Калькулятор расчета количества арматуры и бетона для фундамента «Композит Групп Челябинск»
Варианты равнопрочной замены металлической на стеклопластиковую арматуру
Понятие равнопрочной замены представляет собой замену арматуры произведенной из стали, на арматуру из композитных материалов, которая имеет такую же прочность и схожие прочие физико-механические показатели. Под равнопрочным диаметром стеклопластиковой арматуры, будем понимать ее такой наружный диаметр, при котором прочность будет равна прочности аналога из металла заданного диаметра. Данные по замене приведены в таблице:
Металлическая арматура класса A-III (A400C)Ø | Арматура композитная полимерная стеклопластиковая (АКС)Ø |
---|---|
6 | 4 |
8 | 5,5 |
10 | 6 |
12 | 8 |
14 | 10 |
16 | 12 |
18 | 14 |
20 | 16 |
Варианты равнопрочной замены металлической на стеклопластиковую арматуру
Понятие равнопрочной замены представляет собой замену арматуры произведенной из стали, на арматуру из композитных материалов, которая имеет такую же прочность и схожие прочие физико-механические показатели.
Металлическая арматура класса A-III (A400C) Ø | Арматура композитная полимерная стеклопластиковая (АКС) Ø |
---|---|
6 | 4 |
8 | 5,5 |
10 | 6 |
12 | 8 |
14 | 10 |
16 | 12 |
18 | 14 |
20 | 16 |
Варианты равнопрочной замены металлической на стеклопластиковую арматуру
Понятие равнопрочной замены представляет собой замену арматуры произведенной из стали, на арматуру из композитных материалов, которая имеет такую же прочность и схожие прочие физико-механические показатели.
Металлическая арматура класса A-III (A400C)Ø | Арматура композитная полимерная стеклопластиковая (АКС) Ø |
---|---|
6 | 4 |
8 | 5,5 |
10 | 6 |
12 | 8 |
14 | 10 |
16 | 12 |
18 | 14 |
20 | 16 |
Калькулятор расчета стеклопластиковой арматуры
- Главная
- »
- О компании
- »
- Публикации
- »
- Статьи
- »
- Стеклопластиковая арматура
- »
- Калькулятор расчета стеклопластиковой арматуры
Как всем известно, бетон – не пластичный материал, поэтому под влиянием различных факторов обладает свойством трескаться и растягиваться. Чтобы бетонной конструкции придать прочность, ее нужно армировать. Арматура в железобетонных перекрытиях создает металлический прочный каркас и на себя принимает всю нагрузку растягивания. Один из самых важных этапов строительства — закупка строительных материалов подходящего объема и качества, в согласии с требованиями проектной документации. Чтобы узнать, сколько необходимо приобрести стальной арматуры необходимого диаметра, к примеру, для укладки фундамента малоэтажного дома, совсем необязательным является произведение сложных подсчетов.
Под равно прочностным диаметром при расчете стоимости стеклопластиковой арматуры понимается такой внешний диаметр арматуры, при котором прочность её соответствует прочности металлической арматуры данного диаметра.
Стальная арматура класс АIII (А400С)
Кол-во метров в тонне | Вес м.![]() | Диаметр, мм |
4505 | 0,22 | 6 |
2532 | 0,4 | 8 |
1621 | 0,62 | 10 |
1126 | 0,89 | 12 |
826 | 1,21 | 14 |
633 | 1,58 | 16 |
500 | 2 | 18 |
405 | 2,47 | 20 |
336 | 2,98 | 22 |
260 | 3,85 | 25 |
Стеклопластиковая арматура композиционная
Кол-во метров в тонн | Вес м.![]() | Диаметр, мм |
50000 | 0,02 | 4 |
50000 | 0,02 | 4 |
21276 | 0,049 | 6 |
13333 | 0,082 | 8 |
7936 | 0,134 | 10 |
5917 | 0,185 | 12 |
4065 | 0,276 | 14 |
2272 | 0,352 | 16 |
1724 | 0,44 | 18 |
1370 | 0,73 | 20 |
Познакомиться ближе с процессом производства композитной арматуры
Возврат к списку
Армирующие волокна — Vectorply
Введение
Стекловолокно: Е-стекло
Е-стекло («электрическое» стекло) на сегодняшний день является наиболее используемым волокном в армированных пластиковых композитах.
Во многих отраслях промышленности он составляет более 90% используемого армирования. Его основные преимущества:
- Низкая стоимость
- Высокая прочность
- Малый вес (относительно стали)
- Высокая химическая стойкость
Основные недостатки:
- Низкий модуль (по сравнению с другими армирующими волокнами)
- Низкая усталостная прочность (по сравнению с углеродными волокнами)
- Большой вес (по сравнению с другими армирующими волокнами)
- Высокая абразивность при механической обработке
- Склонность к коррозии под напряжением
Из-за его широкого использования преимущества имеют тенденцию перевешивать недостатки. Почти все стекловолокна продаются в виде прядей сгруппированных волокон или ровингов, связанных с определенным выходом. Урожайность — это количество ярдов ровинга на фунт. Метрической единицей измерения является TEX, который представляет собой вес в граммах на километр (1000 метров).
Уравнение для преобразования между TEX и доходностью (YPP):
Для армирующих тканей, соединенных стежками, типичные размеры используемых ровингов варьируются от 1800 до 113 (от 276 до 4390 TEX). Некоторые распространенные значения выхода стекла и диаметры нитей приведены в таблице ниже:
4400 113 24, 94, Т 2400 206 17, 67, МН 1100 450 17, 67, МН 735 675 13, 51, К 276 1800 13, 51, К
Диаметр отдельных нитей может быть важен, поскольку он представляет собой отношение площади поверхности волокна к его объему.
Меньшие диаметры нитей обеспечивают более высокое отношение площади поверхности к объему, что означает, что у смолы больше площади для связывания. В некоторых случаях филаменты меньшего размера могут давать несколько лучшие свойства. Стекловолокно: стекло E-CR
Стекло E-CR («электрическое» стекло, устойчивое к коррозии) представляет собой разновидность стекловолокна E, которое более устойчиво к разложению в сильнокислых средах. Основное различие между стеклом E и E-CR заключается в исключении оксида бора (B2O3) из базовой рецептуры. Это отличие привело к тому, что свинцовое стекло E-CR обычно называют «стеклом, не содержащим бора», и его можно найти во многих применениях, связанных с коррозией композитов, таких как трубы, отверждаемые на месте (CIPP), а также резервуары и трубы для хранения химикатов.
Стекловолокно: S-стекло
S-стекло (высокопрочное стекло) представляет собой улучшенное стекловолокно для использования в приложениях с более высокими структурными требованиями.
Он имеет значительно более высокую прочность и умеренно более высокую жесткость, чем стандартное волокно из Е-стекла. Плотность S-стекла немного ниже, чем у E-стекла (2,49 г/куб.см против 2,54 г/куб.см), следовательно, можно ожидать, что ламинат будет на 20-35% легче, чем эквивалент из волокна E-стекла. Стекло S-2 (а теперь и S-1) — это коммерческая версия стекла S, изготовленная с менее строгими невоенными спецификациями, но по своим свойствам она аналогична. Существуют и другие варианты высокопрочного стекловолокна, такие как базальтовое (также известное как R-стекло), которые также пытаются получить эквивалентные свойства S-стекла по более низкой цене.
Арамид
Арамидные волокна представляют собой высококристаллический ароматический полиамид, производимый экструдированием кислого раствора запатентованного предшественника. Арамидные волокна имеют очень низкую плотность и высокую удельную прочность на растяжение по сравнению с общедоступными армирующими волокнами. Они наиболее известны своим использованием в пуленепробиваемых жилетах, штанах для бензопилы, защитных перчатках и других устройствах, где требуется устойчивость к порезам и устойчивость к повреждениям.
Основные преимущества арамидных волокон:
- Легкий вес
- Высокая устойчивость к ударным повреждениям
- Высокая прочность на растяжение
- Умеренно высокий модуль упругости при растяжении (средний между E-стеклом и HS-углеродом)
- Отличное гашение вибрации
- Низкое (отрицательное) продольное тепловое расширение
Основными недостатками арамида являются:
- Очень низкая прочность на сжатие
- Восприимчивость к УФ-излучению
- Труднообрабатываемый
- Высокое влагопоглощение
- Очень высокое поперечное тепловое расширение
Арамидные волокна часто используются в сочетании с другими типами волокон. Это позволяет конструктору использовать их уникальные свойства и малый вес, избегая при этом недостатков. Арамидные волокна продаются в некрученых жгутах по денье (г/9000 м), что связано с пределом текучести или текс следующими уравнениями: аэрокосмической, спортивной, морской и инфраструктурной за последние несколько десятилетий.
Сочетание превосходной жесткости, прочности, сопротивления усталости и легкого веса делает его идеальным армирующим волокном для высокоэффективных композитов.
Свойства
По сравнению со всеми другими коммерчески доступными армирующими волокнами, углеродное волокно обеспечивает самый высокий удельный модуль и удельную прочность (модуль и/или прочность, деленные на плотность волокна), а также самый широкий диапазон этих свойств.
Другие свойства, такие как высокая усталостная прочность, тепло- и электропроводность, а также низкое тепловое расширение, позволяют использовать углеродное волокно там, где стандартное E-стекло или арамиды не могут. Многоосное армирование, такое как VectorUltra™, позволяет адаптировать эти уникальные свойства к конкретным потребностям любого применения.
Типы углеродного волокна на основе ПАН
На основе ПАН: Наиболее широко доступный и используемый тип углеродного волокна производится из волокна-предшественника полиакрилонитрила (ПАН) специального состава.
Углеродное волокно PAN, как правило, классифицируется по 3 различным группам в зависимости от модуля:
*Примечание: модуль, прочность и относительное удлинение клюва углеродного волокна являются идеальными значениями, полученными в результате испытаний пропитанной нити, и могут не применяться непосредственно к соответствующей ткани. /композитные свойства из-за смещения волокон, совместимости со смолой и повреждения во время обработки.
Углеродное волокно со стандартным модулем (SM) или высокой прочностью (HS) является наиболее широко используемым и экономичным волокном для промышленных применений, таких как судостроение, ветроэнергетика и транспорт. Этот тип волокна получил свое название от первых лет существования углеродного волокна, когда прочность на растяжение значительно снизилась при увеличении модуля. За это время прочность на растяжение стандартного модульного волокна достигла максимума около 500 тысяч фунтов на квадратный дюйм (3450 МПа), тогда как высокомодульные волокна были намного ниже, около 275 тысяч фунтов на квадратный дюйм (189 МПа).
0 МПа). Углеродные волокна HS по-прежнему имеют одни из самых высоких значений прочности среди всех армирующих волокон промышленного класса, а также модуль примерно в 3 раза больше, чем у стандартного E-стекла. Относительно высокое удлинение до разрыва (1,5-2,0% идеального волокна) углеродных волокон HS также позволяет использовать их в высокодинамичных приложениях, таких как корпуса яхт, мячи для софтбола и кожухи лопастей реактивных двигателей.
Волокна с промежуточным модулем (IM) были разработаны для высокопроизводительных аэрокосмических применений, которые требовали более высокой прочности и модуля, чем стандартные углеродные волокна HS. Несмотря на то, что углеродные волокна IM по-прежнему используются в основном в аэрокосмической отрасли, они также используются в высокопроизводительных сосудах высокого давления, лонжеронах парусных лодок и других промышленных применениях, где производительность перевешивает цену.
Высокомодульные (HM) волокна обычно используются в высококачественных спортивных товарах и космических конструкциях, где высокая жесткость и низкое или нулевое тепловое расширение обеспечивают оптимальный вес и характеристики.
Как правило, по мере увеличения модуля прочность снижается из-за повышенной кристаллизации волокна. За прошедшие годы были сделаны разработки для увеличения прочности волокон из ТМ, снижения их хрупкости (идеальное удлинение волокна до разрыва все еще составляет около 0,5-1,4%) и увеличения их использования. По мере увеличения модуля растет и цена, что делает HM-волокна самыми дорогими и наименее производимыми углеродными волокнами на основе PAN. Углеродные волокна IM и HM меньше в диаметре, чем волокна HS (5 мкм и 7 мкм соответственно), что обеспечивает более тонкий выход или значение TEX для того же размера жгута.
Размер жгута
Количество нитей на пряжу углеродного волокна обозначается как размер его жгута. Размер жгута обычно указывается в единицах «К» или тысячах нитей. Стандартные размеры жгута варьируются от 1К (1000 нитей) до 48К (48000 нитей) и иногда выше. В большинстве аэрокосмических приложений используются небольшие жгуты углерода, такие как 3K и 6K, в то время как в более промышленных приложениях используются жгуты 12K, 24K и 48K.
Как правило, жгуты меньшего размера производят более легкие ткани с хорошим покрытием, в то время как жгуты большего размера производят более тяжелые ткани. Производство жгутов меньшего размера также обходится дороже, чем жгутов большего размера (меньше материала производится при заданной настройке процесса), и, следовательно, они дороже.
Как рассчитать количество полимера и волокон в бетонной столешнице из стеклопластика
Как рассчитать дозу полимера для стеклопластика
Сухие полимеры
Для сухих полимеров просто дозируйте в процентах от общего количества вяжущего материала. Соблюдайте дозировку, рекомендованную производителем.
Например, если производитель рекомендует дозу 3,5% и у вас есть 33,4 фунта вяжущего материала, вам потребуется 1,2 фунта полимера.
Вам не нужно вносить какие-либо изменения в воду для смешивания.
Жидкие полимеры
Полимер чаще всего находится в жидкой форме, поэтому для расчетов правильного количества жидкого полимера необходимо знать содержание твердых веществ в жидком полимере.
Большинство коммерческих полимеров GFRC содержат около 50% твердых веществ. Два широко используемых бренда содержат 51% твердых веществ и 47% сухих веществ.
Если мы используем пример полимера с 51% твердых частиц, 51% веса жидкости составляют твердые частицы полимера, а остальные 49% — вода. Эта вода считается частью смешанной воды, используемой в GFRC.
Я пройдусь по расчетам, так как это становится немного сложным.
Давайте начнем с типичной коммерческой конструкции смеси GFRC, из которой получится 10 кв. футов подложки толщиной ¾ дюйма для GFRC:
- Песок: 33,4 фунта
- 6 % полимера при 51 % твердого вещества: 3,9 фунта
- Вода (0,32 В/Ц): 8,8 фунта
- Портландцемент (80%): 26,7 фунта
- Пуццолан (20%): 6,7 фунта
- 3% стекловолокно AR: 2,5 фунта (3% от общего веса неволокнистых материалов)
- Общий вес партии 82,0 фунта
Эта смесь содержит 33,4 фунта песка и 33,4 фунта (26,7+6,7) всего вяжущего материала.
Все добавки (сухие полимеры, пигменты, суперпластификаторы и т.д.) дозируются в расчете на общую массу вяжущего материала.
Доза 6% твердого полимера означает, что нам нужно 33,4 фунта * 0,06 (или 6%) = 2,0 фунта твердого полимера (не жидкий полимер). Чтобы рассчитать, сколько жидкого полимера (то, что выливается из ведра) необходимо, выполните такой расчет:
2,0 фунта твердых частиц полимера / 0,51 (или 51% содержания твердых веществ) = 3,9 фунта жидкого полимера
Если подумать, примерно половина жидкого полимера — это вода, а другая половина — твердые вещества, так что около 2 фунтов твердых веществ содержится примерно в 4 фунтах жидкого полимера.
Теперь для расчета воды замеса:
- Рассчитайте общее количество необходимой воды: 33,4 фунта вяжущего * 0,32 = 10,7 фунта воды
- Однако часть этой воды поступает из жидкого полимера. Итак, теперь нам нужно рассчитать, сколько воды выйдет из добавляемого нами полимера.
Мы уже подсчитали, что 3,9требуется фунт жидкого полимера, который содержит 2,0 фунта твердых частиц полимера, при этом жидкий полимер добавляет 1,9 фунта воды. (3,9 – 2,0 = 1,9) - Теперь вычтите эту воду из необходимого количества. 10,7 фунта – 1,9 фунта = 8,8 фунта воды для добавления .
Изменение соотношения вода/цемент изменяет только то, сколько воды мы должны дозировать (больше или меньше 8,8 фунтов), но не изменяет количество необходимого жидкого полимера.
Как рассчитать нагрузку на волокно для GFRC
В отличие от других добавок, фибра не дозируется в расчете на сухую массу вяжущего. Нагрузка волокна 3 % означает, что к 97 фунтам неволокнистого материала добавляется 3 фунта волокна, чтобы получить 100 фунтов подложки из стеклопластика. Минимальная эффективная нагрузка волокна для GFRC составляет 3%.
Сначала мы должны определить, сколько у нас неволокнистого материала. Суммируя наши ингредиенты (все, кроме волокон), мы имеем:
33,4 фунта песка + 26,7 фунта цемента + 6,7 фунта пуццолана + 3,9 фунта жидкого полимера + 8,8 фунта воды = 79,5 фунтов неволокнистого материала
Таким образом, вместо 97 фунтов материала у нас есть 79,5 фунтов материала.
Мы можем использовать отношения, чтобы найти количество добавляемых волокон:
- По-английски: 79,5 фунтов равно 97 фунтам, как (неизвестное количество волокон) равно 3 фунтам.
- В математических терминах: 79,5/97 = х/3.
Чтобы найти x, просто умножьте обе части на 3, чтобы исключить 3 справа.
79,5 / 97 * 3 = 2,458 фунта необходимого волокна . (В приведенном выше примере округлено до 2,5.)
Общая сумма покровителя составит 79,5 фунтов + 2,5 фунта = 82,0 фунта .
Другой способ расчета смеси GFRC
Эти расчеты сложны, но необходимы для правильного расчета смеси GFRC. Я включил их, чтобы дать вам полное представление о расчетах смеси GFRC. Легче представить смеси GFRC партиями по 10 кв. футов, которые вы затем можете умножить на количество единиц в 10 кв. футов, которые у вас есть.
Например, если вам нужно изготовить 52 кв. фута стеклопластика, вы можете просто умножить партию в 10 кв.
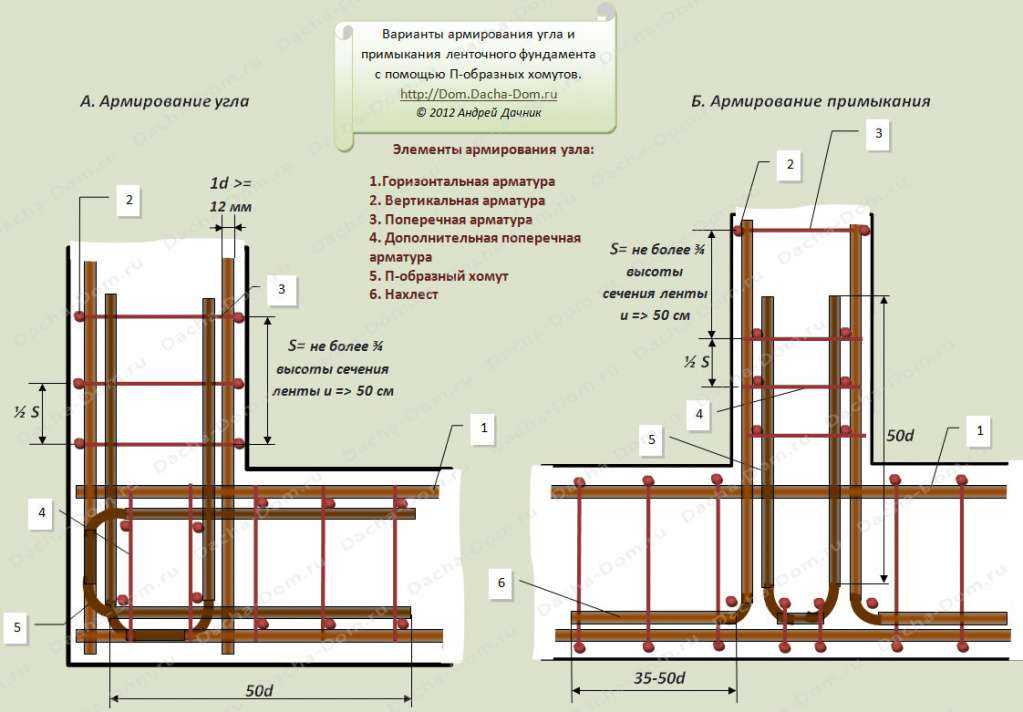
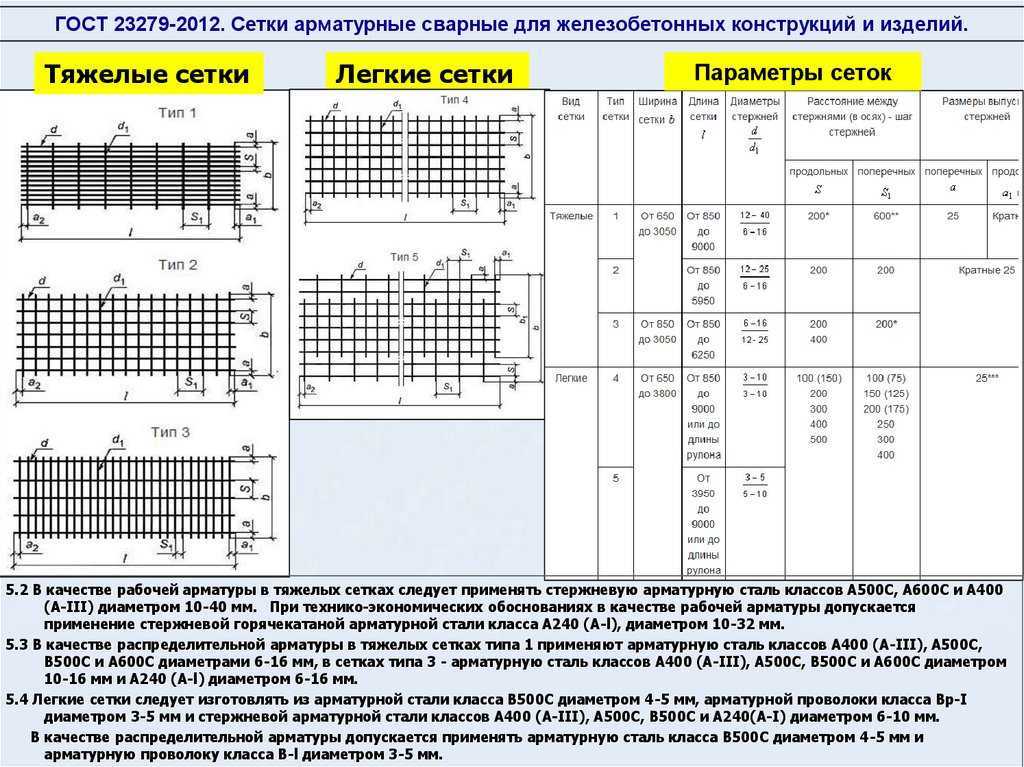
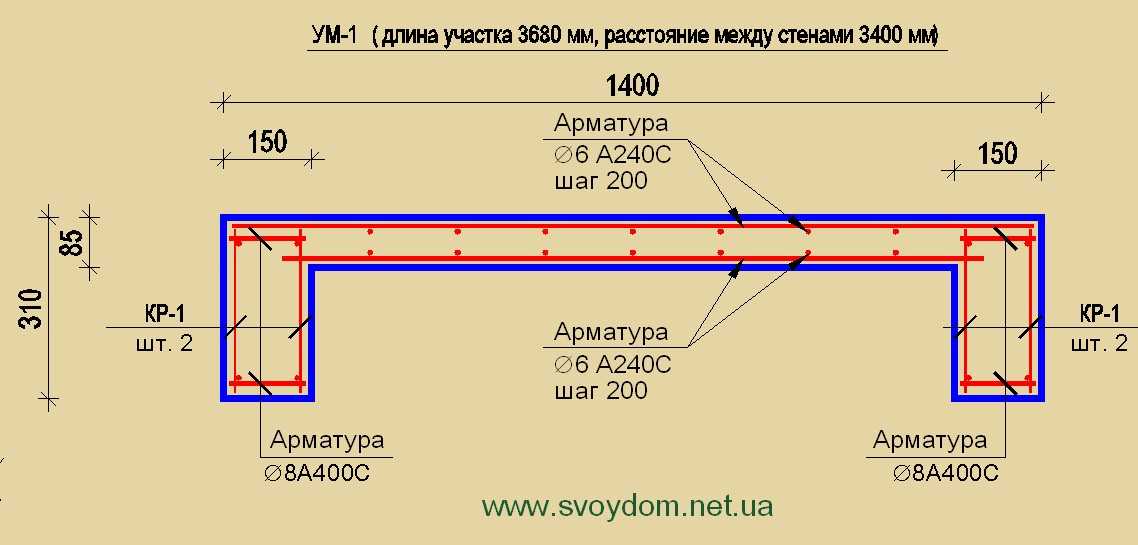
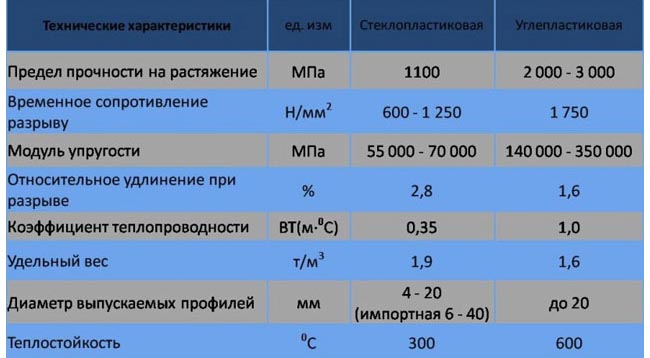
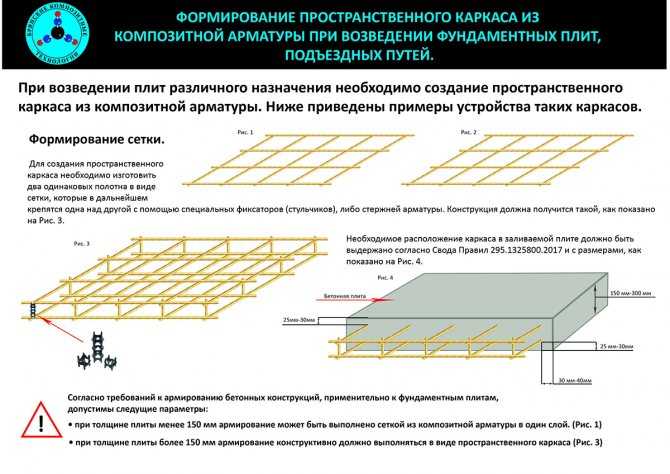
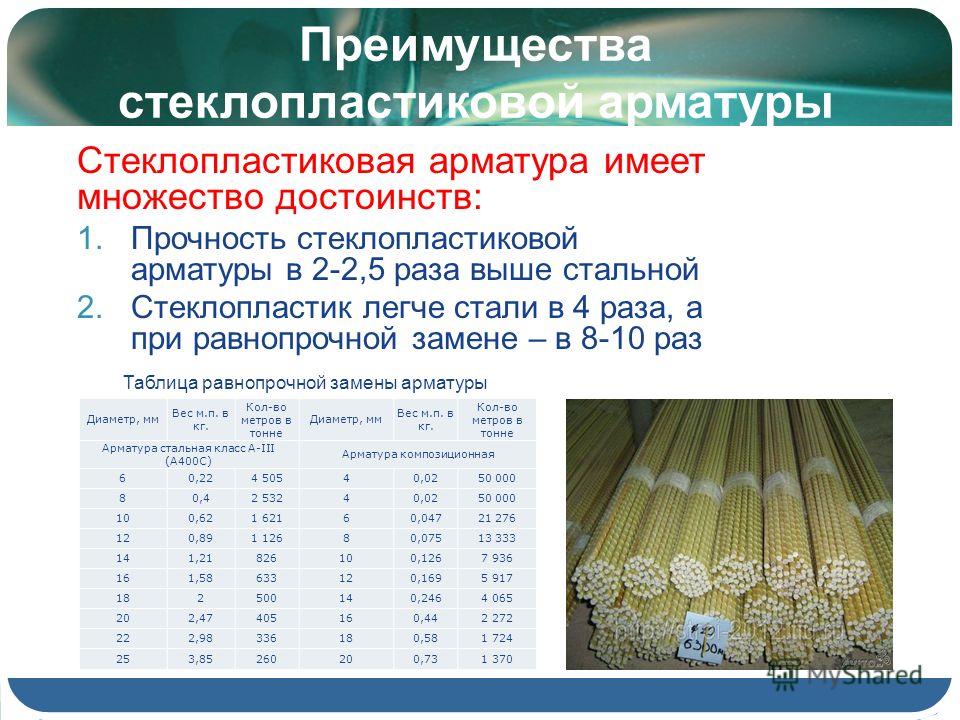

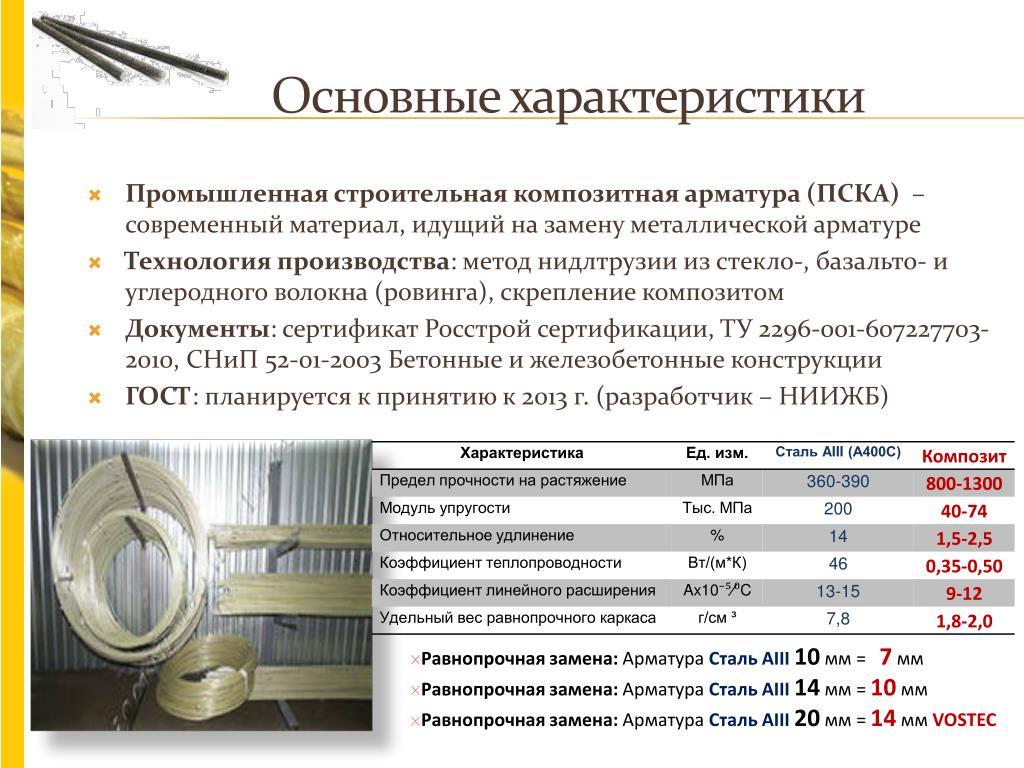
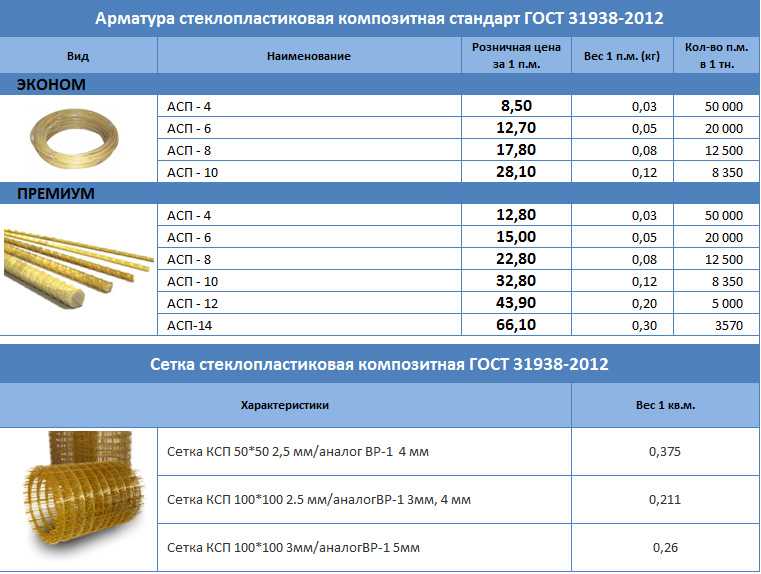

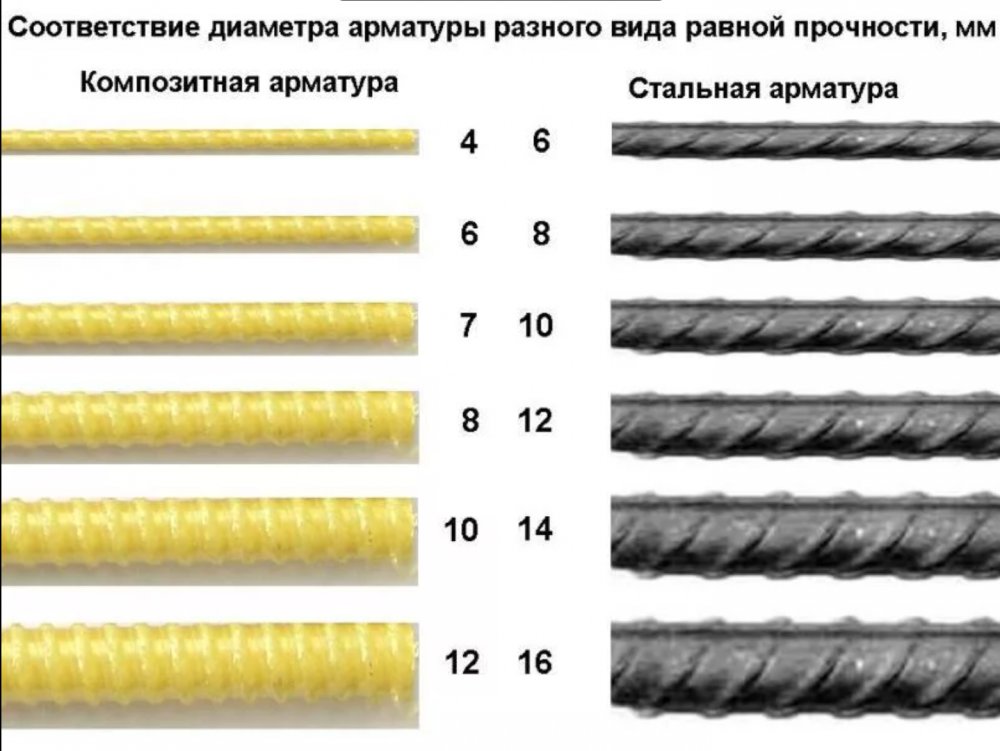
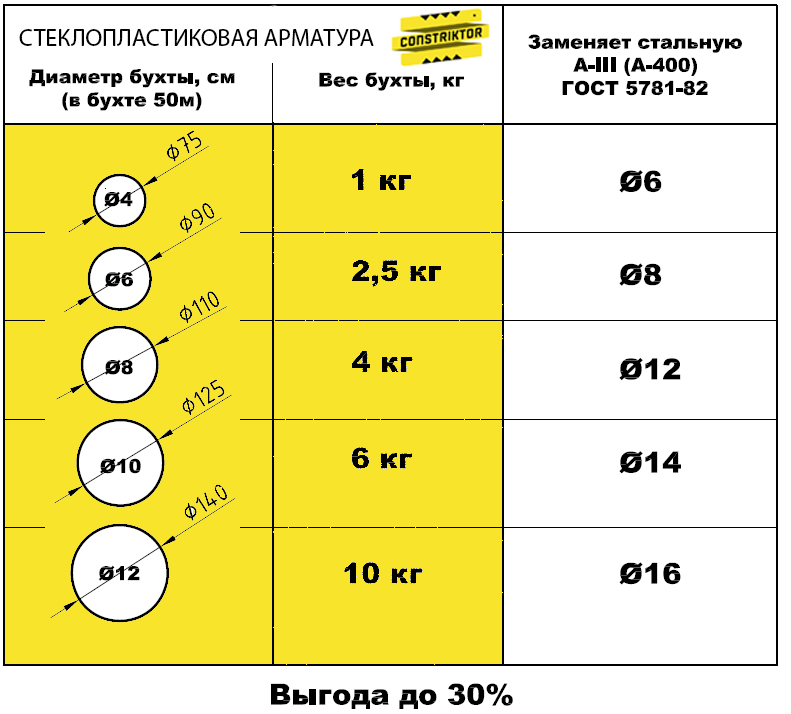
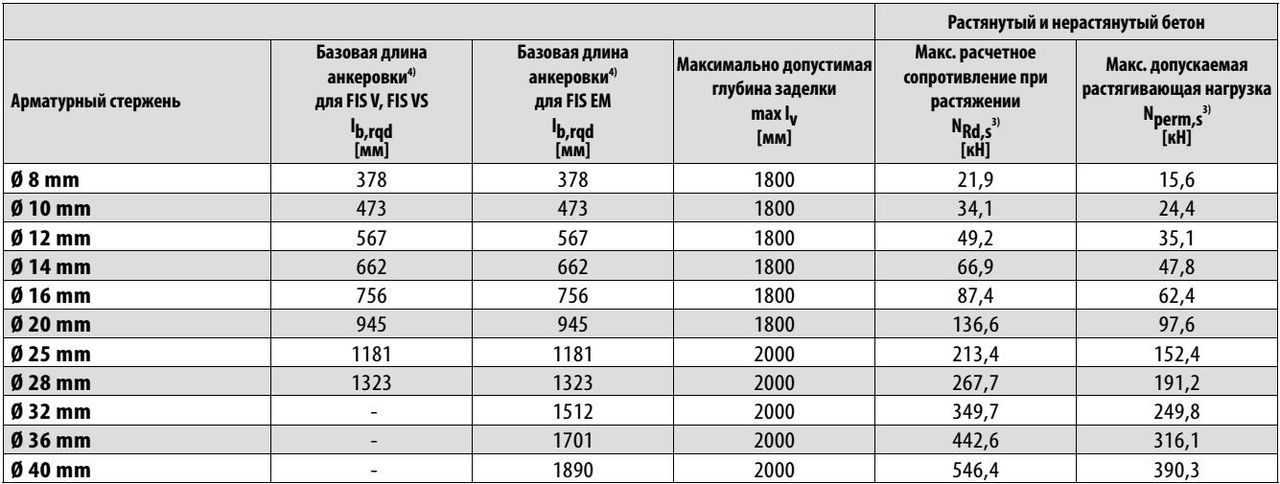
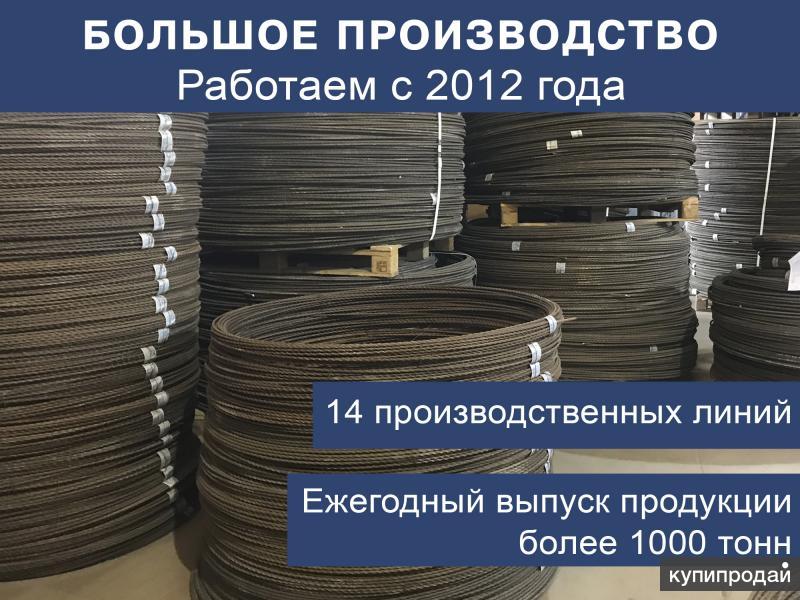
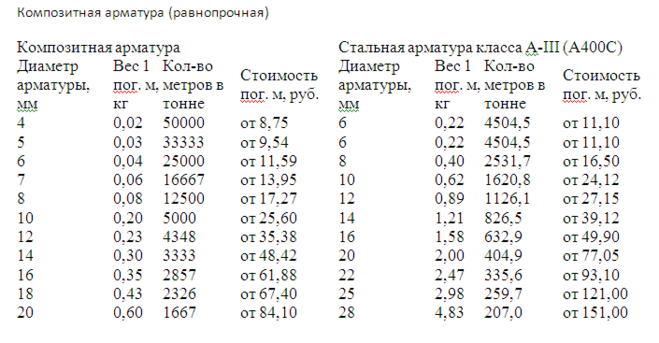