3D-принтеры по металлу, технологии и стоимость
В этом подробном гиде мы рассмотрим основные принципы технологий 3D-печати металлами, расскажем о разнице между ними и приведем примеры применения. Прочитав эту статью, вы узнаете об их преимуществах и ограничениях. Читайте статью и смотрите видео о 3D-печати металлами.
Содержание
SLM & DMLS: в чем разница
Выборочное лазерное плавление (SLM) и прямое лазерное спекание металлов (DMLS) являются двумя процессами аддитивного производства, которые относятся к семейству трехмерной печати порошковым слоем. Эти две технологии имеют много общих черт: обе используют лазер для спекания или выборочного плавления частиц металлического порошка, связывая их вместе и создавая слои изделия, один за другим.
Различия между SLM и DMLS сводятся к основам процесса склеивания частиц (а также к патентам): в SLM лазер расплавляет металлический порошок, а в DMLS частицы порошка нагреваются меньше и спекаются между собой, не переходя в жидкую фазу.
Основное отличие DMLS от традиционных технологий производства металлических деталей в том, что DMLS-принтер создает объекты без остаточных внутренних напряжений, которые могут снижать качество металлических компонентов изготовленных литьем и штамповкой. Это важно для деталей производимых для автомобильной и аэрокосмической отрасли, так как они должны выдерживать высокие нагрузки.
В SLM лазер расплавляет каждый слой металлического порошка, и перепады температур могут приводить к возникновению внутренних напряжений в детали, что потенциально может сказаться на ее качестве, хоть и в меньшей степени чем, например, при литье. В этом вопросе преимущество SLM перед традиционными технологиями меньше, чем преимущество DMLS. С другой стороны, спеченные по технологии DMLS детали уступают в монолитности и запасе прочности деталям напечатанным по методу SLM.
Технологии похожи до степени смешения, как по принципу действия, так и по используемым техническим решениям, потому некоторые 3D-принтеры способны печатать по обеим методикам.
Обе технологии, SLM и DMLS, используются в промышленности для создания деталей для различных областей машиностроения. В этой статье мы используем термин «3D-печать металлами» для обозначения обоих процессов в целом, и описываем их основные механизмы, что поможет инженерам и дизайнерам в понимании преимуществ и ограничений технологии.
Расскажем и о других технологиях 3D-печати металлами, менее распространенных, таких как электронно-лучевое плавление (EBM) и ультразвуковое аддитивное производство (UAM).
Процесс печати SLM / DMLS:
Процессы изготовления деталей по технологиям SLM и DMLS очень схожи.
Основные этапы:
-
Камеру построения сначала заполняют инертным газом (например, аргоном) для минимизации окисления металлического порошка, а затем нагревают до оптимальной температуры производства.
-
Тонкий слой металлического порошка распределяется по платформе построения, а высокомощный лазер сканирует поперечное сечение компонента, плавя или спекая вместе металлические частицы и создавая следующий слой. Вся область модели подвергается обработке, поэтому деталь сразу твердая.
-
После завершения формирования слоя, платформа построения опускается на толщину слоя и рекоутер наносит следующий слой порошка. Процесс повторяется до завершения всей детали.
Когда процесс печати завершается, детали полностью находятся в металлическом порошке. В отличие от процесса спекания полимерного порошкового слоя (такого как SLS), детали прикрепляются к платформе построения с помощью области поддержки. Области поддержки строятся с использованием того же материала, что и деталь, их необходимо использовать для избегания деформации и искажений, которые могут возникнуть из-за высоких температур обработки.
Когда камера построения остывает до комнатной температуры, неизрасходованный порошок вручную удаляется, а детали обычно подвергаются дополнительной термической обработке для снятия остаточных напряжений, затем удаляют поддержки. Детали отделяются от платформы построения и готовы к использованию или последующей обработке.
Схема принтера SLM / DMLS:
Характеристики SLM & DMLS
Параметры принтера
В SLM и DMLS почти все параметры процесса устанавливаются производителем принтера. Высота слоя, используемого в 3D-печати металлами, колеблется обычно от 20 до 50 микрон и зависит от свойств материала.
Стандартная область 3D-печати металлами варьируется около 250 x 150 x 150 мм, доступны принтеры и с большей областью печати, около 500 x 280 x 360 мм. Точность размеров, которую может достичь 3D-принтер для печати металлами, составляет приблизительно ± 0,1 мм.
Металлический порошок в SLM и DMLS используются повторно: обычно менее 5% уходит в отходы. После каждой печати неиспользованный порошок собирают, просеивают и затем смешивают с новым материалом, до состава необходимого для следующей печати.
В отходы идут, в основном, поддержки.
Небольшое серийное производство рамы велосипеда с использованием SLM. Предоставлено: Renishaw и Empire Cycles.
Адгезия между слоями
Металлические детали, изготовленные методами SLM и DMLS, имеют почти изотропные механические и термические свойства. Они твердые, с очень небольшой внутренней пористостью (менее 0,2-0,5%).
Металлические 3D-печатные детали имеют более высокую прочность и твердость и часто более гибкие, чем детали, изготовленные традиционным способом. Однако они более склонны к усталости.
Например, посмотрите в таблице ниже на механические свойства 3D-печатного сплава AlSi10Mg EOS и литого сплава A360. Эти два материала имеют очень похожий химический состав, с высоким содержанием кремния и магния. 3D-печатные детали имеют превосходные механические свойства и более высокую твердость по сравнению с литым материалом.
Из-за гранулированной формы порошка, шероховатость поверхности (Ra) металлической 3D-печатной детали составляет примерно 6-10 мкм. Эта относительно высокая шероховатость поверхности может частично объяснить более низкую усталостную прочность сплава.
Сравнение механических свойств отдельных разновидностей 3D-печатных и литых деталей:
Основные характеристики |
AlSi10Mg (3D-печатный сплав) |
A360 (Литой сплав) |
Предел текучести (деформация на 0,2%) |
XY: 230 MPa Z : 230 MPa |
165 MPa |
Прочность на растяжение |
XY: 345 MPa Z : 350 MPa |
317 MPa |
Модуль |
XY: 70 GPa Z : 60 GPa |
71 GPa |
Удлинение при разрыве |
XY: 12% Z : 11% |
3.5% |
Твердость |
119 HBW |
75 HBW |
Усталостная прочность |
97 MPa |
124 MPa |
Область поддержки и ориентация деталей
Области поддержки при 3D-печати металлами требуются всегда, из-за очень высокой температуры обработки, и они обычно строятся с использованием решетчатой структуры.
Область поддержки в 3D-печати металлами выполняет три функции:
-
Обеспечивает подходящую платформу для следующего слоя;
-
Прикрепляет деталь к платформе построения и предотвращает ее деформацию;
-
Отводит тепло от детали и позволяет ей остывать с контролируемой скоростью.
Детали часто ориентированы под углом, чтобы минимизировать вероятность деформации и максимизировать прочность в критических направлениях. Однако это увеличивает объем необходимой области поддержки, время печати, количество материала и общую стоимость.
Деформация также может быть сведена к минимуму с использованием бессистемных/случайных шаблонов сканирования, т.е. последовательности прохода лазером участков слоя. Эта стратегия сканирования предотвращает накопление остаточных напряжений в каком-либо конкретном направлении.Поскольку стоимость 3D-печати металлами очень высока, часто используются симуляции, для прогнозирования поведения детали во время печати. Алгоритмы непрерывной оптимизации также используются не только для максимизации механических характеристик и создания легких деталей, но и для минимизации необходимой области поддержки и вероятности деформации.
Кронштейн перед снятием с области поддержки, ориентированной под углом 45 °. Предоставлено: Concept Laser.
Полые секции и облегченные конструкции
В отличие от процессов спекания полимерных порошковых слоев, таких как в SLS, большие полые секции обычно не используются в 3D-печати металлами, так как области поддержки нельзя легко удалить.
В качестве альтернативы полым сечениям, детали могут быть спроектированы с оболочкой и ядром. Оболочка и ядро обрабатываются с использованием различной мощности лазера и скорости сканирования, что приводит к различным свойствам областей детали. Использование оболочки и ядра очень полезно при изготовлении деталей с большим сплошным сечением, поскольку оно значительно сокращает время печати и вероятность деформации, а также гарантирует производство деталей с высокой стабильностью и отличным качеством поверхности.
Использование решетчатой структуры также является общей стратегией в 3D-печати металлами, для уменьшения массы детали. Алгоритмы оптимизации топологии также могут помочь в разработке органически легкой формы.
Удаление порошка вокруг деталей, изготовленных методом 3D-печати SLM:
Расходные материалы для SLM и DMLS
SLM и DMLS могут производить детали из большого количества металлов и металлических сплавов, включая алюминий, нержавеющую сталь, титан, кобальтовый хром и инконель. Эти материалы охватывают потребности большинства промышленных применений, от аэрокосмической до медицинской. Драгоценные металлы, такие как золото, платина, палладий и серебро также могут быть использованы, но их применение ограничено, в основном, изготовлением ювелирных изделий.
Стоимость металлического порошка очень высока. Например, килограмм порошка из нержавеющей стали 316L стоит примерно 350 — 450 долларов. По этой причине минимизация объема детали и области поддержки являются ключом к тому, чтобы максимально снизить затраты.
Основным преимуществом 3D-печати металлами является ее способность печатать высокопрочными материалами, такими как никелевые или кобальт-хромовые суперсплавы, которые очень трудно обрабатывать традиционными методами производства. Значительную экономию средств и времени можно получить, используя 3D-печать металлами для создания деталей с почти чистой поверхностью, которая впоследствии может быть финально обработана традиционными способами.
Особенности разных материалов для 3D-печати металлом:
Материалы |
|
Алюминиевые сплавы |
● Хорошие механические и термические свойства ● Низкая плотность ● Хорошая электропроводность ● Низкая твердость |
Нержавеющая сталь и инструментальная сталь |
● Высокая износостойкость ● Большая твердость ● Хорошая пластичность и свариваемость |
Титановые сплавы |
● Коррозионная стойкость ● Отличное соотношение прочности и веса ● Низкое тепловое расширение ● Биосовместимость |
Суперсплавы из кобальта-хрома |
● Отличная стойкость к износу и коррозии ● Отличные свойства при повышенных температурах ● Очень высокая твердость ● Биосовместимость |
Никелевые суперсплавы (Инконель) |
● Отличные механические свойства ● Высокая коррозионная стойкость ● Термостойкость до 1200°C ● Используются в экстремальных условиях |
Драгоценные металлы |
● Используются в ювелирной промышленности ● Не имеют широкого распространения |
Другие технологии
Осаждение материала путем направленного энергетического воздействия (Directed Energy Deposition)
Можно подумать, что среди технологий печатью металлом отсутствует похожая на обычную FDM, однако, это не совсем так. Вы не сможете плавить металлическую нить в своем настольном 3D-принтере, а вот крупные производители владеют такой технологией и пользуются ею. Есть два основных способа печатать цельнометаллическим материалом.
Один из них называется Directed Energy Deposition (DED) или лазерное наплавление (LMD). Он использует лазерный луч для сплавления металлического порошка, который медленно высвобождается и осаждается из экструдера, формируя слои объекта с помощью промышленного манипулятора.
Обычно это делается внутри закрытой камеры, однако, на примере компании MX3D, мы видим возможность реализации подобной технологии в сооружении настоящего полноразмерного моста, который был изготовлен в октябре 2018 года в Амстердаме.
Изображение моста из металла, напечатанного MX3D в Амстредаме.
Еще одна технология наплавления называется Electron Beam Additive Manufacturing (EBАM), это процесс формирования слоев очень мощным электронным лучом, с его помощью расплавляют титановую проволоку толщиной 3 мм и создают крупные конструкции.
Послойное нанесение связующего материала (Binder Jetting)
Изображение работы принтера ExOne:
Технология 3DP от ExOne — еще один профессиональный метод с послойным соединением. Слои образуются путем склеивания металлических частиц и их последующего спекания (или плавления) в высокотемпературной печи, как и при производстве керамических изделий.
Еще один метод, похожий на технологию производства керамики, замешивание металлического порошка в металлическую пасту. 3D-принтер выдавливает ее с помощью пневматической экструзии, подобно тому, как строительный 3D-принтер делает это с бетоном, чтобы сформировать 3D-объекты. После того, как нужная форма напечатана, объекты также спекают в печи.
Постобработка
Различные методы последующей обработки используются для улучшения механических свойств, точности и внешнего вида 3D-печатных деталей.
Обязательные этапы последующей обработки включают удаление остатков порошка и области поддержки, в то время как термообработка (термический отжиг) обычно используется для снятия остаточных напряжений и улучшения механических свойств детали.
Обработка на станках с ЧПУ может быть использована для получения сложных геометрических форм (например, отверстий или резьбы). Обработка давлением, металлизация, полировка и микро-обработка могут улучшить качество поверхности и усталостную прочность металлической 3D-печатной детали.
Спутниковая антенна, изготовленная с помощью технологии DMLS. Предоставлено: Concept Laser and Optisys LLC.
Shining 3D
EP-M100T
EP-M100T — компактный SLM 3D-принтер c областью печати 120х120х80 мм. В силу своих небольших размеров и продуманного удобства использования, лучше всего подойдет для работы в стоматологии и других областях медицины, а также для ювелирного дела.
Органы управления с сенсорным экраном расположены на передней панели, но возможно и удаленное управление.
Видео:
Характеристики Shining 3D EP-M100T:
Технология печати: |
SLM |
Электропитание: |
380 В, 2000 Вт |
Размеры, мм: |
940х1300х1980 |
Рабочая температура, ℃: |
15-30 |
Мощность лазера, Вт: |
100-200 |
Рабочая камера, мм: |
120х120х80 |
ПО: |
Eplus 3D |
Системные требования: |
Windows 7 |
Материалы: |
стали и сплавы, в т. |
Толщина слоя, мкм, от: |
15 |
Цена: |
по запросу, поставляется под заказ |
3DLAM
Mid2019
Mid2019 — многоцелевой 3D-принтер по выгодной цене. Принтер предназначен для печати любыми металлическими материалами. На принтере можно напечатать детали высотой до 220 мм. Напечатанные изделия обладают высоким качеством поверхности благодаря тому, что принтер способен печатать с толщиной слоя от 0.1 мм.
Mid2019 работает “из коробки” — в нем уже имеются предустановки для работы с разными материалами, поэтому для начала работы не нужна специальная подготовка. В принтере также предусмотрена возможность удаленного мониторинга и диагностики.
Высокое качество печати деталей с ровными однородными слоями и минимальной пористостью достигается за счет применения высокоточных шарико-винтовых передач.
Характеристики 3DLAM Mid2019:
Технология печати: Электропитание: Размеры, мм: |
SLM 220В / 15A (возможен вариант с 110В) 1470 х 760 х 1890 |
Мощность лазера, Вт: Рабочая камера, мм: ПО: Толщина слоя, мкм, от: Цена: |
300-500 ø150; высота: 220 мм Netfabb Premium или Netfabb Ultimate 100 по запросу |
Mini2019
Mini2019 — 3D-принтер, который обеспечивает экономичную печать металлами за счет мгновенного начала печати, минимального расхода порошка и системы рециркуляции инертного газа, которая позволяет снизить его потребление до 3 литров в минуту.
Принтер относительно небольшого размера 840х865х1850 мм работает прямо “из коробки” и не требует специфических настроек и углубленного знания оборудования.
Наличие абсолютных энкодеров позволяет приостанавливать печать и возобновлять ее через несколько часов или даже дней. Удаленный мониторинг позволяет следить за печатью из любой точки мира, где есть доступ к Интернету.
Принтер печатает детали высокого качества с ровными однородными слоями и практически без пористости.
Характеристики 3DLAM Mini2019:
Технология печати: Электропитание: Размеры, мм: Мощность лазера, Вт: Рабочая камера, мм: ПО: Толщина слоя, мкм, от: Цена: |
SLM 220В / 12A (возможен вариант с 110В) 840 х 865 х 1850 300 Цилиндр: ø90; высота: 100 мм Netfabb Premium или Netfabb Ultimate 100 по запросу |
Farsoon
FS421
3D-принтер Farsoon FS421M — флагманская модель в своем классе. Имеет большую рабочую камеру — 420 x 420 x 420 мм и оснащен мощным лазером в 500 Вт. Система фильтрации защитного газа позволяет печатать детали с высокой плотностью, ровные и гладкие, с минимальной шероховатостью.
Программное обеспечение MakeStar имеет открытый код. Принтер Farsoon FS421M работает с материалами разных производителей: алюминием, кобальт-хромом, инструментальной и нержавеющей сталью, титаном и другими.
Характеристики Farsoon FS421M:
Размеры, мм Масса, кг Программное обеспечение |
2700 x 1290 x 2290 3450 Farsoon MakeStar |
Рабочая камера Технология печати Толщина слоя от |
420 x 420 x 420 мм SLM 20 мкм |
Поддерживаемые материалы Стоимость |
AlSi10Mg, Ti6Al4V, нержавеющая и инструментальная сталь, кобальт-хром, Ti-6Al-4V по запросу, поставляется под заказ |
FS121M
Еще один 3D-принтер для печати металлами от Farsoon, модель FS121M, имеет вместительную рабочую зону и оснащен волоконным лазером мощностью 200 Вт.
Система фильтрации защитного газа позволяет добиваться гладких деталей с наименьшей шероховатостью и высокой плотностью.
Farsoon предоставляет свободу использования своей продукции, как в плане совместимости с различным ПО, так и в плане выбора материалов для печати.
Характеристики Farsoon FS121M:
Размеры, мм Масса, кг Программное обеспечение |
1000 x 780 x 1700 700 Farsoon MakeStar |
Рабочая камера Технология печати Толщина слоя от Поддерживаемые материалы Стоимость |
120 x 120 x 100 мм SLM 20 мкм AlSi10Mg, Ti6Al4V, нержавеющая и инструментальная сталь, кобальт-хром, Ti-6Al-4V по запросу, поставляется под заказ |
FS271M
Как и у предыдущих моделей, у 3D-принтера Farsoon FS271M большая рабочая зона для печати крупногабаритных деталей.
Благодаря волоконному лазеру мощностью 500 Вт и высокоточным алгоритмам сканирования, принтер отвечает самым высоким требованиям клиентов к производительности и качеству получаемых изделий. Farsoon FS271M подходит для изготовления деталей для аэрокосмической, автомобильной промышленности и медицинской сферы.
Компания Farsoon использует высококачественные комплектующие, новейшие системы безопасности подачи инертного газа, защитные фильтры, что обеспечивает бесперебойную и долгосрочную эксплуатацию.
Характеристики Farsoon FS271M:
Размеры, мм Масса, кг Программное обеспечение |
1750 х 1430 х 1860 2033 Farsoon MakeStar |
Рабочая камера Технология печати Толщина слоя от |
275 х 275 х 340 мм SLM 20 мкм |
Поддерживаемые материалы |
FS 316L, FS 17-4PH, FS 15-5PH, FS 420, FS 18Ni300, FS AlSi10Mg, FS TA15, FS CoCrMoW, FS CoCrMo, FS Ti6Al4V, FS IN625, FS IN718, FS Gh4536, FS CuSn10 и аналоги других производителей |
Стоимость |
по запросу, поставляется под заказ |
FS301M
Высокопроизводительная модель FS301M оснащена двумя лазерами. Оба лазера могут охватывать всю зону сканирования или быть настроены точечно для построения нескольких моделей одновременно. Герметичность конструкции обеспечивает точный контроль за содержанием кислорода во время печати. Благодаря этому достигается однородность порошка, которая влияет на качество напечатанных деталей.
Принтер оснащен встроенной станцией загрузки порошка. Контейнер с материалом используется во время загрузки, разгрузки и просеивания, для удобства переработки порошка и транспортировки между станциями. Автоматическое выравнивание платформы и усовершенствованные системы контроля обеспечивают надежную работу устройства и высококачественные печатные изделия.
Характеристики Farsoon FS301M:
Размеры, мм Масса, кг Программное обеспечение Рабочая камера Технология печати Толщина слоя от Поддерживаемые материалы Стоимость |
2350 х 1550 х 2200 2800 Farsoon MakeStar,BuildStar 305 х 305 х 400 мм SLM 10-20 мкм AlSi10Mg, Ti6Al4V, 316L по запросу, поставляется под заказ |
3D Systems
3D Systems ProX DMP 300
ProX DMP 300 от 3D Systems — еще одна популярная 3D-система печати металлами. Он имеет большую область печати 250 x 250 x 330 мм и предназначен для увеличения скорости производства и сокращения отходов материала. Ключевым удобством с этим 3D-принтером является автоматизированная система загрузки и переработки материалов.
Видео:
Принтер поставляется с запатентованным 3DSystems программным обеспечением 3DXpert.
Благодаря проприетарной системе наплавления, ProXDMP 300 может печатать материал под углом до 20° без поддержки. Меньшее количество поддержек и улучшенное качество отпечатанной поверхности ведут к уменьшению затрат на пост-обработку и материалы, следовательно, экономится время и финансы.
Характеристики ProX DMP 300:
Технология печати |
DMLS |
Страна производитель |
США |
Диапазон толщины слоя, мкм |
10-50 |
Разрешение, мкм |
x=100, y=100, z=20 |
Рабочая камера, мм |
250 x 250 x 300 |
Мощность лазера, Вт |
500 |
Длина волны лазера, nm |
1070 |
Тип лазера |
Волоконный |
Поддерживаемые материалы |
стали и сплавы, керамические материалы |
Поддерживаемые форматы файлов |
STL, IGES, STEP |
Размеры, мм |
2400x2200x2400 |
Вес, кг |
5000 |
Цена |
по запросу, предзаказ |
ИЛИСТ
Установка прямого лазерного выращивания ИЛИСТ-L
Установка прямого лазерного выращивания ИЛИСТ-L была разработана в Институте лазерных и сварочных технологий (ИЛИСТ).
ИЛИСТ-L — это высокопроизводительный промышленный комплекс, которой представляет собой печатающий металлом принтер с функцией лазерной сварки. Комплекс работает как в ручном, так и в автоматическом режиме.
Данный комплекс можно использовать в связке с промышленным роботом. Рабочая камера большого объема позволяет работать с крупногабаритными изделиями.
В комплексе имеется дверь с просветом, большое смотровое окно и камера для видеонаблюдения за рабочей зоной.
ПО собственной разработки обеспечивает высокую эффективность оборудования и контроль технологического процесса на всех стадиях производства.
Характеристики Установки прямого лазерного выращивания ИЛИСТ-L:
Технология печати Страна производитель Точность печати Мощность лазера Потребляемая мощность Рабочая камера Максимальная грузоподъемность, кг Цена: |
LMD Россия 100 мкм 3 кВт; макс 6 кВт 28 кВт 2800 х 2200 х 2380 мм 500 по запросу |
На сей день не существует печатающего металлом 3D-принтера, который можно было бы поставить в городской квартире — все они имеют свои требования к эксплуатации, которые этому препятствуют.
Но можно назвать несколько аппаратов, которые вполне подойдут для небольшой мастерской в гараже или подвале частного дома.
DESKTOP METAL Studio System
Видео:
Технология печати Desktop Metal Studio называется Bound Metal Deposition™ — “размещение связанного металла”. По сути технология очень похожа на FDM, главное отличие в материале — в его составе частицы металла, связанные восковыми и синтетическими составляющими.
Поддержки легко удаляются вручную. После печати готовые детали помещаются в дебайндер — камеру промывки, где из них вымываются связующие вещества, а затем запекаются в печи при температуре до до 1400°C.
Дебайндер и печь также поставляются производителем принтера.
Материалы печати, поставляемые производителем в картриджах: несколько марок нержавеющей стали, медь, Inconel.
Характеристики DESKTOP METAL Studio System:
Технология печати: |
BMD |
Размеры, мм: |
830 x 530 x 950 |
Вес, кг: |
97 |
Программное обеспечение: |
DM Cloud |
Максимальный вес готового изделия, кг: |
10 |
Максимальный размер заготовки, мм: |
255 x 17 x 17 |
Подогреваемая платформа: |
да |
Рабочая камера, мм: |
305 x 205 x 205 |
Температура печатного стола: |
70°C |
Толщина слоя, от, мкм: |
50 |
Диаметр сопла, мм: |
0,4 |
Количество печатающих головок: |
2 |
Скорость печати: |
16 см3/ч |
Цена: |
поставляется по предзаказу |
Но если 3D-принтер для печати металлом нужен вам для работы, а не для испытания себя в качестве инженера-изобретателя, лучше приобрести зарекомендовавшее себя устройство из перечисленных выше.
Вот основные преимущества и недостатки процессов 3D-печати металлами:
Плюсы
-
3D-печать металлами используются для производства деталей со сложной геометрией, которые традиционные производственные методы не могут произвести.
-
3D-печатные детали непрерывно оптимизируются для улучшения производительности печати, сводя к минимуму их массу и общее количество компонентов в сборке.
-
3D-печатные детали обладают отличными физическими свойствами, а доступный диапазон материалов включает в себя сложные для обработки традиционными методами материалы, такие как металлические суперсплавы.
Минусы
-
Материальные и производственные затраты, связанные с 3D-печатью металлами, высоки, поэтому эти технологии не подходят для деталей, которые могут быть легко изготовлены с помощью традиционных методов.
-
Область построения систем 3D-печати металлами ограничена, так как требуются определенные условия производства и контроль процесса.
-
Уже существующие конструкции деталей могут не подходить для 3D-печати металлами и могут потребовать изменений.
Основные характеристики систем SLM и DMLS приведены в таблице ниже:
3D-печать металлами (SLM / DMLS) |
|
Материалы |
Металлы и металлические сплавы (алюминий, сталь, титан и т. д.) |
Точность размеров |
± 0,1 мм |
Стандартный размер печати |
250 x 150 x 150 мм (до 500 x 280 x 360 мм) |
Толщина слоя |
20 – 50 мкм |
Область поддержки |
Всегда требуется |
Выводы
3D-печать металлом может применяться в производстве деталей различных устройств любого назначения — создание деталей с ее помощью происходит быстрее и стоит зачастую дешевле.
Не применима она лишь там, где детали простых форм, не требующие всех возможностей 3D-печати, производятся по традиционным технологиям в массовом порядке, что экономически более целесообразно.
Средняя стоимость 3D-принтера по металлу и самого техпроцесса на единицу детали пока выше, чем у большинства традиционных станков обрабатывающих детали сопоставимых размеров.
Везде же, где требуется изготовление уникальных или малосерийных деталей, 3D-печать металлами и сплавами уже на голову обошла традиционных соперников в скорости и себестоимости производства, а в некоторых случаях и в качестве.
Свяжитесь со специалистами Top 3D Shop, чтобы подобрать и купить 3D-принтер для печати металлом для своего производства, с учетом всех требований и специфики производимых деталей.
Узнайте больше о возможностях усовершенствовать ваше производство интеграцией нового оборудования:
Точная 3D печать металлом на заказ в Sprint 3D
3D печать металлом – аддитивное производство металлических изделий, которое по праву является одним из наиболее перспективных и стремительно развивающихся направлений в трехмерной печати как таковой. Сама технология берет свое начало еще с обычного спекания материалов, применяемого в порошковой металлургии. Но сейчас она стала более совершенной, точной и быстрой. И сегодня компания SPRINT3D предлагает вам печать металлом на 3D принтере на действительно выгодных условиях. Но для начала – немного информации о самом производственном процессе и его возможностях.
Технология селективного лазерного сплавления
SLM или технология селективного сплавления – это тип прямой печати металлом, при котором достигается плотность 99,5%. Разница особенно ощутима, если сравнивать с моделями, полученными обычным литьем. Достигается такой показатель благодаря внедрению новейших технологий именно в аппаратной части:
- Применение специальных роликов для утрамбовки порошков и, как следствие, возможность использования порошков с размером частиц от 5 мкм.
- Повышение насыпной плотности, способствующее уплотнению конечных изделий.
- Создание разреженной атмосферы инертных газов, при которой достигается максимальная чистота материала, отсутствует окисление и исключаются риски попадания сторонних химических соединений в состав.
Но самое главное – современный 3D принтер для печати металлом позволяет легко подобрать индивидуальную конфигурацию для печати конкретным металлическим порошком. Таким образом даже с недорогим материалом можно получить первоклассный результат. Но только при условии использовании качественного современного оборудования. И здесь мы тоже готовы вас удивить!
3D-печать металлом В SPRINT 3D
Установки для 3D печати металлом, которые мы используем
Качество производства – ключевое требование, которое мы ставим перед собой. Поэтому в работе используем только профессиональное оборудование, обладающие широкими возможностями для печати металлом. Рассмотрим подробнее каждую из производственных установок.
Производственная установка SLM 280HL
SLM 280HL – разработка германской компании SLM Solutions GmbH, использующая технологию послойного лазерного плавления порошковых металлических материалов. Установка оснащена большой рабочей камерой и позволяет создавать 3D объекты размерами 280х280х350 мм. Среди главных преимуществ печати данной установкой можно выделить:
- Малую минимальную толщину наносимого слоя – 20 мкм.
- Заполнение рабочей камеры инертным газом, что позволяет работать с различными реактивными металлами.
- Скорость печати составляет до 35 см/час.
- Толщина слоя построения – 30 и 50 мкм.
- Мощность – 400 Вт.
Отдельно отметим запатентованную систему подачи порошкового материала, благодаря которой скорость печати значительно выше, чем на большинстве производственных установок в той же ценовой категории. В производстве мы используем следующие материалы:
- Нержавеющая сталь (отечественная 07Х18Н12М2 (Полема) и импортная 316L).
- Инструментальная сталь (импортная 1.2709).
- Жаропрочные сплавы 08ХН53БМТЮ (аналог Inconel 718, про-во Полема) и ЭП 741 (производства ВИЛС).
- Кобальт-Хром (COCR)
3D-принтер SLM 280HL может использоваться для создания разного рода металлических компонентов, прототипов и конечных изделий. При необходимости мы можем обеспечить мелкосерийное производство.
Производственная установка ProX 100
ProX 100 – компактная установка для 3D печати металлом, разработанная американской компанией 3D Systems. Она работает по технологии прямого лазерного спекания, благодаря чему обеспечивает высокую скорость и точность производства. Среди основных характеристик стоит выделить:
- Размер рабочей камеры – 100х100х80 мм.
- Толщина слоя построения – 20 и 30 мкм.
- Мощность – 50 Вт.
ProX 100 позволяет создавать прототипы, которые невозможно разработать стандартными методами, обеспечивает короткие сроки изготовления, гарантирует отсутствие пористости материала и высокую плотность деталей. Кроме того, отметим стандартизированное качество всех изделий вне зависимости от их структуры. На данный момент модель активно используется в стоматологии при создании высокоточных протезов, но нашла широкое применение и в других отраслях:
- Производство двигателей и отдельных их деталей.
- Разработка медтехники.
- Печать ювелирных изделий и даже предметов современного искусства.
В печати мы используем сплав кобальт-хром КХ28М6 (производство Полема), изначально разработанный для аддитивных технологий при создании эндопротезов.
3D печать металлом – применение в настоящее время
Многие специалисты утверждают, что 3D печать как таковая еще полностью не раскрыла свой потенциал. К примеру, Илон Маск планирует использовать технологию в колонизации Марса для строительства административных и жилых зданий, оборудования и техники прямо на месте. И это вполне реально, ведь уже сейчас технология трехмерной печати металлом активно применяется в различных отраслях:
- В медицине: изготовление медицинских имплантов, протезов, коронок, постов и т.д. Высокая точность производства и относительно доступная цена сделали 3D печать очень актуальной в данной отрасли.
- В ювелирном деле: многие из ювелирных компаний используют технологию 3D печати для изготовления форм и восковок, а также непосредственно создания ювелирной продукции. К примеру, печать титаном позволяет создавать изделия, которые ранее представлялись невозможными.
- В машинной и даже аэрокосмической отраслях: BMW, Audi, FCA и другие компании не первый год используют 3D печать металлом в прототипировании и всерьез рассматривают ее использование в серийном производстве. А итальянская компания Ge-AvioAero уже сейчас печатает компоненты для реактивных двигателей LEAP на 3D принтерах.
И это лишь малая часть того, что можно создавать на современном оборудовании. Практически все металлические изделия, которые вам необходимы, можно создать при помощи технологии 3D печати металлом. И если данная услуга актуальна для вас, обратитесь в SPRINT3D. Мы возьмемся за работу любой сложности и объемов. А главное – предоставим первоклассный результат!
Будущее уже здесь!
Вас может заинтересовать
Как работают 3D принтеры по металлу.
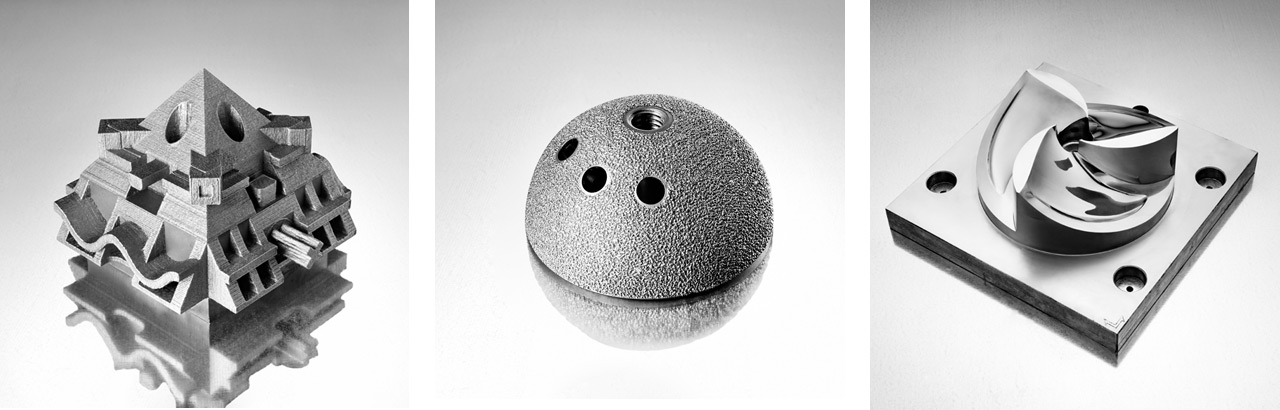
3D печать металлами. Аддитивные технологии.
SLM или DMLS: в чем разница?
Всем привет, Друзья! С Вами 3DTool!
Каталог 3D принтеров по металлу BLT
Селективное лазерное плавление (SLM) и прямое лазерное спекание металла (DMLS) — это два процесса аддитивного производства, которые принадлежат к семейству 3D-печати, с использованием метода порошкового наслоения. Две этих технологии имеют много общего: обе используют лазер для выборочного плавления (или расплавления) частиц металлического порошка, связывая их вместе и создавая модель слой за слоем. Кроме того, материалы, используемые в обоих процессах, являются металлами в гранулированной форме.
Различия между SLM и DMLS сводятся к основам процесса связывания частиц: SLM использует металлические порошки с одной температурой плавления и полностью плавит частицы, тогда как в DMLS порошок состоит из материалов с переменными точками плавления.
В частности:
SLM производит детали из одного металла, в то время как DMLS производит детали из металлических сплавов.
И SLM, и DMLS технологии используются в промышленности для создания конечных инженерных продуктов. В этой статье мы будем использовать термин «металлическая 3D печать» для обобщения 2-х технологий. Так же опишем основные механизмы процесса изготовления, которые необходимы инженерам для понимания преимуществ и недостатков этих технологий.
Существуют и другие технологические процессы для производства плотных металлических деталей, такие как электронно-лучевое плавление (EBM) и ультразвуковое аддитивное производство (UAM).

Как работает 3D печать металлом? Основной процесс изготовления для SLM и DMLS очень похожи.
1. Камера, в которой происходит печать, сначала заполняется инертным газом (например, аргоном), чтобы минимизировать окисление металлического порошка. Затем она нагревается до оптимальной рабочей температуры.
2. Слой порошка распределяется по платформе, мощный лазер делает проходы по заданной траектории в программе, сплавляя металлические частицы вместе и создавая следующий слой.
3. Когда процесс спекания завершен, платформа перемещается вниз на 1 слой. Далее наносится еще один тонкий слой металлического порошка. Процесс повторяется до тех пор, пока печать всей модели не будет завершена.
Когда процесс печати завершен, металлический порошок уже имеет прочные связи в структуре. В отличие от процесса SLS, детали прикрепляются к платформе через опорные конструкции. Опора в 3D-печати металлом, создаётся из того же материала, что базовая деталь. Это условие необходимо для уменьшения деформаций, которые могут возникнуть из-за высоких температур обработки.
Когда камера 3D принтера охлаждается до комнатной температуры, излишки порошка удаляются вручную, например щеткой. Затем детали как правило подвергаются термообработке, пока они еще прикреплены к платформе. Делается это для снятия любых остаточных напряжений. Далее с ними можно проводить дальнейшую обработку. Снятие детали с платформы происходит по средством спиливания.
В SLM и DMLS почти все параметры процесса устанавливаются производителем.

Базовый размер области печати на металлических 3D принтерах составляет 200 x 150 x 150 мм, но бывают и более большие размеры рабочего поля. Точность печати составляет от 50 — 100 микрон. По состоянию на 2020 год, стоимость 3D принтеров по металлу начинается от 150 000 долларов США. Например наша компания предлагает 3D принтеры по металлу от BLT.
3D принтеры по металлу, могут использоваться для мелкосерийного производства, но возможности таких систем в 3D-печати, больше напоминают возможности серийного производства на машинах FDM или SLA.
Металлический порошок в SLM и DMLS пригоден для вторичной переработки: обычно расходуется менее 5%. После каждого отпечатка неиспользованный порошок собирают и просеивают, а затем доливают свежим материалом до уровня, необходимого для следующего изготовления.
Отходы в металлической печати, представляют из себя поддержки (опорные конструкции, без которых не удастся добиться успешного результата). При слишком большом обилии поддержек на изготавливаемых деталях, соответственно будет расти и стоимость всего производства.
Адгезия между слоями.
3D печать металлом на 3D принтерах BLT
Металлические детали SLM и DMLS обладают практически изотропными механическими и термическими свойствами. Они твердые и имеют очень небольшую внутреннюю пористость (менее 0,2 % в состоянии после 3D печати и практически отсутствуют после обработки).
Металлические печатные детали имеют более высокую прочность и твердость и часто являются более гибкими, чем детали, изготовленные традиционным способом. Тем не менее, такой металл быстрее становится «уставшим». Структура поддержки 3D модели и ориентация детали на рабочей платформе.
Опорные конструкции всегда требуются при печати металлом, из-за очень высокой температуры обработки.
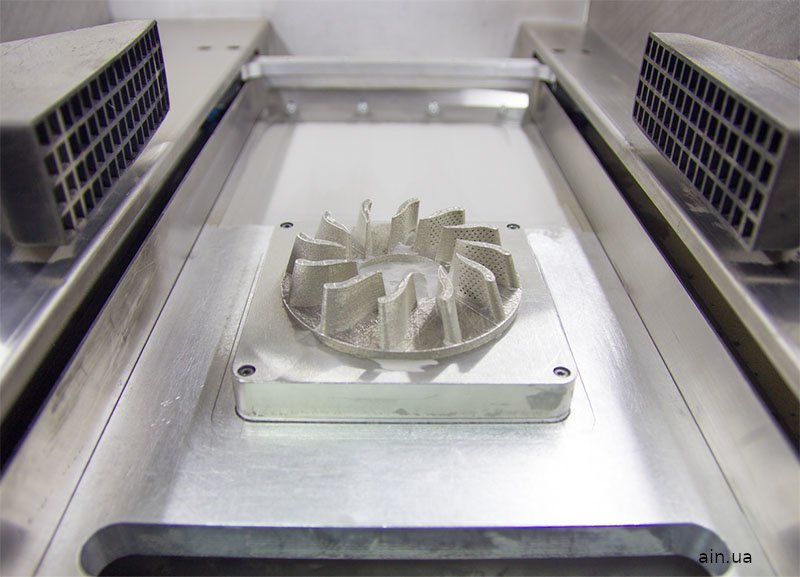
Поддержки в металлической 3D печати выполняют 3 функции:
• Они делают основание для создания первого слоя детали.
• Они закрепляют деталь на платформе и предотвращают её деформацию.
• Они действуют как теплоотвод, отводя тепло от модели.
Детали часто ориентированы под углом. Однако это увеличит и объем необходимых поддержек, время печати, и в конечном итоге общие затраты.
Деформация также может быть сведена к минимуму с помощью шаблонов лазерного спекания. Эта стратегия предотвращает накопление остаточных напряжений в любом конкретном направлении и добавляет характерную текстуру поверхности детали.
Поскольку стоимость металлической печати очень большая, для прогнозирования поведения детали во время обработки часто используются программные симуляторы. Это алгоритмы оптимизации топологии в прочем используются не только для увеличения механических характеристик и создания облегченных частей, но и для того, чтобы свести к минимуму потребности в поддержках и вероятности искривления детали.
Полые секции и легкие конструкции.
Пример печати на 3D принтере BLT
В отличие от процессов плавления с полимерным порошком, таких как SLS, большие полые секции обычно не используются в металлической печати, так как поддержки будет очень сложно удалить, если вообще возможно.
Для внутренних каналов больше, чем Ø 8 мм, рекомендуется использовать алмазные или каплевидные поперечные сечения вместо круглых, так как они не требуют построения поддержек. Более подробные рекомендации по проектированию SLM и DMLS можно найти в других статьях посвященных данной тематике.
В качестве альтернативы полым секциям, детали могут быть выполнены с оболочкой и сердечниками, которые в свою очередь обрабатываются с использованием различной мощности лазера и скорости его проходов, что приводит к различным свойствам материала. Использование оболочки и сердечников очень полезно при изготовлении деталей с большим сплошным сечением, поскольку это значительно сокращает время печати и уменьшает вероятность деформации.
Использование решетчатой структуры является распространенной стратегией в 3D-печати металлом, для уменьшения веса детали. Алгоритмы оптимизации топологии также могут помочь в разработке органичных легких форм.
Расходные материалы для 3D печати металлом.Технологии SLM и DMLS могут производить детали из широкого спектра металлов и металлических сплавов, включая алюминий, нержавеющую сталь, титан, кобальт, хром и инконель. Эти материалы обеспечивают потребности большинства промышленных применений, от аэрокосмической отрасли до медицинской. Драгоценные металлы, такие как золото, платина, палладий и серебро, также могут быть обработаны, но их применение носит незначительный характер и в основном ограничивается изготовлением ювелирных изделий.
Стоимость металлического порошка очень высока. Например, килограмм порошка из нержавеющей стали 316 стоит примерно 350-450 долларов. По этой причине минимизация объема детали и необходимость поддержек является ключом к поддержанию оптимальной стоимости производства.
Основным преимуществом металлической 3D-печати является ее совместимость с высокопрочными материалами, такими как никелевые или кобальт-хромовые супер сплавы, которые очень трудно обрабатывать традиционными методами. За счет использования металлической 3D-печати для создания детали практически чистой формы — можно достичь значительной экономии средств и времени. В последствии такая деталь может быть подвергнута обработке до очень высокого качества поверхности.
Постобработка металла.
Различные методы пост. обработки используются для улучшения механических свойств, точности и внешнего вида металлических печатных изделий.
Обязательные этапы последующей обработки включают удаление рассыпного порошка и опорных конструкций, в то время как термическая обработка (термический отжиг) обычно используется для снятия остаточных напряжений и улучшения механических свойств детали.
Обработка на станках ЧПУ может быть использована для критически важных элементов (таких как отверстия или резьбы). Пескоструйная обработка, металлизация, полировка и микрообработка могут улучшить качество поверхности и усталостную прочность металлической печатной детали.
Преимущества и недостатки металлической 3D печати.Плюсы:
1. 3D печать с использованием металла, может быть использована для изготовления сложных деталей на заказ, с геометрией, которую традиционные методы производства не смогут обеспечить.
2. Металлические 3D печатные детали могут быть оптимизированы, чтобы увеличить их производительность при минимальном весе.
3. Металлические 3D-печатные детали имеют отличные физические свойства, 3D принтеры по металлу могут печатать большим перечнем металлов и сплавов. Включают в себя трудно обрабатываемые материалы и металлические суперсплавы.
Минусы:
1. Затраты на изготовление, связанные с металлической 3D-печатью, высоки. Стоимость расходного материала от 500$ за 1 кг.
2. Размер рабочей области в 3D принтерах по металлу ограничен.
• 3D печать металлом наиболее подходит для сложных, штучных деталей, которые сложно или очень дорого изготовить традиционными методами, например на станке ЧПУ.
• Уменьшение потребностей в построении поддержек, значительно снизит стоимость печати при помощи металла.
• Металлические 3D-печатные детали имеют отличные механические свойства и могут быть изготовлены из широкого спектра инженерных материалов, включая суперсплавы.
А на этом у нас Все! Надеемся, статья была для Вас полезна.
Каталог 3D принтеров по металлу BLT
Приобрести 3d-принтеры по металлу, а так же любые другие 3d-принтеры и ЧПУ станки, вы можете у нас, связавшись с нами:
• По электронной почте: [email protected]
• По телефону: 8(800)775-86-69
• Или на нашем сайте: http://3dtool.ru
Так же, не забывайте подписываться на наш YouTube канал:
Подписывайтесь на наши группы в соц.сетях:
ВКонтакте
3D-печать металлом, металлическая 3D-печать
Только у нас самый большой выбор металлов для 3D-печати!
Металлы для 3D-печати
Металлическая 3D-печать используется в том случае, когда главными качествами изделия должны быть прочность, устойчивость и надежность, но самое важное — это отсутствие альтернативы в способе производства, когда у изделия сложная геометрия. В связи с этим, во всем мире металлическая печать используется в биоинженерии, аэронавтике, космонавтике, архитектуре, протезировании и так далее.
Алюминиевый сплав
Прочный, твердый. Может быть подвергнут постобработке. Детали из этого материала обладают хорошими динамическими качествами.
Нержавеющая сталь
Высокая устойчивость к коррозии, подверженность постобработке. Подходит для инжиниринговых целей, а также для создания изделий бытового потребительского назначения.
Биосовместимый титан
Легкий, устойчив к коррозии. Имеет низкий удельный вес. Биосовместим. Отлично подходит для инжиниринговых целей.
Кобальт-хром-молибден
Прочный, жесткий, устойчивый к коррозии, термостойкий. Стерилизуем, подходит для биомедицинский применений. Может быть подвержен постобработке.
Мартенситно-стареющая сталь
Жесткий, прочный материал, обладающий хорошими механическими свойствами. Подвержен постобработке, термообработке, упрочнению старением. Отлично подходит для применения в сфере инструментальной оснастки.
Нержавеющая сталь
Жесткий, пластичный материал, обладает высокой коррозионной устойчивостью. Может быть подвергнут постобработке. Применяется в инжиниринговых целях (прототипирование).
Порошок на основе бронзы
Отличается высокой детализацией и высоким качеством поверхности. Подвергается дробеструйной обработке и полировке. Гарантирует высокую точность напечатанных деталей. Подвержен постобработке.
Нержавеющая сталь
Прочный, обладает высокой коррозионной устойчивостью, подвержен дополнительной термической обработке. Может быть подвергнут постобработке. Применяется в инжиниринговых целях (прототипирование).
Стоимость 3D-печати металлами
Стоимость печати зависит от модели, т.к. при печати используются поддерживающие структуры. Количество поддержек и выбранный металл влияют на цену. Чтобы посчитать стоимость 3D-печати вашего изделия, свяжитесь с нами, пожалуйста, по электронной почте [email protected], по телефону 8 800 550 40 45 или по форме обратной связи:
Политика конфиденциальности и Пользовательское соглашение
Технология 3D-печати металлами
Мы осуществляем 3D-печать металлом по технологии Direct Metal Laser Sintering или прямое лазерное спекание металлов. Технология печати основана на затекании образовавшегося расплава-связки под действием капиллярных сил в пустоты между частицами. Для успешного выполнения процесса в порошковую смесь добавляют соединения с фосфором. Они снижают поверхностное натяжение, вязкость и степень окисления расплава, таким образом, улучшая смачиваемость. Порошок, используемый в качестве связки, обычно имеет меньший размер, чем порошок основы, поскольку это позволяет увеличить насыпную плотность порошковой смеси и ускорить процесс образования расплава.
Твердость металлических изделий,
напечатанных на 3D-принтере
Механические свойства деталей из разных сплавов
[/mp_span] [/mp_row]
3D-печать металлами — технологии и принтеры / Блог компании Top 3D Shop / Хабр
3D-печать металлом становится все более популярной. И это не удивляет: каждый металлический материал для печати предлагает уникальное сочетание практических и эстетических свойств для того, чтобы удовлетворить требования предъявляемые к различным продуктам, будь то прототипы, миниатюры, украшения, функциональные детали или даже кухонные принадлежности.
Причины печатать металлами настолько веские, что 3D-печать металлами уже внедряется в серийное производство. На самом деле, некоторые 3D-печатные детали уже догнали, а какие-то и превзошли своими свойствами те, что производятся традиционными методами.
Традиционное производство из металлов и пластиков очень расточительно — в авиапромышленности, например, до 90% материалов уходит в отходы. Выход продукции, в некоторых отраслях, составляет не более 30% от использованного материала.
3D-печать металлами потребляет меньше энергии и сокращает количество отходов до минимума. Кроме того, готовое 3D-печатное изделие может быть до 60% легче, по сравнению с фрезерованной или литой деталью. Одна лишь авиационная промышленность сэкономит миллиарды долларов на топливе — за счет снижения веса конструкций. А ведь прочность и легкость нужны и в других отраслях. Да и экономичность тоже.
3D-печать металлом дома
Что можно сделать, если появилось желание попробовать 3D-печать металлом в домашних условиях? Для печати металлом необходимы чрезвычайно высокие температуры, вряд ли вы сможете использовать обычный FDM 3D-принтер для этого, по крайней мере пока. Ситуация может измениться через несколько лет, но сейчас домашней 3D-технике это недоступно.
Если вы хотите сделать выглядящие металлическими распечатки у себя дома, лучший вариант — использование пластика содержащего частицы металла.
Такого например, как Colorfabb Bronzefill или Bestfilament Bronze.
Эти филаменты содержат значительный процент металлических порошков, но и достаточно пластика — для печати при низкой температуре любым 3D-принтером. В то же время, они содержат достаточное количество металла, чтобы соответственно выглядеть, ощущаться и иметь вес близкий к весу металлического предмета.
Изделия из филамента содержащего железо даже покрываются ржавчиной в определенных условиях, что добавляет правдоподобности, а вот проржаветь насквозь и испортиться от этого не смогут — и в этом их преимущество перед настоящими металлическими предметами.
Плюсы таких материалов:
- Уникальный внешний вид распечаток
- Идеально подходит для бижутерии, статуэток, предметов домашнего обихода и декора
- Высокая прочность
- Очень малая усадка во время охлаждения
- Подогреваемый стол не обязателен
Минусы:
- Низкая гибкость изделий, зависит от конструкции распечатки
- Не считается безопасным при контакте с пищей
- Требует тонкой настройки температуры сопла и скорости подачи филамента
- Необходима постобработка изделий — шлифовка, полировка
- Быстрый износ сопла экструдера — филамент с металлом очень абразивен, по сравнению с обычными материалами
Общий температурный диапазон печати обычно составляет 195°C — 220°C.
3D-печать металлом в промышленности
Если вы хотите приобрести 3D-принтер печатающий настоящим металлом, для использования на предприятии, то тут для вас две новости — хорошая и плохая.
Хорошая новость состоит в том, что их ассортимент достаточно широк и продолжает расширяться — можно будет выбрать такой аппарат, который соответствует любым техническим требованиям. Далее в статье можно убедиться в этом.
Плохая же новость одна — цены. Стоимость профессиональных печатающих металлом принтеров начинается где-то от $200000 и растет до бесконечности. Кроме того, даже если вы выберете и приобретете самый недорогой из них, отдельным ударом станет покупка расходников, плановое обслуживание с заменой узлов, ремонт. Не забываем и о персонале, и расходах на постобработку изделий. А на стадии подготовки к печати понадобится специальное ПО и умеющие обращаться с ним люди.
Если вы готовы ко всем этим тратам и трудностям — читайте дальше, мы представим несколько очень интересных образцов.
https://youtu.be/20R9nItDmPY
3D-печать металлом — применение
В некоторых промышленных секторах уже используют металлические 3D-принтеры, они стали неотъемлемой частью производственного процесса, о чем обычный потребитель может и не подозревать:
Наиболее распространенным примером являются медицинские импланты и стоматологические коронки, мосты, протезы, которые уже считаются наиболее оптимальным вариантом для пациентов. Причина: Они могут быть быстрее и дешевле изготовлены на 3D-принтере и адаптированы к индивидуальным потребностям каждого пациента.
Второй, столь же часто встречающийся пример: ювелирное дело. Большинство крупных производителей постепенно переходит от 3D-печати форм и восковок к непосредственной 3D-печати металлом, а печать из титана позволяет ювелирам создавать изделия невозможного ранее дизайна.
Кроме того, аэрокосмическая промышленность становится все более и более зависима от 3D-печатных металлических изделий. Ge-AvioAero в Италии — первая в мире полностью 3D-печатная фабрика, которая выпускает компоненты для реактивных двигателей LEAP.
Следующая отрасль использующая 3D-принтеры по металлу — автопром. BMW, Audi, FCA уже серьезно рассматривают применение технологии в серийном производстве, а не только в прототипировании, где они используют 3D-печать уже многие годы.
Казалось бы — зачем изобретать велосипед? Но и здесь 3D-печать металлом нашла применение. Уже несколько лет производители велосипедных компонентов и рам применяют 3D печать. Не только в мире, но и в России это получило распространение. Производитель эксклюзивных велосипедов Triton заканчивает проект с 3D-печатным элементом титановой рамы, это позволило снизить ее вес без ущерба прочности.
Но прежде, чем 3D-печать металлами действительно захватит мир, необходимо будет преодолеть несколько серьезных проблем. В первую очередь — это высокая стоимость и низкая скорость производства больших серий этим методом.
3D-печать металлом — технологии
Многое можно сказать о применении печатающих металлом 3D-принтеров. Есть своя специфика, но основные вопросы такие же, как и с любыми другими 3D-принтерами: программное обеспечение и аппаратные ограничения, оптимизация материалов и печать несколькими материалами. Мы не будем говорить о программном обеспечении много, упомянем лишь, что наиболее крупные издатели, такие как Autodesk, SolidWorks и SolidThinking — все разрабатывают программные продукты для использования в объемной печати металлами, чтобы пользователи могли воплотить в жизнь изделие любой вообразимой формы.
В последнее время появились примеры того, что 3D-детали напечатанные металлом могут быть столь же прочными, как традиционно производимые металлические компоненты, а в некоторых случаях и превосходят их. Созданные с помощью DMLS, изделия имеют механические свойства такие же, как у цельнолитых аналогов.
Посмотрим же на имеющиеся металлические технологии 3D-печати:
Процесс # 1: Послойное сплавление порошка
Процесс 3D-печати металлами, которым наиболее крупные компании пользуются в наши дни, известен как сплавление или спекание порошкового слоя. Это означает, что лазерный или другой высокоэнергетический луч сплавляет в единое целое частицы равномерно распределенного металлического порошка, создавая слои изделия, один за другим.
В мире есть восемь основных производителей 3D-принтеров для печати металлом, большинство из них расположены в Германии. Их технологии идут под аббревиатурой SLM (выборочное лазерное плавление) или DMLS (прямое спекание металла лазером).
Процесс # 2: Binder Jetting
Еще один профессиональный метод с послойным соединением — склеивание частиц металла для последующего обжига в высокотемпературной печи, где частицы сплавляются под давлением, составляя единое металлическое целое. Печатная головка наносит соединительный раствор на порошковую подложку послойно, как обычный принтер на листы бумаги, после чего изделие отправляется в обжиг.
Еще одна похожая, но отличающаяся технология, в основе которой лежит FDM печать — замешивание металлического порошка в металлическую пасту. С помощью пневматической экструзии, 3D-принтер выдавливает ее, подобно тому, как строительный 3D-принтер делает это с цементом, чтобы сформировать 3D-объекты. После того, как нужная форма напечатана, объекты также спекают в печи. Эту технологию использует Mini Metal Maker — возможно, единственный более-менее доступный 3D-принтер для печати металлом ($1600). Прибавьте стоимость небольшой печки для обжига.
Процесс # 3: Наплавление
Можно подумать, что среди технологий печатью металлом отсутствует похожая на обычную FDM, однако, это не совсем так. Вы не сможете плавить металлическую нить в хот-энде своего 3D-принтера, а вот крупные производители владеют такой технологией и пользуются ею. Есть два основных способа печатать цельнометаллическим материалом.
Один из них называется DED (Directed Energy Deposition), или лазерная наплавка. Он использует лазерный луч для сплавления металлического порошка, который медленно высвобождается и осаждается из экструдера, формируя слои объекта с помощью промышленного манипулятора.
Обычно это делается внутри закрытой камеры, однако, на примере компании MX3D, мы видим возможность реализации подобной технологии в сооружении настоящего полноразмерного моста, который должен быть распечатан в 2017 году в Амстердаме.
Другой называется EBM (Electron Beam Manufacturing — производство электронным лучом), это технология формирования слоев из металлического сырья под воздействием мощного электронного луча, с ее помощью создают крупные и очень крупные конструкции. Если вы не работаете в оборонном комплексе РФ или США, то вряд ли увидите эту технологию живьем.
Еще парочка новых, едва появившихся технологий, используемых пока только их создателями, представлена ниже — в разделе о принтерах.
Используемые металлы
Ti — Титан
Чистый титан (Ti64 или TiAl4V) является одним из наиболее часто используемых металлов для 3D-печати, и безусловно — одним из самых универсальных, так как он является одновременно прочным и легким. Он используется как в медицинской промышленности (в персонализированом протезировании), так и в аэрокосмической и автомобильной отрасли (для изготовления деталей и прототипов), и в других областях. Единственная загвоздка — он обладает высокой реакционной способностью, что означает — он может легко взорваться, когда находится в форме порошка, и обязательно должен применяться для печати лишь в среде инертного газа Аргона.
SS — Нержавеющая сталь
Нержавеющая сталь является одним из самых доступных металлов для 3D-печати. В то же время, она очень прочна и может быть использована в широком спектре промышленных и художественных производств. Этот тип стального сплава, содержащий кобальт и никель, обладает высокой упругостью и прочностью на разрыв. 3D-печать нержавейкой используется, в основном, лишь в тяжелой промышленности.
Inconel — Инконель
Инконель — современный суперсплав. Он производится компанией Special Metals Corporation и является запатентованным товарным знаком. Состоит, по большей части, из никеля и хрома, имеет высокую жаропрочность. Используется в нефтяной, химической и аэрокосмической промышленности (например: для создания распределительных форсунок, бортовых “черных ящиков”).
Al — Алюминий
Из-за присущей ему легкости и универсальности, алюминий является очень популярным металлом для применения в 3D-печати. Он используется обычно в виде различных сплавов, составляя их основу. Порошок алюминия взрывоопасен и применяется в печати в среде инертного газа Аргона.
CoCr — Кобальт-хром
Этот металлический сплав имеет очень высокую удельную прочность. Используется как в стоматологии — для 3D-печати зубных коронок, мостов и бюгельных протезов, так и в других областях.
Cu — Медь
За редким исключением, медь и ее сплавы — бронза, латунь — используются для литья с использованием выжигаемых моделей, а не для прямой печати металлом. Это потому, что их свойства далеко не идеальны для применения в промышленной 3D-печати, они чаще используются в декоративно-прикладном искусстве. С большим успехом они добавляются в пластиковый филамент — для 3D-печати на обычных 3D-принтерах.
Fe — Железо
Железо и магнитный железняк также, в основном, используются в качестве добавки к PLA-филаменту. В крупной промышленности чистое железо редко находит применение, а о стали мы написали выше.
Au, Ag — Золото, серебро и другие драгоценные металлы
Большинство сплавляющих слои порошка 3D-принтеров могут работать с драгоценными металлами, такими как золото, серебро и платина. Главная задача при работе с ними — убедиться в оптимальном расходе дорогостоящего материала. Драгоценные металлы применяются в 3D-печати ювелирных и медицинских изделий, а также при производстве электроники.
3D принтеры печатающие металлом
# 1: Sciaky EBAM 300 — титановый прут
Для печати действительно больших металлических конструкций лучшим выбором будет EBAM от Sciaky. Этот аппарат может быть любого размера, на заказ. Он используется, в основном, в аэрокосмической и оборонной промышленности США.
Как серийную модель, Sciaky продает EBAM 300. Он имеет размер рабочей области со сторонами 5791 х 1219 х 1219 мм.
Компания утверждает, что EBAM 300 является одним из самых быстрых коммерчески доступных промышленных 3D-принтеров. Конструкционные элементы самолетов, производство которых, по традиционным технологиям, могло занимать до полугода, теперь печатаются в течение 48 часов.
Уникальная технология Sciaky использует электронно-лучевую пушку высокой мощности для плавки титанового филамента толщиной 3мм, со стандартной скоростью осаждения около 3-9 кг/час.
# 2: Fabrisonic UAM — ультразвуковой
Другой способ 3D-печати больших металлических деталей — Ultrasound Additive Manufacturing Technology (UAM — технология ультразвукового аддитивного производства) от Fabrisonic. Детище Fabrisonic является трехосевым ЧПУ-станком, имеющим дополнительную сварочную головку. Металлические слои сначала разрезают, а затем сваривают друг с другом с помощью ультразвука. Крупнейший 3D-принтер Fabrisonic — “7200”, имеет объем сборки 2 х 2 х 1,5 м.
# 3: Laser XLine 1000 — металлический порошок
Одним из самых крупных, на рынке 3D-принтеров печатающих с помощью металлического порошка, долго являлся XLine 1000 производства Concept Laser. Он имеет область сборки размером 630 х 400 х 500 мм, а места занимает как небольшой дом.
Изготовившая его немецкая компания, которая является одним из поставщиков 3D-принтеров для аэрокосмических компаний-гигантов, таких как Airbus, недавно представила новый принтер — XLine 2000.
2000 имеет два лазера и еще больший объем сборки — 800 х 400 х 500 мм. Эта машина, которая использует патентованную технологию LaserCUSING (тип селективного лазерного плавления), может создавать объекты из сплавов стали, алюминия, никеля, титана, драгоценных металлов и из некоторых чистых материалов (титана и сортовых сталей.)
Подобные машины есть у всех основных игроков на рынке 3D-печати металлом: у EOS, SLM, Renishaw, Realizer и 3D Systems, а также у Shining 3D — стремительно развивающейся компании из Китая.
# 4: M Line Factory — модульная 3D-фабрика
Рабочий объем: 398,78 х 398,78 х 424,18 мм
От 1 до 4 лазеров, 400 — 1000 Вт мощности каждый.
Концепция M Line Factory основана на принципах автоматизации и взаимодействия.
M Line Factory, от той же Concept Laser, и работающий по той же технологии, делает акцент не на размере рабочей области, а на удобстве производства — он представляет собой аппарат модульной архитектуры, который разделяет производство на отдельные процессы таким образом, что эти процессы могут происходить одновременно, а не последовательно.
Эта новая архитектура состоит из 2 независимых узлов машины:
M Line Factory PRD (Production Unit — производственная единица)
Production Unit состоит из 3-х типов модулей: модуль дозирования, печатный модуль и модуль переполнения (лоток для готовой продукции). Все они могут быть индивидуально активированы и не образуют одну непрерывную единицу аппаратуры. Эти модули транспортируются через систему туннелей внутри машины. Например, когда новый порошок подается, пустой модуль хранения порошка может быть автоматически заменен на новый, без прерывания процесса печати. Готовые детали могут быть перемещены за пределы машины и немедленно автоматически заменяются следующими заданиями.
M Line Factory PCG (Processing Unit — процессинговая единица)
Это независимый блок обработки данных, который имеет встроенную станцию просеивания и подготовки порошка. Распаковка, подготовка к следующему заданию печати и просеивание происходят в замкнутой системе, без участия оператора.
# 5: ORLAS CREATOR — 3D-принтер готовый к работе
Создатели ORLAS CREATOR позиционируют этот 3D-принтер как максимально доступный, простой в обращении и готовый к работе, не требующий установки никаких дополнительных комплектующих и программ сторонних производителей, способный печатать прямо из файла комплектной CAD/CAM их собственной разработки.
Все необходимые компоненты установлены в относительно компактном корпусе, которому необходимо пространство 90х90х200 см. Много места он не займет, хоть и выглядит внушительно, да и весит 350 кг.
Как можно понять из приведенной производителем таблицы, металлический порошок спекается вращающейся лазерной системой, слоями 20-100 мкм толщиной и с размером “пикселя” всего в 40 мкм, в атмосфере азота или аргона. Подключить его можно к обычной бытовой электросети, если ваша проводка выдержит нагрузку в 10 ампер. Что, впрочем, не превышает требований средней стиральной машины.
Мощность лазера — 250 Ватт. Рабочая область составляет цилиндр 100 мм в диаметре и 110 в высоту.
# 6: FormUp 350 — Powder Machine Part Method (PMPM)
FormUp 350, работающий в системе Powder Machine Part Method (PMPM), создан компанией AddUp — совместным проектом Fives и Michelin. Это новейший аппарат для 3D-печати металлами, впервые представленный в ноябре на Formnext2016.
Принцип работы у этого 3D-принтера тот же, что и у приведенных выше коллег, но его главная особенность в другом — она заключается в его включенности в PMPM.
Принтер предназначен именно для промышленного использования, в режиме 24/7, и рассчитан именно на такой темп работы. Система PMPM включает в себя контроль качества всех комплектующих и материалов, на всех стадиях их производства и распространения, что должно гарантировать стабильно высокие показатели качества работы, в чем у Мишлена огромный многолетний опыт.
# 7: XJET — NanoParticle Jetting — струйная печать металлом
Технология впрыска наночастиц предполагает использование специальных герметичных катриджей с раствором, в котором находится взвесь наночастиц металла.
Наночастицы осаждаются и образуют собой материал печатаемого изделия.
Учитывая заявленные особенности технологии (применение металлических частиц наноразмера), несложно поверить создателям аппарата, когда они утверждают о его беспрецедентных точности и разрешении печати.
# 8: VADER Mk1 — MagnetoJet — струйная печать металлом
Технология Зака Вейдера MagnetoJet основана на изучении магнитной гидродинамики, а конкретнее — возможности управлять расплавленным металлом с помощью магнитных полей. Суть разработки в том, что из расплавленного алюминия формируется капля строго контролируемого размера, этими каплями и осуществляется печать.
Размер такой капельки — от 200 до 500 микрон, печать происходит со скоростью 1000 капель в секунду. Рабочая область принтера: 300 мм х 300 мм х 300 мм
Рабочий материал: Алюминий и его сплавы (4043, 6061, 7075). И, пусть пока это только алюминий, но принтер в 2 раза быстрее порошковых и до 10 раз дешевле.
В 2018 году планируется выпуск Mk2, он будет оснащен 10 печатающими головками, что должно дать прирост скорости печати в 30 раз.
# 9: METAL X — ADAM — атомная диффузия
Компания Markforged представила новую технологию 3D-печати металлом — ADAM, и 3D-принтер работающий по этой технологии — Metal X.
ADAM (Atomic Diffusion Additive Manufacturing) — технология атомной диффузии. Печать производится металлическим порошком, где частицы металла покрыты синтетическим связующим веществом, которое удаляется после печати, позволяя металлу соединиться в единое целое.
Главное преимущество технологии — отсутствие необходимости применения сверхвысоких температур непосредственно в процессе печати, а значит — отсутствие ограничений по тугоплавкости используемых для печати материалов. Теоретически, принтер может создавать 3D-модели из сверхпрочных инструментальных сталей — сейчас он уже печатает нержавейкой, а в разработке титан, Инконель и стали D2 и A2.
Технология позволяет создавать детали со сложной внутренней структурой, такой как в пчелиных сотах или в пористых тканях костей, что затруднительно при других технологиях 3D-печати, даже для DMLS.
Размер изделий: до 250мм х 220мм х 200мм. Высота слоя — 50 микрон.
Того гляди, скоро можно будет распечатать высококачественный нож — с нуля, за пару часов, придав ему любой самый замысловатый дизайн.
Хотите больше интересных новостей из мира 3D-технологий?
Подписывайтесь на нас в соц. сетях:
3D-печать металлами
3D-печать металлами можно считать одним из наиболее заманчивых и технологически сложных направлений аддитивного производства. Попытки печати металлами предпринимались с ранних дней развития технологий 3D-печати, но в большинстве случаев упирались в технологическую несовместимость. В этом разделе мы рассмотрим технологии, опробованные для печати как композитными материалами, содержащими металлы, так и чистыми металлами и сплавами.Струйная трехмерная печать (3DP)
Схема работы трехмерных струйных принтеров (3DP)Струйная 3D-печать является не только одним из старейших методов аддитивного производства, но и одним из наиболее успешных в плане использования металлов в качестве расходных материалом. Однако необходимо сразу же пояснить, что это технология позволяет создавать лишь композитные модели ввиду технологических особенностей процесса. Фактически, этот метод позволяет создавать трехмерные модели из любых материалов, которые могут быть переработаны в порошок. Связывание же порошка осуществляется с помощью полимеров. Таким образом, готовые модели нельзя назвать полноценно «металлическими».
В то же время, существует возможность преобразования композитных моделей в цельнометаллические за счет термической обработки с целью выплавки или выжигания связующего материала и спекания металлических частиц. Получаемые таким образом модели не обладают высокой прочностью ввиду пористости. Увеличение прочности возможно за счет пропитки полученной цельнометаллической модели. Например, возможна пропитка стальной модели бронзой с получением более прочной конструкции.
Получаемые подобным образом модели, даже с металлической пропиткой, не используются в качестве механических компонентов ввиду относительно низкой прочности, но активно используются в ювелирной и сувенирной промышленности.
Печать методом ламинирования (LOM)
Схема работы 3D-принтеров, использующих технологию ламинирования (LOM)3D-печать методом ламинирования подразумевает последовательное нанесение тонких листов материала с формированием за счет механической или лазерной резки и склеиванием для получения трехмерной модели.
В качестве расходного материала может использоваться и металлическая фольга.
Получаемые модели не являются полностью металлическими, так как их целостность основана на применении клея, связующего листы расходного материала.
Плюсом же данной технологии является относительная дешевизна производства и высокое визуальное сходство получаемых моделей с цельнометаллическими изделиями. Как правило, этот метод используется для макетирования.
Послойное наплавление (FDM/FFF)
Модель, изготовленная из BronzeFill до и после полировкиНаиболее популярный метод 3D-печати также не обошел стороной попытки использования металлов в качестве расходных материалов. К сожалению, попытки печати чистыми металлами и сплавами на данный момент не привели к значительным успехам. Использование тугоплавких металлов натыкается на вполне предсказуемые проблемы с выбором материалов для конструкции экструдеров, которые, по определению, должны выдерживать еще более высокие температуры.
Печать же легкоплавкими сплавами (например, оловом), возможна, но не дает достаточно качественной отдачи для практического применения.
Таким образом, в последнее время внимание разработчиков расходных материалов переключилось на композитные материалы по аналогии со струйной печатью. Типичным примером служит BronzeFill – композитный материал, состоящий из термопластика (детали не разглашаются, но, по всей видимости, используется PLA-пластик) и бронзового порошка. Получаемые модели имеют высокую визуальную схожесть с натуральной бронзой и даже поддаются шлифовке до глянца. К сожалению, физические и химические свойства готовых изделий ограничены параметрами связующего термопластика, что не позволяет классифицировать такие модели, как цельнометаллические.
Тем не менее, подобные материалы могут получить практическое применение не только в создании макетов, сувениров и предметов искусства, но и в промышленности. Так, эксперименты энтузиастов показали возможность создания проводников и экранирующих материалов с использованием термопластиков с металлическим наполнителем. Развитие этого направления может сделать возможной печать электронных плат.
Выборочное лазерное спекание (SLS) и прямое спекание металлов (DMLS)
Наиболее распространенный метод создания цельнометаллических трехмерных моделей подразумевает использование лазерных установок для спекания частиц металлического порошка. Данная технология именуется «выборочным лазерным спеканием» или SLS. Стоит отметить, что SLS используется не только для работы с металлами, но и с термопластиками в порошковом виде. Кроме того, металлические материалы зачастую покрываются более легкоплавкими материалами для снижения необходимой мощности лазерных излучателей. В таких случаях готовые металлические модели требуют дополнительного спекания в печах и пропитки для повышения прочности.Разновидностью технологии SLS является метод прямого лазерного спекания металлов (DMLS), ориентированный, как понятно из названия, на работу с чистыми металлическими порошками. Данные установки зачастую оснащаются герметичными рабочими камерами, наполняемыми инертным газом для работы с металлами, подверженными оксидации – например, с титаном. Кроме того, DMLS-принтеры в обязательном порядке применяют подогрев расходного материала до точки чуть ниже температуры плавления, что позволяет экономить на мощности лазерных установок и ускорять процесс печати.
Схема работы SLS, DLMS и SLM установок
Процесс лазерного спекания начинается с нанесения тонкого слоя подогретого порошка на рабочую платформу. Толщина наносимых слоев соответствует толщине одного слоя цифровой модели. Затем производится спекание частиц между собой и с предыдущим слоем. Изменение траектории движения лазерного луча производится с помощью электромеханической системы зеркал.
По завершении вычерчивания слоя лишний материал не удаляется, а служит опорой для последующих слоев, что позволяет создавать модели сложной формы, включая навесные элементы, без необходимости построения дополнительных опорных структур. Такой подход вкупе с высокой точностью и разрешением позволяет получать детали, практически не требующие механической обработки, а также цельные детали уровня геометрической сложности, недосягаемого традиционными производственными методами, включая литье.
Лазерное спекание позволяет работать с широким ассортиментом металлов, включая сталь, титан, никелевые сплавы, драгоценные материалы и др. Единственным недостатком технологии можно считать пористость получаемых моделей, что ограничивает механические свойства и не позволяет добиться прочности на уровне литых аналогов.
Выборочная лазерная (SLM) и электронно-лучевая плавка (EBM)
Несмотря на высокое качество моделей, получаемых лазерным спеканием, их практическое применение ограничивается сравнительно низкой прочностью ввиду пористости. Подобные изделия могут быть использованы для быстрого прототипирования, макетирования, производства ювелирных изделий и многих других задач, но малопригодны для производства деталей, способных выдерживать высокие нагрузки. Одним решением это проблемы стало преобразование технологии прямого лазерного спекания металлов (DMLS) в технологию аддитивного производства методом лазерной плавки (SLM). Фактически, единственным принципиальным различием этих методов является степень термической обработки металлического порошка: технология SLM основана на полной плавке для получения гомогенных моделей, практически неотличимых по физическим и механическим свойствам от литых аналогов. Пример титанового имплантата, полученного с помощью технологии электронно-лучевой плавки (EBM)
Параллельным методом, достигшим прекрасных результатов, стала электронно-лучевая плавка (EBM). На данный момент существует лишь один производитель, создающий EBM-принтеры – шведская компания Arcam.
EBM позволяет достигать точности и разрешения, сравнимых с лазерной плавкой, но обладает определенными преимуществами. Так, использование электронных пушек позволяет избавиться от деликатных электромеханических зеркальных систем, используемых в лазерных установках. Кроме того, манипулирование электронными пучками с помощью электромагнитных полей возможно на скоростях, несравнимых более высоких по сравнению с электромеханическими системами, что вкупе с увеличением мощности позволяет добиться повышенной производительности без существенного усложнения конструкции. В остальном же, конструкция SLM и EBM-принтеров схожа с установками для лазерного спекания металлов.
Возможность работы с широким диапазонам металлов и сплавов позволяет создавать мелкие партии специализированных металлических деталей, практически не уступающих образцам, получаемым с помощью традиционных методов производства. При этом отсутствует необходимость создания дополнительных инструментов и инфраструктуры – таких как, литейные формы и печи. Соответственно, возможна значительная экономия при прототипировании или мелкосерийном производстве.
Установки для лазерной и электронно-лучевой плавки успешно используются для производства таких предметов, как ортопедические титановые протезы, лопатки газовых турбин и форсунки реактивных двигателей среди прочих.
Прямое лазерное аддитивное построение (CLAD)
Схема работы установок, использующих технологию CLADНе столько технология 3D-печати, сколько технология «3D-ремонта». Технология применяется исключительно на промышленном уровне ввиду сложности и относительно узкой специализации.
В основе CLAD лежит напыление металлического порошка на поврежденные детали с немедленной наплавкой с помощью лазера. Позиционирование «печатной головки» осуществляется по пяти осям: вдобавок к перемещению в трех плоскостях, головка обладает способностью изменять угол наклона и поворачиваться вокруг вертикальной оси, что позволяет работать под любым углом.
Подобные устройства зачастую используются для ремонта крупногабаритных изделий, включая производственный брак. Например, установки французской компании BeAM используются для ремонта авиационных двигателей и других сложных механизмов.
Полноценные установки CLAD предусматривают использование герметичной рабочей камеры с инертной атмосферой для работы с титаном и другими металлами и сплавами, поддающимися оксидации.
Произвольная электронно-лучевая плавка (EBFȝ)
Схема работы EBFȝ принтеровТехнология, разрабатываемая специалистами НАСА для применения в условиях невесомости. Так как отсутствие гравитации делает работу с металлическими порошками практически невозможной, технология EBFȝ подразумевает использование металлических нитей.
Процесс построения схож с 3D-печатью методом послойного наплавления (FDM), но с использованием электронно-лучевой пушки для плавки расходного материала.
Данная технология позволит создание металлических запасных частей на орбите, что позволит существенно сократить затраты на доставку частей и обеспечит возможность быстрого реагирования на внештатные ситуации.
Перейти на главную страницу Энциклопедии 3D-печати
3d печать металлом – технология 21 века
3d печать металлом — одна из самых востребованных технологий наших дней. Эта технология также известна как прямое лазерное спекание металлов (DMLS) и селективное лазерное плавление (SLM).
Материалы 3д печати разнообразны. Но 3d печать металлом стоит немного особняком. Это вызвано как технологически сложной работой, так и большой стоимостью.
с сайта 3dhubs
3d печать металлом занимает уникальную позицию в современной разработке продукции. Она позволяет напрямую изготавливать сложные детали для конечного использования. А также облегчает оснастку для традиционных производственных технологий. В результате, сокращая затраты и время выполнения заказа.
3d печать металлом также известна как прямое лазерное спекание металлов (DMLS) и селективное лазерное плавление (SLM).
3d печать металлом SLM и DMLS: общее
Селективное лазерное плавление (SLM) и прямое лазерное спекание металлов (DMLS) — это два процесса производства присадок к металлу. 3d печать металлом принадлежат к семейству 3D-печати методом порошкового слоя.
Две технологии имеют много общего. Например, обе используют лазер для сканирования и выборочного плавления (или плавления) частиц металлического порошка. Связывая их вместе и создавая слой слой за слоем. Кроме того, 3d печать металлом в обоих процессах использует материалы, которые имеют гранулированную форму.
3d печать металлом SLM и DMLS может производить детали из широкого спектра металлов и металлических сплавов. Включая, например, алюминий, нержавеющую сталь, титан, кобальт, хром и инконель. Эти материалы покрывают потребности большинства промышленных применений. От аэрокосмической до медицинской.
Драгоценные металлы, например такие как золото, платина, палладий и серебро, также могут быть обработаны. Но их применение носит незначительный характер. 3d печать металлом в этом случае в основном ограничивается изготовлением ювелирных изделий.
Стоимость металлического порошка очень высока. Например, килограмм порошка из нержавеющей стали 316L стоит примерно 350-450 долларов. По этой причине минимизация объема детали и необходимость поддержки является ключом к поддержанию стоимости как можно ниже.
3d печать металлом имеет основное преимущество в совместимости с высокопрочными материалами. Например, такими как никелевые или кобальт-хромовые суперсплавы. Которые очень трудно обрабатывать традиционными методами производства.
Значительная экономия средств и времени может быть достигнута за счет использования металлической 3D-печати для создания детали почти чистой формы. Которая впоследствии может быть подвергнута последующей обработке до очень высокого качества поверхности.
3d печать металлом SLM и DMLS: разница технологий
Различия между SLM и DMLS сводятся к основам процесса связывания частиц. А также к патентам. SLM использует металлические порошки с одной температурой плавления и полностью плавит частицы. В то время как в DMLS порошок состоит из материалов с переменными точками плавления.
3d печать металлом SLM производит детали из одного металла. В то время как DMLS производит детали из металлических сплавов.
И SLM, и DMLS используются в промышленных приложениях для создания конечных инженерных продуктов. В этой статье мы используем термин 3d печать металлом для обозначения обоих процессов в целом. И описываем основные механизмы процесса изготовления. Которые необходимы инженерам и дизайнерам для понимания преимуществ и ограничений технологии.
Но существуют и другие процессы производства добавок. Их можно использовать для производства плотных металлических деталей. Такие как электронно-лучевое плавление (EBM) и ультразвуковое аддитивное производство (UAM). Их доступность и приложения ограничены. Поэтому они не будут представлены здесь.
3d печать металлом — характеристики SLM и DMLS
Характеристики металлов:
Алюминиевые сплавы: Хорошие механические и термические свойства. Низкая плотность. Хорошая электропроводность. Низкая твердость.
Нержавеющая сталь и инструментальная сталь: Высокая износостойкость. Большая твердость. Хорошая пластичность и свариваемость.
Титановые сплавы: Устойчивость к коррозии. Отличное соотношение прочности и веса. Низкое тепловое расширение. Биосовместимые.
Кобальт-Хром суперсплавы: Отличная износостойкость и устойчивость к коррозии. Отличные свойства при повышенных температурах. Очень высокая твердость. Биосовместимые.
Никелевые суперсплавы (Инконель): Отличные механические свойства. Высокая коррозионная стойкость. Термостойкость до 1200 o C. Используется в экстремальных условиях.
Драгоценные металлы: Используется в ювелирном деле. Не широко доступны.
Параметры принтера
В SLM и DMLS почти все параметры процесса устанавливаются производителем станка. Высота слоя, используемого в металлической 3D-печати, варьируется от 20 до 50 микрон. Она зависит от свойств металлического порошка (текучести, гранулометрического состава, формы и т.д.).
Типичный размер сборки металлической системы 3D-печати составляет 250 x 150 x 150 мм. Но также доступны более крупные машины (до 500 x 280 x 360 мм).
3d печать металлом достигает точности размеров приблизительно ± 0,1 мм.
3d печать металлом может использоваться для мелкосерийного производства. Но возможности металлических систем 3D-печати больше напоминают возможности серийного производства на машинах FDM или SLA, чем на принтерах SLS. Они ограничены доступной областью печати (направление XY), так как части должны быть прикреплены к платформе сборки.
Металлический порошок в SLM и DMLS пригоден для вторичной переработки. Обычно расходуется менее 5%. После каждого отпечатка неиспользованный порошок собирают, просеивают. А затем доливают свежим материалом до уровня, необходимого для следующего изготовления.
Адгезия слоя
Металлические детали SLM и DMLS обладают практически изотропными механическими и термическими свойствами. Они являются твердыми с очень малой внутренней пористостью. Менее 0,2-0,5% в состоянии после печати и практически не имеют термической обработки.
3d печать металлом использует металлические печатные детали. Они имеют более высокую прочность и твердость. И часто являются более гибкими, чем детали, изготовленные традиционным способом. Но, тем не менее, они более склонны к усталости.
Из-за зернистой формы необработанного материала шероховатость поверхности (Ra) в металлическом 3D-печатном изделии составляет приблизительно 6-10 мкм. Эта относительно высокая шероховатость поверхности может частично объяснить более низкую усталостную прочность.
Структура поддержки и ориентация детали
Опорные конструкции всегда требуются при печати металлов из-за очень высокой температуры обработки. Они обычно строятся с использованием решетчатого рисунка.
Поддержка в металлической 3D-печати выполняет 3 различные функции:
— они предлагают подходящую платформу для создания следующего слоя.
— закрепляют деталь на сборочной плите и предотвращают коробление.
— действуют как теплоотвод, отводя тепло от детали и позволяя ему охлаждаться с более контролируемой скоростью.
Детали часто ориентированы под углом, чтобы минимизировать вероятность деформации и максимизировать прочность детали в критических направлениях. Однако это увеличит количество необходимой поддержки, время сборки, материальные отходы и (в конечном итоге) общую стоимость.
Деформация также может быть сведена к минимуму с помощью рандомизированных шаблонов сканирования. Эта стратегия сканирования предотвращает накопление остаточных напряжений в любом конкретном направлении. И добавляет характерную текстуру поверхности к детали.
Для прогнозирования поведения детали во время обработки часто используются симуляции. Поскольку стоимость металлической печати очень высока.
Алгоритмы оптимизации топологии также используются не только для увеличения механических характеристик и создания облегченных деталей. Но и для сведения к минимуму потребности в опорной конструкции и вероятности коробления.
3d печать металлом — полые секции и легкие конструкции
Большие полые секции обычно не используются в металлической печати. Поскольку несущие конструкции не могут быть легко удалены. В отличие от процессов плавления в полимерном порошковом слое. Например, таких как SLS.
Для внутренних каналов больше, чем Ø 8 мм, рекомендуется использовать алмазные или каплевидные поперечные сечения вместо круглых. Так как они не требуют опорных конструкций.
В качестве альтернативы полым секциям детали могут быть выполнены с оболочкой и сердечниками. Оболочка и ядра обрабатываются с использованием различной мощности лазера и скорости сканирования. Что приводит к различным свойствам материала.
Использование обшивки и стержней очень полезно при изготовлении деталей с большим сплошным сечением. Поскольку они значительно сокращают время печати и вероятность коробления. А также позволяют получать детали с высокой стабильностью и превосходным качеством поверхности.
Использование решетчатой структуры также является распространенной стратегией в металлической 3D-печати для уменьшения веса детали. Алгоритмы оптимизации топологии также могут помочь в разработке органических легких форм.
Как работает 3d печать металлом SLM и DMLS?
Основной процесс изготовления для SLM и DMLS очень похожи. Вот как это работает:
Сборочная камера сначала заполняется инертным газом (например, аргоном), чтобы минимизировать окисление металлического порошка. А затем нагревается до оптимальной температуры сборки.
Тонкий слой металлического порошка распределяется по строительной платформе. Мощный лазер сканирует поперечное сечение компонента, плавя (или сплавливая) металлические частицы вместе и создавая следующий слой.
Когда процесс сканирования завершен, строительная платформа перемещается вниз на один слой. Перемагничивающее вещество наносит еще один тонкий слой металлического порошка. Процесс повторяется до тех пор, пока вся часть не будет завершена.
Когда процесс сборки закончен, детали полностью заключены в металлический порошок. Детали прикрепляются к строительной платформе через опорные конструкции. В отличие от процесса плавления в слое полимерного порошка. Например, такого как SLS.
Опора в металлической 3D-печати создается из того же материала, что и деталь. И всегда требуется для уменьшения деформации, которая может возникнуть из-за высоких температур обработки.
Когда бункер охлаждается до комнатной температуры, избыток порошка удаляется вручную. Детали обычно подвергаются термообработке для снятия любых остаточных напряжений. Пока они все еще прикреплены к строительной платформе. Затем компоненты отсоединяются от монтажной плиты с помощью резки, механической обработки или электроэрозионной обработки проволоки и готовы к использованию или дальнейшей обработке.
3d печать из металла — постобработка
Различные методы последующей обработки используются для улучшения механических свойств, точности и внешнего вида металлических печатных деталей.
Обязательные этапы последующей обработки включают удаление рассыпного порошка и опорных конструкций. В то время как термическая обработка (термический отжиг) обычно используется для снятия остаточных напряжений и улучшения механических свойств детали.
Обработка на станках с ЧПУ может быть использована для важных размеров (например, отверстий или резьб). Струйная обработка, металлизация, полировка и микрообработка могут улучшить качество поверхности и усталостную прочность металлической печатной детали.
3d печать металлом — преимущества и недостатки
Вот основные преимущества и недостатки процессов 3D-печати на металле:
— 3d печать металлом как процесс может быть использована для изготовления сложных, сделанных на заказ деталей. С геометрией, которую традиционные методы производства не могут изготовить.
— Металлические 3D-печатные детали могут быть топологически оптимизированы для максимизации их производительности при минимальном весе и общем количестве компонентов в сборке.
— Металлические 3D-печатные детали имеют отличные физические свойства. А доступный ассортимент материалов включает в себя трудно обрабатываемые материалы. Такие как металлические суперсплавы.
— Затраты на материалы и изготовление, связанные с металлической 3D-печатью, высоки. Поэтому эти технологии не подходят для деталей, которые могут быть легко изготовлены традиционными методами.
— Размер сборки металлических систем 3D-печати ограничен. Поскольку требуются точные производственные условия и управление процессом.
— Уже существующие дизайны могут не подходить для 3D-печати на металле и могут нуждаться в изменении.
Эмпирические правила
3d печать металлом наиболее подходит для сложных, сделанных на заказ деталей. Которые сложно или очень дорого изготовить традиционными методами.
Минимизация потребности в опорных конструкциях значительно снизит стоимость печати на металле. Оптимизация топологии необходима для максимизации дополнительных преимуществ использования металлической печати.
Металлические 3D-печатные детали имеют отличные механические свойства. И могут быть изготовлены из широкого спектра технических материалов. Например, включая металлические суперсплавы.
3D-печать из металла — сделали велосипед
Компания MX3D занимается разработкой 3D-печать из металла. MX3D — разработчик технологии Robotic Additive Manufacturing (RAM) из Амстердама.
MX3D использовала 3d печать металлом для выпуска обновленной версии велосипеда. Этот велосипед получил название «Arc Bike II». Он напечатан на 3D-принтере из алюминия. Технология называется Wire Arc Additive Manufacturing (WAAM).
Благодаря алюминиевому материалу Arc Bike II значительно легче, чем его предшественник. Т.к. Arc Bike I был изготовлен из нержавеющей стали. К примеру, MX3D объясняет, что новый проект демонстрирует прогресс в развитии технологий в компании. А также скорость, с которой можно перейти от идеи к конечному продукту. Велосипед будет доступен для покупки в ограниченном количестве на сайте MX3D.
Томас Ван Глабеке — руководитель проекта Arc Bike II. Он заявляет: «Потребовалось некоторое время, чтобы освоить алюминиевую печать. Она более сложна, чем другие металлы. В результате из-за этого получился прочный и легкий велосипед». «После того, как начальные технические проблемы были решены, было удивительно видеть скорость от идеи до конечного продукта. И это захватывающе. Я не могу дождаться, чтобы увидеть всю серию этих велосипедов, работающих на производственной линии MX3D».
Программное обеспечение Arc Bike II и MX3D beta
Arc Bike II от MX3D представляет собой первый проект 3D-печати компании, использующий алюминий. Поэтому он выступает в качестве прелюдии к «гораздо большему проекту» в процессе разработки.
Дизайн велосипеда изменят в соответствии с пропорциями тела гонщика. К примеру, с помощью программного обеспечения для генеративного проектирования. Программное обеспечение MX3D затем преобразует генеративные данные дизайна в инструкции для робота. И в течение 24 часов 3D-принтер печатает специально разработанную раму велосипеда.
Программное обеспечение, используемое MX3D для 3D-печати Arc Bike II, в настоящее время находится в стадии бета-тестирования. Но компания сделала свое программное обеспечение доступным для предварительного заказа. К примеру, это поможет промышленным и креативным клиентам разработать собственные масштабные проекты по 3D-печати на металле.
В результате MX3D получил финансирование в первой половине 2019 года от DOEN Participations и PDENH. Это поможет в разработке своей технологии и запуске бета-версии программного продукта. С 19 по 22 ноября во Франкфурте проходит Formnext 2019. Там компания представит свою бета-версию программного обеспечения.
Если Вы еще погуглите в интернете 3d печать металлом, вы найдете еще множество примеров. Прогресс идет семимильными шагами. 3d печать из металла уже вышла из отдельных экспериментов и поднялась до промышленных масштабов.
3d печать из металла – строим мост
Творческие проекты компании, такие как велосипеды, проводятся для целей исследований и разработок с целью получения критического опыта через опыт производства. 3d печать металлом в течение последних четырех лет будет использована MX3D для постройки моста из нержавеющей стали.
Первоначально строительство моста запланировали в 2015 году, но затем перенесли на 2016 год. Однако оно было отложено снова из-за различных неудач. Затем MX3D объявил, что он интегрирует мост с интеллектуальной технологией Для этого используют сенсорную сеть и цифровое двойное устройство для мониторинга состояния моста в режиме реального времени.
Мост был закончен и выставлен на Голландской неделе дизайна (DDW) в Эйндховене в октябре 2018 года. В настоящее время он проходит испытания в Университете Твенте. После чего его установят через канал Oudezijds Achterburgwal в центре Амстердама. MX3D сотрудничает со многими компаниями для создания и реализации своего моста с 3D-печатью.
3d печать металлом — будущее производства
MX3D стремится представить преимущества 3d печать из металла новым и высокоэффективным отраслям промышленности. Для этого необходимо использование интеллектуальной технологии производства роботизированных добавок. В результате компания считает, что будущее производства — это автоматизированное и автономное производство уникальных компьютерных деталей и конструкций с использованием роботов.
3d печать металлом это производственный процесс. MX3D включает использование роботизированной руки и 3D-принтера WAAM. Они сочетаются с программным обеспечением для производства крупных и сложных металлических предметов. Компания утверждает, что ее программное обеспечение может запустить «готовый роботизированный манипулятор и сварочный аппарат в промышленное производство».
Статья относится к теме Материалы 3D-печати.
Все новости в наших группах: вконтакте, twitter, facebook
Введение в 3D-печать металлом
3D-печать или ЧПУ? Найдите лучшую технологию для производства ваших металлических деталей
Загрузите наше руководство по производству металлических деталей
SLM и DMLS: в чем разница?
Выборочная лазерная плавка (SLM) и прямое лазерное спекание металла (DMLS) — это два процесса аддитивного производства металлов, которые относятся к семейству 3D-печати методом расплавления порошка. Эти две технологии имеют много общего: в обеих используется лазер для сканирования и выборочного сплавления (или плавления) частиц металлического порошка, связывания их вместе и создания детали слой за слоем.Кроме того, материалы, используемые в обоих процессах, представляют собой металлы в гранулированной форме.
Различия между SLM и DMLS сводятся к основам процесса связывания частиц (а также патентам): SLM использует металлические порошки с единой температурой плавления и полностью плавит частицы, тогда как в DMLS порошок состоит из материалов с переменной температурой плавления. точки, которые сливаются на молекулярном уровне при повышенных температурах.
По существу:
SLM производит детали из цельного металла , а DMLS производит детали из металлических сплавов .
И SLM, и DMLS используются в промышленных приложениях для создания конечных инженерных продуктов. В этой статье мы используем термин 3D-печать на металле для обозначения обоих процессов в целом и описываем основные механизмы процесса изготовления, которые необходимы инженерам и дизайнерам для понимания преимуществ и ограничений технологии.
Существуют и другие процессы аддитивного производства, которые можно использовать для производства плотных металлических деталей, такие как электронно-лучевая плавка (EBM) и ультразвуковое аддитивное производство (UAM).Однако их доступность и возможности применения ограничены, поэтому здесь они не будут представлены. Щелкните здесь, чтобы получить дополнительную информацию о струйной очистке металлических связующих.
Процесс печати SLM / DMLSКак работает 3D-печать металлом?
Базовый процесс изготовления SLM и DMLS очень похож. Вот как это работает:
- Камера сборки сначала заполняется инертным газом (например, аргоном), чтобы минимизировать окисление металлического порошка, а затем нагревается до оптимальной температуры сборки.
- Тонкий слой металлического порошка распределяется по платформе сборки, и лазер высокой мощности сканирует поперечное сечение компонента, плавя (или сплавливая) металлические частицы вместе и создавая следующий слой. Сканируется вся область модели, поэтому деталь создается полностью цельной.
- Когда процесс сканирования завершен, строительная платформа перемещается вниз на один слой, а устройство для повторного нанесения покрывает еще один тонкий слой металлического порошка. Процесс повторяется до тех пор, пока не будет завершена вся часть.
Когда процесс сборки завершен, детали полностью заключены в металлический порошок. В отличие от процесса сплавления полимерного порошкового слоя (такого как SLS), детали прикрепляются к платформе сборки через опорные конструкции . Опора в металлической 3D-печати изготавливается из того же материала, что и деталь, и всегда требуется для смягчения деформации и искажения, которые могут возникнуть из-за высоких температур обработки.
Когда бункер охлаждается до комнатной температуры, излишки порошка удаляются вручную, а детали обычно подвергаются термообработке, пока они еще прикреплены к платформе сборки, чтобы снять любые остаточные напряжения.Затем компоненты отделяются от рабочей пластины с помощью резки, механической обработки или электроэрозионной обработки и готовы к использованию или дальнейшей постобработке.
Схема принтера SLM / DMLSПовысьте свои навыки проектирования 3D-печати
Получите бесплатный плакат с правилами дизайна для 3D-печати
Характеристики SLM и DMLS
Параметры принтера
В SLM и DMLS почти все параметры процесса устанавливаются производителем станка. Высота слоя , используемого в 3D-печати на металле, варьируется от 20 до 50 микрон и зависит от свойств металлического порошка (текучесть, гранулометрический состав, форма и т. Д.).
Типичный размер сборки металлической системы 3D-печати составляет 250 x 150 x 150 мм, но также доступны машины большего размера (до 500 x 280 x 360 мм). Размерная точность , которую может достичь металлический 3D-принтер, составляет приблизительно ± 0,1 мм.
Металлические принтеры могут использоваться для мелкосерийного производства , но возможности систем трехмерной печати на металле больше напоминают возможности серийного производства машин FDM или SLA, чем SLS-принтеров: они ограничены доступной областью печати (направление XY ), так как детали должны быть прикреплены к платформе сборки.
Металлический порошок в SLM и DMLS пригоден для вторичной переработки. : обычно менее 5% теряется. После каждой печати неиспользованный порошок собирается, просеивается, а затем доливается свежим материалом до уровня, необходимого для следующей сборки.
Отходов при печати металла, хотя поставляется в виде опорной конструкции , которые имеют решающее значение для успешного завершения сборки, но может увеличить количество требуемого материала (и стоимость) резко.
Мелкосерийное производство велосипедной рамы с использованием SLM.Предоставлено: Renishaw и Empire CyclesАдгезия слоев
Металлические детали из SLM и DMLS имеют почти изотропные, механические и термические свойства. Они твердые, с очень небольшой внутренней пористостью (менее 0,2–0,5% в состоянии после печати и практически отсутствует после термической обработки).
Металлические печатные детали имеют на более высокую прочность и твердость и часто на более гибкие, , чем детали, изготовленные с использованием традиционного метода. Однако они более склонны к утомлению.
Например, взгляните на механические свойства металлического сплава для 3D-печати AlSi10Mg EOS и литого под давлением сплава A360 . Эти два материала имеют очень похожий химический состав с высоким содержанием кремния и магния. Напечатанные детали имеют превосходные механические свойства и более высокую твердость по сравнению с кованым материалом.
Из-за гранулированной формы необработанного материала заводская шероховатость поверхности (Ra) металлической детали, напечатанной на 3D-принтере, составляет приблизительно 6-10 мкм.Эта относительно высокая шероховатость поверхности может частично объяснять более низкую усталостную прочность .
AlSi10Mg (сплав для 3D-печати) | A360 (литье под давлением) | |
---|---|---|
Предел текучести (деформация 0,2%) & ast; | XY: 230 МПа Z: 230 МПа | 165 МПа |
Прочность на растяжение и аст; | XY: 345 МПа Z: 350 МПа | 317 МПа |
Модуль и аст; | XY: 70 ГПа Z: 60 ГПа | 71 ГПа |
Удлинение при разрыве & ast; | XY: 12% Z: 11% | 3.5% |
Твердость и аст; | 119 HBW | 75 HBW |
Усталостная прочность & ast; & ast; | 97 МПа | 124 МПа |
& ast; : Термическая обработка: отжиг при 300 & # 8451 в течение 2 часов. & ast; & ast; : Проверено на реальных образцах
Опорная конструкция и ориентация деталей
Опорные конструкции всегда требуются при печати на металле из-за очень высокой температуры обработки, и они обычно строятся с использованием решетчатого узора.
Поддержка 3D-печати металлом выполняет 3 разные функции:
- Они предлагают подходящую платформу для строительства следующего слоя.
- Они прикрепляют деталь к рабочей пластине и предотвращают деформацию.
- Они действуют как теплоотвод , отводят тепло от детали и позволяют ей охлаждаться с более контролируемой скоростью.
Детали часто ориентируют под углом, чтобы свести к минимуму вероятность деформации и максимизировать прочность детали в критических направлениях.Однако это увеличит объем необходимой поддержки, время сборки, отходы материалов и (в конечном итоге) общую стоимость.
Искажение также можно минимизировать с помощью рандомизированных шаблонов сканирования . Эта стратегия сканирования предотвращает накопление остаточных напряжений в любом конкретном направлении и добавляет детали характерную текстуру поверхности.
Поскольку стоимость печати на металле очень высока, моделирование часто используется для прогнозирования поведения детали во время обработки. оптимизации топологии алгоритмы также используется не только для увеличения механических характеристик и создавать облегченные части, но и свести к минимуму потребности в опорной конструкции и вероятность коробления.
Металлический кронштейн перед снятием опоры, ориентированный под углом 45 o . Предоставлено: Concept Laser
Полые профили и легкие конструкции
В отличие от процессов сплавления в полимерном порошковом слое, таких как SLS, большие полые секции обычно не используются в печати на металле, поскольку несущие конструкции не могут быть легко удалены.
Для внутренних каналов диаметром более 8 мм рекомендуется использовать ромбовидные или каплевидные поперечные сечения вместо круглых, так как они не требуют опорных конструкций. Дополнительные рекомендации по проектированию SLM и DMLS можно найти в этой статье.
В качестве альтернативы полым профилям детали могут быть выполнены с оболочкой и сердечником. Кожа и сердечники обрабатываются с использованием различной мощности лазера и скорости сканирования, что приводит к различным свойствам материала. Использование оболочки и стержней очень полезно при производстве деталей с большим твердым сечением, поскольку они значительно сокращают время печати и вероятность деформации и позволяют производить детали с высокой стабильностью и превосходным качеством поверхности.
Использование решетчатой структуры также является распространенной стратегией в 3D-печати металлом для уменьшения веса детали. Алгоритмы оптимизации топологии также могут помочь в разработке органической облегченной формы .
Удаление порошка вокруг металлических деталей, изготовленных методом SLM-печати.Общие материалы SLM и DMLS
SLM и DMLS могут производить детали из большого количества металлов и металлических сплавов, включая алюминий, нержавеющую сталь, титан, кобальт-хром и инконель.Эти материалы удовлетворяют потребности большинства промышленных применений, от аэрокосмической до медицинской. Драгоценные металлы, такие как золото, платина, палладий и серебро, также могут обрабатываться, но их применение является второстепенным и в основном ограничивается изготовлением ювелирных изделий.
Стоимость металлического порошка очень высока. Например, килограмм порошка из нержавеющей стали 316L стоит примерно 350-450 долларов. По этой причине минимизация объема деталей и необходимость поддержки являются ключом к поддержанию как можно более низких затрат.
Ключевым преимуществом металлической 3D-печати является ее совместимость с высокопрочными материалами, такими как никель или кобальт-хромовые суперсплавы, которые очень трудно обрабатывать традиционными методами производства. Существенная экономия средств и времени может быть достигнута за счет использования 3D-печати металлом для создания детали почти чистой формы, которую впоследствии можно подвергнуть последующей обработке до очень высокого качества поверхности.
Материал | |
---|---|
Алюминиевые сплавы | Хорошие механические и термические свойства Низкая плотность Хорошая электропроводность Низкая твердость |
Нержавеющая сталь и инструментальная сталь | Высокая износостойкость Высокая твердость Хорошая пластичность и свариваемость |
Титановые сплавы | Коррозионная стойкость Отличное соотношение прочности и веса Низкое тепловое расширение Биосовместимый |
Кобальт-хромовые суперсплавы | Превосходная износостойкость и коррозионная стойкость Отличные свойства при повышенных температурах Очень высокая твердость Биосовместимый |
Никелевые суперсплавы (инконель) | Отличные механические свойства Высокая коррозионная стойкость Термостойкость до 1200 o C Используется в экстремальных условиях |
Драгоценные металлы | Используется в ювелирном деле Широко недоступен |
Сравните затраты на 3D печать металлом
Получите мгновенную цитату
Постобработка
Для улучшения механических свойств, точности и внешнего вида металлических печатных деталей используются различные методы постобработки.
Обязательные этапы постобработки включают удаление рыхлого порошка и опорных конструкций, в то время как термическая обработка (термический отжиг) обычно используется для снятия остаточных напряжений и улучшения механических свойств детали.
Обработка с ЧПУможет использоваться для критически важных деталей (таких как отверстия или резьба). Пескоструйная очистка, металлизация, полировка и микрообработка могут улучшить качество поверхности и усталостную прочность металлической детали с печатью.
Спутниковая антенна изготовлена с использованием DMLS. Предоставлено: Concept Laser и Optisys LLC
Подробнее о станках с ЧПУ
Скачать руководство по проектированию и производству
Преимущества и ограничения 3D-печати металлом
Вот основные преимущества и недостатки процессов 3D-печати металлом:
С помощью процессов 3D-печати металлом можно изготавливать сложные индивидуальные детали с геометрией, которую невозможно получить с помощью традиционных методов производства.
Металлические детали, напечатанные на 3D-принтере, можно топологически оптимизировать, чтобы максимизировать их производительность при минимальном весе и общем количестве компонентов в сборке.
Металлические детали, напечатанные на 3D-принтере, обладают отличными физическими свойствами, а диапазон доступных материалов включает труднообрабатываемые иным образом материалы, такие как металлические суперсплавы.
Затраты на материалы и производство, связанные с 3D-печатью на металле, высоки, поэтому эти технологии не подходят для деталей, которые можно легко изготовить традиционными методами.
Размер сборки систем трехмерной печати на металле ограничен, так как требуются точные производственные условия и контроль процесса.
Уже существующие конструкции могут не подходить для 3D-печати металлом, и их, возможно, придется переделать. ВНИМАНИЕ !!!!!!!!!!!!!!!!!!!!!!!!!!!!!!!!!!!!!!!!!!!!!!!!!!!!!!!!!!!!!!!!!!!!!!!!!!!!!!!!!!!!!!!!!!!!!!!!!!!!!!!!!!!!!!!!!!!!!!!!!!!!!!!!!!!!!!!!!!!!!!!!!!!!!!!!!!!!!!!!!!!!!!!!!!!!!!!!!!!!!!!!!!!!!!!!!!!!!!!!!!!!!!!!!!!!!!!!!!!!!!!!!!!!!!!!!!!!!!!!!!!!!!!!!!!!!!!!!!!!!!!!!!!
Подробное руководство по проектированию металлической 3D-печати дано в этой статье Базы знаний. Основные характеристики систем SLM и DMLS приведены в таблице ниже:
Металл 3D-печать (SLM / DMLS) | |
---|---|
Материалы | Металлы и металлические сплавы (алюминий, сталь, титан и т. Д.) |
Точность размеров | ± 0.1 мм |
Типичный размер сборки | 250 x 150 x 150 мм (до 500 x 280 x 360 мм) |
Толщина общего слоя | 20-50 мкм |
Опора | Всегда требуется |
Практические правила
- Металл 3D-печать наиболее подходит для сложных, сделанных на заказ деталей, которые сложно или очень дорого производить традиционными методами.
- Сведение к минимуму необходимости в опорных конструкциях значительно снизит стоимость печати на металле.
- Оптимизация топологии важна для получения максимальных дополнительных преимуществ от использования печати на металле.
- Металлические детали, напечатанные на 3D-принтере, обладают отличными механическими свойствами и могут изготавливаться из широкого спектра конструкционных материалов, включая металлические суперсплавы.
Узнайте разницу между 3D-печатью металлом и ЧПУ
Загрузите наше руководство по производству металлических деталей
Металлическая 3D-печать: опровергнуты 7 распространенных заблуждений
3 марта 2020 г. Отсутствие понимания возможностей и ограничений 3D-печати металлом остается одной из ключевых проблем на пути к более широкому внедрению этой технологии.Заблуждения, возникшие вокруг технологии, только подливают масла в огонь.
В сегодняшней статье мы разберем некоторые распространенные мифы, связанные с 3D-печатью металлом, чтобы раскрыть правду и вооружить вас фактами.
Аддитивное производство металлов (AM) может быть дорогостоящей технологией. Некоторые металлические системы AM могут стоить до миллиона долларов, что делает их доступными только для крупных предприятий.
Тем не менее, некоторые компании понимают, что такие капиталовложения недопустимы для небольших фирм и механических цехов, и специально разработали 3D-принтеры по цене ниже 200 000 долларов. Такие системы нацелены на демократизацию 3D-печати металлом, открывая доступ к технологиям для более широких рынков.
Примеры включают такие компании, как Xact Metal, Laser Melting Innovations (LMI) и One Click Metal, которые демократизируют технологию плавления металлического порошка.
В большинстве случаев эти компании оснастили свои системы более экономичными компонентами, чтобы снизить затраты на оборудование. Например, в 3D-принтере LMI Alpha 140 используется диодный лазер, который дешевле и менее подвержен повреждениям, чем CO2-лазер. И вместо дорогих систем сканирования Alpha 140 оснащена лазерной системой с декартовым движением. Благодаря этим изменениям компания смогла снизить цену на свою машину до менее чем 100 000 евро.
Кроме того, другие компании, такие как Desktop Metal и Markforged, разработали новый подход к 3D-печати металлом, чтобы сделать ее более доступной.И система Desktop Metal Studio, и система Metal X от Markforged основаны на аналогичной технологии, в то время как металлические порошки, заключенные в пластиковую нить, экструдируются через сопло для создания сырых деталей, которые затем спекаются в печи.
Что делает этот подход более доступным, так это более дешевые компоненты, необходимые для производства принтера, и более низкие эксплуатационные расходы, достигаемые за счет более дешевых материалов для литья металла под давлением.
По цене менее 200 000 долларов и Metal X, и Studio System открыли новые возможности в области 3D-печати металлом, сделав процесс менее дорогостоящим, удобным для офиса и более простым в управлении.
Еще одно распространенное заблуждение — все металлические 3D-принтеры похожи. На самом деле существует целых пять ключевых технологий 3D-печати металлом, каждая со своими уникальными требованиями и функциональностью.
Даже в пределах одной технологической группы 3D-принтеры могут существенно различаться. В качестве примера возьмем сплавление в металлическом порошковом слое (PBF), процесс, при котором металлические порошки наплавляются слой за слоем с помощью мощного источника тепла.Хотя ключевая идея PBF остается прежней, существует несколько совершенно уникальных подходов к этой технологии.
Например, VELO3D разработала 3D-принтер для расплавления порошкового слоя, который отличается уникальным механизмом повторного нанесения покрытия и тесно интегрирован с программным обеспечением. Это дает системе уникальную возможность печатать детали практически без опорных конструкций.
В другом примере Aurora Labs разрабатывает металлический 3D-принтер PBF, который сможет печатать детали с беспрецедентной технологией PBF — до тонны металла в день.
В целом ландшафт 3D-печати металлом довольно сложен, и за ним бывает трудно следить. Вы можете прочитать наше полное руководство по 3D-печати из металла, чтобы узнать больше об этой технологии.
3D-печать металлом — это действительно популярная технология, когда нужно производить небольшие объемы деталей. Однако на этом его возможности не заканчиваются. Некоторые 3D-принтеры по металлу, в частности те, которые основаны на технологии струйной печати связующего, могут работать со средними и большими партиями деталей.
Одна компания, иллюстрирующая это, — 3DEO. Компания, занимающаяся 3D-печатью металла, разработала запатентованную технологию Intelligent Layering, которая позволяет производить массовое, воспроизводимое и автоматизированное производство металлических деталей.
[Изображение предоставлено 3DEO]
Аддитивный процесс 3DEO состоит из трех этапов. Сначала машина распределяет тонкий слой стандартного металлического порошка для литья под давлением (MIM). Затем распыляет связующее на весь слой. Наконец, он использует концевую фрезу с ЧПУ для точного определения формы детали на каждом слое.Такой гибридный подход позволяет компании, которая использует свою технологию в качестве услуги, обрабатывать заказы объемом 250 000 штук в год.
Другим примером является производственная система Desktop Metal’s Production, машина для струйной печати связующего, способная печатать со скоростью до 12 000 см3 / час, что составляет более 60 кг металлических деталей в час. Такая скорость на порядки выше, чем у большинства металлических 3D-принтеров на рынке, что делает его идеальным для производства сложных металлических деталей в больших объемах.
В качестве потенциальной альтернативы традиционным методам, таким как механическая обработка, эти методы демонстрируют, что отрасль разрабатывает решения для более быстрой 3D-печати металлом, выводя эту технологию в новую сферу более массового производства.
Metal AM действительно был впервые применен для высокотехнологичных приложений в аэрокосмической и медицинской промышленности. Однако с распространением более доступных решений для 3D-печати металлом спектр приложений расширился до запасных частей, функциональных прототипов и нестандартных инструментов.
Интересно, что способность 3D-печати улучшать существующие производственные процессы с помощью аддитивных форм, приспособлений и приспособлений считается одним из основных преимуществ AM, согласно недавнему отчету EY.
Например, компания по производству инструментов Built-Rite использует собственную систему Studio Desktop Metal для производства компонентов для сборки быстроповоротных пресс-форм. Система Studio работает путем нагрева и экструзии металлических стержней — металлического порошка и полимерных связующих — формируя сырую деталь слой за слоем, а затем деталь спекается в удобной для офиса печи.
Этот процесс позволяет Built-Rite сделать компоненты на 90 процентов дешевле и на 30 процентов быстрее, чем при аутсорсинге, при этом уменьшая вес и, следовательно, использование материалов, на 40 процентов.
Когда дело доходит до производства запасных частей, metal AM может помочь устранить несколько основных факторов, влияющих на послепродажное обслуживание и ремонт: большие запасы, старые запасные части, пользующиеся меньшим спросом, и устаревшие или немоторные части на складах.
Очевидно, что преимущества 3D-печати металлом выходят за рамки дорогостоящих аэрокосмических и медицинских компонентов, поскольку она становится технологией с широким спектром недорогих приложений.
Многие производители не уверены, могут ли металлические детали, напечатанные на 3D-принтере, быть такими же, как и детали, изготовленные традиционным способом.Это заблуждение возникло в основном из-за новизны металлической 3D-печати, которая еще должна доказать свою пригодность для производства деталей конечного использования.
Rocket Lab использует 3D-печать на металле для производства всех основных компонентов своего ракетного двигателя Rutherford [Изображение предоставлено: Rocket Lab]
На самом деле, приверженцы технологий уже доказали, что качество металлических деталей, напечатанных на 3D-принтере, равно или даже превосходит качество традиционных аналогов.Вот почему мы все чаще видим, как металлические детали AM используются в критических системах, таких как ракетные двигатели, теплообменники и различные детали турбин.
Несмотря на то, что создание квалифицированного рабочего процесса AM для металла может быть сложной задачей, производители внедряют эту технологию, чтобы в конечном итоге воспользоваться преимуществами более эффективных, легких и эффективных металлических компонентов.
По мере роста спроса на более крупные металлические детали технология эволюционировала, позволяя производить более крупные компоненты.
В 2020 году большинство 3D-принтеров, особенно на основе порошковой технологии и технологии струйной печати связующего, будут создавать мелкие детали, измеряемые в сантиметрах. Например, в случае технологии PBF, когда слои металлического порошка плавятся с помощью лазера или электронного луча, большие детали трудно создать из-за накопления напряжений внутри детали. Чем больше деталь, тем больше изменения температуры, которые увеличивают остаточное напряжение и изменение деформации детали.
Вот почему для производства более крупных деталей часто используются другие технологии AM, такие как прямое энергетическое напыление и аддитивное производство проволочной дуги.
Например, производитель 3D-принтеров для металла, Sciaky, предлагает одни из крупнейших в мире 3D-принтеров для металла, основанные на технологии электронного лучевого аддитивного производства (EBAM). Sciaky позиционирует свою систему AM как более быструю и доступную альтернативу крупногабаритным поковкам и отливкам.
Один из ее 3D-принтеров, EBAM 150, имеет впечатляющий объем сборки 3708 x 1575 x 1575 мм.
EBAM использует процесс, подобный сварке, когда электронный луч используется для плавления металла в форме проволоки.Это означает, что данная технология хорошо подходит для обработки широкого спектра свариваемых материалов, от титана до инконеля и нержавеющей стали.
Lockheed Martin напечатала на 3D-принтере титановые купола для космических кораблей [Изображение предоставлено Lockheed Martin]
Lockheed Martin — один из пользователей технологии EBAM. Аэрокосмическая компания применила его для создания двух гигантских куполов для резервуаров высокого давления, несущих топливо на борту спутников. Эта технология позволила Lockheed Martin напечатать на 3D-принтере два купола диаметром 116 см каждый за три месяца вместо двух лет, что на целых 87 процентов сократило время выполнения заказа.
Возможности 3D-печати металлом явно выходят за рамки простых компонентов, открывая возможность 3D-печати крупномасштабных деталей более быстрым и гибким способом.
Последнее заблуждение, которое мы обсудим сегодня, заключается в том, что повторное использование и переработка порошка в процессе PBF на основе лазера отрицательно влияет на свойства материала и приводит к ухудшению качества деталей.
В PBF после завершения процесса печати нерасплавленный порошок повторно используется, а затем смешивается с новым порошком в заданной пропорции.Однако инженеры, скептически относящиеся к переработке материалов, часто указывают максимальный возраст порошка и требуют от поставщиков AM выбросить весь старый порошок.
Тем не менее, многочисленные исследования доказывают, что повторное использование и переработка порошка с надлежащим контролем не только не влияет на механические свойства, но также позволяет использовать PBF на основе лазера как более эффективный и экономичный процесс AM.
Поставщик услуг 3D-печати, компания Stratasys Direct Manufacturing, например, провела углубленное исследование влияния вторичной переработки на детали, изготовленные из суперсплавов на основе никеля.Измеряя различные параметры, такие как прочность на разрыв и предел текучести деталей, напечатанных на 3D-принтере из переработанного материала, исследование показало, что переработка практически не влияет на свойства Inconel 718 и Inconel 625 при комнатной или повышенной температуре.
В другом исследовании Renishaw , производитель металлических 3D-принтеров, выполнил в общей сложности 38 сборок с использованием переработанного порошка Ti6Al4V ELI (Extra Low Interstitial) из титанового сплава. Компания пришла к выводу, что изменения в порошке за период исследования не были достаточно значительными, чтобы повлиять на настройки параметров материала, и нет никаких доказательств того, что потребуется утилизация порошка.
По мере того, как металлическая 3D-печать продолжает развиваться, один из способов сделать эту технологию более распространенной — информировать людей об истинных возможностях и ограничениях этой технологии.
В конечном итоге, вооруженная современными знаниями, металлургическая промышленность AM может быстрее продвигаться по пути индустриализации, открывая технологию для более широких рынков и приложений.
Система 3D-печати Metal X
Принтер Metal XMarkforged Metal X — это новый тип принтера по металлу.Печатая металлическим порошком в пластиковой матрице, Markforged стала первой компанией, которая устранила риски безопасности, связанные с традиционными металлическими 3D-принтерами. Это означает отсутствие рассыпчатого порошка, лазеров и традиционных мер предосторожности. Его безопасно использовать в магазине с минимальными модернизациями оборудования.
На практике Metal X — это, по сути, очень продвинутый 3D-принтер FFF. Metal X оснащен высокоточным порталом с механической обработкой, камерой с подогревом и станиной для печати, а также современным оборудованием для экструзии.Он специально разработан, чтобы изнашиваемые компоненты и расходные материалы, включая листы для печати, сопла и щетки, были доступны и легко заменялись.
Мойка-1Wash-1 — это система удаления связующего на основе растворителя. В основном он использует Opteon SF-79, высокоэффективную жидкость, разработанную для обеспечения превосходной очищающей способности, более высокой эффективности и безопасности без ущерба для окружающей среды — при необходимости можно заменить Opeton SF-80 или Tergo Metal Cleaning Fluid.
Wash-1 работает с простой вентиляцией и отличается чрезвычайно простым пользовательским интерфейсом. Это было протестировано и подтверждено как безопасная для магазинов система.
Синтер-2 и Синтер-1Markforged Sinter-2 и Sinter-1 — это высокооптимизированные трубчатые печи, используемые для спекания металлических деталей, напечатанных на 3D-принтере. Они обеспечивают лучшую в своем классе надежность спекания и время работы и оснащены передовыми функциями безопасности.Sinter-2 более продвинутый, чем Sinter-1, с большим рабочим объемом, более точным контролем температуры и механической блокировкой дверцы.
Агрегаты Sinter-1 и Sinter-2 обычно имеют время работы от 26 до 31 часа. Однако Sinter-2 может обрабатывать мелкие детали в экспресс-режиме, где он может спекать до 250 г деталей всего за 17 часов.
Нержавеющая сталь 17-4 PH — прочный металл Материал для 3D-печати
Сокращение сроков поставки металлических инструментов, приспособлений и прототипов
17-4 PH Нержавеющая сталь — это сталь многоцелевого назначения, используемая в промышленности.Markforged 17-4 PH, термообрабатываемый до твердости 36 HRC и обладающий 95% -ной прочностью на деформацию, позволяет печатать высокопрочные и прочные металлические детали для самых разных областей применения.
Приложения:
- Концевые инструменты
- Легкие кронштейны
- Универсальная износостойкая оснастка
- Функциональные прототипы
- Ключи и розетки на заказ
- 1050 МПа
- После спекания
- 1250 МПа
- термообработанные
- 30 HRC
- После спекания
- 36 HRC
- Термообработка.
Guhring UK
ЗаказчикОснованная в 1973 году компания Guhring UK — филиал группы Guhring в Бирмингеме — производит прецизионные режущие инструменты. Компания начинала как акционер более стандартизированных режущих и фрезерных инструментов.Сегодня Guhring UK производит специальные режущие и фрезерные инструменты для некоторых крупнейших мировых компаний, включая BMW, Jaguar Land Rover, Airbus и BAE Systems. Опыт Guhring в производстве режущего инструмента из карбида и поликристаллического алмаза (PCD) известен во всем мире. Их ассортимент инструментов PCD изготавливается по индивидуальному заказу в соответствии с требованиями клиентов и производится путем пайки алмазных режущих головок сверхвысокой твердости промышленного класса на специально изготовленные корпуса из закаленной инструментальной стали.
— Алан Пирс, руководитель производства PCD, Guhring UK
Задача
Каждая часть специального инструмента, производимого Guhring UK, сначала должна быть спроектирована и одобрена заказчиком.В зависимости от размера и сложности компонента на разработку, тестирование и производство специального инструмента может уйти до восьми недель, а работа над инструментом даже не может начаться, пока проект не будет одобрен. Более мелкие производители с меньшими объемами не могут оправдать затраты или время выполнения заказа на специальные инструменты.
«Когда мы начали искать клиентов в небольших объемах, это стало проблемой», — говорит Алан Пирс, руководитель производства ПХД в Guhring UK. Это побудило компанию рассмотреть аддитивное производство как возможность открыть новые потоки доходов, сократить время выполнения заказов для существующих и управлять сроками для более мелких клиентов.
Инженеры Guhring UK смогли быстро создать прототип режущего инструмента из композитных материалов, прежде чем печатать его из металла. Решение
Команда изучила промышленную 3D-печать, чтобы сделать свои продукты и услуги доступными для более широкого круга предприятий, особенно для небольших. «Идея заключалась в том, чтобы снизить стоимость прототипа и время итеративного цикла», — говорит Пирс. Они объединились с местным партнером Markforged Mark3D UK, чтобы найти лучший 3D-принтер для своих нужд, и выбрали систему Markforged Metal X, а также непрерывный волоконный 3D-принтер Markforged для образцов клиентов и технического обслуживания оборудования.Затем компания начала использовать свой 3D-принтер из углеродного волокна для изготовления небольших прототипов специальных инструментов и быстро обратилась к 3D-печати на металле для производства функциональных инструментов. «Теперь мы можем изготавливать единичную производственную деталь и поставлять ее заказчику менее чем в одной трети времени и с меньшими затратами», — говорит Пирс.
Наконечники инструментов были прикреплены к 3D-печатному телу перед шлифовкой до требуемой формы.
Первым 3D-печатным инструментом, изготовленным компанией Guhring UK, была базовая фреза с использованием инструментальной стали h23.«В течение одного дня мы спроектировали и напечатали инструмент из оникса [нейлона, смешанного с рубленым углеродным волокном], и мы могли сразу увидеть, собираемся ли мы столкнуться с какими-либо проблемами при его производстве. В течение пяти дней мы напечатали и спекли полностью функциональный корпус фрезы по металлу. Использование 3D-принтеров Markforged просто ускоряет все ». После добавления режущих головок Геринг квалифицировал фрезу, сначала протестировав ее как развертку для алюминия, и обнаружил, что она работает очень хорошо. Затем инженеры изменили конфигурацию геометрии наконечника инструмента и запустили инструмент, напечатанный на 3D-принтере, как фрезу, чтобы проверить его возможности со смещенной нагрузкой.Это тоже сработало точно так, как планировалось. Инструмент, напечатанный на 3D-принтере, на 60% легче своего традиционного предшественника, что позволяет быстрее менять инструмент в циклах и сокращать время цикла. Это открытие приложений позволило компании производить более универсальные и легкие инструменты для своих клиентов по гораздо более низкой цене.
Компания Guhring UK отправила клиентам металлические инструменты для 3D-печати для тестирования новых концепций. Будущее
Guhring UK теперь имеет возможность обслуживать малые предприятия, делая их продукты и услуги более доступными.Инженеры компании даже начали экспериментировать с напечатанными на 3D-принтере схемами подачи охлаждающей жидкости — один из первых клиентов Markforged, сделавших это. Дополнительные деньги, которые Guhring UK сэкономила, добавив 3D-принтеры Markforged, не будут потрачены зря, и Пирс сказал, что любые сэкономленные средства будут «реинвестированы обратно в компанию, чтобы мы могли продолжать расти и поставлять нашим клиентам более крупные и лучшие продукты. ” Что касается дополнительного сэкономленного времени, Пирс говорит, что оно будет направлено на изготовление производственных деталей.Добавление 3D-принтеров Markforged уже позволило инженерам освободить свои 5-осевые фрезы и традиционные технологии для производства других деталей, приносящих доход, что увеличило прибыль компании.
Шукла Медикал
ЗаказчикShukla Medical, дочерняя компания, полностью принадлежащая аэрокосмическому производителю S.S. White Technologies, разрабатывает и производит универсальные инструменты для удаления ортопедических имплантатов, такие как универсальная система удаления позвоночного имплантата Xtract-All® Spine (см. Изображение на обложке).Их продукция используется хирургами по всему миру для эффективного удаления старых имплантатов перед заменой их новыми, при этом сохраняя кость пациента. Большинство инструментов для удаления ортопедических имплантатов сложны и требуют значительного времени для работы, тогда как универсальные инструменты Shukla Medical известны своим простым и интуитивно понятным дизайном.
The Challenge
Продукция Shukla разработана для хирургов-ортопедов с такими функциями экономии времени, как быстрое соединение и несколько вариантов удаления.«Общеизвестно, что каждая минута в операционной обходится очень дорого, — сказал Зак Свейтцер, менеджер по разработке продуктов в Shukla Medical. «Так что любое время, которое вы можете сэкономить, очень полезно». Стоимость операционной может варьироваться от 35 до 100 долларов, хотя она варьируется в зависимости от больницы и хирургической процедуры. Инструменты Shukla должны быть быстро прототипированы и протестированы хирургами-ортопедами-имплантологами для проверки формы и соответствия перед изготовлением конечного продукта. Первоначально команда создавала прототипы деталей с помощью своего станка с ЧПУ или отправляла проекты третьей стороне, но обнаружила, что длительное время выполнения заказа значительно замедляет работу над прототипами и не позволяет им быстро вывести свой продукт на рынок.
— Адам Госик-Вулф, инженер-механик, Shukla Medical
Гнезда для вертолетов, которые позволяют полностью удалить винтовые конструкции, были первым прототипом, который позволил хирургам-ортопедам проверить форму и соответствие всего хирургического инструмента.
РешениеShukla Medical приобрела 3D-принтер Markforged, способный печатать на непрерывном углеродном волокне, в 2017 году и начала использовать его для создания прототипов своих инструментов вместо станка с ЧПУ.Это было фантастическое дополнение к возможностям команды. «Мы сильно нагружаем наши инструменты, и углеродное волокно придает им немного большей жесткости, поэтому они не кажутся игрушечными», — говорит Адам Госик-Вулф, инженер-механик в Shukla Medical. Но Адам и его команда хотели чего-то большего — они хотели металлические прототипы, чтобы хирургам было еще проще представить себе использование этого инструмента. Субраманья Наглапура, вице-президент по операциям в Shukla Medical, также увидел потенциал и поддержал покупку Metal X.После большого опыта работы со своим 3D-принтером Markforged из углеродного волокна, команда приняла решение добавить систему Metal X — при полной управленческой поддержке
Используя нержавеющую сталь 17-4 PH, Shukla Medical смогла создать прототип из того же материала, что и многие другие. готовой продукции. Теперь они используют свой 3D-принтер из углеродного волокна для первоначальных прототипов, а затем систему Metal X для окончательного прототипа, который передается в руки хирургов для оценки. «Хирург может представить себе, как он использует его в самом разрезе, и может сказать нам, правильно ли он чувствует себя в его руках», — говорит Свитцер.«Возможность более эффективного прототипирования и более быстрого вывода готовой продукции на рынок позволит нам оставаться в авангарде отрасли». 3D-принтер с непрерывным углеродным волокном также используется для изготовления мягких губок для любых деталей Metal X, требующих постобработки, что делает его и Metal X идеальным решением для 3D-печати для команды.
— Зак Свитцер, менеджер по развитию продукции в Shukla Medical
Shukla Medical создала прототип деталей, используя 3D-печать из нержавеющей стали 17-4 PH.
БудущееShukla Medical значительно сократила время коммерциализации своей продукции за счет использования 3D-принтера из углеродного волокна и системы Metal X. Инженеры S.S. White Technologies, дочерней компанией которой является Shukla Medical, часто используют принтеры Markforged для изготовления инструментов и приспособлений для аэрокосмической, автомобильной и медицинской промышленности. «Мы собираемся быстрее вывести на рынок намного больше продуктов с нашими принтерами Markforged, и, наконец, у нас появилась свобода дизайна для этого», — говорит Свитцер.
ученых ORNL разработали термостойкий материал для 3D-печати «Mighty Mo» EBM
Ученые из Национальной лаборатории Ок-Ридж (ORNL) разработали новую формулу молибдена (Mo), которая специально оптимизирована для использования с 3D-принтерами для электронно-лучевой плавки (EBM).
Смешивая порошки молибдена с карбидом титана (TiC), команда ORNL смогла создать материал «Mighty Mo», который преодолевает обычную хрупкость сплава и реактивность кислорода.После 3D-печати EBM композит с металлической матрицей дает плотные детали без трещин, которые способны выдерживать экстремальные температуры, что потенциально делает его идеальным для использования в сложных аэрокосмических приложениях.
«Наши результаты показали, что возможно изготовление из механически легированного композитного порошка с металлической матрицей», — сказал Майк Кирка из ORNL. «Структуры, образованные плавлеными порошками, могут выдерживать высокие температуры, что указывает на то, что молибден и его сплавы могут использоваться в аэрокосмической сфере и для преобразования энергии.”
SEM-изображение материала «Mighty Mo», напечатанного командой ORNL на 3D-принтере. Изображение предоставлено ORNL.Укрощение проблемных Пн
Молибден, как тугоплавкий металл, обладает рядом свойств, которые делают его привлекательным вариантом для использования в сверхчувствительных к температуре областях. Сплав характеризуется повышенной температурой плавления 2622 o ° C, а также низким коэффициентом теплового расширения, теплопроводностью и коррозионной стойкостью, но также известно, что он показывает низкую ударную вязкость при определенных температурах.
Кроме того, молибден чрезвычайно чувствителен к загрязнению азотом и кислородом во время обработки, что может вызвать сегрегацию границ его зерен, что приведет к растрескиванию деталей. В ограниченных исследованиях, которые уже были проведены в этой области, ученые смешали металл с другими материалами в попытке лучше контролировать его рекристаллизацию и размер зерна, но без особого эффекта.
Еще в 2017 году исследователям из австрийского производителя порошков Plansee Group удалось использовать данные моделирования для количественной оценки того, как размер частиц молибдена влияет на чувствительность печати SLM, но не решила проблему полностью.В отличие от этого, группа ORNL теперь обнаружила, что, добавляя частицы TiC в сплав и переходя на EBM, можно изготавливать микроструктуры с новыми уровнями прочности и жесткости.
Команда ORNL использовала настроенный 3D-принтер Arcam (на фото) для проведения своего исследования. Изображение из журнала «Аддитивное производство для энергетики».Формула ORNL «Могучий Мо»
Для создания своего материала ученые смешали порошки Mo и TiC в соотношении 60:40 внутри градуированного цилиндра, который был заполнен газообразным аргоном для предотвращения окисления.Затем полученный композит с металлической матрицей был механически сплавлен с использованием планетарной шаровой мельницы в течение восьми часов, пока он не был готов для 3D-печати.
Для обработки нового порошка команда ORNL разработала индивидуальный 3D-принтер Arcam S12 EBM с модифицированной камерой сборки, состоящей из поршня, питателя, грабли и системы подачи порошкового слоя со стола. Модернизация машины позволила эффективно оптимизировать ее для небольших сборок, обеспечивая при этом расширенный мониторинг процесса и подачу вторичного материала.
Используя свою машину, исследователи решили напечатать на 3D-принтере шесть деталей размером 12 мм (D) x 13 мм (H) с многослойными структурами, содержащими слой Mighty Mo, заключенный между двумя слоями чистого молибдена. Интересно, что изображение с помощью СЭМ показало, что ни один из чистых образцов не имел каких-либо трещин, но они действительно демонстрировали некоторые поверхностные несоответствия из-за растекания порошка.
Позже команда провела термодинамическое моделирование, которое также показало, что процесс остается чрезвычайно чувствительным к изменениям состава и температуры.В результате ученые ORNL предположили, что строгое управление входными данными процесса будет ключом к созданию будущих микроструктур из молибдена, не вызывая изменений в консистенции частичного слоя или температурных градиентах во время обработки.
В конечном итоге исследователи также пришли к выводу, что они продемонстрировали возможность 3D-печати чистого молибдена без трещин, а с усовершенствованным набором параметров сплав может найти новые применения в аэрокосмической отрасли или в секторах преобразования энергии, в таких областях, как теплопередача. составные части.
3D-печать на основе молибдена
Хотя 3D-печать чистого молибдена без трещин остается сложной задачей, ряду производителей материалов удалось смешать сплав с другими металлами, чтобы получить гораздо больше обрабатываемых продуктов. Например, заказчик компании Farsoon Hiwing Titanium Industrial недавно разработал термостойкий материал для 3D-печати TA32 с пропиткой молибденом.
Способный выдерживать рабочие температуры до 550 o C, этот металл разработан как альтернатива стали или суперсплавам на никелевой основе.Аналогичным образом, сингапурским ученым ранее удавалось улучшить печатные характеристики сплава Inconel 625, содержащего Мо, путем смешивания его с наночастицами диборида титана.
В другом месте производитель 3D-принтеров Meltio сообщил, что он также проверяет молибден для использования с последней версией своего патентованного движка Meltio Engine. Успешно протестировав нержавеющую сталь, инконель (718 и 625) и Ti-6Al-4V (сорта 5 и 23), компания теперь проверяет, среди прочего, медь, алюминий, вольфрам, X9 и золото.
Выводы исследователей подробно описаны в их статье под названием « Аддитивное производство чистого сплава Mo и Mo + TiC MMC с помощью электронно-лучевого порошкового сплава Fusion ». Соавторами исследования были Кристофер Рок, Эдгар Лара-Курцио, Бетси Эллис, Кристофер Ледфорд, Донован Н.