово Источник: http://lenta.ru/world/2004/10/24/rugova/ ДСК дачно строительный кооператив Словарь: С. Фадеев. Словарь сокращений современного русского языка. С. Пб.: Политехника, 1997. 527 с. ДСК Дом студента на… … Словарь сокращений и аббревиатур
СЕНЕГАЛ — Республика Сенегал, гос во на 3. Африки. Совр. название гос ва Сенегал и одноименной с ним реки, протекающей по его сев. границе, по видимому, восходят к названию королевства Сангана, которое упоминается араб, географом XI в. Аль Бакри. В основе… … Географическая энциклопедия
срок — 3.1 срок службы: Расчетное время работы труб при заданных параметрах эксплуатации трубопровода. Источник: ГОСТ Р 54468 2 … Словарь-справочник терминов нормативно-технической документации
срок годности — (expiry date or expiration date): Дата, указываемая на упаковке/этикетке АФС, обозначающая период времени, в течение которого гарантируется сохранение свойств АФС в рамках установленных спецификаций при хранении в определенных условиях и после… … Словарь-справочник терминов нормативно-технической документации
Андраник Маркарян — Андраник Нахапетович Маркарян родился 12 июня 1951 года в Ереване в семье учителя. С 14 ти лет занимался политической деятельностью. В 1968 году вступил в подпольную Национальную Объединенную партию. В 1972 году окончил факультет технической… … Энциклопедия ньюсмейкеров
Саркисян, Арам Завенович — Арам Завенович Саргсян арм. Արամ Զավէնի Սարգսյան Армянский политик Дата рождения: 2 января 1961(1961 01 02) (51 год) … Википедия
СГСЭУ — Саратовский государственный социально экономический университет (СГСЭУ) Год основания 1916 Ректор В.А. Динес … Википедия
Саркисян А. — Арам Завенович Саркисян арм. Արամ Զավէնի Սարգսյան Армянский политик Дата рождения: 2 января 1961 Место рождения: Арарат, Армянская ССР Арам Завенович Саркисян (арм … Википедия
Саркисян А. З. — Арам Завенович Саркисян арм. Արամ Զավէնի Սարգսյան Армянский политик Дата рождения: 2 января 1961 Место рождения: Арарат, Армянская ССР Арам Завенович Саркисян (арм … Википедия
universal_ru_en.academic.ru
Планирование производства
Подготовка производства
Техническая подготовка производства нацелена на формирование нормативной базы производственного предприятия, включающей описание продукции, техпроцессов и требуемых для производства ресурсов.
Подготовка производства делится на конструкторскую и технологическую и включает:
- проектирование новых и совершенствование конструкций ранее выпускаемых изделий, обеспечение их производства техническими условиями, чертежами, спецификациями и прочей конструкторской документацией;
- разработку новых и улучшение действующих технологических процессов, обеспечение производства технологической документацией;
- разработку прогрессивных технических нормативов трудоемкости обработки, норм расхода материалов и инструмента.
Для повышения эффективности работы с информационной системой специалистов предприятия в ней организованы специализированные режимы «Рабочее место конструктора», «Рабочее место технолога» и «Рабочее место нормировщика ПТН».
Конструкторская подготовка производства
Конструкторская подготовка производства в системе Олимп включает в себя формирование полного списка изготавливаемых на предприятии деталей и сборочных единиц (ДСЕ). О каждой ДСЕ указывается основная информация, необходимая для нормирования ресурсов, планирования и учета производства.
В рамках конструкторской подготовки производства вносится информация о составах сборочных единиц и допустимых заменах в составах.
Технологическая подготовка производства
Технологическая подготовка заключается в указании для каждой ДСЕ последовательности операций процесса производства и объема требуемых ресурсов. Последовательность операций с информацией о цехе и участке описывает маршрут изготовления. Для операции может быть указано основное и дополнительное оборудование, инструмент и вспомогательные материалы.
Для того, чтобы учесть все существующие на предприятии варианты организации производственного процесса, присутствует возможность кроме основного указать альтернативные технологические процессы.
Для деталей и заготовок технолог в процессе подготовки производства указывает используемый материал и его норму расхода. Могут быть указаны допустимые варианты замены основного материала.
Нормирование труда
Помимо материальных ресурсов для производства необходимо оборудование и рабочие. Нормирование этих ресурсов осуществляется путем задания времени выполнения технологической операции.
Кроме нормы времени указывается информация, необходимая для проведения сводных расчетов требуемой численности рабочих и производственных мощностей.
Расчеты и анализ
На основе конструкторских и технологических данных можно получать различные аналитические отчеты. Отчеты можно разделить на три направления: анализ требуемых ресурсов, анализ структуры производства и оптимизация подготовки производства.
Анализ требуемых ресурсов можно вести отдельно по их видам на одно изделие (узел) либо на произвольный список ДСЕ. Среди таких отчетов: «Ведомость материальных затрат», «Ведомость трудоемкости и расценок». Аналитический режим «Калькуляция цены» позволяет проводить сводный анализ всех требуемых ресурсов, в том числе в стоимостном выражении.
Для анализа структуры производства можно использовать аналитические режимы: «Спецификация — расцеховка», «Применяемость операций ТП».
Техническая подготовка производства обеспечивает актуальной нормативной информацией все процессы планирования и учета хода производства. Полнота информации о ДСЕ, большое количество специализированных аналитических отчетов способствует совершенствованию подготовки производства и его унификации.
www.olimp.udm.ru
Диспетчеризация производства: нюансы автоматизации | Директор информационной службы
В проектах внедрения автоматизированной системы управления производством сначала необходимо запустить подсистему производственного учета с решением задач диспетчеризации — централизованного оперативного контроля и координации управления производственными процессами, а затем — производственное планирование. Какие при этом необходимо учесть нюансы?
Современное машиностроительное или приборостроительное производство — сложная система, требующая централизованного управления. Производственные корпуса, инженерное оборудование и технологические линии нужно выстроить во взаимодействующие подсистемы — ими нужно эффективно управлять.
Как показывает практика, автоматизация диспетчеризации способна многократно увеличить отдачу от специалистов, занятых учетом производства и планированием. Работа диспетчера приобретает интеллектуальный характер — основной акцент в ней смещается c рутинных методов поиска и обработки фактической информации о выполненных работах к анализу текущей производственной ситуации и предупреждению нежелательных явлений, таких как простои и задержки выполнения заказов (см. рис. 1).
![]() |
Рисунок 1 |
Диспетчеризация как процесс управления
Представим себе новенький завод из восьми — двенадцати цехов, с современным оборудованием и с подготовленным персоналом. В административный корпус стоит очередь из заказчиков, в архиве лежит полный комплект документации на изделия с инновационными технологиями производства. Что дальше?
А дальше нужно:
1. Принять заказы, оценивая возможности их выполнения по срокам.
2. Спланировать закупки комплектующих и материалов.
3. Сформировать планы производства, которые могут быть многоуровневыми (предприятие, цех, участок, рабочий центр) и обязаны быть взаимосвязанными.
4. Спланировать мероприятия, обеспечивающие выполнение планов в условиях существующих ограничений (организация сверхурочных или сменных работ, передача работ субподрядчикам, оптимизация мощностей и запасов).
5. Оценить выполнение плановых заданий на каждом из уровней и выработать корректирующие решения.
Вроде бы классический пример цикла Деминга — Шухарта («планируй — делай — проверяй — улучшай»). Однако применительно к управлению производством он может оказаться не таким уж простым.
Спланировать работу предприятия в целом, его служб и цехов на основе имеющихся данных об изделиях и технологиях — задача сама по себе непростая, особенно если учитывать ограничения и тем более на нижних уровнях (выполнение технологических операций). При отсутствии автоматизации централизованное планирование на предприятии обычно ограничивается подготовкой плана по выпуску готовой продукции и укрупненными графиками изготовления изделий с длинным производственным циклом. Реже централизованно формируются планы для цехов, иногда укрупненные до узлов или планово-учетных единиц. Более детальные планы для цехов при ручном планировании формируются непосредственно в цехах и на участках. При этом цеховые планы труднее синхронизировать между собой — ведь у них разные авторы. Получается довольно сложная и «медленная» система планирования. Но самое главное — сформированный сегодня план уже завтра становится неактуальным: часть его должна быть выполнена, другая часть — откорректирована. А собрать фактические сведения по выполнению планов — дело еще более сложное, ведь нужно за относительно короткий срок собрать большой объем сведений, чтобы данные учета были актуальны.
К счастью, ручные планирование и учет производства уступают место, пусть пока и неохотно, автоматизированным системам управления производством. При этом функция планирования сама по себе представляется организационно более простой, так как основывается на статичных описаниях изделий (структура, техпроцесс) и производственной среды (структура предприятия, описание и графики работы рабочих центров, справочники). Для диспетчеризации необходимо предусмотреть и механизмы сбора постоянно меняющихся данных, и их верификацию.
При рассмотрении функций планирования и диспетчеризации производства между ними можно увидеть связь: для планирования нужны данные о текущем состоянии производства. Без обратной связи, информирующей о ходе выполнения работ, планирование теряет актуальность и перестает быть ценным. Именно поэтому в проектах внедрения автоматизированной системы управления производством сначала необходимо запустить подсистему производственного учета с решением задач диспетчеризации, а затем — производственное планирование.
![]() |
Рисунок 2 |
Уровни и задачи диспетчеризации
Для предприятия с делением на цеха (или производства) характерна двух- или трехуровневая система диспетчеризации.
1. Уровень центральной службы управления производством (обычно планово-диспетчерского отдела) — основными задачами диспетчеризации здесь чаще всего являются контроль выполнения планов предприятия и графиков изготовления изделий (заказов), планов цехов, оценка степени готовности изделия или заказа (например, по трудоемкости) и оценка запасов деталей и сборочных единиц (ДСЕ), а также полуфабрикатов.
2. Цеховой уровень управления производством (планово-диспетчерское бюро) — здесь контролируют выполнение плана цеха и обеспечивающих его планов участков (если составляются).
3. Управление производством на уровне участка — начальник участка или мастер осуществляет пооперационный контроль выполнения работ.
При этом автоматизированная система управления производством должна обеспечивать доступность сведений нижестоящих уровней диспетчеризации на всех вышестоящих уровнях. Например, у начальника планово-диспетчерского отдела должна быть возможность самостоятельно контролировать выполнение и планов участков (если составляются), и отдельных технологических операций для партий ДСЕ.
На практике не всегда применяют наиболее детальный пооперационный учет изготовления ДСЕ в автоматизированных системах. Это связано, во-первых, с потребностями рассматриваемого уровня диспетчеризации. Например, для уровня планово-диспетчерского отдела объектами учета могут выступать только заказы, партии заказов (изделия), крупные узлы из графиков изготовления изделий и партии ДСЕ. Этого вполне достаточно для оценки выполнения основного производственного плана, графиков изготовления изделий и номенклатурных планов цехов. При этом прохождение партий ДСЕ по цехам и участкам и выполнение отдельных технологических операций в цехах может не рассматриваться — как избыточная информация.
Во-вторых, в автоматизированную систему могут быть переданы упрощенные сведения об изделии или производственной среде, что не позволяет опуститься ниже определенного уровня объектов учета при диспетчеризации производства. Например, технологические операции в автоматизированных системах могут быть описаны упрощенно: «мехобработка» вместо фактически выполняемых операций «токарная», «фрезерная», «сверлильная». Или в расцеховочном маршруте могут быть не указаны некоторые цеха или цехозаходы, в справочнике подразделений могут отсутствовать участки или склады. Подобные упрощения часто используются сознательно — для снижения общих затрат на учет и на описание моделей изделий и предприятия, если более детальный учет вести нецелесообразно. В некоторых случаях потребность в точном пооперационном учете может существовать, но при этом ресурсов для быстрого ввода большого количества данных оказывается недостаточно, поэтому детализация диспетчеризации производится поэтапно, в соответствии с графиком проекта внедрения автоматизированной системы управления производством. При этом сама автоматизированная система должна поддерживать возможность использовать различные уровни детализации учета, не теряя работоспособности.
Актуальность данных при диспетчеризации
Одним из важнейших условий успешного использования автоматизированной системы управления производством для целей диспетчеризации является обеспечение актуальности поступающих данных. При «простой» автоматизации учета, когда пользователи обязаны «прямолинейно» вводить данные (например, о выполненных операциях или изготовленных ДСЕ) в систему автоматизации, увеличивается вероятность получения неактуальных сведений. Это происходит по разным причинам: невнимательность и ошибки, нарушение периодичности ввода данных, невнесение отклонений фактических сведений от плановых и пр. При автоматизации производственного учета важно максимально предотвратить появление подобных ситуаций.
Наиболее действенным способом повышения актуальности данных диспетчеризации являются встраивание процедур ввода данных о ходе производства в естественные процессы работы сотрудников и обеспечение сквозной прослеживаемости объектов учета в производстве.
Прослеживаемость объектов учета должны обеспечить сопроводительные документы, модифицированные для быстрой обработки машинным способом. Это могут быть, например, дополнительно указанные коды и обозначения объектов учета из базы данных автоматизированной системы в сочетании с использованием штрихового кодирования.
Сами сопроводительные документы должны при этом появляться из системы автоматизации, а не вноситься в нее с бумажных носителей. Кроме того, они должны быть связаны между собой в соответствии с принятой на предприятии методикой учета. При выполнении перечисленных условий учетные документы будут существовать одновременно и в бумажном (где это необходимо), и в электронном виде, а их обработка будет осуществляться в автоматизированной системе и служить объективным источником данных для диспетчеризации. Диспетчеризация производства будет осуществляться автоматически на основании выполняемых пользователем действий по работе с документами. Такой подход — работа «от документа» — позволяет избежать дополнительных затрат на ведение регламентированного учета одновременно на бумаге и в информационных системах, а также сократить влияние человеческого фактора.
Цели диспетчеризации
Диспетчеризация производства может использоваться в следующих целях.
1. Учет выполненных работ с различной детализацией, учет выполнения планов и графиков. Потребителями данной информации являются производственные службы всех уровней управления и службы, заинтересованные в информации по готовности заказов.
2. Учет фактических прямых производственных затрат (материальных и трудовых), а также незавершенного производства в целях регламентированного учета.
3. Складской учет полуфабрикатов, готовых ДСЕ и готовой продукции.
Средствами диспетчеризации производства каждая из перечисленных целей может достигаться либо отдельно, либо совместно в произвольном сочетании. Однако каждая цель предъявляет свои требования к функционалу производственного учета.
Учет выполняемых работ по изготовлению партий ДСЕ требует своевременного и наиболее быстрого обновления сведений (см. рис. 2). Во главу угла ставится контроль номенклатуры выполненных работ и сроков их выполнения. Пользователям нужна информация о состоянии дел на настоящий момент для принятия своевременных и верных решений по управлению производственными процессами. И если детализация учета достигает контроля выполнения отдельных технологических операций, то время появления фактических данных в информационной системе должно исчисляться минутами. Диспетчеризация производства в этом случае предъявляет наиболее высокие требования к исполнительской дисциплине и поддержанию актуальности данных об изделиях и производственной среде в производственных спецификациях.
Учет затрат и незавершенного производства в целях регламентированного учета требует актуализации сведений на начало или конец отчетного периода. Как правило, это месяц, квартал или год. Учет затрат требует наличия в моделях предприятия и изделия лишь мест учета затрат или незавершенного производства и стоимостных оценок по переделам или условным технологическим операциям. Другими словами, в целях учета затрат и «незавершенки» вполне допустимо укрупнение объектов учета и интервалов актуализации данных, что снижает затраты на учет.
Складской учет может производиться в целях как регламентированного, так и оперативного учета — например, для комплектования сборочных единиц либо учета складских запасов при планировании производства или закупок. В обоих случаях требуется более простая модель предприятия — только места хранения (кладовые и склады). Интервал актуализации данных зависит от целей складского учета и соответствует случаям, рассмотренным выше.
При автоматизации производственного учета нельзя упускать из виду цели такого проекта. Если, помимо регламентированного учета затрат или складских запасов, диспетчеризация нужна для оперативного управления производством и планирования, то заказчик функционала и руководитель проекта должны обеспечить исполнительскую дисциплину и механизмы поддержания необходимой точности и актуальности данных. Если этого не происходит, то даже верно спроектированная и реализованная подсистема диспетчеризации может «деградировать» и превратиться в подсистему упрощенного регламентированного учета, непригодную в качестве обратной связи для планирования и принятия своевременных решений.
При решении задач диспетчеризации важно найти компромисс между необходимой точностью и своевременностью учета производства, с одной стороны, и затрачиваемыми для этого усилиями — с другой. Наиболее логичным способом представляется построение системы диспетчеризации в два или три этапа, соответствующих уровням управления производством. Сначала система охватывает учет готовых изделий (уровень предприятия), затем — учет выполненных работ по партиям ДСЕ без учета отдельных технологических операций внутри цеха или участка (уровень цехов, производств, участков), а затем — пооперационный учет (внутрицеховой уровень). На каждом этапе необходимо определить объекты учета и требуемую частоту актуализации данных, достаточную для своевременной реакции на отклонения. Каждый уровень учета должен быть независим от нижестоящего, чтобы его можно было сразу же использовать, но должен предусматривать механизмы получения результатов работы нижестоящего уровня после его внедрения.
С экономической точки зрения целесообразно совмещать достижение различных целей диспетчеризации с помощью единого модуля производственного учета системы управления производством. Правильной представляется интеграция такого модуля с системой регламентированного учета, в которую поступает консолидированная учетная информация и из которой появляются отдельные учетные сведения, например для складского учета.
? Сергей Бонакер, ведущий аналитик группы внедрения промышленных систем компании «Аскон»; [email protected]
Поделитесь материалом с коллегами и друзьями
www.osp.ru
Статья «TechnologiCS — гибкий инструмент реализации производственного учета» из журнала CADmaster №1(51) 2010 (январь-март)
Создание автоматизированной системы производственного учета — важнейшее условие обеспечения эффективного управления предприятием. Такая система, используя обоснованные, полные, достоверные и своевременно поступающие данные, должна обеспечить рачительное использование ресурсов предприятия. Особенно актуальной эта задача стала для предприятий машиностроительной сферы, для которых характерны сложность выпускаемой продукции, состоящей из многочисленных деталей и узлов, и наличие (иногда сложного) маршрута их обработки и сборки. При этом предприятия имеют разные типы производства — от единичного до крупносерийного и массового. В последнее время все отчетливее заметен процесс специализации машиностроительных предприятий — возрастает удельный вес покупных изделий и приобретаемых на стороне полуфабрикатов, что, безусловно, требует индивидуального подхода к системе учета затрат и определению себестоимости продукции.
![]() |
![]() |
В этой статье мы сделаем акцент только на производственном учете, оставив тему учета затрат и расчета себестоимости для следующих публикаций.
Основными задачами производственного учета являются:
- определение фактического объема выпускаемой продукции, ее ассортимента и качества и осуществление контроля выполнения планов по этим показателям;
- исчисление всех фактических затрат на производство, себестоимости единицы вырабатываемой продукции для определения отклонений от плановых затрат;
- выявление внутренних резервов предприятия для дальнейшего снижения материальных, трудовых и денежных затрат на единицу продукции.
Автоматизированная система -новая жизнь
Приходит человек в патентное бюро с большим ящиком:
— Я изобрел автомат для бритья!
— И как он работает? — Клиент опускает монетку, засовывает голову в отверстие и шесть лезвий начинают его брить.
— Позвольте, но ведь у каждого индивидуальное строение лица?
— Да, но это только в первый раз.
Анекдот
В статье «TechnologiCS: опыт внедрения в ЗАО «ВолгАэро» мы рассказали об особенностях использования системы TechnologiCS в ЗАО «ВолгАэро». Продолжая начатую тему, поговорим сегодня о реализации производственного учета в системе TechnologiCS на двух предприятиях, которые отличаются как производимой продукцией, так и идеологией организации производственного процесса.
Но прежде хотелось бы сказать несколько слов о внедрении как о весьма сложном и рискованном процессе. Создание информационных систем корпоративного класса, как правило, подразумевает реинжиниринг бизнес-процессов организации, то есть — без преувеличения можно сказать — революцию. Внедрение TechnologiCS в этом смысле не исключение, хотя продукт и не затрагивает финансово-экономический блок.
При внедрении корпоративной информационной системы бизнес-процессы предприятия (с разной степенью успеха) приводят в соответствие с бизнеслогикой, реализованной в выбранной информационной системе. Такой подход, будучи верным по сути, становится весьма затратным из-за объективных обстоятельств:
- устоявшаяся практика ведения бизнеса;
- неготовность персонала к нововведениям;
- ограниченность ресурсов предприятия (человеческих, временных, денежных).
В такой ситуации большое значение приобретают гибкость программного обеспечения, а также компетенция и мотивация группы внедрения, то есть коллектива специалистов предприятия и компании-консультанта.
С другой стороны, гибкость системы, дающая возможность полностью продублировать существующие процессы производственного учета, во-первых, делает внедрение дорогостоящим, а управление проектом трудоемким и рискованным; во-вторых, стремление автоматизировать все нужные и ненужные процессы (угодить каждому пользователю) доводит идею создания логически стройной системы до абсурда. Случается, что, автоматизируя сложившийся процесс как он есть, получают, извините, автоматизированный бардак.
Особенности и различия предприятий
При внедрении системы TechnologiCS на любом предприятии компания CSoft стремится максимально учесть особенности организационной структуры и уже сложившихся бизнес-процессов. Поэтому для двух представленных в этой статье предприятий выбор путей автоматизации производственного учета был обусловлен спецификой существующих у них производств. Еще на этапе подготовки к проекту со специалистами предприятия подробно обсуждались тонкости реализации тех или иных характерных моментов работы производственных служб.
Последние зачастую получают информацию из конструкторско-технологических подразделений на бумажных носителях либо в сильно урезанном виде из систем финансово-экономического или бухгалтерского направления. Это значительно затрудняет возможность ее полноценного использования при планировании и учете производства. Задача ПП TechnologiCS состояла в том, чтобы консолидировать информацию и использовать ее в штатных блоках планирования и учета производства.
О ЗАО «ВолгАэро» и процессе внедрения на нем системы TechnologiCS было подробно рассказано в статье, упомянутой выше. Напомним лишь, что основной задачей совместного французскороссийского предприятия является выполнение заказов на обработку высокотехнологичных деталей авиадвигателей.
ОАО «Русская Механика» — второе предприятие, о котором пойдет речь в статье, — на сегодня является единственным отечественным производителем серийных снегоходов «Буран» и «Тайга».
Рассмотрим различия выбранных нами предприятий по следующим критериям:
- тип производства;
- требования к качеству продукции;
- дискретность учета деталей и сборочных единиц (ДСЕ) в производстве.
Тип производства (серийность продукции)
Кардинальные отличия этих предприятий обусловлены, прежде всего, выпускаемой ими продукцией. Тип производства ЗАО «ВолгАэро» — мелкосерийный, близкий к единичному. В то же время ОАО «Русская Механика» производит изделия достаточно крупными сериями. Месячный объем производимой продукции, как и ее тип, определяется здесь отделом маркетинга предприятия на основе исследований рынка, то есть не зависит напрямую от портфеля заказов.
Требования к качеству продукции
При том что оба предприятия стремятся максимально удовлетворять потребности своих потребителей как в отношении функциональных возможностей производимой продукции, так и в отношении ее качества, контроль качества продукции и его доля в конечной стоимости продукта на предприятиях значительно различаются.
ЗАО «ВолгАэро» является предприятием авиадвигателестроительного комплекса. Производимая им продукция имеет большое количество особо ответственных параметров. Для ЗАО «ВолгАэро» качество продукции и отсутствие производственного брака является критически важной характеристикой конечного продукта, поэтому методы контроля качества и применяемое здесь оборудование весьма дорогостоящи.
ОАО «Русская Механика» сосредотачивает внимание не на выявлении брака, а на его предупреждении, на тщательном контроле производственного процесса. Целью в данном случае является выпуск качественной продукции по умеренной цене. ОАО «Русская Механика» является классическим примером предприятия общего машиностроения.
Дискретность учета ДСЕ в производстве. Прослеживаемость
Термин «прослеживаемость» происходит от английского термина «traceability» и применяется, в основном, при производстве номерных ДСЕ, как это делается, например, в авиации. Там на всех деталях и сборочных единицах, как правило, имеется информация о том, кто, когда и на каком станке изготовил конкретную деталь, об индивидуальном номере, сертификатах на материал и комплектующие, аттестованных технологических процессах и т.д. В общем, полная история их производства.
Для предприятия общего машиностроения, каковым является ОАО «Русская механика», такая скрупулезность избыточна. Главное — обеспечить производство комплектующими, минимизировать «незавершенку», поддерживая заданный уровень качества продукции и темп производства. Все изготовленные в разное время ДСЕ с одним обозначением абсолютно идентичны с точки зрения системы учета при условии отсутствия брака и изменений технической документации.
Теперь перейдем к описанию реализации производственного учета на двух упомянутых предприятиях.
Схема производственного учета в ЗАО «ВолгАэро»
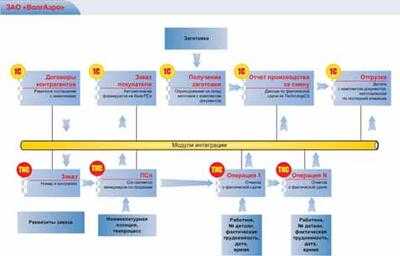
Процесс формирования производственной программы и плана для производственных подразделений полностью исключает обезличивание продукции, начиная с момента получения заготовки и вплоть до печати сопроводительной документации. То есть запуск одной и той же номенклатурной позиции для разных заказчиков не допускает возможности смешивания их в процессе производства. В рамках существующего договора с заказчиком на предприятие поступают отдельные заказы, в которых указываются количество и срок изготовления определенного вида изделий. Такая схема распространена на многих предприятиях, выпускающих литерную продукцию.
Итак, процедура производственного учета на ЗАО «ВолгАэро» начинается с момента получения предприятием заготовки (реже — материала) с соответствующей сопроводительной документацией. Номер заготовки заносится в систему Technologies менеджером по продажам. Номер производственной спецификации (ПСп) составлен из кода заказчика, изделия и номера сопроводительной карты, который генерируется системой Technologies автоматически в порядке возрастания.
Менеджер по продажам указывает, что и когда должно быть изготовлено. Алгоритм выбора версии технологического процесса на предприятии автоматизирован, так как деталь или сборочная единица может быть изготовлена на предприятии только согласно технологическому процессу, утвержденному в рамках ОКПИ (отчета по контролю первого изделия), аналогичного французскому DVI (Dossier de validation industrielle).
Многое из того, что на этапе согласования проекта внедрения планировалось к выполнению, оказалось невостребованным ввиду объективных причин, одной из которых стало изменение бизнес-логики учета производства продукции и исключение ненужных процессов. Так случилось, например, с ролью менеджера по планированию в цепочке производственного учета, и теперь его функции система выполняет автоматически.
После того как менеджер по продажам присвоит ПСп статус «В производстве», содержащиеся в ней данные появляются на закладках производственных модулей системы TechnologiCS.
Плановик линии на основании данных из ПСп формирует пооперационный план для своей линии (участка) и печатает сопроводительную карту (СК). Затем связывает номер заготовки с номером сопроводительной карты и с индивидуальным номером готового изделия, если они различны. Деталь движется по маршруту вместе с приложенной к ней СК, в которой работник, выполнивший операцию, указывает параметры изготовления и расписывается.
Изначально задумывалось, что данные по фактическому изготовлению будет заносить в систему TechnologiCS сам работник, выполнивший данную операцию, но из-за организационных проблем (недоверие к операторам оборудования, отсутствие компьютеров на их рабочих местах и пр.) реализация этой схемы была отложена, хотя осуществить ее не составляет большого труда.
В сопроводительной документации каждой позиции плана (операции, назначенной к выполнению) присваивается свой уникальный код. При помощи сканера штрих-кода специально назначенный оператор ЭВМ оформляет по этому коду фактическую сдачу. Также с помощью сканера можно позиционироваться на нужную ПСп, деталь или операцию.
Из вышесказанного следует, что на предприятии реализован пооперационный учет. Вся информация в TechnologiCS по учету деталей в производстве ведется в модуле «Производство». В этом же модуле формируется вся отчетность по выполнению производственной программы: план-факт на месяц, отчет о выпуске продукции за месяц и т.д. Стоит отметить, что большую часть форм производственных отчетов сотрудники ЗАО «ВолгАэро» разработали самостоятельно.
Принцип прослеживания основан на том, что операции на предприятии всегда выполняются последовательно. Порядок их следования никогда не нарушается. Поэтому определить местоположение детали в определенный момент времени можно следующим образом. В графе «Кол-во» указывается планируемое к изготовлению количество деталей, в графе «Изгот. по опер.» — количество деталей, изготовленных на данной операции, в графе «Готово» — количество деталей, изготовленных на последней операции технологического процесса, то есть окончательно готовых. На представленном рисунке видно, что деталь изготавливается на операции № 13, так как процесс дошел только до этой операции. Следовательно, она должна находиться на той производственной линии, где согласно технологическому процессу выполняется эта операция.
Номер операции является внутрисистемным, а не технологическим (он на рисунке скрыт) и фиксирует лишь порядок следования. В данном случае не требуется дублировать в системе складского учета TechnologiCS внутризаводские перемещения деталей. Все же остальные движения ТМЦ ведутся в системе 1С: Предприятие.
Несмотря на кажущуюся жесткость подобного подхода, сохранилась возможность оформлять выполнение операции на линии, отличной от указанной в технологическом процессе, а также пропускать выполнение отдельных операций.
Трудоемкость проставляется фактическая, так как плановое штучное время имеется не во всех технологических процессах, они большей частью не отработаны. Идет постоянное повышение производительности труда и, следовательно, уменьшение штучного времени и времени подготовительно-заключительного (на наладку). Производительность повышается за счет того, что работники осваивают оборудование, сокращается время на наладку, оптимизируются программы для станков с ЧПУ, написанные в материнской компании для аналогичного оборудования. В связи с этим и система оплаты труда работников повременная.
Модули складского учета в системе TechnologiCS не используются. Весь складской учет ведется в системе 1С: Предприятие, в которую информация из TechnologiCS поступает с помощью модулей интеграции, использующих функции API обеих систем.
Схема производственного учета в ОАО «Русская Механика»
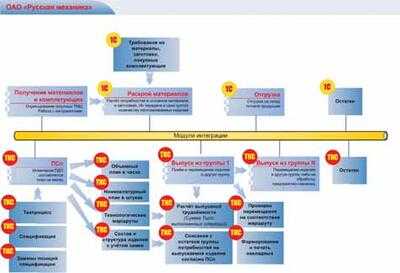
Как отмечалось выше, на ОАО «Русская Механика» тип производства — крупносерийный, характеризующийся большим коэффициентом закрепления операций. План предприятия формируется на месяц, с еженедельной корректировкой (уточнением). Еще одним ключевым моментом схемы планирования ОАО «Русская Механика» является наличие сборочных единиц с большим количеством возможных замен, которые действуют только для конкретной сборочной единицы. Поэтому в процессе формирования номенклатурного плана, кроме разузлования изготавливаемого изделия, важно наличие механизма простановки замен ДСЕ, что позволяет сформировать потребность в ДСЕ, которые впоследствии будут списаны при выпуске изделия из группы (участка).
Замены могут быть временными, обусловленными выпуском ВТИ (временное техническое извещение), в этом случае для замены указывается период действия и система Technologies производит замену автоматически, если начало сборки узла попадает в указанный период. Остальные замены либо не проводятся, и изготовление идет по основному составу, либо сотрудник планово-технического отдела (ПДО) проводит их по каждой позиции отдельно — так сказать, вручную.
Производственный план на месяц формируется в двух видах: номенклатурный план и объемный. Номенклатурный план — перечень номенклатур -ных позиций, которые следует изготовить за определенный период, с указанием дат запуска/выпуска. Объемный план показывает трудоемкость, которую должны выполнить цех или группа (участок) за определенный промежуток времени. При этом на предприятии исторически принято допущение: плановая трудоемкость и та, что фактически затрачена на выполнение технологической операции, равны.
Производственный учет на ОАО «Русская Механика» реализован в системе Technologies с помощью модулей складского учета. Производственные модули в Technologies не используются.
В начале внедрения производственного учета заказчиком было высказано требование: сделать работу пользователей максимально простой и максимально автоматизировать их действия. Оформление фактического изготовления и движения ТМЦ по производственным подразделениям предприятия выполняется неквалифицированным (с точки зрения ИТ) персоналом, и потому необходимо было исключить возможность некорректного ввода данных. Это стало едва ли не определяющим условием при внедрении автоматизированной системы учета. Вся логика реализации учета должна была по возможности максимально использовать алгоритм, реализованный в существующей на предприятии системе АСУП.
Вызвано это тем, что внедрение предложенных нами схем производственного учета потребовало бы больших затрат на переобучение или замены производственного персонала, а главное — повлекло бы за собой изменение существующих бизнес-процессов. То, что является стандартной практикой при внедрении системы в обычных условиях, в нашем случае не прошло. Заказчик был тверд: «Вы сюда пришли не для того чтобы революцию делать!» Кто был прав, а кто нет — рассудит время.
Таким образом, для пользователя в цеховой учетной точке (группе) работа почти не изменилась, за исключением замены текстового интерфейса MS-DOS на графический интерфейс Windows. А вот что касается пользователей в ПДО и руководителей складских подразделений, то для них рабочий процесс изменился значительно.
Итак, как уже отмечалось, весь производственный учет реализован с помощью складского учета двух систем — Technologies и 1С: Предприятие. Принцип разделения функций схож с разделением, принятым в ЗАО «ВолгАэро»: все движения ТМЦ внутри предприятия поддерживает Technologies, все перемещения вовне и извне — 1С.
Принятая на предприятии система учета описывала только межцеховые передачи. В Technologies он был детализирован до межгруппового учета. Алгоритм реализации получился следующий. Фиксация фактической сдачи осуществляется не по выполнении операции, как на ЗАО «ВолгАэро», а при передаче номенклатуры из одной группы в другую (внутри одного цеха, между цехами либо на сторону, если операция выполняется на предприятии-смежнике по кооперации), то есть при перемещении между учетными точками.
При этом, если перемещалась деталь, то система анализирует загруженную в актуальную производственную спецификацию версию технологического процесса этой детали. Если такая передача в технологическом процессе встречается один раз, система перемещает деталь и добавляет трудоемкость выполненных по технологическому процессу операций в данной группе к выполненной трудоемкости группы. Если передача из группы, А в группу В по маршруту встречается два и более раз, система запрашивает пользователя, оформляющего перемещение, какую из передач совершить. При этом в остатках группы детали разной степени обработки на разных заходах в группу не перемешиваются благодаря разным учетным карточкам, на которые они приходуются и с которых расходуются из группы. Таким же образом реализовано движение деталей не по маршруту, когда передача из группы, А в группу В не встречается по технологическому процессу вовсе. При этом, правда, группе не добавляется трудоемкость. Затем автоматически формируется заполненный бланк накладной, которая выводится на печать.
При передаче сборочной единицы кроме трудоемкости система автоматически списывает с группы комплектующие, необходимые для изготовления этой сборки по разузлованию в ПСп и по технологическому процессу. Если между разузлованием, выполненным по активным версиям спецификаций, и технологическим процессом имеются несоответствия, система списывает совпадающие позиции по техпроцессу, а отличающиеся по разузлованию.
Таким образом, выполняя оформление передачи номенклатурной позиции, работник учетной точки провоцирует в системе Technologies расчет выполнения номенклатурного и объемного плана для данной группы (изготовление номенклатурных позиций и выработанную трудоемкость), учитывает и списывает комплектующие и сами изготавливаемые позиции плана.
Все это дает возможность в реальном времени сверять плановые и фактические показатели в системе Technologies. Работники различных служб предприятия могут пользоваться отчетами, которые в различных разрезах в реальном времени позволяют контролировать ход выполнения производственных планов. Благодаря развитым возможностям программного доступа к данным системы Technologies по определенному регламенту вся информация передается в систему 1С: Предприятие для расчета заработной платы, отчислений и т.д. Данные передаются в систему 1С: Предприятие раз в сутки, что гарантирует их актуальность. В свою очередь, данные по приходу покупных комплектующих в группы TechnologiCS импортирует из системы 1С: Предприятие через файл импорта. Таким образом, мы получили замкнутую цепочку движения ТМЦ по предприятию.
Заключение
Рассмотренные в нашей статье два варианта решения задачи автоматизации производственного учета на базе Technologies ни в коей мере не являются эталонными. На любом другом предприятии, даже с похожим производством, решать эту задачу можно, а может быть даже и нужно, другими способами. Благо Technologies позволяет делать это с помощью достаточно гибких модулей «Производство» и «Склад». Нашей целью было лишь поделиться опытом использования этой гибкости в решении конкретных задач производственного учета.
www.cadmaster.ru
Новинки ГОЛЬФСТРИМ 2014!
Новинки ГОЛЬФСТРИМ 2014!
Новые инструменты создания номенклатурных планов
В новой версии ГОЛЬФСТРИМ 2014 были внесены изменения в инструмент создания номенклатурных планов выпуска деталей и сборочных единиц (ДСЕ), направленные на дальнейшее повышение удобства регулярного использования этих инструментов.
Во-первых, добавлена возможность интерактивного анализа загрузки производственных мощностей. Какие это дает преимущества?
Создание плана выполняется в одной рабочей задаче, предоставляющей все необходимые данные для принятия управленческого решения. Система автоматически подбирает ДСЕ, которые должны быть включены в план. Будущие плановые позиции выделяются цветом: зеленые — включение таких позиций обязательно из-за высокого приоритета заказа; красные — такие позиции просрочены. Это позволяет визуально определить необходимый минимум позиций для подбора. По выбранным позициям производится расчет суммарной трудоемкости и стоимости.
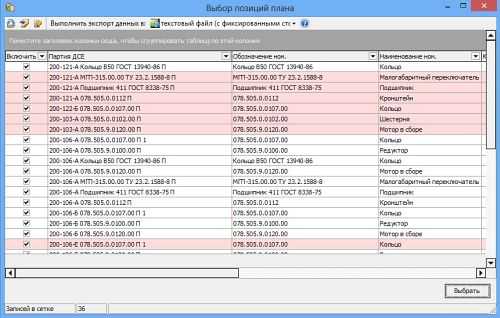
Подбор плановых позиций
Для того, чтобы оценить реалистичность плана, можно воспользоваться прогнозом загрузки ключевых производственных мощностей, который включен в форму создания плана. Прогноз загрузки производится по наиболее важным, критичным производственным ресурсам. Под такими ресурсами понимается оборудование или рабочие определенных профессий, отсутствие которых может серьёзно повысить риск срыва плана.
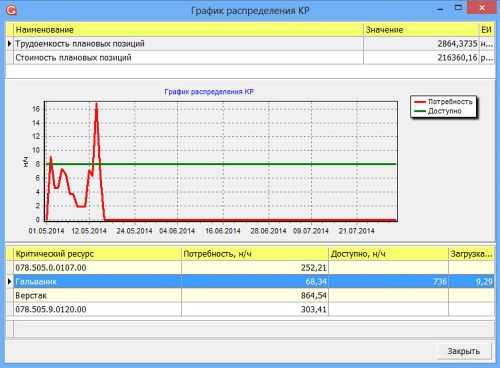
Анализ создаваемого плана по критическим ресурсам
Во-вторых, реализована возможность создания цепочки взаимосвязанных номенклатурных планов выпуска.
На выполнение плана в срок и в заданном объеме номенклатуры влияет слаженная работа всех производственных подразделений. Для этого необходимо рассматривать план для производственного подразделения не автономно, а в рамках системы взаимосвязанных планов всех производственных подразделений предприятия. Работа в рамках цепочки взаимосвязанных номенклатурных планов выпуска позволяет: а) снизить трудоемкость учета взаимосвязи номенклатурных планов, б) обеспечить фактическую взаимосвязь планов производственных подразделений. Логика работы системы может быть проиллюстрирована следующим примером.
Имеется план выпуска для сборочного цеха. Для того, чтобы обеспечить выпуск запланированного количества сборочных единиц, в том числе, требуется включение и выполнение плановых позиций входящих ДСЕ, за выпуск которых отвечают цеха по расцеховочному маршруту данных ДСЕ. Следовательно требуется обеспечить наличие всех необходимых ДСЕ в планах других подразделений. Номенклатурные планы рассматриваются взаимозависимыми, например «основным» будет план сборочного цеха, а номенклатурные планы для промежуточных цехов станут «зависимыми». ГОЛЬФСТРИМ позволяет автоматически создавать планы для «зависимых» цехов, а если такой план был уже создан ранее — принудительно включать необходимые детали и сборочные единицы. При этом, состояние как основного, так и дополнительного плана может быть зафиксировано.
Новые алгоритмы планирования
В 2014 версии расчет дат запуска и изготовления деталей и сборочных единиц возможен несколькими алгоритмами, реализованными в системе. Выбор предпочтительного (для условий и требований предприятия) алгоритма обычно производится в при внедрении:
- расчет по классическому алгоритму MRP;
- расчет по группам опережения партий в производственном цикле изготовления изделия;
- расчет посменного плана рабочих центров с учетом загрузки производственных мощностей.
При календарном планировании по методике MRP определяются сроки начала и окончания производства партий ДСЕ с учетом применяемости каждой ДСЕ в составе изготавливаемого изделия. Помимо применяемости, для выполнения расчета необходимо знать плановую дату окончания производства заказа и длительности производственных циклов каждой партии ДСЕ.
Согласно методике MRP расчет плановых дат изготовления выполняется «из будущего в настоящее» — от даты исполнения заказа назад, к сегодняшнему дню. Пример диаграммы Гантта, построенной по результатам расчета, приведен на рис. 3. Как видно из диаграммы, MRP пытается спланировать все материалы «точно ко времени» их потребности на следующем этапе производства или сборки. При этом алгоритм не анализирует загрузку производственных мощностей, так как стандарты MRP II предполагают итерационный подход к процедуре планирования: рассчитали — проанализировали — внесли изменения в данные — пересчитали и т.д. до получения приемлемого плана. Можно сказать, что MRP-алгоритм рассчитывает «идеальный» (с точки зрения длительности цикла) график изготовления изделия.
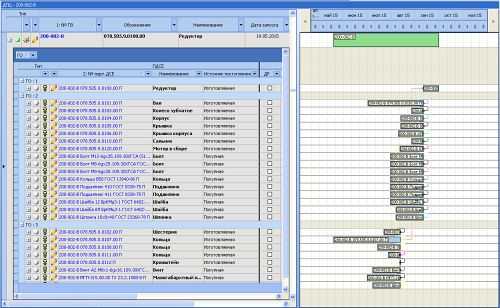
Отображение результатов расчета по алгоритму MRP
Алгоритм расчета дат по группам опережения во многом схож с MRP-алгоритмом — так же выполняет расчет дат «из будущего в настоящее» без учета загрузки производственных мощностей. Основное отличие заключается в распределении ДСЕ по шкале времени — партии группируются по так называемым «группам опережения», соответствующим уровню ДСЕ в дереве состава изделия. Пример диаграммы Гантта, по результатам расчета алгоритмом групп опережения, приведен на рис. 4. Как видно из диаграммы, для контроля изготовления заказа необходимо в первую контролировать партии ДСЕ с максимальной длительностью производственного цикла. Другие партии ДСЕ данной группы опережения имеют временной задел.
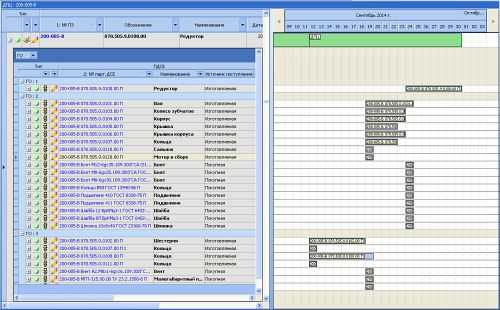
Отображение результатов расчета по группам опережения
Как показывает практика, такой алгоритм лучше, нежели MRP, подходит для планирования изготовления сложных изделий (10000…100000 элементов состава) в условиях невысокого качества данных для расчета длительностей производственных циклов. Наличие временных заделов дает планировщику больше свободы в корректировке расчетных дат и сглаживает неточности расчета на временной шкале. К ограничениям алгоритма следует отнести 2 особенности: во-первых, итоговый расчетный цикл изготовления в большинстве случаев длиннее, чем по результатам MRP-расчета; во-вторых, при очень больших разбросах в длительностях циклов ДСЕ качество результатов расчета резко снижается.
Следует отметить, что оба алгоритма достаточно требовательны к точности и полноте данных для расчета. Для снижения потребностей к точности исходной информации в ГОЛЬФСТРИМ 2014 предусмотрено значительное число настраиваемых параметров, позволяющих по мере необходимости быстро заменить недостающие данные усредненными значениями. Таким образом, начать практическое использование алгоритмов можно в минимальные сроки.
Посменное планирование
Посменное планирование является инструментом расчета плановых сроков изготовления заказа, который учитывает загрузку мощностей с детализацией до смен. Планирование загрузки выполняется на уровне рабочих центров. При этом, под рабочим центром понимается группа взаимозаменяемого оборудования, расположенная на локальном производственном участке. Для организации планирования потребности в мощностях (CRP) и подробного календарного планирования рабочий центр рассматривается как одна производственная единица. Примером рабочего центра может выступать отдельный станок, группа станков или участок, на котором выполняется определенный тип работ. При этом, предварительное заполнение справочника рабочих центров не является обязательным (ГОЛЬФСТРИМ может заполнять такой справочник самостоятельно), также не является необходимым предварительное указание рабочих центров в PLM-системе.
Точность посменного планирования напрямую зависит от наполнения системы данными. Например, минимально необходимым для расчета посменного плана является наличие графика работы оборудования, пронормированных технологических операций с указанным оборудованием и профессиями. При отсутствии в цехе, участке или рабочем центре отдельного графика работы оборудования — будет использован график работы более высокого уровня. Минимально необходимым для расчета является наличие графика работы оборудования для предприятия в целом, который может быть создан на основе шаблонов.
Алгоритм посменного планирования позволяет оптимизировать переналадки оборудования, за счет группировки технологических операций одинаковых ДСЕ из разных заказов. При создании посменного плана используется приоритет максимальной загрузки рабочего центра с учетом доступного рабочего времени. При расчете учитываются возможные отклонения от графика работы оборудования. Например, при расчете возможен учет запланированных планово-предупредительных ремонтов для оборудования, сверхурочная работа и др.
Результаты расчетов посменного плана представлены в отдельной интерактивной задаче. Вы можете выполнять ручную коррекцию результатов расчета. В системе реализовано отображение загрузки рабочих центров (что позволяет определить, на какую дату и в какой объеме есть доступное время), а также учесть взаимосвязь технологических операций.

Результат расчета посменного плана
Позаказный складской учет
В новой версии ГОЛЬФСТРИМ значительно расширены возможности управления потоками материальных ресурсов в производстве.
Позаказный учет остатков позволяет точно знать для какого заказа предназначены те или иные материалы и ДСЕ и позволяет предприятию значительно увеличить эффективность управления производством. С одной стороны, повышается степень контроля за обеспечением потребностей в материальных ресурсах для конкретного заказа. С другой стороны, понимание того, в какому заказу относятся те или иные материалы и ДСЕ, позволяет не допустить повышение уровня незавершенного производства, а также рационально использовать существующие остатки.
Адресное хранение
Адресное хранение это способ организации складского хранения, учитывающий особенности материально-производственных запасов и особенности мест хранения. Автоматизация данной функции — это прежде всего стимул повышения качества управления материальными потоками за счет сокращения длительности выполнения второстепенных этапов (например поиск товара на складе), а также повышение контроля остатков материально-производственных запасов. Использование адресного хранения позволяет хранить остатки МПЗ по отдельным участкам склада (местам хранения). Вы можете получить информацию о текущих остатках в разделе отдельных мест хранения в режиме реального времени.
Инструментарий адресного хранения выполнен с возможностью расширения и конфигурирования, что позволяет максимально приблизить учетную структуру склада к реальной и легче использовать технологии оптимизации.
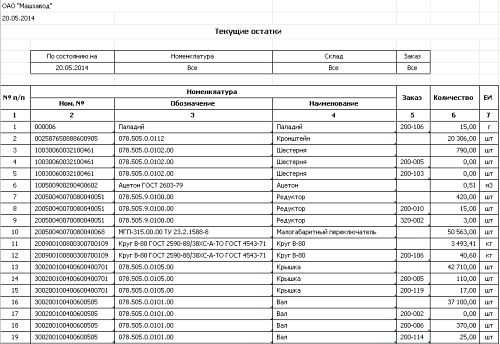
Отчет по остаткам в местах хранения
Учет экземпляров в производстве
В новой версии ГОЛЬФСТРИМ появилась возможность ведения учета экземпляров в производстве.
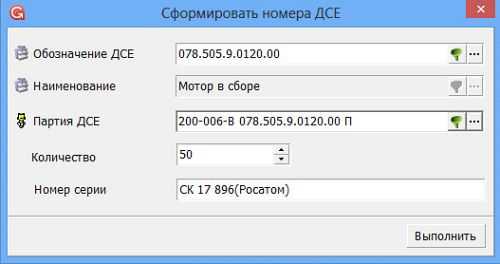
Генерация номеров сборочных единиц
Вы можете:
- Выполнять автоматическую генерацию номеров узлов;
- Связывать номерной узел с конкретным заказом потребителя;
- Определять конструкторское обозначение номерного узла, а также кода комплектации номерного узла;
- Вести состав номерного узла по входящим в него другим номерным узлам и деталям;
- Получать данные о применяемости номерного узла в номерном изделии;
- Получать данные об иерархии входимости номерного узла;
- Получать данные о движении номерного узла по учетным операциям.
По каждому номерному узлу или детали существует возможность в электронном виде хранить информацию о движении в производстве, исполнителях технологических операций и др.
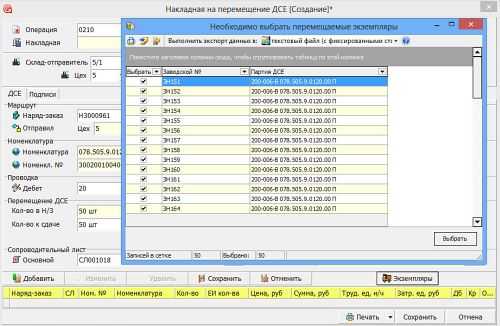
Выбор перемещаемых номерных сборочных единиц
Групповое управление производственными спецификациями
Производственная среда динамична и изменчива и в ряде случае требуется оперативное изменение огромных объемов данных. В ГОЛЬФСТРИМ 2014 предложен универсальный инструмент группового управления производственными спецификациями. Данный инструмент позволяет дополнять и обновлять информацию производственных спецификаций.
Например, производственная спецификация содержит вспомогательный материал с определенной нормой расхода. Однако данный материал закупить не удалось и принято решение использовать материал-аналог. Механизм группового изменения производственных спецификаций позволяет внести такие изменения по интересующим партиям ДСЕ (даже если такие партии запущены в производство).
Групповое управление производственными спецификация позволяет:
- изменять применяемость ДСЕ;
- изменять, добавлять заготовку;
- редактировать данные об основных и вспомогательных материалах;
- править расцеховочный маршрут и техпроцессы и др.
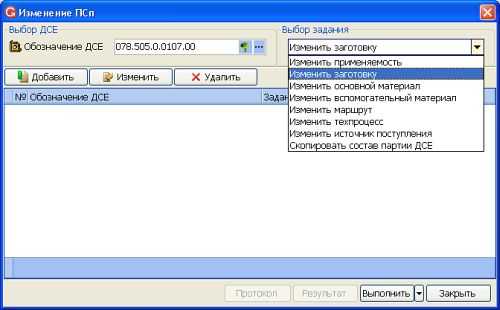
Редактирование заготовки для группы партий ДСЕ
Все изменения записываются и сохраняются в специальной картотеке. При этом, существует возможность получить информацию о внесенных изменения по отдельной партии ДСЕ конкретного заказа и при необходимости отменить изменения.
Предложенный механизм позволяет запустить работу системы на неполных данных и по мере их появления повышать актуальность производственных спецификаций.
Использование ДСЕ в других заказах
Следующую возможность легко проиллюстрировать примером: в рамках производственного заказа выполнялось изготовление сложного изделия. Однако заказчик отказался от заказа. Детали и сборочные единицы заказа требуется использовать в других заказах, чтобы минимизировать потери.
Для решения поставленной задачи предусмотрен специальный инструмент, позволяющий использовать для выполнения заказа, готовые или изготавливаемые ДСЕ, другого заказа. При закреплении ДСЕ за другим заказом пересчет понесенных фактических трудовых затрат выполняется автоматически. Кроме того, система сохраняет сведения о том, откуда и куда было проведено изменение.
Закрепление ДСЕ за другим заказом
Шифры производственных затрат
В новой версии ГОЛЬФСТРИМ появилась возможность работы с шифрами производственных затрат. Шифры производственных затрат (далее — ШПЗ) используются для быстрой и однозначной идентификации оперативных документов с точки зрения отнесения его к различным системам классификации (например вид производства, статья затрат и др.) затрат. Для этого каждому виду изделий, заказу или статье расходов присваиваются условные числовые обозначения (шифры). Пользование шифрами вырабатываемой продукции, выполняемых заказов и статей затрат позволяет сократить работу по указанию на документах, куда должен быть отнесен тот или иной расход материальных и денежных средств.
ШПЗ могут использоваться для ускорения:
- ручной обработки оперативных документом за счет наличия шифра на самих шаблонах. Это позволяет быстро найти интересующий документ.
- получения аналитической отчетности в разрезе элементов шифра статьи затрат и непосредственно статей затрат.
gulfstream-mrp.ru
Организация производственного процесса во времени.
Цель и задачи исследования.
Закрепление теоретических знаний по темам «Организация производственного процесса», «Оперативно-производственное управление».
Практическое ознакомление:
с видами движения партий деталей в производстве;
с методами определения длительности производственного цикла простого и сложного процессов.
2.Теоретические положения
Общие положения
Производственный процесс представляет собой совокупность отдельных процессов труда и естественных процессов, в результате которых исходные материалы превращаются в готовые изделия.
Процесс изготовления отдельных детале-сборочных единиц (ДСЕ) называется простым процессом, а процесс производства изделий – сложным.
Производственный процесс протекает в пространстве и во времени. Его рациональное осуществление в пространстве обеспечивается рациональной производственной структурой участка, цеха, предприятия. А согласование и планомерное протекание во времени – правильным построением его производственного цикла.
Производственным циклом Тп называется календарный период времени от начала до окончания производственного процесса.
Основные задачи в организации производственного процесса во времени: выбрать наиболее рациональный способ передачи ДСЕ с операции на операцию (вид движения ДСЕ), определить длительность производственного цикла простого процесса по отдельным ДСЕ на этапе заготовительных работ, механообработки и др. и длительность цикла сложного процесса изготовления изделия с тем, чтобы можно было определять сроки запуска ДСЕ в производство.
2.2. Простой процесс.
Производственный цикл простого процесса складывается из следующих составляющих:
Тп=Тт+Тпер+Те, (1)
где Тт– технологический цикл обработки ДСЕ;
Тпер– межоперационные перерывы и перерывы, связанные с режимом работы;
Те– естественные процессы.
Технологический цикл состоит из операционных циклов. Операционный цикл
— это продолжительность обработки партии
ДСЕ на данной,i-й
операции;
,
(2)
где n – размер партии ДСЕ, шт.;
ti– штучно-калькуляционная норма времени на операцию, мин/шт.;
сi– число рабочих мест наi-й операции.
Технологический цикл многооперационного процесса не есть арифметическая сумма операционных циклов. Его величина зависит от способа передачи ДСЕ с операции на операцию (вида движения). Идея о видах движения: последовательном, параллельно-последовательном, параллельном, являющаяся фундаментом теории организации производственных процессов, принадлежит профессору Ленинградского политехнического института О.И.Непоренту.
При последовательном виде движения каждая последующая операция над партией ДСЕ начинается только после обработки всех ДСЕ на предыдущей операции. Таким образом, партия не дробится, технологический цикл определяется ( рис.1) так:
.
(3)
При
параллельно-последовательном виде
движения партия ДСЕ вnштук обрабатывается на каждой операции
непрерывно, но с операции на операцию
передается частями – передаточными
партиями врштук. Это обеспечивает
сокращение технологического цикла за
счет частичного совмещения времени
выполнения смежных операций. (рис. 2):
(4)
где — совмещение операционных циклов междуi-й и (i+1)-й
операциями вследствие работы передаточными
партиями.
Анализ и
на рис. 2 показывает, что в общем случае
определяется по формуле:
(5)
где р– размер передаточной партии, шт.;
— время выполнения (с учетом числа рабочих
мест) более короткой операции при
сравнении двух смежных операций.
Так, из операций №1 и 2 более коротким операционным циклом обладает первая, из операций №2 и 3 – третья.
Следовательно, вторая операция (поскольку она длиннее первой) может начаться сразу после окончания обработки на первой операции первой передаточной партии ДСЕ (р=2 шт.). Остальные передаточные партии успевают попасть на вторую операцию, не нарушая непрерывности их выполнения.
Но непрерывность обработки ДСЕ на третьей операции может быть достигнута лишь при накоплении перед ее началом минимально необходимого числа ДСЕ. Поэтому момент начала выполнения третьей операции графически может быть определен исходя из условия, что последняя передаточная партия со второй операции сразу поступает на третью, а все предыдущие передаточные партии должны быть непрерывно обработаны к этому моменту на третьей операции.
Подставив значение в формулу (4), получим выражение для
расчета технологического цикла при
параллельно-последовательном виде
движения ДСЕ:
(6)
При параллельном виде движения передаточные партии передаются с предыдущей операции на последующую немедленно после окончания их обработки на предыдущей. Поэтому непрерывно выполняется только одна операция, имеющая наибольшую продолжительность. Но каждая передаточная партия движется по операциям непрерывно, не пролеживая в ожидании обработки (рис. 3).
Характеристики различных видов движения ДСЕ приведены в табл. 1.
Из графика видно, что
(7)
где — время выполнения с учетом числа рабочих
мест самой продолжительной операции.
Таблица 1 — Характеристика видов движения ДСЕ
Виды движения | Преимущества | Недостатки | Целесообразные области применения |
Последовательный | Простота планирования производства | Длительный цикл производства | Мелкосерийное, единичное производство при малых партиях ДСЕ и невысокой трудоемкости |
Параллельно-последовательный | Сокращение цикла производства | Увеличение числа планово-учетных единиц | Серийное производство |
Параллельный | Короткий цикл производства | При отсутствии синхронизации операций – простои оборудования | Крупносерийное и массовое производство |
studfiles.net