Технология производства бетона
Технология производства бетона подразумевает смешивание воды, цемента, заполнителей в виде песка или щебня и, в некоторых случаях, различных химических добавок. Не существует одной единой технологии изготовления бетона, поскольку в каждом отдельном случае свойства готового продукта должны опираться на условия окружающей среды, требования по прочности и твёрдости бетона.
Вопросом «рецептуры» цемента занимались русские учёные Н.М. Беляев, С.А. Миронов, Н.А. Попов и другие. Сформулированные ими принципы сделали возможным изготовление бетона с заранее известными свойствами. Качество итогового продукта определяется химическими и физическими параметрами составных частей смеси.
Производство бетона в Москве – востребованный, динамично развивающийся бизнес, одним из бесспорных лидеров которого является компания «СтройПоставка». Молодая компания, которая накопила огромный опыт в производстве качественного строительного материала, создала мощную производственную базу и готова выполнить заказы любых объемов с высоким качеством.
Состав бетонной смеси
Крупный заполнитель: гравий (естественные обломки горных пород, имеют обкатанную, овальную форму) и щебень (продукт искусственного дробления камня). Крупный заполнитель имеет функцию «скелета» будущего бетонного изделия, а значит, гранулы должны быть прочными. Гравий для этой роли предпочтительнее по причине своей естественной формы. Также в качестве крупных заполнителей могут использоваться пемза и шлаки. Они буквально всасывают из цемента лишнюю воду, что положительно сказывается на прочности, но требует добавления большего количества цемента. |
Мелкий заполнитель: песок. Следует отметить, что песок бывает различного происхождения и в каждом случае это совершенно отдельный строительный материал. Пески разделяются по минералогическому составу (кварцевые, полевошпатные, известняковые и доломитовые), и по происхождению (горные, овражные, речные, морские, гравийные, валунные, дюнные и барханные). |
Вода. При производстве бетона используется вода, по возможности очищенная от химических примесей (сульфаты, кислоты, жиры и т.д.). Запрещается использовать морскую воду для строительства: высокая концентрация солей делает раствор хрупким. |
Цемент. Его функция в связывании между собой частиц заполнителя. Чем выше вяжущее свойство цемента, тем качественнее получится раствор. Цемент изготавливается из клинкера — обожжённого естественного сырья или искусственной смеси. |
Технология производства
В лаборатории составляется точная пропорция всех компонентов, которые необходимо загрузить в бетономешалку для получения продукта оптимального качества. Смешивание компонентов с водой происходит в течение длительного времени, после чего бетонная смесь достигает полной однородности. В случае, если производство смеси осуществляется не на строительной площадки, необходимо доставить продукт к месту назначения, не допустив расслоения состава. Для этого применяются специальные машины — автобетоносмесители.
Подготовленный таким образом бетон отгружается получателям. Во избежание расслаивания смеси во время транспортировки и потери свойств, доставку готового бетона необходимо осуществлять с использованием специального транспорта осуществляющим перемешивание, предотвращающим замерзание смеси в холодное время и потерю влаги при высоких температурах.
Условий поставки бетона, аналогичных существующим в компании «СтройПоставка» не предложит никто!
Технология производства бетона на заводе.
На практике дело обстоит несколько сложнее. Трудно самому постоянно замешивать большие партии материала со стабильно высоким качеством. Поэтому для больших и сложных объектов приобрести бетон лучше в готовом виде и у профессионалов. Компания «Бетон центр» готова продать нужный объем смесей с собственного завода по их производству. А к самостоятельному изготовлению бетона вы сможете прибегнуть при несложном строительстве или ремонте.
Производственный цикл
Технология производства бетона на заводе в Твери предусматривает несколько этапов.
- Сначала подготавливаются все необходимые ингредиенты. Цемент, щебень и песок просеиваются. На нашем предприятии организованы складские запасы. Поскольку смесь быстро схватывается, невозможно произвольно приостанавливать и возобновлять производственный процесс. Если любой из ингредиентов неожиданно закончится, всю партию придется отбраковывать.
- Подготовленные ингредиенты смешиваются в нужной пропорции. Соотношение зависит от марки и некоторых особенностей состава смеси. Доля цемента прямо пропорциональна марке бетона. Концентрацию вяжущего можно немного снижать, если брать цемент с более высокой маркой. Одновременно с этим корректируют соотношение других компонентов. В зависимости от условий транспортировки и других требований могут использоваться специальные присадки.
- Ингредиенты тщательно размешиваются до равномерной консистенции. Затем смесь сразу же отгружается в автобетоносмесители и доставляется на стройплощадки. Миксеры — стандартный и наиболее эффективный способ перевозки.
Контроль качества
Оборудование для производства бетона, совершенная технология, оптимизация работы предприятия и прочее не имеют значения, если на заводе не контролируется качество продукции. Только мероприятия по контролю технологии производства могут гарантировать, что бетонирующие смеси обладают всеми нужными свойствами.
Используются визуальные и лабораторные методы контроля. В последнем случае отбираются образцы смесей. Они формуются в виде небольших кубов и выдерживаются в определенных условиях. Далее застывший бетон помещается под пресс. Максимальное давление и характер деформации фиксируются. На основе полученных данных делаются выводы, насколько правильно организованы производственные процессы. Узнать о результатах проверок на нашем предприятии можно по номеру 8-800-222-15-05 или 8-920-150-31-00.
Оборудование для производства бетона – мобильное и стационарное
Бетонный раствор незаменим во многих отраслях строительных работ и при ремонте. Замешивать его вручную достаточно трудоемко, но технология изготовления материала достаточно проста. В промышленных масштабах бетон производится на крупных заводах, для малого потребления раствора используют бетономешалки. А вот владельцы строительных компаний, занимающие средний сегмент рынка, стараются приобрести оборудование для производства бетона, чтобы обеспечить свои нужды в полном объеме. Кстати, это является неплохой идеей и для малого бизнеса. Мини-завод по выпуску бетонных смесей на сегодняшний день является актуальным, особенно в регионах, где ведется интенсивное строительство.
Бетон: технология изготовления
На сегодня наиболее востребованным из всех строительных материалов является бетон. Без его присутствия сложно возвести кирпичный или монолитный дом, выполнить стяжку под напольное покрытие или кровлю, отремонтировать лестницу или стену, выложить пешеходную дорожку или смонтировать колодец. Бетон настолько окружил повседневную жизнь человека, что никто даже не задумывается над альтернативой, которой до сих пор не существует.
Близкий аналог бетона известен еще с древнеримских времен, но его состав несколько отличался. В то время в качестве связующего не использовали цемент. Он был изобретен и запатентован намного позже, в первой половине 19 века, каменщиком из Англии Джозефом Аспдином. Порошок серого цвета получил тогда название «Портландцемент» в честь серых скал, раскинувшихся неподалеку от английской гавани Портленд. О современном бетоне, производимом на цементном вяжущем, стало известно лишь в 1844 году.
Необходимое сырье для производства бетонаВ настоящее время производится большой ассортимент различных видов бетона. Каждый из них классифицируется по целому ряду признаков, назначению, маркам и добавкам. В состав классического бетонного раствора в обязательном порядке входят следующие компоненты:
- цемент – серый порошок с содержанием известняка, превращающийся в твердую глыбу при увлажнении. Цемент является основой бетонной смеси, ее связующим веществом;
- карьерный песок – размер песчинок зависит от возможного применения готового бетонного раствора.
Он может варьировать в пределах 0,65-2,5мм;
- щебень – дробленые твердые горные породы, колотый кирпич, шлаки, керамзит. Материал должен быть плотным, прочным, морозоустойчивым, иметь как можно меньший показатель лещадности (содержание пластинчатых и игольчатых зерен). Щебень подразделяется на гранитный и гравийный, известковый и доломитовый;
- балласт – наиболее подходящий состав содержит одну часть речного песка и три части гравийной крошки;
- вода – без примесей и каких-либо включений. Ее объем определяется ориентировочно, а окончательное количество складывается «по месту», в процессе приготовления бетонной смеси.
Примерное соотношение ингредиентов для правильного замеса классического бетона: на три части цемента берется пять частей песка и 10 частей щебня. Сухие составляющие смешиваются, а затем подается вода. Но пропорции могут быть и другими.
Чтобы получился бетон определенной прочности, марку цемента для приготовления смеси выбирают в 2-3 раза выше.
![]()
В процессе изготовления бетона предпринимателю, взявшему в аренду или купившему оборудование для производства бетона, придется столкнуться и с дополнительными работами:
- разведением химических добавок;
- подогревом заполнителей;
- цементным помолом.
Химдобавки растворяют в чистой воде до определенной концентрации. Для этого используются емкости с химически устойчивой системой трубопроводов, где добавки смешиваются под действием сжатого воздуха.
Хранящиеся на открытом воздухе в холодный период года заполнители (щебень, песок) прогревают на крытых складах, либо в бункерах. Наиболее экономичным, но не слишком эффективным, является вариант пропускания сквозь материалы горячего воздуха. Но прогрев в специальном бункере с помощью паровых труб предпочтительнее, особенно в случае постоянно действующего производства.
Помол цемента производится не всегда, хотя благодаря данному процессу конечный продукт затвердевает намного быстрее.
Мобильное оборудование и мини-заводы по производству бетона
Как правило, рассматриваемое оборудование имеет целую систему автоматизированных линий. Это повышает качество бетона на выходе. Но вовсе не обязательно, что мини-заводик должен иметь всю комплектацию оборудования для производства бетона. Стоимость минимальной и максимальной сборки может разниться в 3-4 раза. Поэтому, составляя бизнес-план, следует хорошо все взвесить и решить, какая именно линия должна быть установлена на определенной площадке.
На оставшиеся средства не следует покупать не востребованное оборудование. Будет правильнее приобрести автобетоносмеситель для доставки потребителю бетонной смеси. Это поможет привлечь новых заказчиков.
Для строительной компании очень выгодно приобретение мобильного оборудования. Оно может кочевать вместе с перемещением строительных бригад с одного объекта на другой, особенно если они находятся вдалеке от населенных пунктов.
В состав мини-заводов могут входить следующие линии:
- силосы;
- дозаторы;
- смесители;
- конвейеры;
- шнеки;
- подъемники;
- погрузчики;
- снижатели;
- кабины с пультами управления.
Несмотря на высокую стоимость оборудования по производству бетонных растворов, оно считается быстро окупаемым. При стабильном спросе и работе на полную мощность, мини-завод способен принести достаточно высокую месячную прибыль своему хозяину. И это при том, что для обслуживания оборудования потребуется всего лишь 3-4 человека.
Для возможности полноценного функционирования оборудования по производству бетона, на выделенной территории и за ее пределами обустраивают склады для хранения сыпучих материалов, подъездные пути и площадки отдыха для персонала и водителей. Желательно присутствие поблизости магистральных водопроводов или скважин с возможностью выкачки большого объема воды.
Мобильное оборудование, установленное непосредственно на строительной площадке, позволит свести к минимуму материальные и временные расходы на транспортировку бетонного раствора к месту укладки. Оно полностью избавит строящийся объект от зависимости в отношении поставщиков, которые, к сожалению, не всегда придерживаются своих обязательств. Раствор всегда будет подаваться вовремя и в нужном количестве.
Передвижные заводы по производству бетона компактны и удобны, перевозить их можно на одном грузовом автомобиле, а их установка на новом месте дислокации займет всего лишь день.
В качестве стационарного оборудования производители предлагают не только огромные комплексы, но и мини-линии. Они имеют сравнительно невысокую стоимость и требуют малую площадь при размещении. Производительность установки невелика, а процесс не полностью автоматизирован, но для небольшого предприятия это вполне приемлемо.
Производство бетона технология, производства тяжелого, ячеистого, прозрачный бетон, технологический процесс, монолитного
При производстве бетона технология, а точнее точное ее соблюдение, является основой для получения качественного продукта. Так как существует несколько видов бетона, то и способы приготовления будут отличаться.
Производство бетона и технологический процесс
- Процесс производства начинается с подбора состава. Обязательно учитывается тип бетона, который нужно получить на выходе. Он должен отвечать требованиям морозостойкости, плотности, подвижности, водонепроницаемости. Так же рассчитывают правильное соотношение компонентов.
- Далее происходит загрузка ингредиентов в бетоносмесители и тщательное перемешивание.
- Следующий этап — транспортировка на объект. Перевозка смесей осуществляется только специальной техникой.
Технология производства тяжелого бетона
Тяжелый бетон — материал повышенной плотности, который используется в строительстве мостов, хранилищ, монолитных фундаментов. Для его изготовления берут прочные наполнители (гранитный или гравийный щебень), песок, цемент и химические добавки, повышающие его полезные свойства.
Все компоненты, очищенные от ненужных примесей, загружают в бетоносмеситель и тщательно перемешивают. На выходе смесь должна соответствовать ГОСТу. Крупные заводы имеют свою собственную лабораторию для контроля качества.
Технология производства ячеистого бетона
Ячеистый бетон отличается по составу и способу приготовления от обычных растворов. Это пористый и легкий материал. Достичь пористости можно разными способами. При производстве газобетона, в смесь из цемента, извести, песка и воды добавляют алюминиевую пасту. Она вступает в реакцию с известью и образует водород. Таким образом, происходит вспучивание материала. Пенобетон делают по другой технологии. Поры получают при введении в раствор специального пенообразователя.
Технология производства монолитного бетона
Монолитный бетон используется при возведении домов. Это достаточно новый вид строительства. Смысл заключается в следующем: в опалубку помещают каркас из арматуры и заливают его готовой бетонной смесью, состоящей из песка, цемента, воды и щебня. Такой способ удобен и менее затратен, так как сокращает расходы на технику и позволяет осуществлять все работы непосредственно на объекте.
Прозрачный бетон технология производства
Технология приготовления этого вида бетона существенно отличается от замешивания стандартной смеси. В специальный короб заливают часть мелкозернистого раствора бетона. Вторым слоем укладывают специальное стекловолокно и немного утапливают его в раствор. Чередование слоев происходит до заполнения короба. Во время приготовления каждому слою дают время схватиться. После высыхания плиту шлифуют и полируют.
Прозрачный бетон — это современный, прочный материал. Он имеет привлекательный внешний вид и способность пропускать солнечный свет.
Компания «НИКС-К» предлагает купить товарный бетон по низким ценам от производителя. Мы на рынке с 2002 года и успешно сотрудничаем с крупными предприятиями.
Сотрудничать с «НИКС-К» выгодно
- Возможность приобрести продукцию оптом и в розницу.
- Доставка осуществляется в любую точку Москвы и области.
- Собственный парк спецтехники.
- Удобство заказа: по телефону, электронной почте или лично на заводе.
- Скидки от объема закупки.
- Продукция соответствует ГОСТ и проверяется в собственной лаборатории.
Технология приготовления бетонной смеси — Статьи — Стройка.ру
Основные требования к материалам для приготовления бетонной смеси
Наименование материала |
Комментарии |
---|---|
Цемент | Портландцемент применяется в том случае, если среднесуточная температура ниже +10°С. При высокой температуре используется шлакопортландцемент. Хранение цемента – только в герметичной таре (в противном случае он быстро впитает влагу из воздуха и начнет твердеть). |
Песок | Для того, чтобы избавиться от инородных включений, песок следует просеять (в случае применения неочищенного песка расход цемента может увеличиться на 20%). Диаметр зерен – до 2 мм. |
Щебень | Используйте щебень из мелкого речного гравия или горных пород.![]() |
Известь | Применяется как для повышения удобоукладываемости раствора, так и для получения цементно-известковых растворов. При работе обязательно защитите кожу рук, не допускайте попадания извести в глаза! |
Добавки | Использование добавок так или иначе влияет на качество конечного продукта. Пластификаторы повышают текучесть смеси. Суперпластификаторы увеличивают прочность и морозостойкость. Существуют специальные ускорители/замедлители твердения раствора. Аэрирующие добавки также повышают морозостойкость, снижая при этом влагоемкость бетона. |
Вода | Ее качество регламентировано ГОСтом (не допустимо наличие примесей – как химического, так и биологического происхождения). |
Рецепт приготовления бетона В7,5 М100
Бетон указанной марки используется в подготовительных работах: укладывается на песчаную подушку фундамента, после чего можно начинать арматурные работы. Применяется и в дорожном строительстве (в качестве основания для бордюрного камня).
Количество | Цемент, кг | Песок, кг | Вода, литр |
---|---|---|---|
Расчет для 1 куб. м | 160 | 2200 | 75 |
Расчет на мешок цемента (25 кг) | 25 (1 мешок) | 344 | 11 |
Рецепт приготовления бетона В15 М200
Данная марка бетона отличается разнообразными областями применения (изготовление бетонных стяжек; отмосток; различного типа фундаментов; лестниц; дорожное строительство).
Количество | Цемент, кг | Песок, кг | Гравий, кг | Вода, литр | |
---|---|---|---|---|---|
Расчет для 1 куб. м | 275 | 590 | 1377 | 165 | |
Расчет на мешок цемента (25 кг) | 25 (1 мешок) | 54 | 125 | 15 | |
Расчет на бетономешалку (200 л) | 44 | 94 | 220 | 26 |
Правила бетонирования
- Установите бетономешалку максимально близко к месту бетонирования (перевозка смеси на тачке допустима лишь на расстояние до 40 м).
- Набрасывайте смесь с высоты не более 1 м, дабы избежать расслоения составляющих.
- Для укладки жидкой смеси используйте желобы (высота – не более 50 см).
- Не начинайте бетонирование во время дождя, жары, низкой (ниже +5°С) температуры.
- Следите за временем! Максимально допустимый перерыв в бетонировании составляет 3 часа.
- Если за время перерыва смесь успела затвердеть, сбейте верхний слой молотком, очистите и смочите водой.
- Трамбовать уложенную смесь можно вручную – при помощи стального прута. Оптимальная толщина слоя для штыкования – не более 20 см.
- Если смесь приобрела пластичное состояние, то штыковать ее следует сплющенной на конце деревянной палкой.
- В местах укладки арматуры смесь, помимо штыкования, нужно простучать.
- Обязательно дайте бетону схватиться! В случае использования портландцемента достаточно 7 дней, 2 недели потребуются для шлакопортландцемента.
- Не забывайте поливать бетон водой во время жары. Для защиты от солнечных лучей, ветра или осадков можно использовать пленку.
- Если все-таки пришлось готовить смесь при низкой температуре, то компоненты можно подогреть с помощью горячей воды (это правило не касается тех случаев, когда в состав смеси введены противоморозные добавки).
Удачной работы!
Прочтений: 4133 Распечатать Поделиться:Мой мир
Вконтакте
Одноклассники
Какие характеристики указываются согласно ГОСТ при производстве бетона?
бетон бетонные работы
12.05.2020 | Стройка.ру
Как выбрать бетономешалку для строительства дома или дачи? Какую бетономешалку купить, чтобы она прослужила вам верой и правдой долгие годы?
бетон бетоносмеситель бетономешалка бетонные работы
26. 04.2020 | Стройка.ру
Бетон представляет собой материал, который получается при смешивании нескольких ингредиентов с водой и последующим затвердевании этой смеси.
бетон бетоносмеситель автобетоносмеситель бетонолом бетонолом-экскаватор аренда бетононасоса бетонный завод бетономешалка бетонные работы бадья для бетона
10.06.2019 | Стройка.ру
Вы должны понимать, что от уровня надежности бетонного раствора зависит надежность самого строения: очень внимательно отнеситесь к соотношению компонентов в готовой смечи и соответствие требованиям стандартов.
бетон бетоносмеситель автобетоносмеситель
17. 05.2019 | Стройка.ру
Речь пойдет о домах площадью до 150 квадратных метров, рассчитанных в основном на сезонное проживание в дачных обществах.
бетон бетонные работы
03.04.2019 | Стройка.ру
Технология производства и применение бетона
Этот продукт использовался ещё многие столетия тому назад и сегодня стал непременным атрибутом любой стройки. Технологический прогресс не смог не влиять на специфику производства, но все так же наиболее широко применяются всего несколько подвидов бетона с завода, соответствующего определенным строительным требованиям.
За счёт чего он бывает разным?
С одной стороны, эксплуатационные характеристики будущего продукта зависят от пропорций основных компонентов:
- связующее вещество — портландцемент, гипс и прочее;
- песок;
- наполнитель — гравий, щебень;
- жидкость — вода, щелочные растворы.
С другой стороны, будущие параметры зависят от выбранного компонента в каждом отдельном случае. Так, наиболее распространённые цементные продукты изготавливают из портландцемента (шлакопортландцемента, пуццоланового цемента), речного песка (промытого и очищенного карьерного), гравия и воды. А вот силикатные производят из негашёной перетёртой извести, фракционированного кварцевого песка, простого кварцевого песка и воды. Зачастую разница между разными видами продукта заключается только в одном компоненте. Например, цементный от шлакощелочного отличается только тем, что в первом случае используется вода, а во втором — щелочной раствор.
Стоит отметить, что большую роль в качестве итогового материала играет корректное следование стандартизированному производственному процессу. Например, если применить простой карьерный песок, то итоговые прочностные характеристики неизменно пострадают, поскольку в таком компоненте обязательно присутствует мелкая пыль, органические и земляные вкрапления.
Безграничные сферы применения
Стоит отметить, что вариативность характеристик продукта достаточно широка и всегда можно добиться получения материала, который сильно отличается от массовых решений. Показателен пример, с которым столкнулись строители известного небоскрёба — «Башен Петронас» в Куала-Лумпур. Малайзия не производит достаточно стали, которая является основным конструкционным элементом любых небоскрёбов, и не была готова экспортировать её огромное количество, необходимое для двух массивных зданий высотой в 452 метров. В итоге было принято решение впервые в строительной индустрии применить сверхпрочный бетон для возведения столь высокого здания. Такой материал был специально разработан, при этом большую роль играл фактор, чтобы бетон с доставкой транспортировался согласно очень точному графику поставок.
Что уж говорить, если требуется решить намного более простые и тривиальные задачи: заливка фундамента любого типа или создание железобетонных конструкций. При необходимости этот материал может обладать самыми разными характеристиками. К примеру, стоит только добавить к традиционной смеси фосфатные связующие и жидкое стекло вместе с кремнефтористым натрием, как на выходе получается стройматериал, обладающий устойчивостью к воздействию агрессивных кислот и высокой температуры. Конечно, от этого значительно повысится цена бетона, но такое последствие полностью компенсируется обретёнными качествами.
Технология изготовления бетонной смеси
Бетон является единственным материалом, без которого трудно представить себе какое-либо строительство. Возведение любого сооружения начинается с вопроса, как приготовить бетон. Уникальность этого материала позволяет применять его при изготовлении фундамента, стен, колонн, различных перекрытий и т.д.
В настоящее время технология серийного производства основных компонентов бетона позволяет ему конкурировать с признанными природными материалами, такими как камень или гранит. Основные его прочностные и технологические свойства во многом зависят от того, как приготовить бетон. В целом такой процесс достаточно прост. Он может быть выполнен собственными силами и требует только аккуратного подхода.
Основные свойства бетона
Бетон представляет собой водную смесь цементного раствора и различных наполнителей и добавок. В свою очередь, цементный раствор (или простейший бетон) состоит из смеси цемента и песка, приготовленного в виде водного раствора. Полный состав конкретного типа бетона определяется рецептурой в зависимости от назначения материала.
Схема состава бетонаГлавным параметром бетона при определении его назначения и качества является механическая прочность на сжатие, т.е. стойкость при вертикальной нагрузке. Принятые стандарты регламентируют прочность бетона в пределах от 7,5 до 80 мПа. Соответственно, марки строительного бетона колеблются от В7,5 до В80.
Прочность в основном зависит от прочностных свойств цемента (марки используемого цемента) и в определенной степени от содержания и качества других компонентов. Для повышения прочностных свойств специальных типов бетона, в их состав могут включаться армирующие добавки.
К технологическим параметрам бетона можно отнести эластичность (пластичность), вязкость и однородность раствора. Для облегчения работ по наложению материала и улучшения внешнего вида укладки в состав могут добавляться пластификаторы и другие добавки. Вопросы вязкости решаются изменением объема воды, а однородность массы зависит от качества перемешивания.
Важным свойством бетона является то, что окончательное его высыхание протекает очень медленно, и в течение всего этого процесса материал увеличивает свои прочностные характеристики. Окончательное высыхание бетона наблюдается не ранее, чем через 6 месяцев после укладки, а наивысшей своей прочности он достигает примерно через 12 месяцев. Такое свойство бетона в основном определяется особенностью цемента.
Цемент, песок и заполнитель
Цемент
Цемент является основой бетона и обеспечивает связывание всех компонентов в единое целое. Он во многом определяет прочность и монолитность всего соединения. Самым распространенным типом цемента, используемым для изготовления бетона, стал портлендцемент, который практически на 80% состоит из силиката кальция, что обуславливает его хорошее склеивание (адгезию) с другими веществами.
Такой цемент прекрасно показал себя при низких температурах. Для увеличения механической прочности бетона широко применяются и другие типы цементов с прочностью до 500 мПа.
Технические характеристики цементаМаркировка серийно реализуемого цемента указывает его основные характеристики, знание которых необходимо для обеспечения нужной рецептуры бетона. Например, цемент марки М500-Д20. Первые цифры определяют механическую прочность материала на сжатие.
При изготовлении бетона обычно используется цемент М400 или М500; при этом следует помнить, что для особо нагруженных элементов следует использовать наиболее прочный материал. В мало ответственных элементах строительных конструкциях (например, подушка под фундамент) достаточно применение цемента М300.
Вторые цифры в маркировке (совместно с индексом «Д») определяют наличие и процентное содержание примесей (добавок). Для особо важных элементов целесообразно применение цемента с «Д0». В целом, при изготовлении бетона допускается использование цемента до «Д20», т.е. с содержанием примесей не более 20%.
Цемент, предназначенный для изготовления бетона, должен быть сухим, без комков и сыпучим. При неправильном хранении цемент достаточно быстро впитывает воду и теряет свои важнейшие свойства. Во время приобретения цемента необходимо проверить целостность упаковки и срок его изготовления. Приобретать цемент лучше не ранее, чем за 10 дней до начала работ с ним.
Песок
Песок является одним из основных компонентов бетона, обеспечивающим его объем и структуру. В цементных растворах (для штукатурных и укладочных работ) он является основным наполнителем объема. В общем случае строительный песок представляет собой сыпучую смесь твердых силикатных частиц размером 0,15-5 мм. В зависимости от происхождения песок подразделяется на речной, морской, озерный, карьерный, овражный и т.д.
Для приготавливаемого бетона лучше всего подходит песок с размером частиц 1-2 мм. Если бетон предназначен для фундамента наиболее подходящим является речной песок, так как он практически не содержит глины и удовлетворяет требованиям по размеру частиц.
В цементных растворах для кирпичных кладок и штукатурки можно использовать песок с содержанием глины и илистых включений, так как они повышают пластичность смеси. Абсолютно не допускается наличие в песке примесей растительного происхождения или других веществ, способных гнить и распадаться.
Песок в процессе приготовления бетона должен надежно скрепиться цементом, а наилучшая адгезия наблюдается у достаточно крупных частиц. В связи с этим применение песка с большим содержанием очень мелких пылеобразных частиц (менее 0,15 мм) не рекомендуется. Находит применение тяжелый карьерный песок, полученный при дроблении горных пород. Такой песок несколько тяжелей по массе, но имеет необходимые размеры частиц (зерен).
Заполнитель
В качестве объемного заполнителя бетона используются щебень и гравий. Они представляют собой сыпучий материал в виде кусочков горной породы и обеспечивают основную прочность. Размер используемых для бетона кусочков колеблется от 5 до 35 мм.
Лучше всего подходит материал, полученный дроблением породы, так как он обеспечивает наилучшую адгезию цемента за счет неровности (шероховатости) поверхности. Применение речной или морской гальки не желательно, в связи с тем, что ее поверхность отшлифована водой и не гарантирует нужное сцепление.
Таблица характеристик щебняНаполнитель должен содержать кусочки щебня или гравия разного размера, что необходимо для более плотного их прилегания друг к другу и снижения риска образования пустот. Если приобретенный материал состоит в основном из крупных элементов, рекомендуется добавить щебень размером 8-10 мм; и, наоборот, в мелкий щебень следует добавить кусочки размером 20-30 мм.
Крупные куски размером более 35 мм лучше удалить, так как они затруднят перемешивание массы. Не допускается наличие в наполнителе посторонних примесей в виде грязи, почвы, растительных волокон и т.д.
Вспомогательные компоненты
В состав бетона может входить ряд вспомогательных компонентов. Для увеличения текучести и технологичности смеси обычно добавляются пластификаторы. В бетоне для фундаментов их применение необязательно, а вот для кладок или штукатурки — целесообразно.
Схема приготовления бетонной смеси в бетоносмесителяхДля повышения пластичности массы находит применение добавка в смесь гашеной извести. В то же время следует помнить, что известь может уменьшить адгезию цемента к наполнителю, что требует осторожного подхода к количеству этой добавки.
Находят применение суперпластификаторы, которые повышают технологические свойства бетона, увеличивают его влагостойкость и морозоустойчивость. Для удобства работы с бетоном иногда добавляются ускорители и замедлители высыхания раствора.
Все рекомендуемые вспомогательные компоненты выпускаются серийно и предлагаются торгующими организациями. Следует помнить, что общее количество добавок не должно превышать 2% от массы бетона, для того чтобы они не повлияли на прочностные характеристики материала.
Вода
Не следует халатно относиться к использованию воды, чтобы приготовить бетон. Вода не должна иметь загрязнений и примесей, особенно органического происхождения. Заметное влияние на качество бетона может оказать присутствие в воде кислотных или щелочных веществ, масел и сахаров.
Запрещено применение болотных или неочищенных сточных вод. Осторожно следует использовать воду из рек и других водоемов. Наиболее удовлетворяет всем требованиям водопроводная питьевая вода.
Рецептура бетона своими руками
Схема пропорций бетонной массыЧтобы приготовить бетон, прежде всего следует определиться с его рецептурой. Она зависит от назначения бетона и может варьироваться в достаточно широких пределах. Самый простой бетон (так называемый, тощий бетон) марки В7,5 приготавливается в следующем соотношении ингредиентов:
- цемент М400 — 1 часть;
- песок — 10 частей;
- вода — 0,5 части.
Такой бетон используется для подложек (в том числе под фундамент), черновых сглаживающих заливок и т.д. Он не отличается прочностью и пластичностью.
Достаточно распространен бетон марки В15, имеющий следующую рецептуру:
- цемент М400 — 1 часть;
- песок — 2,1 части;
- щебень или гравий — 5 частей;
- вода — 0,6 части.
Большей прочностью обладает бетон марки В25 (цемент М500 — 1 часть, песок — 2 части, щебень — 4 части, вода — 0,5 части). При самостоятельном приготовлении бетона для фундамента часто усредняют рецептуру: цемент М500 — 1 часть, заполнитель — 5 частей, вода — 0,5-1 часть.
Для части фундамента, расположенной ниже поверхности земли содержание наполнителя уменьшают до 3 частей. Следует помнить, что содержание песка во всем объеме наполнителя должно быть не менее 30%. Добавление дополнительных компонентов производится по усмотрению исполнителя работ.
Приготовление бетона: инструкция
Инструмент и приспособления
Понадобится:
- емкость для перемешивания;
- мерное ведро;
- вибратор;
- лопата;
- безмен;
- кувалда;
- сито;
- тачка или носилки;
- совок или мастерок.
Для того чтобы приготовить бетон, необходимо выполнить несколько операций: подготовка компонентов, приготовление смеси компонентов и перемешивание смеси с водой. Подготовка компонентов включает удаление примесей, просеивание и развеску согласно рецептуре. Цемент тщательно разминается во избежание попадания комочков и при необходимости просеивается через мелкое сито.
Песок для удаления примесей и крупных зерен просеивается через сито с размером ячеек до 5 мм. Гравий и щебень целесообразно просеять через это же сито с целью удаления частиц размером менее 5 мм.
Развеску ингредиентов лучше производить с помощью мерного ведра, т.е. по объему (поэтому рецептуру удобнее указывать в частях).
Взвешивание компонентов может привести к заметной погрешности из-за различной степени влажности песка и колебания удельного веса материала наполнителя. Для ориентирования можно привести примерное соответствие объемного и весового измерения. Так, объем стандартного мерного ведра (10 л) соответствует 13 кг цемента М500, 14 кг песка или гравия.
Приготовление смеси компонентов возможно двумя способами. Первый способ основан на сухом перемешивании всего объема цемента и наполнителя с последующим заливом водой. Такой способ при ручном перемешивании не дает гарантии, что весь объем будет полностью перемешан и на дне не останется сухого остатка.
Второй метод предусматривает поочередную загрузку компонентов в воду при одновременном перемешивании. Этот способ грешит тем, что не может обеспечить равномерного распределения ингредиентов по объему. Наиболее частое применение находит все-таки второй способ.
Перемешивание компонентов с водой производится до получения монолитной массы густой сметанообразной консистенции равномерного серого цвета. Не допускается наличия сухих комочков. Дополнительные компоненты предварительно размешиваются в воде и добавляются в раствор бетона при одновременном перемешивании.
Если необходимо приготовить бетон для фундамента в больших количествах, целесообразно арендовать механическую бетономешалку, что намного ускорит и облегчит работы. В этом случае подготовка ингредиентов производится так же. Замешивать смесь следует в следующем порядке: залить в бетономешалку воду и замесить в ней цемент до сметанообразного состояния; загрузить наполнитель и все перемешать в течение не менее 2 минут (до 5 мин) до получения однородной массы.
Бетон должен получиться пластичным, но не очень густым и достаточно текучим, чтобы заполнить опалубку без образования пустот. Время использования раствора не должно превышать 1,5 часа. Укладка бетона должна сопровождаться уплотнением (утрамбовкой). Если нет специальных вибраторов, утрамбовку можно произвести самому методом штыкования стальным прутом. Такое уплотнение целесообразно проводить через каждые 20 см заливки.
При любом строительстве необходим бетон. Приготовить бетон самому не представляет больших сложностей. Главное — необходимо правильно определить требуемые параметры материала, а исходя из них, выбрать нужную рецептуру. Сам процесс приготовления бетона достаточно прост и обеспечит необходимое качество при выполнении элементарных правил.
Смотрите также:Manufacturing Technology из журнала International Cement Review Magazine
15 июня 2021 г.
В связи с резким сокращением количества пассажиров поездов в Великобритании и сокращением расписания движения пассажирских поездов из-за COVID-19, грузовая и логистическая компания Freightliner изучает новые виды услуг для повышения эффективности и производительности.В этих инициативах участвуют крупные британские поставщики строительных материалов, а также Freightliner позволяет еще больше повысить экологичность железных дорог. Произведено Freightliner, Великобритания. …
07 июня 2021 г.Карьер завтрашнего дня
Говорят ли полномасштабные цифровые решения для малых и средних горнодобывающих предприятий о будущем или они уже стали реальностью? Независимый OEM-пакет smartQuarry от немецкой начинающей компании talpasolutions использует расширение…
10 мая 2021 г.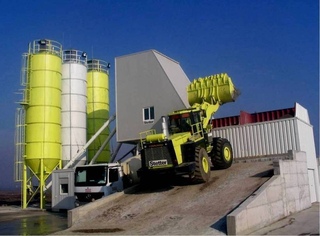
Универсальное прожигание AF
KHD PYROROTOR ® — это роторный реактор для сжигания, который перерабатывает отходы с низкими характеристиками горения в качестве альтернативного топлива в процессе производства цемента. На сегодняшний день установлено семь промышленных установок, …
27 апреля 2021 г.Вклад Вика в SeRaMCo
Французская многонациональная группа Vicat вносит свой вклад в европейский проект SeRaMCo (Вторичное сырье для железобетонных изделий), направленный на сокращение углеродного следа в строительном секторе…
26 апреля 2021 г.Умные ходы FLSmidth
С запуском ECS / ProcessExpert® V8. 5 FLSmidth привносит технологии искусственного интеллекта (AI) в расширенное управление процессами. Но что именно это означает для производителей цемента? Хавьер Пигасо Мерино, FLSmidt …
JK White Cement: путь к постоянному совершенствованию
Производство белого клинкера и белого цемента требует правильного сырья, надлежащей гомогенизации, правильного топлива и оптимальных производственных условий.Завод JK White Cement в Готане, Индия, обязуется обслуживать …
22 марта 2021 г.Информированная оптимизация процесса
Успешная эксплуатация цементных печей с большим количеством альтернативных видов топлива имеет важное значение для перехода к устойчивому производству цемента. Для обеспечения стабильных условий процесса необходим подробный мониторинг.Инфракрасный …
Повышение эффективности охладителя
Новый охладитель четвертого поколения Tianjin Cement Industry Design and Research Institute Co, названный «Sinowalk», включает в себя такие ключевые особенности, как высокая эффективность рекуперации тепла, стабильные механические характеристики и интеллект …
8 марта 2021 г.Работа с пылью
При этом химический состав пыли варьируется между прямым режимом работы, когда сырьевая мельница не работает, и непрямым режимом работы, когда сырьевая мельница работает, поиск места назначения для пыли рукавного фильтра при поддержании гомогенной печи. ..
Повышение производительности стана
Снижение клинкерного фактора без ущерба для качества и растущий спрос на высокоэффективные цементы представляют собой серьезную проблему для технологии тонкого помола, используемой на цементных заводах. В рамках своей зеленой цементной пла …
26 января 2021 г.ESP превращается в рукавный фильтр
Когда электрофильтры не могут соответствовать более строгим нормам по выбросам, может быть более экономичным превратить их в рукавные фильтры, а не заменять их новым рукавным фильтром.Gorco SA выделяет ключевые направления …
8 марта 2021 г.Трехкратное увеличение срока службы футеровки
Вьетнамский цементный завод более чем в три раза увеличил срок службы огнеупорной футеровки в более прохладном корпусе за счет использования сборной модульной футеровки от HASLE Refractories. Снижение абразивного и щелочного воздействия с …
7 декабря 2020 г.Цементный завод XXI века: экологичнее и взаимосвязаннее
Цементный завод будущего будет придерживаться тенденций оцифровки и устойчивого развития, чтобы получить конкурентное преимущество и повысить устойчивость.Элефтериос Хараламбус, Томас Циглер, Рамез Хаддадин, Себастьян Райтер и …
10 ноября 2020 г.Следим за шестернями
Одна из самых серьезных механических проблем при техническом обслуживании вращающейся печи сегодня — поддержание эффективной работы венцовой шестерни и зацепления шестерни. Несоосность во время производства создает неравномерное и нестабильное напряжение…
18 февраля 2021 г.От WHRPG до EfW
По мере того как цементные заводы ищут способы уменьшить свой углеродный след, системы выработки электроэнергии с рекуперацией отходящего тепла (WHRPG) становятся все более популярными. Использование биомассы также имеет потенциал в качестве энергии из отходов (E …
13 Октябрь 2020Энергосбережение при раздельном тонком помоле
Раздельное измельчение и последующее смешивание — широко используемая практика в цементной промышленности, позволяющая снизить удельное потребление электроэнергии за счет использования высокоэффективных методов измельчения.Пока мяч …
границ | Обзор новых технологий аддитивного производства в 3D-печати цементных материалов в строительной отрасли
Введение
Строительные компании сталкиваются с многочисленными и существенными проблемами, связанными с производственными затратами. Например, процесс заливки бетона на месте приводит к образованию большого количества отходов, которые впоследствии выбрасываются, особенно если опалубка больше не используется.Напротив, подмости, пригодные для повторного использования, сокращают количество отходов. Однако такие формы относительно дороги в производстве, и необходимы длинные серии строительных лесов, чтобы сделать эти формы рентабельными (De Witte, 2015). Жизненный цикл строительных лесов — еще одна проблема с точки зрения воздействия строительных лесов на окружающую среду, особенно с учетом выбросов парниковых газов. Это, в свою очередь, вызывает много повторений, что позволяет улучшить изготовление, точное изготовление элементов и распечатать любую геометрию, что трудно сделать для обычного применения, такого как элементы фасада (Buswell et al., 2007; Лим и др., 2012).
Было показано, что технологии быстрых прототипов (например, 3D-печать) могут полностью изменить ряд производственных методов (Lipson and Kurman, 2013). Основным преимуществом технологий быстрого прототипирования является непосредственное создание деталей за один шаг на основе данных САПР (Vaezi and Chua, 2011). Например, использование 3D-печати может снизить на 35–60% общую стоимость бетонного строительства, просто устранив необходимость в опалубке (Lloret et al., 2015).
Существуют проблемы с использованием форм для строительства, такие как их пригодность для вторичной переработки и ограничения по размеру строительных лесов для ряда структурных компонентов.Многие компоненты произвольной формы отливаются на месте , где их качество невозможно контролировать (Elhag et al., 2008). По этой причине высокопроизводительные компоненты (например, балки и колонны) производятся в контролируемой среде. В процессах аддитивного производства (AM) используются различные 3D-методы, такие как 3D-сканирование в процессе цифрового производства и для генерации файлов (Ma et al., 2017).
Избыточный заказ бетона (Tam et al., 2006) и завязанная опалубка (Cole, 1998) являются основными источниками дополнительных выбросов CO 2 при заливке бетона на месте и огромных отходов материалов.Далее при затвердевании бетона производит CO 2 . Таким образом, разработка новых и инновационных методов строительства мотивируется стремлением к экономическим, экологически чистым и архитектурным преимуществам. Bos et al. (2016) считали, что использование технологии 3DP является достойным вводным шагом к замене цемента в строительной отрасли менее энергоемкими материалами, такими как летучая зола и геополимерный бетон.
Есть некоторые проблемы и ограничения, связанные с 3D-печатью, такие как низкая жесткость и прочность напечатанных строительных материалов, а также размер печати (Edwards et al.(2013). Bos et al. (2016) упомянули, что компания WinSun может напечатать большой строительный компонент (~ 36,6 × 12,2 × 6,1 м) с помощью своего 3D-принтера и автоматизированного манипулятора. Также Weger et al. (2016) сообщили о печати конструктивных элементов с поперечным сечением до 6 × 6 м с использованием D-образного принтера путем заливки жидкости на порошковые материалы. Еще одно ограничение заключается в том, что предполагаемый размер печати не соответствует спецификациям всех видов 3D-принтеров, поскольку каждый принтер имеет свои собственные спецификации для изготовления структурных элементов.Существуют также опасения по поводу методов 3D-печати на основе порошка, а именно, необходимость поддержки веса печатного объекта до тех пор, пока материал не наберет достаточную прочность. Кроме того, дизайн смеси и использование крупных заполнителей — еще одна проблема для 3D-печати бетона. Например, компания WinSun использовала только мелкие вяжущие материалы без крупного заполнителя в своем приложении для 3D-печати.
В этом исследовании представлен обзор доступных и перспективных методов печати или нанесения вяжущих материалов и их адаптации к различным ингредиентам смеси и процессу смешивания.
Обзор технологий быстрого прототипа в строительной отрасли
По данным Tay et al. (2016) быстрое прототипирование в строительстве было представлено как инновационный подход к построению конструкций (Pegna, 1997). С тех пор быстрое прототипирование, а затем и цифровое изготовление стали популярными в строительной отрасли, а также во многих других областях, таких как автомобилестроение, аэрокосмическая промышленность и биомедицина (см. Buswell et al., 2007; Berman, 2012). Feng et al.(2015a) классифицировали технологии быстрого прототипирования (RP) на три основные категории: аддитивные, аддитивные / вычитающие и вычитающие, как показано на рисунке 1.
Рисунок 1 . Обзор технологий быстрого прототипирования и методов, обсуждаемых в этой статье. Во вставке выделены методы, использованные в этой статье.
При субтрактивном производстве трехмерный объект создается путем удаления материала из блока с помощью станков для резки материалов. В аддитивном производстве, которому посвящена эта бумага, загружаемый материал в виде порошка, жидкости, нити, клея или связующего добавляется к подложке, слой за слоем, для создания трехмерного объекта.Количество материалов, оставшихся после этого процесса, часто бывает значительно больше, чем результат процесса аддитивного производства при создании одного и того же трехмерного объекта (Ambrosi and Pumera, 2016).
Li et al. (2016) рассмотрели технологии аддитивного производства и 3D-печать с различным сырьем на рынке. Они обнаружили, что фотополимеры занимают самую большую долю рынка 3D-печати (56% по весу), за ними следуют термопласты (42%), металлы (только 1%). Доля рынка керамики, бетонных материалов в сумме составила около 1%.
В этой статье мы обсуждаем ключевые методы аддитивного производства, которые могут быть использованы в строительной отрасли.
Струйная печать (струйная печать по переплету)
Струйная печать, также известная как струйная печать вяжущего, является одним из распространенных методов печати, используемых для 3D-печати деталей в различных отраслях промышленности, и имеет большой потенциал для создания больших конструкций из вяжущих материалов. В этом методе наносится тонкий слой печатного материала, часто в виде порошка, но иногда в виде стружки (например,г., валиком) над твердой площадкой или лотком. Затем на слой порошка наносится жидкое связующее, как показано на рисунке 2. Связующее склеивает порошок вместе, образуя твердую часть. Этот процесс повторяется несколько раз, и слои печатаются друг на друге, образуя трехмерный объект. Следует отметить, что для некоторых печатных материалов может потребоваться отверждение (Wu et al., 2016) или обжиг в печи (Withell et al., 2011) в качестве дополнительной стадии постобработки. Это сделало бы струйную печать энергоемкой техникой для создания крупных структур.Одна из основных функций порошка — поддерживать деталь, в то время как связующее наносится поверх верхнего слоя, который был напечатан на предыдущем этапе (Tay et al., 2017). Хотя с помощью этого метода можно напечатать сложные геометрические формы, готовая деталь часто содержит пустоты, которые ухудшают качество детали. Струйная печать больше подходит для печати деталей и структур, в которых высокая скорость печати предпочтительнее точности печати согласно Wu et al. (2016). Исследователи сообщили об использовании различных комбинаций порошка и связующего.Например, Feng et al. (2015b) использовали гипс и воду в качестве порошка и связующего соответственно. Withell et al. использовали жидкость на водной основе для связывания частиц глины, в то время как Хенке и Тремл (2012) пытались связать древесную стружку (частицы) смесью воды, целлюлозы и цемента (связующее). Гиббонс и др. (2010) использовали быстротвердеющий портландцемент со связующим из поливинилового спирта для печати структур на основе цемента. Дополнительные процедуры после процесса печати (этап постобработки) часто применяются к печатной части, как указано в таблице 1.
Рисунок 2 . Схематическое изображение процесса струйной 3D-печати.
Таблица 1 . Типы порошка, связующего и постобработки для струйной печати.
Селективное лазерное спекание (SLS)
Селективное лазерное спекание (SLS) — это процесс послойного спекания порошков (Kruth et al., 2005). Выбранные области порошкового слоя подвергаются воздействию тепловой энергии лазерного луча. Эта технология была представлена в 1986 году Карлом Декардом и Джо Биманом в Техасском университете согласно Липсону и Курману (2013).Каньете Вела (2014) заявил, что лазерное спекание можно использовать для изготовления металлических и полимерных объектов. Этот метод похож на тот, который используется в стереолитографии (SLA), в котором процесс фотоотверждения инициируется светом для создания цепочки взаимосвязанных молекул.
В SLS в качестве лазерного луча используется струя CO 2 , которая направляет свет на порошки. Порошки могут быть порошками различных материалов, таких как сплавы, керамика, металлокерамика, нейлон, композитное стекло, металл, сталь и карбонат (Jeng et al., 2000). На рисунке 3 схематически показано, как лазер используется для плавления порошка или суспензии. Расплавленные материалы превращаются в жидкое образование и полностью затвердевают при понижении температуры (Колосов и др., 2004). Вычислительное моделирование использовалось в некоторых исследованиях для лучшего понимания процесса SLS (Kumar, 2003). Питер и Жан-Пьер (2006) исследовали остаточные напряжения при селективном лазерном спекании (SLS) и селективном лазерном плавлении (SLM), стремясь лучше понять явление спекания.Было обнаружено, что свойства чистого порошка различных порошков SLS влияют на процесс изготовления и в конечном итоге приводят к улучшению механических свойств полученных компонентов (Dalgarno and Stewart, 2001). Подобно деталям, напечатанным на струйной печати, детали SLS обычно требуют постобработки, которая может повлиять на структурные характеристики готовой детали. Следовательно, постобработка и знание явлений спекания должны быть интегрированы в процесс проектирования и планирования, чтобы получить 3D-печатную деталь оптимального качества (Ian and Dongping, 1997).
Рисунок 3 . Схема селективного лазерного спекания.
Исследование, проведенное Dalgarno и Stewart (2001), сообщило о результатах исследования дизайна производственных инструментов, используемых в промышленном процессе SLS. В обоих вышеупомянутых исследованиях оценивается повышение производительности за счет использования конформных каналов охлаждения, а также изучается износ инструмента.
Экструзионная печать (процесс на основе экструзии)
Технология экструзионной печати позволяет создавать трехмерные объекты из компьютерной модели, как в типичном процессе быстрого прототипирования.Подробные модели могут быть получены из сканирования компьютерной томографии, сканирования магнитно-резонансной томографии или данных модели, созданных с помощью систем оцифровки трехмерных объектов и используемых в этой технике. В методе моделирования наплавленного осаждения (FDM) термопластичный волокнистый материал экструдируется и осаждается в виде полурасплавленного полимера на платформу в цикле слой за слоем. На рисунке 4 показано, как создается каждый слой; основание платформы опускается, и следующий слой укладывается поверх другого, как предписано компьютерной моделью (Zein et al., 2002). 3D-печать / печать бетона методом экструзии была основана на процессе FDM. Первоначальная идея экструзионной печати строительных элементов была предложена в конце 1990-х годов Пегной (1997). Позже этот метод был использован в Университете Южной Калифорнии (USC) с некоторыми корректировками и модификациями. Этот процесс был назван созданием контура Хошневисом и Даттоном (1998) и Хвангом и Хошневисом (2004). Дельгадо Камачо и др. (2018) утверждали, что использование новых технологий 3DP (в основном экструзии) в строительной отрасли может снизить затраты на рабочую силу, уменьшить отходы материалов и создать сложные геометрические формы, которые трудно получить с помощью обычных строительных технологий.Более того, Lloret et al. (2015) стремились связать весь цифровой дизайн, аддитивное производство и свойства материалов для создания сложной формы из бетонных конструкций.
Рисунок 4 . Графическое объяснение экструзионной печати с использованием робота с 6 степенями свободы и винтового насоса.
Lim et al. (2012) представили применение крупномасштабного печатного бетона с помощью процессов аддитивного производства, которые называются бетонной печатью. Были обсуждены экструдированная суспензия строительного раствора и несколько новых критериев, таких как конструкция смеси строительного раствора и система подачи, которая была разработана для печатного процесса.Таблица 2 объясняет три основных метода аддитивного производства для строительных приложений.
Таблица 2 . Сравнение аддитивных технологий производства в строительной сфере.
Свойства различных конструкций бетонной смеси и различных ингредиентов были рассмотрены с учетом соответствующей реологии влажного бетона, а также соотношения вязкости для стабильности размеров (Zijl et al., 2016).
Ашраф и др. (2018) сосредоточились на металлических 3D-печатных структурах и изучали микрочастицы печатных структур из нержавеющей стали и титана.
Эти пути и шаги жизненно важны для создания объекта, когда процесс аддитивного производства включает в себя управляемую машину, такую как робот, как показано на рисунке 4.
Конструкция бетонной смеси
Дизайн бетонной смеси играет важную роль как в процессе 3D-печати цементного бетона, так и в структурных характеристиках печатных бетонных элементов. При 3D-печати материалов свежий бетон или строительный раствор накладываются один слой на другой, в то время как нижние слои удерживают слои над ними.Хотя технологии быстрых прототипов и методы 3D-печати были достаточно подробно рассмотрены в литературе, лишь в нескольких исследованиях изучалась роль конструкций из бетонных смесей в 3D-печати цементных материалов. Некоторые недавние исследования были сосредоточены на различных пропорциях химических добавок и соотношении вода / цемент, тогда как более ранние Jeon et al. (2013) попытались использовать менее крупный агрегат. Пропустить через насос и маленькое сопло крупные агрегаты чрезвычайно сложно. Кроме того, слои с крупными агрегатами не могли сохранять исходную форму напечатанных слоев.
Le et al. (2012a) подготовили бетонные смеси для печати 3D фибробетона с мелкими заполнителями. Целью экспериментальных исследований было изучить экструдируемость и способность бетонных смесей к разложению. Диаметр систем подачи сопел составляет 9 мм, что обеспечивает высокое разрешение печати. Таблица 3 суммировала пропорции смеси бетона. В своем исследовании они рассматривали прочность на сдвиг для удобоукладываемости бетона и прочность на сжатие для напечатанных образцов.Оптимальная прочность на сжатие, достигнутая при отверждении в течение 28 дней, составила 110 МПа.
Таблица 3 . Расчетные пропорции смеси для бетона и раствора 3DP в литературных исследованиях.
Malaeb et al. (2015) попробовали разные пропорции смеси бетона, как показано в таблице 3, для печати прямых линий. В своем исследовании они выбрали пропорцию смеси номер 3 в таблице 3, в которой соотношение воды и цемента ( w / c ) составляет ~ 0,4. Более низкое соотношение w / c , которое увеличивает прочность бетона и подходящее соотношение воды в бетонном вспомогательном материале для поддержания максимальной строительной способности печатного бетона.Примерная прочность на сжатие таких конструкций смеси составляет 42 МПа.
Tay et al. (2016) провели расчет бетонной смеси 3DP, как описано в таблице 3. Они обнаружили, что эта смесь является отличным дизайном бетонной смеси для 3DP. В этом исследовании была изготовлена недорогая смесь с добавлением 1,05% суперпластификатора по весу воды. Экструдируемость и возможность сборки принтера были изменены в соответствии с вариациями дизайна смеси.
Gosselin et al. (2016) исследовали пропорции бетона в смеси 3DP (см. Таблицу 3).Материалы состоят из строительной пасты со сверхвысокими характеристиками с добавлением полимерной смолы для улучшения качественных границ раздела слоев и ускорителей для достижения адекватной реологии. Образцы призм (40 × 40 × 160 мм) готовили в течение 90 дней при температуре окружающей среды, чтобы проверить испытание образцов на прочность на изгиб. В этой работе вместо передвижного крана была использована роботизированная рука с 6 степенями свободы, а также была представлена структурная печать сложной геометрии.
Хамбах и Фолькмер (2017) исследовали конструкции смесей 3DP и продемонстрировали оптимальную пропорцию смеси для своего исследования (Таблица 3). В своей статье они подготовили и напечатали образцы, используя машину WASP Clay Extruder Kit с диаметром сопла 2 мм. В ходе испытаний изучались плотность, пористость и прочность образцов, напечатанных на 3D-принтере с короткими волокнами (углеродные, стеклянные и базальтовые волокна). Волокна использовались в разных направлениях, и максимальная полученная прочность на изгиб составляла 30 МПа при содержании 1% углеродного волокна для траектории печати.Оптимальная прочность на сжатие для коротких углеродных волокон объемом 1%, параллельных печатной детали, достигала 80 МПа.
В том же исследовании авторы подготовили пропорции смеси для иерархических материалов. В сухой смеси использовались все виды армирования волокнами. Агент, понижающий содержание воды, смешивали с водой с помощью специального смесителя для получения гомогенной смеси. Наконец, волокна продолжали добавлять в смесь до полного диспергирования волокон. Максимальная прочность на изгиб в иерархических материалах для 3DP составляет 17.5 ± 0,5 МПа. Оптимальная прочность на трехточечный изгиб наблюдается в диагональных сечениях образцов, заполненных раствором.
Kazemian et al. (2017) разработали различные конструкции смеси для бетона в 3DP. В таблице 3 показаны различные смеси, такие как PPM (только портландцемент), SFPM (содержащий микрокремнезем), FRPM (содержащий волокно), NCPM (содержащий наноглину). Были предложены два различных метода формообразования «оседание слоя» и «стабильность цилиндра». Результаты экспериментов показали, что наноглина и микрокремнезем улучшили формуемость свежей смеси, в то время как небольшое улучшение было замечено в печатной части при добавлении полипропиленового волокна.
Согласно исследованию Rushing et al. (2017) состав смеси для экструзионной печати был подготовлен, как показано в таблице 3. Было отмечено, что смесь B3 имеет наилучшую экструзию смеси. Исследование коротких волокон в бетоне показало, что короткие волокна не уменьшают текучесть и в большинстве случаев волокна улучшают стабильность формы свежего бетона.
Согласно исследованию, проведенному Shakor et al. (2017a), пропорция смеси в бетоне может быть приготовлена на основе испытаний на текучесть при сжатии, прочности на сжатие, испытания на осадку и испытания Вика.В таблице 3 показаны основные испытания бетонной смеси. В предыдущем исследовании были проведены различные вяжущие смеси, которые представляют собой растворные смеси с различным соотношением воды и химической добавки. Это могло значительно изменить текучесть бетона. В рамках исследования проводится 22 испытания для подготовки бетонной печати. Далее, три из этих испытаний были выбраны для испытаний на текучесть при сжатии, механические характеристики и сыпучесть. Было установлено, что тройные слои в пятом испытании, состоящие из строительной смеси, имеют меньшее смещение, чем смесь, содержащая крупный заполнитель.
В приведенных выше таблицах представлены различные пропорции смеси при 3DP-печати и используются различные химические добавки для контроля реологии материалов. Различное соотношение смеси привело к разным результатам и разным окончательным формам структурных компонентов. Более того, многие бетонные смеси были отверждены с помощью специальной процедуры. Тем не менее, в каждом исследовании есть разные измерения времени схватывания бетонного раствора на основе w / c и пропорций добавок.
В приведенных выше таблицах соотношение раствора w / c находится между (0,3 и 0,4). В большинстве исследований использовалось соотношение w / c , равное 0,4. Соотношение w / c бетонной смеси в экспериментальном исследовании имеет большое влияние на текучесть смеси и формуемость печатных бетонных деталей.
Установленное соотношение ускорителя имеет такое же соотношение в большинстве исследований, как и суперпластификатор. Время перемешивания бетона — важная часть процесса печати, но в каждом исследовании было разным, в зависимости от пропорций смеси и соотношения воды и цемента.В исследовании Kazemian et al. (2017) процесс перемешивания занял 8 минут, в то время как в Le et al. (2012b) 15 минут было потрачено на замешивание бетона для напечатанных образцов. В предыдущей работе, выполненной Shakor et al. (2017а) среднее время перемешивания 5–8 мин.
Конструкция бетонной смеси продемонстрировала ограничения различных смесей. Большинство смесей не включают крупный заполнитель из-за большого размера частиц и плохой формообразования. Таким образом, исследователи обычно выбирают строительный раствор или мелкие частицы, чтобы его было легко перекачивать.Однако грубый заполнитель нельзя было использовать для всех типов насосов. Кроме того, печатный бетон с крупными частицами не выглядел достойно после набивного бетона.
Результаты эталонного эксперимента
Струйная печать
Состав порошка для струйной печати 3DP
В струйной технологии 3DP решающим фактором перед началом печати является адаптируемость и совместимость порошка с типом принтера. Нанесение печати будет простым, если размер частиц, текучесть и смачиваемость порошка совпадают с рекомендованным производителем порошка.Соответственно, анализ размера частиц рекомендованного материала важен для определения ближайшего диапазона частиц, которые, как ожидается, приведут к успешной печати.
В предыдущих исследованиях автора Shakor et al. (2017b) и Shakor et al. (2018) был проанализирован и идентифицирован размер распределения порошка, который использовался в струйном 3D-принтере (Z-printer150, Z-Corporation, США). Данные были получены с помощью лазерного анализатора размера частиц (Cilas 1190), рис. 5А.Рекомендуемый производителем порошок (ZP 151) содержит основные материалы: гипс, углеводы и виниловый полимер. Описательные значения среднего размера частиц для 10, 50 и 90% материалов составляют D10, D50 и D90 соответственно. Полученные значения D равнялись 1,48, 23,07 и 70,12 мкм соответственно. Удельная поверхность порошка ZP 151 была зафиксирована на установке (BELSORP-max) как 0,999 м 2 / г.
Рисунок 5. (A) Гранулометрический состав цементного раствора и Zpowder (ZP 151) для струйной печати, (B) Анализ размера частиц раствора по сравнению спроцент прохождения для экструзионной печати.
На рис. 5А показаны детали гранулометрического состава ZP 151 и цементного раствора, который использовался в процессе струйной печати. На рисунке 5A размер частиц цементного раствора показан под наклоном к правой стороне графика, что означает, что размер частиц немного больше, чем рекомендованный порошок (ZP 151), который для значений D90 составляет около 80 мкм для модифицированного порошка. (цементный раствор). Судя по графику, ни один из обоих порошков не идеально подходит, но они достаточно похожи, что помогает обеспечить регулярный поток порошка через бункер подачи принтера и возможность плавной печати структурных образцов.
Подготовка образцов и определение соотношения вода / цемент
Этот метод печати строительных элементов представляет собой струйную печать (струйную печать связующего вещества), аналогичную офисному принтеру, в котором вместо печати на бумаге капли чернил капают на порошковые материалы. В D-образном принтере также используется похожий процесс. В способе распыления связующего порошок обычно состоит из композитного материала. Жидкое связующее представляет собой в основном воду, которая используется в качестве активатора для связывания порошка.Процесс печати проводится с использованием послойного нанесения. На рисунке 6 показаны кубические образцы при одноосной сжимающей нагрузке, на рисунке 6b показаны сердцевина и оболочка образцов после испытания. Уровень насыщения определяется как количество жидкого связующего на основе порошковой печати, которое выпадает из печатающей головки (Miyanaji et al., 2016).
Уровень насыщения = VbinderVenv.powderРисунок 6 . Цементный куб, напечатанный на струйном 3D-принтере: (a) сжат под одноосной нагрузкой, (b) растрескивается и отслаивается части оболочки и сердечника.
Где V binder — объем связующего, а V env . порошок — объем порошка после его прокатки в камере сборки (бункер; порошок в оболочке).
Поскольку плотность и масса известны, приведенное выше уравнение можно использовать для определения отношения w / c для обоих материалов.
Различные уровни насыщения в жидком связующем означают, что оболочка и сердцевина имеют одинаковое соотношение w / c , а аналогичные уровни насыщения означают разные отношения w / c внутри оболочки куба.
Уровни насыщенности при струйной печати зависят от внутренней и внешней поверхности детали, напечатанной на 3D-принтере. Внешняя часть называется оболочкой, а внутренняя часть — ядром (Withell et al., 2011).
Файлы для объектов 3D-печати — это файлы STL, которые можно легко смоделировать и отправить на принтер для печати сегментов (Cox et al., 2015; Hager et al., 2016).
Отпечатанная деталь под действием одноосной сжимающей нагрузки может сломаться в различных направлениях в зависимости от направления печати.Рисунок 6b, в тех же образцах насыщения, таких как (S100 C100), часть оболочки под одноосной сжимающей нагрузкой отделяла свои части от основной части образцов (Shakor et al., 2017b). Кроме того, необходимы исследования для определения причин наблюдаемых результатов, рис. 6.
Разрешение и шероховатость поверхности порошкового слоя
После подготовки материалов и подачи порошков из питателя необходимо исследовать еще одну переменную — шероховатость поверхности порошка и шероховатость образцов.Эта переменная в основном связана с препаратами в виде порошка. Один из методов, который можно использовать для оценки шероховатости порошка, — это визуальный осмотр слоя порошка в бункере для печати принтера. Визуальный осмотр различных типов гипса проводился в исследованиях Zhou et al. (2014), которые сравнили крупный и мелкий порошок, а также исследовали плотность обоих порошков. Распределение частиц порошка, однородность порошка, гигроскопические свойства в порошке имеют большой вклад в конечный печатный продукт.Каждый из порошков имеет разные свойства для развития электропроводности и микроструктурной прочности материалов.
Модифицированные материалы (цементный раствор) более способны поглощать воду и проявлять реакции гидратации. Это связано с тем, что основным ингредиентом порошка является цемент на основе алюмината кальция, который претерпевает аморфную фазу, что приводит к росту взаимосвязанных кристаллов с плотной микроструктурой. Таким образом, появилась высокая ранняя прочность при быстром схватывании алюминатного цемента кальция.С другой стороны, развитие слишком большого количества кристаллов вызывает пористую микроструктуру и приведет к снижению прочности и долговечности (Sugama and Carciello, 1991).
В целом гигроскопические свойства и агломерация цементного порошка вызывают плохую набивку порошкового слоя в камере печати принтера. Таким образом, порошок необходимо тщательно перемешать и разжижить перед печатью каких-либо объектов.
При струйной печати существует явная разница между цементным порошком и рекомендуемым гипсовым порошком на камере печати принтера.Однако Shakor et al. (2018) наблюдали значительное количество пор, пустот и шероховатостей на порошке цементного раствора. Следовательно, это приведет к получению слабого напечатанного образца и уменьшению механической прочности напечатанных образцов. По этой причине настоятельно рекомендуется хорошо перемешать материалы перед началом процесса печати. Кроме того, используйте свежий цементный порошок и контролируйте температуру и влажность в лабораторных условиях. Кроме того, существуют другие методы снижения влажности материалов и повышения прочности, например.g., используя стекловолокно, которое использовалось в других исследованиях для увеличения гибкости и прочности напечатанных элементов конструкции (Shakor et al., 2011) и (Shakor and Pimplikar, 2011).
Селективное лазерное спекание
Целью данного исследования является изучение возможностей аддитивного производства и использования 3D-печати для производства строительных лесов или конструктивных элементов, которые в настоящее время полезны для строительной отрасли.
Тест SLS был проведен для цементной пасты.Этот тест был организован для определения реакции материалов под воздействием тепла лазерного луча и инфузии между частицами.
Ограниченные количества цемента и воды были приготовлены с 630 г цемента и 282 мм водяного столба, соответственно, и соотношением в / ц , равным 0,45. Толщина пасты на лотке составляла 6 мм. В этом пробном испытании паста была приготовлена на плоском лотке, так что свет луча мог легко проходить через пасту на лотке. Лазер применяли к цементной пасте с целью упрочнения и сушки бетонной смеси, как показано на Рисунке 7 и Таблице 4.Примечательно, что лазерное спекание существенно не повлияло на цементный тесто и не вступило в реакцию с суспензией. Лазер также был протестирован при разной мощности и в разных местах на цементном тесте, в результате чего на поверхности цементного теста образовалось слегка засохшее пятно. Эти испытания проводились на машине Voxeljet VX1000. Как показано на Рисунке 7, первая линия на лотке прорезается лазерным лучом с размером пятна 1 мм, затем размер пятна был увеличен до 24 мм, что не оказывало заметного эффекта высыхания на пасте из-за большой размер прожектора.Таким образом, в четвертой строке прожектор уменьшен наполовину (т.е. 12 мм). Это резко изменило цвет цементной пасты на желтоватый, что означает пригоревший. Остальные линии были высушены и обезвожены с различным соотношением размеров пятен. Например, девятая строка стала умеренно сухой по сравнению с другими строками.
Рисунок 7 . Использование лазерного спекания (SLS) для цементного теста с различной мощностью (Вт).
Таблица 4 .Продемонстрируйте скорость, размер пятна, мощность и температуру для каждой линии на Рисунке 7.
В таблице 4 показано соотношение подачи в мм / мин, размер пятна (мм), мощность (ватты) и температура (° C). Понятно, что скорость и температура являются решающими факторами в процессе SLS, и они оба влияют на получаемую цементную пасту.
Экструзионная печать
Дизайн смеси для цементных материалов
В качестве пилотного исследования Shakor et al. (2017a) использовали разные бетонные смеси и разные размеры сопел с промышленным роботом для печати цементного раствора.Робот также был запрограммирован на печать сложных компонентов, как показано на рисунке 8. В настоящее время экструзионная печать является одним из наиболее распространенных методов в строительстве. Экструзионная печать [например, печать на бетоне (Le et al., 2012a), создание контуров (Khoshnevis et al., 2001)] уже широко применяется в области строительства.
Рис. 8. (a) Печатный раствор методом экструзии, (b) Печатный раствор, полученный роботизированной экструзией, высушенный при температуре окружающей среды в течение 1 дня.
Методология Gosselin et al. (2016) был обновлен с 3D-печати 3DOF Design 2.5D (Le et al., 2012b) до 6DOF (3D-печать) с использованием промышленного робота. 2.5D печать — это процесс нанесения на 3 оси принтера, который имеет ограниченную возможность маневрировать печатающей головкой. Однако 3D-печать известна как полный процесс применения робота с шестью степенями свободы, который можно плавно перемещать с минимальными граничными ограничениями.
На рис. 8 показано, как после высыхания напечатанных линий в местах засорения насоса возникали усадочные трещины.Это может произойти, когда по подающей трубе не выходит достаточное количество подаваемого материала, выходящего из сопла. Однако усадочные трещины можно устранить, добавив волокна, такие как стекловолокно или полипропиленовые волокна (Shakor and Pimplikar, 2011) и немного увеличив соотношение w / c (Rashidi et al., 2018) или добавив проволоку (308LSo нержавеющая сталь) для увеличения прочности на разрыв печатаемых объектов (Laghi et al., 2018). Еще одним ограничением, с которым сталкиваются при печати бетона, были колебания, испытываемые суставами 4 и 6 промышленного робота, когда робот приближается к сингулярным конфигурациям.Эта проблема изначально обострилась, так как эти суставы испытывали большинство движений и изменений скорости. Однако это колебание можно решить, применив метод наименьших квадратов с затуханием (DLS) для предотвращения сингулярности роботов, как описано в предыдущей работе (Shakor et al., 2017a).
Кроме того, ситовый анализ и гранулометрический состав раствора имеют большое влияние на текучесть материалов и осадку строительного раствора. На рис. 5В показан процент прохождения частиц из сита для мелкого песка и обычного портландцемента по сравнению слогарифмический размер частиц для экструзионной печати. Очевидно, что размер частиц сухих порошков не превышает 300 мкм. Однако размер частиц может быть увеличен до более крупных частиц, то есть до 1,0 мм, в виде крупного песка для повышения прочности строительного раствора и уменьшения усадочных трещин в печатных объектах.
Система адаптации и доставки экструдера
Системы адаптации и доставки экструдера имеют наиболее значительное влияние на то, будет ли экструзионная печать производить удовлетворительный печатный объект.Удовлетворительный результат печати объектов обычно означает хорошие механические свойства материалов и хорошую формуемость печатных частей. На рисунке 9 показана разработанная модель экструдированной детали, которая была разработана для крепления к рабочему элементу робота с 6 степенями свободы в данном исследовании.
Рисунок 9 . Концепция узла экструдера в разобранном виде, который соединен с винторезным насосом и прикреплен к концу робота.
Соединения роботов, которые преимущественно использовались в процессе печати, — это шарнир 4 и 6.Эти два соединения часто используются для вращения и перемещения печатающего сопла по желаемому пути для печати элементов. По этой причине в этих двух суставах возникали в основном колебания.
Форма и размер сопла считаются еще одним эффективным фактором механической прочности и формообразования печатаемых объектов. Следовательно, эти два фактора следует учитывать при проектировании сопла.
Кроме того, необходимо учитывать систему доставки.Система подачи оказывает большое влияние на результаты печати, такие как формуемость и оседание бетона или раствора. Насосы — это наиболее распространенная система подачи, используемая в полиграфических приложениях. У насосов разные типы и разный процесс доставки материала от источника к рабочему элементу принтера. На рис. 4 представлена графическая иллюстрация системы печати с использованием 6-степеней свободы и винтового насоса с прогрессивной разверткой в текущем исследовании (Shakor et al., 2017a). В 3DP по бетону использовались различные насосы, такие как винтовой насос винтового типа (Shakor et al., 2017a), перистальтический насос (Gosselin et al., 2016), пневматический насос (Bos et al., 2018) и поршневой насос (Malaeb et al., 2015). У каждого из насосов были ограничения, такие как давление, скорость потока и передача тепла суспензии. Таким образом, ни один из насосов не является идеальным со 100% -ным КПД. Потеря энергии и преобразование тепла в суспензию делает насос более теплым, а бетон также нагревается. Однако некоторые из насосов имеют меньше полостей и воздушных пустот, чем другие, такие как пневматические, центробежные и перистальтические насосы.Вышеупомянутые типы насосов вызывают меньшее проникновение воздуха из-за принципа работы турбины и легкости установки демпферов в таких насосах. Конструкция винтовых насосов прогрессивного типа создает полости и пустоты, которые могут привести к выпуску воздуха на конце ротора вместе с материалами. Более того, когда время работы в насосе увеличивается, скорость потока насосов резко уменьшается, в отличие от скорости потока во вращающемся лепестке, который остается постоянным и постоянным (Boring, 2016).
Обсуждение
Струйная печать является вторым наиболее известным процессом печати в строительной области и состоит из порошка и связующего.Порошки могут быть любыми используемыми материалами, которые могут легко реагировать со связующим.
Chua and Leong (2014) и Low et al. (2017) ссылались на крупные принтеры, такие как Voxeljet и ExOne, которые могут печатать большие детали размером до (4 2 1 м). Voxeljet — немецкая компания, специализирующаяся на услугах систем 3D-печати. Кроме того, ExOne — американская компания, предоставляющая услуги, аналогичные Voxeljet, с той лишь разницей, что отличия заключаются в некоторых технических характеристиках. Например, ExOne имеет две камеры сборки и может печатать одновременно, но Voxeljet имеет только одну камеру.Размеры камеры сборки Voxeljet больше, чем у ExOne, и достигают (4 2 1 м), но максимальные размеры ExOne достигают (2,2 1,2 0,6) 2 м.
В настоящее время основная конкуренция между этими принтерами связана с разрешением и скоростью, которые играют важную роль в внешнем виде и механических характеристиках изготавливаемых деталей. Chuang (2017) утверждал, что при изменении угла установки картриджа с 1,1 до 90 ° разрешение струйной печати изменилось с 5080 до 100 dpi. В результате расстояние между каплями увеличивается с 5 до 254 мкм.Напечатанные точки имеют нежелательно большое перекрытие, когда расстояние между каплями слишком близко (короткое), что вызывает большое распространение чернил из-за истечения чернил. С другой стороны, линия неоднородной ширины или отдельные точки появляются, когда расстояние между каплями слишком велико, чтобы перекрывать каждую точку.
Одним из ограничений струйной печати является высокая пористость, которая делает образец более хрупким и проницаемым (то есть через него легко пропускается вода). Следовательно, требуется дополнительная постобработка, такая как отверждение при нагревании или с использованием водяного пара под давлением (Dikshit et al., 2018).
С другой стороны, высокая пористость делает деталь, напечатанную на 3D-принтере, очень легкой и простой в обращении, что может быть очень полезно для печати структурных компонентов. Это снижает вес здания и может быть очень эффективным в сейсмической зоне.
In Zhou et al. (2014) в исследовании была предложена плотность порошка над камерой сборки, которая называется плотностью слоя в процессе. Эта плотность обычно ниже истинной плотности и выше объемной плотности по величине.Однако это улучшение может подразумеваться типом упаковки порошкового слоя в камеру за счет изменения механической силы, приложенной к порошковому слою. Это может увеличить требуемое усилие ролика на слои слоя, что помогает уменьшить пустоты внутри частиц порошка. Результатом будет более высокая плотность и меньшая пористость, что, в свою очередь, устранит или уменьшит дополнительную постобработку.
Таблица 5 объясняет настройки струйного принтера, экструзионного принтера и выборочного лазерного спекания.
Таблица 5 . Объяснение настроек печати и способов печати.
SLS имеет широкое применение в других областях, но в области строительства он имеет ограниченное применение. Основными материалами, используемыми в этом процессе, являются порошки. Большинство порошков, используемых в этом приложении, представляют собой полимеры (нейлон). В процессе SLS порошки сплавляются или взаимодействуют друг с другом с помощью лазера. Если порошки не реагируют с помощью лазера, это неэффективный метод.
В некоторых исследованиях использовалась техника SLS для стоматологической работы, SLS и традиционный процесс.В процессе заметил, что зазор при литье при производстве SLS больше, чем при обычном литье во всех измеренных областях (Kim et al., 2013). Таким образом, методология SLS аналогична обработке струйной печати, которая создает аналогичные пустоты среди частиц.
Другим ограничением SLS является низкое разрешение из-за ограничений порошковых материалов, которые связаны с агломератами мелких частиц (Cao et al., 2015).
Экструзионная печать имеет наибольший потенциал для использования в области строительства по сравнению с другими методами аддитивного производства.В экструзионной печати существуют определенные ограничения, которые можно устранить в зависимости от масштаба проекта и материалов для печати (Wu et al., 2016).
Берман (2012) продемонстрировал, что быстрое прототипирование является наиболее успешным процессом для изготовления небольших частей строительных лесов.
Часто задаваемый вопрос: можно ли с помощью 3DP печатать в больших масштабах конструктивные элементы с прочными механическими свойствами. Однако в последние десятилетия на этот вопрос был дан ответ с развитием аддитивного производства.Например, компания WinSun в Китае построила сборные железобетонные изделия размером 150 10 6,6 м (Feng, 2014). Однако не было доказано, в какой степени эти элементы, напечатанные на 3D-принтере, могут выдерживать суровые условия окружающей среды и погодные условия.
Кроме того, было обнаружено, что скорость откачки и скорость движущегося рычага или сопла (механизма подачи) имеют решающее влияние на печатаемые объекты и разрешение образцов. Shakor et al. (2017a) провели всестороннее экспериментальное исследование различных бетонных смесей в отношении скорости робота, как показано в таблице 6.Оптимальная скорость печатающей головки робота составляет 39,36 мм / с при общей длине печатной линии (1580) мм, однако при использовании двигателя шнека в адаптированном экструдере 15–19 вольт.
Таблица 6 . Объясняет время и скорость печати конкретных результатов.
Исследование El Cheikh et al. (2017) исследовали скорость смещения горизонтальной плоскости с постоянной скоростью ( V p ), равной 50 д / с, где д / с — диаметр трубы в секунду.В исследовании Хамбаха и Фолькмера (2017) была получена скорость печати 30 мм / с за счет регулировки высоты слоя до 1,5 мм. Kazemian et al. (2017) использовали линейную скорость печати 60 мм / с. Однако Shakor et al. (2017a) в своем исследовании доказали, что наиболее подходящая скорость манипулятора робота, подходящая для печати на бетоне, составляет 39,36 мм / с для их смеси.
Скорость печати для экструзии материалов зависит от нескольких факторов: реологии материалов, размера сопла, формы сопла, расстояния между соплом и платформой для печати, а также расстояния между методом доставки и экструдером.
Моделирование в 3D-печати
Проанализированные исследования показывают, что различные смеси должны разрабатываться в зависимости от используемой техники печати. Бетон может быть напечатан с помощью различных процессов AM, таких как 2.5DP или 3DP. Например, процесс 2.5DP был реализован Lim et al. (2012), установив подвижную раму в трех направлениях, и 3DP был выполнен Gosselin et al. (2016), который с помощью робота приготовил строительный раствор для коротких колонн для изготовления сложной печатной геометрии.
Еще одна важная проблема в 3D-печати — это механические свойства (жесткость и прочность) печатного материала по отношению к его микроструктуре. Наличие заполнителей в бетоне может улучшить его механические свойства (Wu et al., 2001). Вместо крупных заполнителей, обычно используемых в бетоне, в смесь можно использовать более мелкие (2 ~ 4 мм) для улучшения механических свойств цемента (Lee et al., 2007). Кроме того, в конструкцию смеси могут быть добавлены короткие волокна (сталь, углерод или древесина) и некоторые отходы, такие как зола и шлак (Hambach and Volkmer, 2017), для улучшения механических свойств печатного материала.Хотя новые экструзионные принтеры (например, разработанные авторами) предлагают гибкость в 3D-печати сложных конструкций с различными бетонными смесями, оптимальные конструкции смеси для конкретного приложения (или условий нагрузки) требуют разработки универсальных многомасштабных моделей и различной геометрии. Недавно в Массачусетском технологическом институте была разработана многомасштабная вычислительная модель для 3D-печати коротковолокнистых композитов (Malek et al., 2017), чтобы лучше понять влияние различных параметров конструкции на эффективные свойства печатного материала.В настоящее время авторы разрабатывают аналогичную многомасштабную модель для 3D-печати железобетона с короткими волокнами.
В дополнение к механическим характеристикам, печатаемость и текучесть материала будут зависеть от изменения конструкции смеси (Lim et al., 2012). Следовательно, прогнозирование реологических свойств цементного теста с наполнителями необходимо интегрировать с вышеупомянутой многомасштабной моделью. Предполагается, что разработка интегрированной структуры моделирования для бетона, аналогичной разработанной для усовершенствованных композитов, армированных волокном (Johnston et al., 2001; Haghshenas et al., 2018), в следующие десятилетия предложат интеллектуальный дизайн и печать различных бетонных смесей.
Заключение
В этой статье были рассмотрены различные методы аддитивного производства, которые можно использовать для черчения / печати в строительной отрасли. Обсуждался выбор принтера, дизайна смеси и метода печати. Для сравнения характеристик и ограничений различных методов 3D-печати бетона были выбраны три эталонных примера.Результаты показали, что экструзионная печать с помощью промышленных роботов-манипуляторов является универсальной техникой, которую можно адаптировать для быстрых и индивидуальных строительных проектов. Были изучены несколько параметров и характеристик принтера, включая скорость, прочность, точность и разрешение печати вместе с бетонной смесью. Было обнаружено, что, управляя различными функциями экструзионного принтера, такими как скорость, диаметр сопла и расстояние от субстрата, можно печатать различные бетонные смеси; Таким образом, в будущем возможно строительство большого количества сложных конструкций различных размеров.Тем не менее, необходимы дальнейшие исследования для улучшения (и прогнозирования) механических свойств и пригодности для печати структурных элементов, напечатанных на 3D-принтере. Примечательно, что реология смеси и взаимосвязь с ортотропными свойствами бетона требуют дальнейшего изучения. Дальнейшая работа будет сосредоточена на разработке физических моделей в различных масштабах (например, чистый цемент, заполненный цемент и готовый бетон), которые, в свою очередь, позволят оптимизировать параметры печати, используемые в технике экструзии.
Авторские взносы
PS и SN внесли свой вклад в концепцию и идею обзорной статьи. PS организовал всю базу данных и интерпретацию микса обзорных статей. СМ выполнял интерпретацию раздела моделирования. GP рассматривает первый вариант рукописи и проверяет все мехатронные темы, связанные с его областью. PS, SN, GP и SM просмотрели все разделы рукописи. Все авторы внесли свой вклад в организацию рукописи, прочитали, отредактировали и одобрили представленную версию.
Заявление о конфликте интересов
Авторы заявляют, что исследование проводилось при отсутствии каких-либо коммерческих или финансовых отношений, которые могут быть истолкованы как потенциальный конфликт интересов.
Благодарности
Авторы хотели бы выразить свою благодарность Технологическому университету Суинберна (Центр устойчивой инфраструктуры) за установку SLS. Авторы также хотели бы выразить искреннюю благодарность компании Sika Australia за поставку химических материалов и Elasto Plastic Concrete за предоставленные материалы.
Список литературы
Ашраф М., Гибсон И. и Рашед М. Г. (2018). «Проблемы и перспективы 3D-печати в строительстве», 13-я Международная конференция по стальным, космическим и композитным конструкциям (Перт, Вашингтон).
Google Scholar
Барнетт, Э., Госселин, К. (2015). Масштабная 3D-печать с помощью робота на тросе. Аддитивное производство. 7, 27–44. DOI: 10.1016 / j.addma.2015.05.001
CrossRef Полный текст | Google Scholar
Берман, Б.(2012). 3-D печать: новая промышленная революция. Business Horizons 55, 155–162. DOI: 10.1016 / j.bushor.2011.11.003
CrossRef Полный текст | Google Scholar
Бос Ф., Вольфс Р., Ахмед З. и Салет Т. (2016). Аддитивное производство бетона в строительстве: возможности и проблемы 3D-печати бетоном. Virtu. Phys. Прототип. 11, 209–225. DOI: 10.1080 / 17452759.2016.1209867
CrossRef Полный текст | Google Scholar
Бос, Ф.П., Ахмед, З. Ю., Вольфс, Р. Дж. М., и Салет, Т. А. М. (2018). 3D-печать бетона с армированием. Высокотехнологичный бетон: место встречи технологий и инженерии . Чам: Издательство Springer International. 2484–2493. DOI: 10.1007 / 978-3-319-59471-2_283
CrossRef Полный текст | Google Scholar
Браун, А. (2015). 3D-печать в учебной среде: определение иерархии занятий в учебной программе. TechTrends 59, 16–24. DOI: 10.1007 / s11528-015-0887-1
CrossRef Полный текст | Google Scholar
Басвелл, Р.А., Соар Р., Гибб А. Г. и Торп А. (2007). Строительство произвольной формы: мегамасштабное быстрое производство для строительства. Автомат. Построить. 16, 224–231. DOI: 10.1016 / j.autcon.2006.05.002
CrossRef Полный текст | Google Scholar
Каньете Вела, И. (2014). Дизайн электроники для 3D-принтеров . Политехнический университет Каталонии.
Google Scholar
Цао С., Цю Ю., Вэй Х.-Ф. и Чжан Х.-Х. (2015). Экспериментальное и теоретическое исследование наслоения ультратонких порошков в трехмерной печати (3DP) с помощью нового механизма двойного сглаживания. J. Mater. Процесс. Technol. 220, 231–242. DOI: 10.1016 / j.jmatprotec.2015.01.016
CrossRef Полный текст | Google Scholar
Castilho, M., Dias, M., Gbureck, U., Groll, J., Fernandes, P., Pires, I., et al. (2013). Изготовление компьютерных каркасов с помощью низкотемпературной 3D-печати. Биологическое производство 5: 035012. DOI: 10.1088 / 1758-5082 / 5/3/035012
PubMed Аннотация | CrossRef Полный текст | Google Scholar
Кастильо, М., Гувейя, Б., Пирес, И., Родригес, Дж., И Перейра, М. (2015). Роль уровня насыщения оболочки / ядра на точность и механические характеристики моделей пористого фосфата кальция, изготовленных методом 3D-печати. Rapid Prototyp. J. 21, 43–55. DOI: 10.1108 / RPJ-02-2013-0015
CrossRef Полный текст | Google Scholar
Кастильо, М., Пирес, И., Гувейя, Б., и Родригес, Дж. (2011). Структурная оценка прототипов строительных лесов, изготовленных методом трехмерной печати. Внутр.J. Adv. Производство. Technol. 56, 561–569. DOI: 10.1007 / s00170-011-3219-4
CrossRef Полный текст | Google Scholar
Крист С., Шнабель М., Ворндран Э., Гролл Дж. И Гбурек У. (2015). Армирование волокном при 3D-печати. Mater. Lett. 139, 165–168. DOI: 10.1016 / j.matlet.2014.10.065
CrossRef Полный текст | Google Scholar
Чуа, К. К., и Леонг, К. Ф. (2014). 3D-печать и аддитивное производство: принципы и приложения (с сопутствующим медиа-пакетом) быстрого прототипирования .Сингапур: Singapore World Scientific Publishing Co Inc.
Google Scholar
Чуанг, М. Ю. (2017). Струйная печать наночастиц Ag с использованием струйного принтера Dimatix. № 2.
Коул Р. Дж. (1998). Выбросы энергии и парниковых газов, связанные со строительством альтернативных структурных систем. Сборка. Environ. 34, 335–348. DOI: 10.1016 / S0360-1323 (98) 00020-1
CrossRef Полный текст | Google Scholar
Кокс, С.К., Торнби, Дж. А., Гиббонс, Г. Дж., Уильямс, М. А., и Маллик, К. К. (2015). 3D-печать пористых гидроксиапатитовых каркасов, предназначенных для использования в инженерии костной ткани. Mater. Sci. Англ. C , 47 (Дополнение C), 237–247. DOI: 10.1016 / j.msec.2014.11.024
PubMed Аннотация | CrossRef Полный текст | Google Scholar
Далгарно К. и Стюарт Т. (2001). Производство технологической оснастки для пресс-форм с конформными каналами охлаждения посредством непрямого селективного лазерного спекания. Proc. Institut. Мех. Англ. В 215, 1323–1332. DOI: 10.1243 / 0954405011519042
CrossRef Полный текст | Google Scholar
Де Витте, Д. (2015). Бетон в процессе AM: обработка бетона произвольной формы . TU Delft.
Дельгадо Камачо, Д., Клейтон, П., О’Брайен, В. Дж., Сиперсад, К., Юнгер, М., Феррон, Р. и др. (2018). Применение аддитивного производства в строительной отрасли — перспективный обзор. Автомат. Построить. 89, 110–119. DOI: 10.1016 / j.autcon.2017.12.031
CrossRef Полный текст | Google Scholar
Дикшит В., Нагалингам А. П., Яп Ю. Л., Синг С. Л., Йонг В. Ю. и Вэй Дж. (2018). Мониторинг трещин и расследование отказов сэндвич-структур, напечатанных на струйной печати, при квазистатическом испытании на вдавливание. Mater. Проект 137, 140–151. DOI: 10.1016 / j.matdes.2017.10.014
CrossRef Полный текст | Google Scholar
Эдвардс, Л., Холт, К., Кейт, Л.и Ллойд Р. (2013). «Строительная 3D-печать», бетон , бетон (Голд-Кост, QLD).
Google Scholar
Эль Шейх, К., Ремон, С., Халил, Н., Ауад, Г. (2017). Численные и экспериментальные исследования блокирования заполнителей при экструзии строительных растворов. Construct. Строить. Матер. 145, 452–463. DOI: 10.1016 / j.conbuildmat.2017.04.032
CrossRef Полный текст | Google Scholar
Эльхаг, Х., Гласс, Дж., Гибб, А. Г., Кларк, М., Бадж, К., и Бейли, Г.(2008). Внедрение экологических улучшений в производственном контексте: структурированный подход для промышленности сборного железобетона. Внутр. J. Environ. Technol. Manag. 8, 369–384. DOI: 10.1504 / IJETM.2008.017508
CrossRef Полный текст | Google Scholar
Фарзади А., Варан В., Солати-Хашджин М., Асади-Эйдиванд М. и Абу Осман Н. А. (2014). Влияние толщины слоя и ориентации печати на механические свойства и точность размеров пористых образцов, напечатанных на 3D-принтере, для инженерии костной ткани. PLoS ONE 9: e108252. DOI: 10.1371 / journal.pone.0108252
PubMed Аннотация | CrossRef Полный текст | Google Scholar
Фарзади А., Варан В., Солати-Хашджин М., Рахман З. А. А., Асади М. и Осман Н. А. (2015). Влияние задержки печати слоя на механические свойства и точность размеров пористых прототипов, напечатанных на 3D-принтере, в инженерии костной ткани. Керамика Инт. 41, 8320–8330. DOI: 10.1016 / j.ceramint.2015.03.004
CrossRef Полный текст | Google Scholar
Фенг, Л.Ю. (2014). Исследование статус-кво и проблем 3D-печати зданий в Китае. Global J. Hum. Soc. Sci. Res. 14: 5.
Google Scholar
Фэн П., Мэн Х., Чен Дж.-Ф. и Е Л. (2015a). Механические свойства конструкций, напечатанных на 3D-принтере цементными порошками. Construct. Строить. Матер. 93, 486–497. DOI: 10.1016 / j.conbuildmat.2015.05.132
CrossRef Полный текст | Google Scholar
Фэн П., Мэн X. и Чжан Х. (2015b).Механическое поведение армированных листов FRP 3D-элементов, напечатанных с использованием вяжущих материалов. Композитная конструкция. 134, 331–342. DOI: 10.1016 / j.compstruct.2015.08.079
CrossRef Полный текст | Google Scholar
Гараи, С. Х., Морси, Ю., и Масуд, С. Х. (2013). Прочность на растяжение обработанного 3D-принтера порошкового материала ZP150. Adv. Матер. Res. 699, 813–816. DOI: 10.4028 / www.scientific.net / AMR.699.813
CrossRef Полный текст | Google Scholar
Гиббонс, Г.Дж., Уильямс, Р., Пурнелл, П., и Фарахи, Э. (2010). 3D-печать цементных композитов. Adv. Прил. Керамика 109, 287–290. DOI: 10.1179 / 174367509X12472364600878
CrossRef Полный текст | Google Scholar
Госслен, К., Дюбале, Р., Ру, П., Годильер, Н., Дирренбергер, Дж., И Морель, П. (2016). Масштабная 3D-печать бетона со сверхвысокими характеристиками — новый технологический путь для архитекторов и строителей. Mater. Дизайн 100, 102–109. DOI: 10.1016 / j.маты.2016.03.097
CrossRef Полный текст | Google Scholar
Хагер И., Голонка А. и Путанович Р. (2016). 3D-печать зданий и их компонентов как будущее устойчивого строительства? Proc. Англ. 151, 292–299. DOI: 10.1016 / j.proeng.2016.07.357
CrossRef Полный текст | Google Scholar
Haghshenas, S.M., Vaziri, R., and Poursartip, A. (2018). Интеграция течения смолы и развития напряжения при моделировании процесса композитов: часть II — трансверсально изотропная формулировка. J. Comp. Матер. 52, 3157–3171. DOI: 10.1177 / 0021998318762296
CrossRef Полный текст | Google Scholar
Хамбах, М., Фолькмер, Д. (2017). Свойства армированной волокном портландцементной пасты, напечатанной на 3D-принтере. Цементно-бетонные композиты 79, 62–70. DOI: 10.1016 / j.cemconcomp.2017.02.001
CrossRef Полный текст | Google Scholar
Хенке, К., Тремл, С. (2012). Объемный материал на основе древесины в процессах 3D-печати для применения в строительстве. евро. J. Wood Wood Products 71, 139–141. DOI: 10.1007 / s00107-012-0658-z
CrossRef Полный текст | Google Scholar
Hwang, D., and Khoshnevis, B. (2004). «Изготовление бетонных стен методом контурной обработки», 21-й Международный симпозиум по автоматизации и робототехнике в строительстве (ISARC 2004) , Чеджу. DOI: 10.22260 / ISARC2004 / 0057
CrossRef Полный текст | Google Scholar
Ян, Г., и Дунпин, С. (1997). Свойства материалов и параметры изготовления в процессе селективного лазерного спекания. Rapid Prototyp. J. 3, 129–136. DOI: 10.1108 / 135525497101
CrossRef Полный текст | Google Scholar
Jeng, J.-Y., Peng, S.-C., and Chou, C.-J. (2000). Быстрое изготовление прототипов металла с использованием технологии селективной лазерной наплавки. Внутр. J. Adv. Производство. Technol. 16, 681–687. DOI: 10.1007 / s001700070039
CrossRef Полный текст | Google Scholar
Jeon, K.-H., Park, M.-B., Kang, M.-K., and Kim, J.-H. (2013). «Разработка автоматизированной системы строительства произвольной формы и ее строительных материалов», в Труды 30-го Международного симпозиума по автоматизации и робототехнике в строительстве и горнодобывающей промышленности .Citeseer. 1359–1365. DOI: 10.22260 / ISARC2013 / 0153
CrossRef Полный текст | Google Scholar
Jianchao, Z., Zhang, T., Faried, M., and Wengang, C. (2017). «Чернила на основе цемента для 3D-печати и их применение в строительной отрасли», в MATEC Web of Conferences (Малакка: EDP Sciences).
Google Scholar
Джонстон А., Вазири Р. и Пурсартип А. (2001). Модель плоской деформации для технологической деформации слоистых композитных конструкций. J. Composite Mater. 35, 1435–1469. DOI: 10.1106 / YXEA-5MH9-76J5-BACK
CrossRef Полный текст | Google Scholar
Каземян А., Юань X., Кокран Э. и Хошневис Б. (2017). Вяжущие материалы для 3D-печати в строительных масштабах: лабораторные испытания свежей смеси для печати. Construct. Строить. Матер. 145, 639–647. DOI: 10.1016 / j.conbuildmat.2017.04.015
CrossRef Полный текст | Google Scholar
Хошневис, Б., Буккапатнам, С., Квон, Х., и Сайто, Дж. (2001). Экспериментальное исследование контурной обработки керамическими материалами. Rapid Prototyp. J. 7, 32–42. DOI: 10.1108 / 13552540110365144
CrossRef Полный текст | Google Scholar
Хошневис Б. и Даттон Р. (1998). Инновационный процесс быстрого прототипирования позволяет создавать сложные формы большого размера с гладкой поверхностью из самых разных материалов. Mater. Technol. 13, 53–56. DOI: 10.1080 / 10667857.1998.11752766
CrossRef Полный текст | Google Scholar
Ким, К.-B., Kim, J.-H., Kim, W.-C., Kim, H.-Y., and Kim, J.-H. (2013). Оценка краевого и внутреннего зазора металлокерамической коронки, изготовленной по технологии селективного лазерного спекания: методы двумерной и трехмерной реплик. J. Adv. Протезирование , 5, 179–186. DOI: 10.4047 / jap.2013.5.2.179
PubMed Аннотация | CrossRef Полный текст | Google Scholar
Колосов, С., Бойя, Э., Глардон, Р., Фишер, П., и Локер, М. (2004). Трехмерное КЭ-моделирование эволюции температуры в процессе селективного лазерного спекания. Внутр. J. Станки Производство. 44, 117–123. DOI: 10.1016 / j.ijmachtools.2003.10.019
CrossRef Полный текст | Google Scholar
Крут, Дж. П., Мерселис, П., Ван Вэренберг, Дж., Фройен, Л., и Ромбоут, М. (2005). Механизмы связывания в селективном лазерном спекании и селективном лазерном плавлении. Rapid Prototyp. J. 11, 26–36. DOI: 10.1108 / 13552540510573365
CrossRef Полный текст | Google Scholar
Кумар, С. (2003). Селективное лазерное спекание: качественный и объективный подход. JOM 55, 43–47. DOI: 10.1007 / s11837-003-0175-y
CrossRef Полный текст | Google Scholar
Лаги В., Палермо М., Праглиола М., Джирелли В. А., Фельден Г. В. Д. и Тромбетти Т. (2018). «К стальным сетчатым оболочкам, напечатанным на 3D-принтере: основная идея и первые исследования», в материалах Труды симпозиума IASS 2018 «Творчество в структурном дизайне». Бостон: IASS2018.
Google Scholar
Ле, Х. П. (1998). Прогресс и тенденции в технологии струйной печати. J. Imaging Sci. Technol. 42, 49–62.
Google Scholar
Ле Т. Т., Остин С. А., Лим С., Басвелл Р. А., Гибб А. Г. Ф. и Торп Т. (2012a). Сочетание дизайна и свежих свойств для получения высококачественного полиграфического бетона. Mater. Struct. 45, 1221–1232. DOI: 10.1617 / s11527-012-9828-z
CrossRef Полный текст | Google Scholar
Ле, Т. Т., Остин, С. А., Лим, С., Басуэлл, Р. А., Лоу, Р., Гибб, А. Г. Ф. и др. (2012b). Упрочненные свойства высокопроизводительного полиграфического бетона. Цемент Бетон Рес. 42, 558–566. DOI: 10.1016 / j.cemconres.2011.12.003
CrossRef Полный текст | Google Scholar
Ли, С. С., Ким, С. Г., Ким, Х. Дж., И Ан, С. Х. (2007). Измерение анизотропной прочности на сжатие деталей для быстрого прототипирования. J. Mater. Процесс. Technol. 187–188, 627–630. DOI: 10.1016 / j.jmatprotec.2006.11.095
CrossRef Полный текст | Google Scholar
Льюис, Дж. А., Смей, Дж. Э., Стюкер, Дж. И Чезарано, Дж.(2006). Прямое рукописное написание трехмерных керамических структур. J. Am. Керамический Soc. 89, 3599–3609. DOI: 10.1111 / j.1551-2916.2006.01382.x
CrossRef Полный текст | Google Scholar
Ли Т., Асплер Дж., Кингсленд А., Кормье Л. М. и Цзоу X. (2016). 3D-печать — обзор технологий, рынков и возможностей лесной отрасли. J. Sci. Technol. Для. Prod. Процесс , 5:30.
Google Scholar
Лим, С., Басуэлл, Р.А., Ле Т. Т., Остин С. А., Гибб А. Г. Ф. и Торп Т. (2012). Развитие процессов аддитивного производства в строительных масштабах. Автомат. Построить. 21, 262–268. DOI: 10.1016 / j.autcon.2011.06.010
CrossRef Полный текст | Google Scholar
Лим, С., Басвелл, Р. А., Валентин, П. Дж., Пайкер, Д., Остин, С. А., и Де Кестелье, X. (2016). Моделирование траекторий печати с изогнутыми слоями для изготовления крупногабаритных строительных компонентов. Аддитивное производство. 12 (Часть B), 216–230. DOI: 10.1016 / j.addma.2016.06.004
CrossRef Полный текст | Google Scholar
Липсон, Х., Курман, М. (2013). Изготовлено: новый мир 3D-печати . Нью-Йорк, штат Нью-Йорк: Джон Уайли и сыновья.
Google Scholar
Льорет, Э., Шахаб, А. Р., Линус, М., Флатт, Р. Дж., Грамацио, Ф., Колер, М. и др. (2015). Сложные бетонные конструкции: объединение существующих технологий литья с цифровым производством. Comput. Система автоматизированного проектирования 60, 40–49.DOI: 10.1016 / j.cad.2014.02.011
CrossRef Полный текст | Google Scholar
Лоу, З.-Х., Чуа, Ю. Т., Рэй, Б. М., Маттиа, Д., Меткалф, И. С., и Паттерсон, Д. А. (2017). Перспективы 3D-печати разделительных мембран и сравнение с соответствующими нетрадиционными технологиями производства. J. Membrane Sci. 523, 596–613. DOI: 10.1016 / j.memsci.2016.10.006
CrossRef Полный текст | Google Scholar
Лу К., Хизер М. и Ву В. (2009). Влияние размера частиц на трехмерные печатные сетчатые структуры. Порошок Технол. 192, 178–183. DOI: 10.1016 / j.powtec.2008.12.011
CrossRef Полный текст | Google Scholar
Лу К. и Рейнольдс В. Т. (2008). Процесс 3DP для печати мелкоячеистой структуры. Порошок Технол. 187, 11–18. DOI: 10.1016 / j.powtec.2007.12.017
CrossRef Полный текст | Google Scholar
Ма, Г., Ван, Л., Цзюй, Ю. (2017). Современное состояние технологии 3D-печати из цементного материала — новая техника для строительства. Sci. China Technol. Sci. 61, 475–495. DOI: 10.1007 / s11431-016-9077-7
CrossRef Полный текст | Google Scholar
Малаеб З., Хашем Х., Турбах А., Маалуф Т., Эль Зарви Н. и Хамзех Н. (2015). 3d печать на бетоне: дизайн машин и смесей. Внутр. Дж. Гражданский английский язык . 6, 14–22.
Google Scholar
Марчелли, Г., Прабхакар, Р., Сторти, Д., и Гантер, М. (2011). Руководство по 3D-печати стеклом: разработки, методы, диагностика и результаты. Rapid Prototyp. J. 17, 187–194. DOI: 10.1108 / 13552541111124761
CrossRef Полный текст | Google Scholar
Миянаджи, Х., Чжан, С., Лассел, А., Зандинеджад, А., и Ян, Л. (2016). Оптимальные технологические параметры для 3D-печати керамических конструкций. Proc. Производство. 5, 870–887. DOI: 10.1016 / j.promfg.2016.08.074
CrossRef Полный текст | Google Scholar
Мюллер, С., Им, С., Гуревич, С., Тейбрих, А., Пфистерер, Л., Гимбретиере, Ф., и другие. (2014). «WirePrint: предварительные просмотры на 3D-принтере для быстрого прототипирования» в материалах Труды 27-го ежегодного симпозиума ACM по программному обеспечению и технологиям пользовательского интерфейса . Гонолулу, Гавайи: ACM, 273–280. DOI: 10.1145 / 2642918.2647359
CrossRef Полный текст | Google Scholar
Мукеш, А., Дэвид, Б., Джозеф, Б., Харрис, М., и Джоэл, Б. (1995). Прямое селективное лазерное спекание металлов. Rapid Prototyp. J. 1, 26–36. DOI: 10.1108 / 13552549510078113
CrossRef Полный текст | Google Scholar
Нерелла, В.N., Schroefl, C., Yazdi, M.A., Alghazali, A., Secrieru, E., Shyshko, S., et al. (2017). «Микро- и макроскопические исследования границы раздела между слоями цементных элементов, напечатанных на 3D-принтере», на Международной конференции по достижениям в области строительных материалов и систем ICACMS 2017, , Ченнаи.
Google Scholar
Нго, Т. Д., Кашани, А., Имбальзано, Г., Нгуен, К. Т. К. и Хуэй, Д. (2018). Аддитивное производство (3D-печать): обзор материалов, методов, приложений и проблем. Композиты B Eng. 143, 172–196. DOI: 10.1016 / j.compositesb.2018.02.012
CrossRef Полный текст | Google Scholar
Пенья, Дж. (1997). Исследовательское исследование массивных конструкций произвольной формы. Автомат. Построить. , 5, 427–437. DOI: 10.1016 / S0926-5805 (96) 00166-5
CrossRef Полный текст | Google Scholar
Перро А., Рэнджерд Д. и Пьер А. (2015). Структурное наращивание из материалов на основе цемента, используемых для экструзионных технологий 3D-печати. Mater. Struct. 49, 1–8. DOI: 10.1617 / s11527-015-0571-0
CrossRef Полный текст | Google Scholar
Питер, М., и Жан-Пьер, К. (2006). Остаточные напряжения при селективном лазерном спекании и селективном лазерном плавлении. Rapid Prototyp. J. 12, 254–265. DOI: 10.1108 / 13552540610707013
CrossRef Полный текст | Google Scholar
Раэль Р., Сан Фрателло В. (2011). Проектирование и анализ материалов для 3D-печати компонентов здания из цементного полимера, армированного волокном .Калифорния, Калифорния: СТУДИЯ RAEL SAN FRATELLO.
Google Scholar
Рашиди, М., Аштиани, Р. С., Си, Дж., Иззо, Р. П., и МакДэниел, М. (2018). Практический подход к оценке прочностных и упругих свойств вяжущих материалов. Транспорт. Res. Рек. 2018: 0361198118769900. DOI: 10.1177 / 0361198118769900
CrossRef Полный текст | Google Scholar
Рашинг, Т.С., Аль-Чаар, Г., Эйк, Б.А., Берроуз, Дж., Шеннон, Дж., Барна, Л., и другие. (2017). Исследование бетонных смесей для аддитивного строительства. Rapid Prototyp. J. 23, 74–80. DOI: 10.1108 / RPJ-09-2015-0124
CrossRef Полный текст | Google Scholar
Шакор П., Неджади С., Пол Г. и Санджаян Дж. (2018). «Новая методология порошковых цементных материалов в 3D-струйной печати для строительных приложений», в Шестая международная конференция по долговечности бетонных конструкций . (Лидс, Великобритания: Whittles Publishing).
Google Scholar
Шакор П., Пимпликар С. и Гаре У. (2011). Технико-коммерческие аспекты использования стекловолокна в строительной промышленности, Достижения и тенденции в конструкционных материалах и их применении , Монреаль; Оттава, Онтарио: передовые инженерные решения.
Google Scholar
Шакор П., Реннеберг Дж., Неджади С. и Пол Г. (2017a). «Оптимизация различных конструкций бетонной смеси для 3D-печати с использованием промышленного робота 6DOF, ISARC», в материалах Труды Международного симпозиума по автоматизации и робототехнике в строительстве .Тайбэй: Вильнюсский технический университет им. Гедиминаса, факультет экономики строительства и собственности.
Google Scholar
Шакор П., Санджаян Дж., Назари А. и Неджади С. (2017b). Модифицированный порошок для 3D-печати для материала на основе цемента и механических свойств цементных лесов, используемых в 3D-печати. Construct. Строительный матер. 138, 398–409. DOI: 10.1016 / j.conbuildmat.2017.02.037
CrossRef Полный текст | Google Scholar
Шакор П. Н., Пимпликар С.(2011). Применение бетона, армированного стекловолокном, в строительстве. Внутр. J. Technol. Англ. Syst . 2: 2.
Google Scholar
Шофнер М., Лосано К., Родригес-Масиас Ф. и Баррера Э. (2003). Полимеры, армированные нановолокном, полученные путем моделирования методом наплавления. J. Appl. Polymer Sci. 89, 3081–3090. DOI: 10.1002 / app.12496
CrossRef Полный текст | Google Scholar
Spath, S., and Seitz, H. (2013). Влияние размера и гранулометрического состава гранул на удобоукладываемость при 3D-печати. Внутр. J. Adv. Производство. Technol. 70, 135–144. DOI: 10.1007 / s00170-013-5210-8
CrossRef Полный текст | Google Scholar
Сугама Т. и Карсьелло Н. Р. (1991). Повышение прочности фосфатно-алюминатных цементов на основе кальция. J. Am. Керамический Soc. 74, 1023–1030. DOI: 10.1111 / j.1151-2916.1991.tb04338.x
CrossRef Полный текст | Google Scholar
Там, В. В., Там, К., Чан, Дж. К., и Нг, В. К. (2006). Рубка строительных отходов сборным способом. Внутр. J. Construct. Manag. 6, 15–25. DOI: 10.1080 / 15623599.2006.10773079
CrossRef Полный текст | Google Scholar
Тай, Ю. В., Панда, Б., Пол, С. К., Мохамед, Н. А. Н., Тан, М. Дж., Леонг, К. Ф. и др. (2016). Обработка и свойства строительных материалов для 3D-печати . Форум по материаловедению.
Google Scholar
Тай, Ю. В. Д., Панда, Б., Пол, С. К., Мохамед, Н. А. Н., Тан, М. Дж., И Леонг, К. Ф. (2017). Тенденции 3D-печати в строительстве: обзор. Virtu. Phys. Прототип. 12, 261–276. DOI: 10.1080 / 17452759.2017.1326724
CrossRef Полный текст | Google Scholar
Утела Б., Сторти Д., Андерсон Р. и Гантер М. (2008). Обзор этапов разработки процессов для новых систем материалов в трехмерной печати (3DP). J. Manufactur. Процесс. 10, 96–104. DOI: 10.1016 / j.jmapro.2009.03.002
CrossRef Полный текст | Google Scholar
Ваези М. и Чуа К. (2011). Влияние толщины слоя и параметров уровня насыщения связующего на процесс 3D-печати. Внутр. J. Adv. Производство. Technol. 53, 275–284. DOI: 10.1007 / s00170-010-2821-1
CrossRef Полный текст | Google Scholar
Власеа М., Пиллиар Р. и Тойсеркани Э. (2015a). Контроль структурных и механических свойств биокерамических заменителей кости путем ориентации укладки слоев аддитивного производства. Аддитивное производство. 6, 30–38. DOI: 10.1016 / j.addma.2015.03.001
CrossRef Полный текст | Google Scholar
Власеа, М., Тойсеркани, Э., и Пиллиар Р. (2015b). Влияние уровней связующего в серой шкале на аддитивное производство пористых каркасов с гетерогенными свойствами. Внутр. J. Appl. Керамика Technol. 12, 62–70. DOI: 10.1111 / ijac.12316
CrossRef Полный текст | Google Scholar
Вегер Д., Лоук Д. и Гелен К. (2016). «3D-печать бетонных конструкций из цемента на основе силиката кальция с использованием метода селективного цементирования — влияние технологии бетона на глубину проникновения цементного теста», в Бетон со сверхвысокими характеристиками и высокоэффективные строительные материалы , HiPerMat 2016, 193.
Google Scholar
Вителл, А., Дигель, О., Групп, И., Рей, С., де Бир, Д., и Потгитер, Дж. (2011). «Пористые керамические фильтры через 3D-печать, инновационные разработки в области виртуальных и физических прототипов», в материалах Труды 5-й Международной конференции по перспективным исследованиям в области виртуальных и быстрых прототипов (Leiria: CRC Press), 313.
Google Scholar
Ву, К.-Р., Чен, Б., Яо, В., и Чжан, Д. (2001). Влияние типа крупного заполнителя на механические свойства высокопрочного бетона. Цемент Бетон Рес. 31, 1421–1425. DOI: 10.1016 / S0008-8846 (01) 00588-9
CrossRef Полный текст | Google Scholar
Ву П., Ван Дж. И Ван Х. (2016). Критический обзор использования трехмерной печати в строительной отрасли. Автомат. Построить. 68, 21–31. DOI: 10.1016 / j.autcon.2016.04.005
CrossRef Полный текст | Google Scholar
Зейн И., Хутмахер Д. В., Тан К. К. и Теох С. Х. (2002). Моделирование наплавленного осаждения новых архитектур каркасов для приложений тканевой инженерии. Биоматериалы 23, 1169–1185. DOI: 10.1016 / S0142-9612 (01) 00232-0
PubMed Аннотация | CrossRef Полный текст | Google Scholar
Чжоу З., Бьюкенен Ф., Митчелл К. и Данн Н. (2014). Возможность печати порошков фосфата кальция: сульфата кальция для применения тканевых костных каркасов с использованием технологии 3D-печати. Mater. Sci. Англ. C Mater. Биол. Заявление . 38, 1–10. DOI: 10.1016 / j.msec.2014.01.027
PubMed Аннотация | CrossRef Полный текст | Google Scholar
Чжоу, З., Митчелл, К. А., Бьюкенен, Ф. Дж., И Данн, Н. Дж. (2013). Влияние термической обработки на механические свойства и характеристики разрушения каркасов на основе сульфата кальция, напечатанных на 3D-принтере. ISRN Биоматериалы 2013, 1–10. DOI: 10.5402 / 2013/750720
CrossRef Полный текст | Google Scholar
Зиджл, Г., Суваш, К., Пол, С., и Тан, М. Дж. (2016). «Свойства бетона для 3D-печати», 2-я Международная конференция по прогрессу в аддитивном производстве (Pro-AM 2016) , Наньян.
Google Scholar
Производство бетона — обзор
11.3.1 Переработанные заполнители
По мере того, как производство бетона во всем мире продолжает расти, растет и использование и потребление абиотических ресурсов, таких как заполнители. Чтобы подтвердить это утверждение, совокупный мировой спрос вырастет с 45,9 до 66,3 Гт в течение 10 лет (например, 2012–22 годы) (Freedonia, 2012). Еще один четкий показатель использования и роста бетона связан с производством цемента, который увеличится с 2.От 77 Гт в 2007 году (USGS, 2008) до от 3,8 до 4,6 Гт в 2050 году (IEA, 2010). Учитывая эти показатели, совершенно необходимо появление новых решений по замене НА в производстве бетона.
Среди возможных решений для этого повышенного совокупного спроса замена НП на РП промышленных побочных продуктов кажется логичным и экологически привлекательным решением: это не только помогает решить проблему абиотического истощения, но также может помочь в данной теме. удаления промышленных отходов, что часто сопряжено с серьезными экологическими проблемами (Samuelson, 2009).Основным источником этих RA являются отходы строительства и сноса (CDW), но к другим возможным из них относятся, среди прочего, отходы горнодобывающей промышленности, отходы пластмасс, угольная зола, резина шин, шлаки, промышленные шламы (de Brito and Saikia, 2013). Учитывая их природу и состав, как КДВ, так и отходы горнодобывающей промышленности принято определять как минеральные отходы, выделяя их отдельно от остальных с точки зрения потенциального использования в качестве РЗ.
НаКДВ в 2012 г. приходилось около 33% (821 млн т) всех отходов, произведенных в Европейском союзе, за которыми следовали отходы горнодобывающей промышленности, что соответствовало 29% (734 млн т).В целом, минеральные отходы составляют 62% от общего количества производимых отходов, что подчеркивает важность, которую побочные продукты могут иметь в любых будущих решениях для более экологичного бетона. CDW включает в себя широкий спектр материалов, различный химический и минералогический состав, а также различные уровни опасности. Эти различия обычно используются для определения меньших категорий CDW, которые классифицируют материалы по их возможности вторичной переработки. Например, Европейский Союз (Комиссия ЕС, 2016) создал девять подгрупп CDW, начиная от «17 01 — бетон, кирпич, плитка и керамика», наиболее подходящие материалы для вторичной переработки, до «17 09 — Другие CDW». , без возможности повторного использования.Среди всего объема КДВ бетон, строительный раствор и керамика составляют основной объем всех месторождений, что соответствует 60–80% от всего объема КДВ (Mália et al., 2013; EPA, 2016). Имея это в виду, мировые исследования в основном сосредоточены на использовании этих видов материалов в качестве замены NA в бетоне, и результаты показали, что RA подходят для замены их естественных аналогов, даже если необходимо пойти на некоторые компромиссы, так как бетон производительность имеет тенденцию к снижению по мере увеличения коэффициента замещения (Rao et al., 2007; Ли, 2008; Макнил и Канг, 2013; Бехера и др., 2014; Евангелиста и де Брито, 2014).
Одной из основных проблем, с которыми сталкивается строительный сектор при использовании RA, является их неоднородность. В отличие от НА, которые обладают относительно стабильными свойствами, учитывая их минералогическую природу, свойства РА зависят не только от источника КДВ, но и от их переработки и обработки на заводе по переработке (Ulsen et al., 2010; Florea and Brouwers, 2013; Pedro и др., 2014). Эти различные методы обработки изменяют ключевые свойства, такие как плотность и водопоглощение, морфология, микроскопия и содержание загрязняющих веществ, среди прочего (Rodrigues et al., 2013; Ulsen et al., 2013; Сильва и др., 2014). Следовательно, крайне важно классифицировать RA из CDW не только по их составляющим, но и по некоторым фундаментальным, но легко определяемым свойствам.
Чтобы удовлетворить потребность в категоризации RA на основе их характеристик, а не их составляющих, Silva et al. (2014) исследовали свойства почти 600 различных RA от широкого круга авторов со всего мира, установив кривую корреляции между RA, плотностью высушенной в печи и их водопоглощением, как показано на рис.11.1. Основываясь на этой кривой и на потерях при истирании в Лос-Анджелесе, авторам удалось создать новую категоризацию для RA (от A — лучший результат до D — худший результат), которая не зависит от их минералогической природы. С помощью этой новой системы классификации стало возможным соотнести характеристики заполнителей с характеристиками бетона, как указано в следующих разделах.
Рисунок 11.1. Корреляция между водопоглощением и плотностью переработанных заполнителей после высушивания в печи (Silva et al., 2014).
Производство цемента | Центр и сеть климатических технологий
Цемент — это глобальный товар, производимый на тысячах заводов. Отрасль консолидируется во всем мире, но на долю крупных международных компаний приходится лишь 30% мирового рынка. Основным и наиболее заметным рынком цемента является строительная промышленность, где он используется в различных областях, где он смешивается с водой для изготовления бетона. В большинстве современных проектов гражданского строительства, офисных зданий, квартир и жилых домов используется бетон, часто в сочетании с системами стальной арматуры.По данным UNEPTIE, во многих развитых странах рост рынка очень медленный, и цемент в больших объемах используется в основном для строительства инфраструктуры. На рынках развивающихся стран (например, Китая) темпы роста более высокие. Поскольку цементная промышленность носит одновременно глобальный и локальный характер, она сталкивается с уникальным набором проблем, которые привлекают внимание как на местном, так и на международном уровне.
На цемент приходится 83% общего потребления энергии при производстве неметаллических полезных ископаемых и 94% выбросов CO2. Энергия составляет от 20% до 40% общей стоимости производства цемента.Производство цементного клинкера из известняка и мела путем нагревания известняка до температур выше 950 ° C является основным энергоемким процессом. Портландцемент, наиболее широко используемый тип цемента, содержит 95% цементного клинкера. Большое количество электроэнергии используется для измельчения сырья и готового цемента.
В процессе производства клинкера также выделяется CO2 в качестве побочного продукта при кальцинировании известняка. Эти технологические выбросы не связаны с использованием энергии и составляют около 3,5% выбросов CO2 во всем мире и 57% общих выбросов CO2 от производства цемента.Выбросы при кальцинировании известняка нельзя уменьшить за счет мер по повышению энергоэффективности или замены топлива, но их можно уменьшить за счет производства смешанного цемента и выбора сырья.
Введение
Цемент — это глобальный товар, производимый на тысячах заводов. Промышленность консолидируется во всем мире, но на крупные международные фирмы приходится лишь 30% мирового рынка (European Commission, 1997). Основным и наиболее заметным рынком цемента является строительная промышленность, где он используется в различных областях, где он смешивается с водой для изготовления бетона.На обрабатывающую промышленность в целом приходится треть мирового потребления энергии. Прямые выбросы промышленной энергии и технологического CO2 составляют 6,7 гигатонн (Гт), что составляет около 25% от общих мировых выбросов, из которых 30% приходится на металлургическую промышленность, 27% — на неметаллические полезные ископаемые (в основном цемент) и 16% — на химическое и нефтехимическое производство (IEA, 2008). Производство цемента включает нагрев, кальцинирование и спекание смешанных и измельченных материалов для образования кликера. В результате производство цемента является третьей по величине причиной антропогенных выбросов CO2 из-за производства извести, ключевого ингредиента цемента.Следовательно, экономия энергии при производстве цемента может привести к снижению воздействия на окружающую среду. В цементной / бетонной промышленности повышение энергоэффективности и сокращение выбросов CO2 может быть достигнуто в основном с помощью двух процедур: (i) путем изменения производственных процессов и (ii) путем корректировки химического состава цемента. Производство и производственные процессы можно улучшить, изменив управление энергопотреблением и вложив средства в новое оборудование и / или модернизацию. Было продемонстрировано, что изменения в химическом составе цемента способствуют экономии энергии и сокращению выбросов CO2, но их широкому распространению пока препятствует тот факт, что разработка нового промышленного стандарта сложна и требует времени.Это, в частности, относится к цементной промышленности, которая является высоко капиталоемким и конкурентоспособным сектором с длительным экономическим сроком службы существующих предприятий, так что изменения в существующем капитале не могут быть легко осуществлены.
Наибольшие возможности для повышения энергоэффективности и сокращения выбросов CO2 могут быть достигнуты за счет улучшения процесса производства цемента. В цементной промышленности пиропроцессинг (переработка сырья в цемент при высокой температуре, например, выше 8000C) является очень распространенной технологической процедурой, на которую приходится 74% потребления энергии в мировой цементной / бетонной промышленности. Поскольку термический КПД за счет использования этой традиционной технологии пиропроцессинга в среднем немного превышает 30% (Mersmann, 2007), существуют значительные возможности для улучшений. На измельчение и помол приходится 5,8% энергопотребления цемента / бетона (Choate, 2003). Эти операции имеют энергоэффективность от 6 до 25%, а также предоставляют большие возможности для экономии энергии.На следующем рисунке представлен процесс производства цемента.
Потенциальные возможности для повышения энергоэффективности и снижения выбросов CO2 при производстве сырья и производстве бетона меньше, чем при производстве цемента. Например, выбросы CO2 во время транспортировки можно уменьшить, заменив дизельное топливо биодизелем. Обычно повышение энергоэффективности пропорционально сокращает выбросы CO2, образующегося при сжигании ископаемого топлива и производстве электроэнергии.Однако следует отметить, что сокращение выбросов CO2 от производства цемента на процент, пропорциональный повышению энергоэффективности, невозможно. Более половины выбросов CO2, связанных с цементом / бетоном, является результатом химических реакций, необходимых для преобразования сырья, а не результатом энергии, необходимой для этих реакций. Например, если топливо с почти нулевым выбросом CO2 (например, ядерная энергия, биомасса) использовалось для всех потребностей в энергии пиропроцессинга, то выбросы CO2 можно было бы сократить на 54%.
Еще один способ сократить выбросы — заменить ископаемое топливо отходами или биомассой. Цементные печи хорошо подходят для сжигания отходов из-за их высокой температуры процесса, а также из-за того, что клинкерный продукт и известняковое сырье действуют как газоочистители. Использованные шины, древесина, пластмассы, химикаты и другие виды отходов сжигаются в цементных печах в больших количествах. Заводы в Бельгии, Франции, Германии, Нидерландах и Швейцарии достигли среднего уровня замещения от 35% до более 70%.Некоторые отдельные заводы даже достигли 100% -ной замены с использованием соответствующих отходов. Однако очень высокие показатели замещения могут быть достигнуты только при наличии специальной системы предварительной обработки и наблюдения. Например, твердые бытовые отходы необходимо предварительно обработать для получения однородной теплотворной способности и характеристик корма. Цементная промышленность в Соединенных Штатах сжигает 53 миллиона изношенных шин в год, что составляет 41% от всех сгоревших шин, что эквивалентно 0,39 Мт или 15 ПДж.Около 50 миллионов шин, или 20% от общего количества, по-прежнему используются на свалках. Еще один потенциальный источник энергии — ковры: около 100 ПДж в год выбрасываются на свалки — вместо этого их можно сжигать в цементных печах. Хотя эти альтернативные материалы широко используются, их использование все еще вызывает споры, поскольку цементные печи не подлежат такому же жесткому контролю выбросов, как установки для сжигания отходов. Согласно статистике МЭА, цементная промышленность в странах ОЭСР в 2005 году использовала 1,6 млн тнэ горючих возобновляемых источников энергии и отходов, половина из которых — промышленные отходы, а половина — древесные отходы (Taylor, 2006).Во всем мире сектор потребил 2,7 Мтнэ биомассы и 0,8 Мтнэ отходов. Это составляет менее 2% от общего расхода топлива в этом секторе. С технической точки зрения использование альтернативных видов топлива может быть увеличено с 24 до 48 Мтнэ, хотя между регионами будут различия из-за разной доступности таких видов топлива. Это приведет к сокращению выбросов CO2 в диапазоне от 100 до 200 млн тонн в год.
Еще один способ снизить энергетические и технологические выбросы при производстве цемента — это смешивание цементов с увеличенными долями альтернативного (не клинкерного) сырья, такого как вулканический пепел, гранулированный доменный шлак от производства чугуна или летучая зола от сжигания угля. выработка энергии.Использование таких смешанных цементов широко варьируется от страны к стране. Он высокий в континентальной Европе, но низкий в США и Великобритании. В США и Китае другие заменители клинкера добавляют непосредственно на стадии изготовления бетона. В долгосрочной перспективе цементу не хватает жизнеспособной безуглеродной альтернативы, и сценарии МЭА предполагают сильную зависимость от цементных печей для улавливания и хранения углерода (CCS) с кислородным топливом (IEA, 2008).
Осуществимость технологий и производственные потребности
В процессе пиропроцессинга цемента важно помнить, что отходы горят и горят при разных температурах и в разных условиях.Следовательно, твердые топливные отходы необходимо вводить в печь таким образом, чтобы они не влияли существенно на температурный профиль и химические реакции в процессе пиропроцессинга в целом. Иногда необходимо добавлять твердые отходы через люк или клапан в оболочке печи, что представляет собой техническую проблему и частично компенсирует повышение эффективности и сокращение выбросов CO2. Наконец, получение и обращение с альтернативным или отработанным топливом может вызвать техническую ответственность и политические проблемы.Компании-производители цемента не хотят, чтобы их называли обработчиками опасных отходов, и окружающие сообщества могут беспокоиться о транспортировке и обращении с опасными отходами на ближайшем цементном заводе.
Кроме того, смешанные цементы открывают большие возможности для энергосбережения и сокращения выбросов, но их использование во многих случаях потребует пересмотра строительных стандартов, кодексов и практик.
Из этапов цепочки производства цемента операции измельчения и помола достаточно энергоэффективны.Как упоминалось ранее, типичные системы обычно работают с энергоэффективностью на месте от 6 до 25% (Министерство энергетики США, 2003). Повышение энергоэффективности измельчения и измельчения можно повысить за счет использования современных систем мельниц, которые включают несколько единиц технологического оборудования с двухвалковыми прессами высокого давления, трубными мельницами, шаровыми мельницами и обычными или высокоэффективными сепараторами (IEA, 2009).
Состояние технологии и ее будущий рыночный потенциал
Основной потенциал в снижении энергопотребления и выбросов CO2 при производстве цемента / бетона заключается в улучшении пиропроцессинга цемента.Пиропереработка превращает сырую смесь в клинкер. В настоящее время около 78% производства цемента в Европе приходится на сухие печи, еще 16% производства приходится на полусухие и полумокрые печи, а оставшаяся часть европейского производства, около 6%, приходится на мокрые печи. технологические печи. Как правило, ожидается, что при обновлении печи мокрого процесса, работающие в Европе, будут преобразованы в системы обжига сухого процесса, как и системы обжиговых печей полусухого и полувлажного процесса. В среднем системы пиропереработки в ЕС и США работают с термическим КПД ниже 35%, что довольно мало.В развивающихся странах процент еще ниже (Карстенсен, без даты). Эти улучшения процесса будут происходить за счет лучшего управления энергопотреблением, модернизации существующего оборудования (например, замена мокрых печей, модернизация до подогревателей и прекальцинаторов), внедрения новых технологий пиропроцессинга (например, систем с псевдоожиженным слоем) и, в более долгосрочной перспективе, выполнения НИОКР, необходимых для разработки новых концепции процессов производства цемента.
Япония является ведущей страной в области энергоэффективности в цементном секторе.Европа (в среднем 4,1 ГДж / т цемента) не могла конкурировать с Японией (3,1 ГДж / т), но многие другие части мира демонстрируют гораздо более высокие модели энергопотребления, например средний уровень энергопотребления в США (5,3 ГДж / т) или в Китае намного выше, чем в среднем по Европе (Worrell et al., 2004).
Типичные балансы энергии для основных систем пиропроцессинга показаны ниже. Эти балансы показывают, где происходят потери энергии и, таким образом, представляют возможность для повышения энергоэффективности и снижения выбросов CO2 на основе топлива.В частности, таблица показывает, что можно добиться значительных улучшений, если перейти от мокрого цементирования к сухому. Отдельные области использования энергии (например, разгрузка клинкера, оболочка печи и т. Д.) В таблице показывают площадь и величину возможностей, доступных для управления потерями энергии путем улучшения конкретного оборудования или методов.
Посредством энергетических аудитов, включая тестирование производительности печной системы и расчет баланса массы и тепла, можно определить конкретные возможности повышения энергоэффективности и снижения выбросов CO2.Энергетический аудит производства цемента должен как минимум рассматривать использование энергии и рекомендовать возможные действия, такие как:
- Меньшие потери газа на выходе из печи
- установить устройства, обеспечивающие лучшую кондуктивную теплопередачу от газов к материалам, например цепи печи
- работают при оптимальном уровне кислорода (контроль подачи воздуха для горения)
- Оптимизация формы пламени и температуры горелки
- увеличить или увеличить мощность подогревателя
- Более низкие возможности поглощения влаги для сырьевой муки и топлива: устранение необходимости испарения адсорбированной воды
- Уменьшение количества пыли в выхлопных газах за счет сведения к минимуму турбулентности газа: пыль уносит энергию от печи, где она улавливается пылесборниками; пыль перерабатывается в сырьевую муку и подается в печь, где ее повторно нагревают
- Более низкая температура на выходе клинкера, сохранение большего количества тепла в системе пиропереработки
- Нижняя температура дымовой трубы охладителя клинкера
- рециркуляция избытка охлаждающего воздуха
- регенерировать более холодный воздух, используя его для сушки сырья и топлива или подогрева топлива или воздуха
- Снижение потерь на излучение в печи за счет использования правильной смеси и более энергоэффективных огнеупоров для контроля температурных зон печи
- Нижняя утечка холодного воздуха
- закройте ненужные отверстия
- обеспечивает более энергоэффективные уплотнения
- работают с максимально высокой температурой первичного воздуха
- Оптимизируйте работу печи, чтобы избежать сбоев.
Производство цемента мокрым способом включает смешивание сырья (известняк и глина или суглинок) с водой с целью получения суспензии. Далее в процессе из гомогенизированной смеси испаряется вода, и этот этап производства требует значительного количества энергии. Сырьевая мука (высушенный шлам) подвергается воздействию высоких температур во вращающейся печи, где происходит реакция прокаливания (ее конечными продуктами являются известь и CO2). На известь также влияют температуры от 1400 до 1450 ° C.Эта реакция, называемая спеканием, приводит к образованию клинкера. Заключительный этап производства цемента — тонкое измельчение клинкера и смешивание вещества с минеральными компонентами, такими как шлак, летучая зола или гипс.
В случае производства сухого цемента сырье смешивается без воды, поэтому процесс испарения можно не проводить. Последняя технология может снизить потребление энергии от «мокрого» до «сухого» процесса более чем на 50%.
Существующие технологии в цементной промышленности можно модернизировать несколькими способами.В Таблице 26-3 показано, основанное на данных цементных заводов США, влияние возможных мер по модернизации, таких как переход от мокрых процессов к сухим и в рамках последней категории, влияние использования технологий подогревателя и прекальцинатора. Таблица показывает, что, если все заводы в США модернизируют свою пиропроцессинг до уровня лучших заводов США (т. Е. Система сухого процесса с подогревателем с технологией прекальцинатора), промышленность снизит потребление энергии на 30% до примерно 3 407 650 Джоулей на тонну цементировать и сократить выбросы CO2 на 13% до 75.3 млн т / год.
Что касается новых технологий в цементном секторе, несколько технологий проходят испытания и демонстрируются, например, печи с псевдоожиженным слоем. С середины 1990-х годов было разработано несколько опытных образцов крупномасштабных печей с псевдоожиженным слоем (200 т / день), которые продемонстрировали значительную экономию энергии. Например, по оценкам, полномасштабная система с псевдоожиженным слоем (3000 тонн / день) будет столь же эффективна, как самая передовая обжиговая печь в США, использующая подогреватель и прекальцинатор, и на 37% эффективнее, чем средняя установка в США.Для систем с псевдоожиженным слоем требуемые капитальные затраты примерно на 12% ниже, чем у современного цементного завода, а их эксплуатационные расходы составляют около 75% от эксплуатационных расходов современного цементного завода (Министерство энергетики США, 2003). Однако по сравнению со старыми, полностью капитализированными установками на базе печей, системы с псевдоожиженным слоем относительно дороги, поэтому их, вероятно, можно будет рассматривать только для будущего увеличения мощности. Еще одним препятствием для внедрения систем с псевдоожиженным слоем является нежелание вкладывать средства в такие большие капитальные затраты, поскольку системы были продемонстрированы только на небольших предприятиях.
Цементные заводы, учитывая их крупномасштабный спрос на промышленную тепловую энергию, предлагают возможности для комбинированного производства электроэнергии и / или пара, особенно если система когенерации является частью первоначального проекта завода. Это может значительно повысить общую энергоэффективность некоторых производственных операций. В настоящее время пять заводов по производству цемента вырабатывают электроэнергию на месте за счет когенерации (Министерство энергетики США, 2003 г.). Более того, использование отработанного тепла в системах теплообмена подогревателя обычно более энергоэффективно, чем когенерация электроэнергии с присущей ему низкой эффективностью преобразования тепловой энергии в электрическую (обычно для производства 1 кВтч требуется около 10 481 Джоулей).Хотя совместное производство пара на цементном заводе возможно, цементные заводы обычно требуют небольшого количества пара и расположены в изолированных районах, где рынки для избыточного производства пара часто недоступны.
Вклад технологий в экономическое развитие (включая поддержку энергетического рынка)
Важным преимуществом повышения энергоэффективности в цементной промышленности могло бы стать снижение затрат на электроэнергию. В целом, в цементной промышленности ЕС расходы на электроэнергию составляют около 40% от общих производственных затрат, в то время как европейские технологии производства цемента являются одними из самых энергоэффективных в мире.С 1970-х годов в Европе энергия, необходимая для производства цемента, упала примерно на 30%, а возможности для дальнейших улучшений стали довольно небольшими. Однако в других частях мира по-прежнему возможна более значительная экономия на энергозатратах.
В производстве цемента рентабельное повышение эффективности от 10% до 20% уже возможно при использовании коммерчески доступных технологий. Энергоемкость большинства промышленных процессов как минимум на 50% выше теоретического минимума, определяемого основными законами термодинамики.Энергоэффективность обычно ниже в регионах с низкими ценами на энергию. Комплексные технологии для двигателей и паровых систем позволят повысить эффективность во всех отраслях промышленности с типичной экономией энергии в диапазоне от 15% до 30%. Срок окупаемости может составлять всего два года, а в лучшем случае финансовая экономия в течение срока службы улучшенных систем может достигать 30–50%. В тех процессах, где эффективность близка к практическому максимуму, инновации в материалах и процессах позволят добиться еще большего выигрыша (IEA, 2008).
Климат
При производстве цемента выделяется CO2, так как для сжигания сырья и придания клинкеру уникальных свойств требуются очень высокие температуры. CO2 образуется из трех независимых источников: декарбонизация известняка в печи (около 525 кг CO2 на тонну клинкера), сжигание топлива в печи (около 335 кг CO2 на тонну цемента) и использование электроэнергии (около 50 кг. кг CO2 на тонну цемента). Существует три основных меры, с помощью которых цементная промышленность может сократить прямые выбросы CO2 в ближайшем будущем:
- Повышение энергоэффективности (все еще возможно максимум 2%),
- Снижение соотношения клинкер / цемент (введение полезных промышленных побочных продуктов), и
- Увеличение использования отходов в качестве альтернативного топлива (национальные инициативы, адекватное национальное выполнение определенных директив, касающихся конкретных отходов).
На основании анализа IEA (2008) для смешанных цементов в целом потенциал экономии в этом случае составляет от 300 до 450 млн тонн CO2 к 2050 году. Основные подходы к этому заключаются в использовании:
- Доменный шлак, охлажденный не воздухом, а водой. Около половины всего доменного шлака уже используется для производства цемента, где шлак охлаждается водой и где расстояния транспортировки и затраты приемлемы. Если бы был использован весь доменный шлак, это привело бы к сокращению выбросов CO2 примерно на 100 млн тонн CO2.
- Летучая зола от угольных электростанций. Но содержание углерода в летучей золе может повлиять на время схватывания бетона, которое определяет качество цемента. Для использования в качестве заменителя клинкера высокоуглеродистая летучая зола должна быть улучшена. Технологии для этого только появляются. Специальные методы измельчения также изучаются как способ увеличения скорости реакции летучей золы, что позволяет повысить содержание летучей золы в цементе до 70% по сравнению с максимальным значением 30% в настоящее время (Justnes et al., 2005). Китай и Индия могут значительно увеличить использование летучей золы.Если бы 50% всей летучей золы, которая в настоящее время отправляется на свалки, можно было бы использовать, это привело бы к сокращению выбросов CO2 примерно на 75 млн. Т.
- Стальной шлак. Процесс CemStar, который использует 15% -ную загрузку стального шлака с воздушным охлаждением в смеси сырья вращающейся печи, был разработан и успешно применяется в Соединенных Штатах, что привело к снижению выбросов CO2 примерно на 0,47 т / т добавленного стального шлака ( Yates et al., 2004). В Китае насчитывается около 30 сталелитейных цементных заводов с совокупной годовой производительностью 4.8 млн т. Однако качество стального шлака варьируется, и его трудно перерабатывать, что ограничивает его использование. Если бы общий мировой ресурс сталеплавильного шлака конвертерных печей и ЭДП в размере от 100 до 200 млн тонн в год был использован таким образом, потенциал сокращения выбросов CO2 составил бы от 50 до 100 млн тонн в год. Для подтверждения жизнеспособности этого варианта необходим дальнейший анализ. Другие материалы, которые могут быть использованы в большей степени в качестве заменителей клинкера, включают вулканический пепел, молотый известняк и битое стекло. Такие подходы могли бы облегчить проблемы доступности заменителей клинкера и, возможно, проложить путь к 50% сокращению энергопотребления и выбросов CO2.В долгосрочной перспективе могут быть разработаны новые типы цемента, в которых известняк не используется в качестве основного ресурса. Эти новые виды называются синтетическими пуццоланами. Технологическая осуществимость, экономические и энергетические эффекты таких альтернативных цементов остаются спекулятивными.
- Смешанные цементы предлагают большие возможности для энергосбережения и сокращения выбросов, но их использование во многих случаях потребует пересмотра строительных стандартов, кодексов и практик. В целом потенциал экономии для смешанных цементов составляет от 300 до 450 млн тонн CO2 к 2050 году.Скорость обучения для цементных печей CCS при текущей стоимости 200 долларов США за тонну CO2 составляет около 5%, в то время как целевой показатель затрат на коммерциализацию в долларах США составляет 75 долларов США.
Для расчета этих сокращений выбросов парниковых газов рекомендуется применять утвержденные методологии для консолидированной методологии увеличения смеси при производстве цемента, методологии сокращения выбросов парниковых газов за счет рекуперации отходящего тепла и использования для выработки электроэнергии на цементных заводах, перехода на ископаемое топливо, энергоэффективности и мер по замене топлива для промышленных объектов, сокращение выбросов за счет частичной замены ископаемых видов топлива с альтернативными видами топлива или менее углеродоемкими видами топлива в проекте по производству цемента (крупномасштабные мероприятия), который был разработан в рамках Механизма чистого развития Киотского протокола РКИК ООН (МЧР).Эта методология помогает определить базовый уровень выбросов парниковых газов в отсутствие проекта (т. Е. При обычном ведении бизнеса), как можно рассчитать сокращения выбросов ниже этого базового уровня и как можно отслеживать эти сокращения. Общую информацию о том, как применять методологии CDM для учета парниковых газов, можно найти здесь.
Финансовые потребности и затраты
Прогнозируется, что мировой спрос на цемент будет расти на 4,7% ежегодно до 2,8 млрд метрических тонн в 2010 году. Китай, который уже является крупнейшим рынком цемента в мире, продемонстрирует наибольший рост общего объема проданного цемента.Другие развивающиеся части Азиатско-Тихоокеанского региона и Восточной Европы, а также ряд стран в регионах Африки / Ближнего Востока и Латинской Америки также продемонстрируют прирост рынка цемента выше среднего, чему способствуют хорошие перспективы строительства. Ожидается, что Вьетнам, Таиланд, Украина, Турция и Индонезия также продемонстрируют значительный рост в процентном отношении. Рыночный рост будет менее устойчивым в развитых регионах США, Японии и Западной Европы, при этом основная часть роста спроса на цемент до 2010 года будет приходиться на ремонтно-эксплуатационное строительство.Однако увеличение расходов на строительство в Германии и Японии после продолжительного периода спада поможет поддержать общий рост развитых мировых рынков.
Цементная промышленность приложила значительные усилия для внедрения инновационных технологий в производство цемента. В последние годы были потрачены значительные ресурсы на изучение новых и, надеюсь, не вызывающих споров и экологически чистых технологий. К сожалению, многие такие технологии обладают низкой производительностью (некоторые все еще находятся в стадии разработки), технически сложны и в настоящее время недоступны для многих развивающихся стран.При сравнении современных технологий с точки зрения устойчивости, пригодности, производительности, надежности, рентабельности, патентных ограничений (доступности) и требований к компетентности можно сделать вывод, что, по крайней мере, в краткосрочной перспективе цементная промышленность будет базироваться на на мельницах пирообработки и помола.
Как описано выше, наиболее традиционный способ производства цемента — в печах. Хотя в развитом мире это стандартная процедура, в развивающемся мире мы можем столкнуться с финансовыми требованиями, которые нелегко удовлетворить.Высокотемпературные печи для обжига цемента широко распространены и доступны в большинстве развивающихся стран и могут представлять собой доступную, экологически безопасную и устойчивую альтернативу обработке. Выбор мельницы будет варьироваться на разных предприятиях из-за ряда факторов. Хотя энергопотребление (и, следовательно, затраты на энергию) на трубных станах выше, они имеют более низкие эксплуатационные расходы и затраты на техническое обслуживание, чем другие типы станов. Инвестиционные затраты трудно сравнивать в общих чертах, потому что ограничения, характерные для конкретного объекта, играют важную роль.Факторы, не связанные с затратами, которые влияют на инвестиционные решения, включают содержание влаги в сырье, вертикальные валковые мельницы могут как сушить, так и измельчать материалы, и поэтому они наиболее подходят для сырья с более высоким содержанием влаги, в то время как валковые прессы и горизонтальные валковые мельницы могут потребовать отдельная сушилка.
В 1999 году десять ведущих цементных компаний, представляющих примерно одну треть мирового производства цемента, добровольно приступили к реализации того, что стало Инициативой устойчивого развития цемента (CSI), программой под руководством членов Всемирного делового совета по устойчивому развитию (WBCSD ).Его цель — найти для отрасли новые способы уменьшения воздействия на окружающую среду, понимания потенциала ее социального вклада и расширения взаимодействия с заинтересованными сторонами.
Список литературы
- Американская ассоциация угольной золы (ACAA), 2001. Обзор продуктов сжигания угля.
- Чоат, W., 2003. Энергия и возможности сокращения выбросов в цементной промышленности. Министерство энергетики США.
- Европейская комиссия, 1997. 4-я рамочная программа исследований и технологического развития (RTD), проект ATLAS.
- МЭА, 2008. Перспективы энергетических технологий — сценарии и стратегии до 2050 года. Международное энергетическое агентство.
- МЭА, WBSCD, 2009. Дорожная карта цементных технологий на 2009 год — Сокращение выбросов углерода до 2050 года. Международное энергетическое агентство.
- Джастнес, Х., Эльфгрен, Л. и Ронин, В., 2005. Механизм действия энергетически модифицированного цемента по сравнению с соответствующей смешанной цементной смесью, исследования цемента и бетона, 35 (2), стр. 315-323.
- Karstensen, K.H. (без даты).Звуковое уничтожение устаревших пестицидов в цементных печах в развивающихся странах, Фонд научных и промышленных исследований (SINTEF).
- Мерсманн, М., 2007. Технология пиропроцесса. Отчет о технической конференции по цементной промышленности, IEEE, стр. 90-102.
- Перри, Курт Э., 1986. Энергия и возможности сокращения выбросов для цементной промышленности — Вращающаяся цементная печь, Chemical Publishing Co., Inc., Нью-Йорк, стр. 107
- Scalon, J., 1992. Добавка минералов, сборник ACI 22.
- Тейлор, М. 2006. Энергоэффективность и выбросы CO2 в мировой цементной промышленности. Документ подготовлен для семинара IEA-WBCSD, Международное энергетическое агентство.
- Министерство энергетики США, 2003 г. Энергетика и возможности сокращения выбросов для цементной промышленности, Вашингтон, округ Колумбия, США.
- Уоррелл, Э., Прайс, Л. и Галицкий, К., 2004. Новые энергоэффективные технологии в промышленности: тематические исследования отдельных технологий, Nr. LBNL-54828: Департамент анализа энергии, Отдел экологических энергетических технологий, Национальная лаборатория Эрнеста Орландо Лоуренса в Беркли, Калифорнийский университет, Беркли, Калифорния 94720.
- Йейтс, Дж. Р., Перкинс, Д. и Санкаранараянан, Р., 2004. Процесс и технология Cemstar для снижения парниковых газов и других выбросов при увеличении производства цемента, Хэтч, Канада.
Достижения в технологии бетона | Agg-Net
Использование достижений в бетонных технологиях для улучшения решений по восстановлению смеси
Стив Кромптон, национальный технический директор, CEMEX UK Materials
Товарный бетон впервые был использован почти 100 лет назад на строительной площадке в Балтиморе, США, а во многих развитых странах сейчас на его долю приходится более половины всего цемента, используемого в строительстве.Ежегодный объем производства бетона во всем мире составляет 4 миллиарда кубических метров, поэтому бетон является наиболее широко используемым строительным материалом в мире благодаря уникальному сочетанию универсальности, экономичности и долговечности.
Хотя основная концепция продукта осталась неизменной, современные бетоны мало похожи на те, которые впервые были произведены в начале 20 века. Замечательные разработки в области технологии цементных материалов, минеральных добавок и добавок, в сочетании с достижениями в методах производства, привели к появлению широкого спектра высокоэффективных бетонов, которые могут обеспечить рентабельные и экологически безопасные решения для самых требовательных областей применения.
Требования клиентов, конкурирующие технологии и растущее стремление к экологически безопасным методам строительства усилили давление на отрасль, заставляя ее внедрять новые и инновационные способы удовлетворения этих требований. Промышленность отреагировала тем, что переместила инновации в бетонных технологиях из исследовательских лабораторий в поле, и ассортимент доступных в настоящее время бетонов больше, чем когда-либо в истории отрасли.
Однако претворить исследовательские идеи в жизнь непросто.Скривенер и Киркпатрик (1) выделили три основных препятствия на пути внедрения инноваций в бетонную промышленность:
- Конструктивная безопасность — Необходимый расчетный срок службы 100 лет или более может привести к консервативному подходу к принятию новых идей, чтобы избежать последствий отказа.
- База эмпирических знаний — Отсутствие знаний о физических и химических процессах, которые определяют характеристики вяжущих материалов на макроскопическом уровне, что приводит к необходимости итерационных и полномасштабных испытаний.
- Рыночная ниша и критическая масса. Успех бетона как строительного материала во многом основан на его дешевизне в производстве. Однако это возможно только из-за экономии на масштабе, особенно при производстве цемента. Требования к нише меньшего масштаба могут быстро увеличить затраты, сводя на нет одно из фундаментальных преимуществ продукта.
Несмотря на эти препятствия на пути внедрения, были достигнуты заметные успехи в применении передовых технологий в производстве товарного бетона с такими разработками, как высокопрочный бетон, фибробетон, использование самоуплотняющегося бетона и широкое распространение использование высокоэффективных добавок и добавок для изменения свойств бетона.
В этой статье рассматриваются некоторые ключевые разработки в технологии производства бетона, которые привели к изменениям в конструкции и производстве товарного бетона за последние 30 лет, а также рассматриваются некоторые текущие исследования, которые могут в дальнейшем повлиять на характер отрасли.
ЦЕМЕНТНАЯ ТЕХНОЛОГИЯ
Достижения в технологии производства цемента привели к большей стабильности и улучшенным характеристикам традиционных цементов. Произошли значительные изменения в использовании альтернативных видов топлива, которые снижают воздействие на окружающую среду производства цемента, которое остается энергоемким процессом, который по самой природе химических реакций производит CO2.Тем не менее, цементная промышленность добилась успеха в сокращении количества CO2, выделяемого во время производства, и часто приводимая статистика о том, что каждая тонна произведенного цемента выделяет эквивалентный вес CO2, больше не соответствует действительности, поскольку многие производители заявляют, что снизили выброс CO2 на 30% и более.
За последние 30 лет произошло резкое увеличение доступности и использования дополнительных вяжущих материалов. В частности, преимущества, вытекающие из следующих материалов, привели к их широкому распространению:
Шлак доменный гранулированный
Измельченный гранулированный доменный шлак (ggbs) является побочным продуктом производства чугуна и образуется при быстром охлаждении расплавленного доменного шлака.Вяжущие свойства ggbs известны давно (свидетельства его первого использования датируются более 80 лет), и его использование широко распространено в ряде стран по всему миру.
Его можно перемалывать с цементным клинкером для производства цемента с заводскими смесями, и этот подход распространен в Европе, хотя в Великобритании ggbs обычно добавляют в бетономешалку для получения эквивалентной комбинации цемента.
Обычно ggbs используется для замены 50% компонента CEM I в смеси, хотя в специализированных приложениях его можно использовать при уровнях замещения до 90%.
Значительные улучшения устойчивости к атаке хлоридов достигаются при использовании ggbs при уровнях замещения, превышающих 40%. Его использование также улучшает стойкость бетона к сульфатному воздействию, что признано британскими стандартами, где рекомендуется использовать высокие уровни замены ggbs для наиболее серьезных категорий химического воздействия.
Использование ggbs также снижает риск вредной щелочно-кремнеземной реакции (ASR), и снова это признано в национальных руководящих документах, которые поощряют использование ggbs там, где есть потенциал для ASR.
Еще одним преимуществом ggbs является более низкая теплота гидратации, что делает его популярным в массовых конструкциях для уменьшения проблем, связанных с проявлением высоких температур.
Неудивительно, что, учитывая потенциальные преимущества использования ggbs, наблюдается устойчивый рост его использования в товарном бетоне, хотя при использовании материала для производителя есть последствия:
- Требуется дополнительная емкость хранения.
- Дополнительные требования по контролю качества для расширенного ассортимента смесей.
- Небольшое увеличение содержания цемента, когда требуется эквивалентная 28-дневная прочность.
- Увеличенное время схватывания, особенно в холодную погоду, может привести к повышенному кровотечению, хотя это можно контролировать с помощью добавок и изменения состава смеси.
В общем, использование ggbs не представляет особых проблем для производителя товарного бетона и является наиболее часто используемым дополнительным вяжущим материалом в Великобритании.
Зола пылевидная
Зола пылевидного топлива (PFA) является побочным продуктом при производстве электроэнергии на угольных электростанциях, и пуццолановая реакционная способность материала хорошо задокументирована при использовании в сочетании с портландцементами.
PFA может быть перемолот с цементным клинкером для производства цемента заводского смешивания или может быть добавлен в бетономешалку для получения эквивалентной комбинации цемента. Оба метода широко используются в Великобритании.
PFA обычно используется с более низким уровнем замещения, чем ggbs, обычно около 30%, хотя иногда для конкретных приложений используются более высокие уровни.
Было показано, что использование PFA улучшает долговечность бетона (2) за счет уменьшения проникновения хлоридов, улучшения сульфатостойкости и минимизации риска вредного ASR.Он также может улучшить свежие свойства бетона с пониженным содержанием воды, что приведет к меньшему просачиванию и улучшенным характеристикам текучести.
Использование PFA продолжало расти, хотя доступность материала в течение длительного времени ограничивала его рост по сравнению с ggbs.
С точки зрения товарного бетона использование PFA имеет некоторые последствия:
- Требуется дополнительная емкость для хранения и необходимость в усиленной аэрации силосов для обработки более мелкого PFA по сравнению с цементом или ggbs.
- Дополнительные требования по контролю качества для расширенного ассортимента смесей.
- Увеличение содержания цемента там, где требуется эквивалентная 28-дневная прочность. Эти дополнительные увеличения несколько больше, чем при использовании ggbs, и могут достигать 40 кг / м3.
Microsilica
Microsilica является побочным продуктом производства кремния и ферросилиция. Это очень мелкий, высокореакционный пуццолан с высоким содержанием SiO2, который значительно снижает пористость бетона.
Microsilica обычно используется в качестве добавки для улучшения свойств высокоэффективных бетонов и используется при дозах добавки от 5 до 20% от веса цемента.
Было показано, чтоMicrosilica улучшает долговечность, сопротивление истиранию и прочностные характеристики бетона, но этот материал значительно дороже, чем цемент, и его использование в значительной степени ограничивается специальными применениями или высокопрочными бетонами (обычно> 80 Н / мм2).
Метакаолин
Метакаолин производится путем прокаливания каолина при температуре 700–900 ° C для получения высокореактивного пуццолана при смешивании с CEM I.Обычно он используется аналогично микрокремнезему, то есть в качестве добавки (5–15% от веса цемента) для производства высококачественного бетона.
Ограниченная доступность и практический опыт применения метакаолина привели к более низкому уровню его использования по сравнению с другими минеральными добавками, такими как ggbs, PFA и микродиоксид кремния. Тем не менее, данные исследований показывают, что уровни эффективности аналогичны тем, которые наблюдаются при использовании микрокремнезема.
Сводка
Значительные исследования и полевой опыт показали, что использование минеральных добавок улучшает характеристики бетона за счет улучшения ряда ключевых свойств.Это признано британскими и европейскими стандартами, и дизайнеры все чаще определяют использование таких материалов. Промышленность товарного бетона отреагировала тем, что сделала такие материалы широко доступными, и, по оценкам, 75% всех товарных бетонов теперь содержат минеральные добавки.
ТЕХНОЛОГИЯ ПРИМЕСЕЙ
Возможно, наиболее значительный прогресс в технологии бетона был достигнут в области добавок, что позволило разработать ряд высокоэффективных бетонов, которые позволили проектировщикам в полной мере использовать преимущества материала.Крупные компании-производители добавок вкладывают значительные средства в исследования и разработки, и за последние 30 лет значительно увеличился ассортимент добавок, доступных как для производителя цемента, так и для производителя товарного бетона:
Водоредуцирующие добавки
Это наиболее часто используемые добавки, обычно добавляемые для снижения содержания воды при сохранении удобоукладываемости и, таким образом, уменьшения содержания цемента при заданной прочности.
Редукторы высокого давления
Все чаще используется для увеличения консистенции бетона при сохранении прочности.Возможно, наиболее значительный прогресс был достигнут в этой области технологии смешения с разработкой продуктов на основе поликарбоксилатного эфира (PCE). Это привело к разработке самоуплотняющегося бетона и сыграло решающую роль в достижении еще большей прочности бетона. Добавками PCE можно управлять, чтобы изменить их влияние на важные свойства бетона, такие как когезия, скорость набора прочности, консистенция и сохранение осадки.
Модификаторы вязкости
Модификаторы вязкости были разработаны для поддержания когезии при очень высоких значениях консистенции и обычно используются при производстве самоуплотняющегося бетона.
Шлифовальные добавки
Шлифовальные добавки, оптимизирующие процесс производства цемента и снижающие потребление энергии, теперь стали обычным явлением наряду с химическими веществами, улучшающими прочностные характеристики цемента.
Добавки для компенсации усадки
Этот набор добавок снижает внутреннюю усадку бетона, которая является неизбежным результатом процесса гидратации. Использование этих добавок особенно полезно при строительстве бетонных полов, где они позволяют значительно увеличить расстояние между швами.В сочетании с другими технологическими разработками, такими как стальная фибра, они могут даже использоваться для производства «бесшовных» полов.
Ингибиторы коррозии
Дополнительную стойкость арматуры к коррозии можно получить путем введения в бетон ингибиторов коррозии, и такие добавки часто используются в критических проектах.
Пигменты
Пигментыбывают самых разных цветов и дают дизайнерам художественную лицензию, позволяя им использовать бетон по-разному.
Добавки для гидроизоляции
Блокаторы пор все чаще используются при проектировании и строительстве водонепроницаемых конструкций, и в этой области постоянно ведутся разработки для улучшения характеристик таких добавок, особенно там, где бетон подвергается внешнему давлению воды.
Приведенный выше список ни в коем случае не является исчерпывающим, и другие добавки, такие как замедлители схватывания и воздухововлекающие добавки, обычно используются для изменения свойств свежего и затвердевшего бетона.
Преимущества добавок в увеличении долговечности, сокращении времени укладки, сокращении затрат и улучшении показателей устойчивости бетона широко признаны, и рост использования добавок отражает это, поскольку объем продаж в Великобритании утроился за последние 15 лет. , как показано на рисунке 1.
В производстве товарного бетона в настоящее время производство бетона без добавок является скорее исключением, чем правилом, и все большая доля включает высокодисперсные водоредуцирующие добавки (HRWRA), что также отражено на рисунке 1.
ВОЛОКНА
Использование волокон в бетоне и растворах не ново, о чем свидетельствует использование волокон животного происхождения в некоторых из самых ранних зарегистрированных бетонов. Как и в случае с добавками, произошли значительные изменения в типах, доступности и характеристиках волокон, и на рынке доступны три основных типа волокна:
Стальная фибра
Стальные волокна производятся различных форм и размеров, и хотя обычно они изготавливаются из низкоуглеродистой стали, они доступны из нержавеющей стали и в оцинкованной форме.Обычно их добавляют при дозировке от 15 до 50 кг / м3 в зависимости от типа волокна и желаемых свойств бетона.
Стальная фибра может повысить ударную вязкость и пластичность бетона и широко используется в промышленных покрытиях во всем мире. Совсем недавно были разработаны методы строительства из композитных материалов, которые позволяют стальной фибре заменять традиционную конструкционную арматуру в некоторых областях применения.
Стальной фибробетон можно приобрести на большинстве заводов по производству товарных смесей по всей Великобритании, хотя может потребоваться уведомление за несколько дней, чтобы гарантировать наличие указанного волокна на складе на заводе.Важно убедиться, что волокна полностью диспергированы в бетоне, и обычно для стального фибробетона также используется водоредуцирующая добавка с высоким содержанием воды для улучшения консистенции бетона и облегчения тщательного перемешивания.
Полипропиленовые волокна
Полипропиленовые волокна обычно вводятся с гораздо более низкими дозами, чем стальные волокна, обычно менее 1 кг / м3, и в основном используются для изменения пластических свойств бетона, чтобы минимизировать проблемы пластического растрескивания.Они также способствуют повышению стойкости к истиранию, повышению ударопрочности и устойчивости к растрескиванию при пожарах.
Использование полипропиленовых волокон неуклонно растет с 1980-х годов, и по оценкам, более 5% всего товарного бетона в Великобритании в настоящее время содержат такие волокна. С точки зрения производителя, волокна просты в обращении и легко добавляются в бетон, хотя необходимо следить за тем, чтобы учесть влияние на прочность консистенции.
Синтетические макроволокна
Синтетические макроволокна являются более поздней разработкой и обычно производятся из смесей различных органических полимеров, включая полиэтилен и полиолефины (3).Последние разработки позволили изготавливать материалы с более высоким модулем упругости с различными механизмами крепления, которые улучшают сцепление и приводят к улучшенным характеристикам этого типа волокна.
Несмотря на то, что они относительно новы в Великобритании, их пониженная дозировка (обычно 2–7 кг / м3) делает их популярными среди производителей товарного бетона, поскольку с ними легче обращаться, чем со стальными волокнами. Их использование в таких областях, как промышленные полы и настил из композитной стали, продолжает расти.
Комбинации типов волокон также могут использоваться для реализации преимуществ пластического состояния, обеспечиваемых полипропиленовыми волокнами, в сочетании с преимуществами затвердевшего состояния, которые связаны с использованием стальных или синтетических макроволокон.
УСТОЙЧИВОСТЬ
Концепция устойчивого развития стала важной темой во всех сферах строительства, и производство товарного бетона не исключение (4). Устойчивое развитие станет основным двигателем будущего развития цементных материалов, и компании все чаще будут стремиться снизить воздействие своей продукции на окружающую среду.
Устойчивость можно рассматривать как сочетание социальных, экономических и экологических воздействий, и вместе они влияют на восприятие продукта.Экологичный материал должен продемонстрировать:
- Минимальный ущерб окружающей среде (возобновляемый, нетоксичный, пригодный для вторичной переработки, биоразлагаемый и т. Д.).
- Минимальные отходы, связанные с его использованием (отходы при производстве; чрезмерный заказ; предварительная сборка за пределами объекта и т. Д.).
- Местное снабжение (при наличии на месте, поездки сведены к минимуму, что снижает вредные выбросы топлива).
- Низкие выбросы CO2 (учитываются все выбросы во время поиска, производства и жизненного цикла материала / продукта).
Кроме того, экологически чистый материал должен быть прочным, прочным, огнестойким и обеспечивать адекватную безопасность.
Промышленность товарного бетона ответила на эти вызовы:
Снижение загрязнения и выбросов
- За последние 20 лет выбросы пыли сократились на 90%
- Снижение содержания углекислого газа в воздух на 18%
- Снижение содержания диоксида серы на 46%
- 17% снижение оксидов азота
- 60% -ная экономия твердых частиц.
Увеличение использования вторичного сырья
- Цементная и бетонная промышленность Великобритании продолжает вносить свой вклад в Стратегию Великобритании по отходам, потребляя отходы, произведенные в других отраслях, и перерабатывая собственные отходы
- Цементная промышленность играет важную роль в минимизации некоторых проблем страны с удалением отходов путем переработки отдельных отходов в альтернативные виды топлива для печей
- Использование ggbs и летучей золы в бетоне и цементе увеличивается, что позволяет сократить выбросы CO2 до 45%.
Снижение отходов и повышение эффективности
- соблюдение строгого экологического законодательства
- Аккредитация ISO 14001 становится нормой
- бетонных заводов перерабатывают воду (достижимо до 65%)
- , удельное потребление энергии при производстве цементного клинкера снизилось на 30% с 1970-х годов.
Меньшая зависимость от первичных полезных ископаемых
- 1,5 миллиона тонн ГГБ и летучей золы используются в Великобритании каждый год в качестве замены цемента
- сокращение выбросов CO2 на 1.5 миллионов тонн
- сокращение потребления первичной энергии на 2 000 миллионов киловатт в час
- экономия 1,5 млн тонн карьеров
- экономит 1,5 миллиона тонн полигона.
Снижение использования первичных агрегатов
- Снижение производства первичных заполнителей на 45% с 1989–2011 гг.
- Увеличение на 94% использования переработанных и вторичных заполнителей
- К 2011 году 30% агрегатов (70 миллионов тонн) будет поступать из неосновных источников.
Отрасль осознает свою ответственность в отношении вопросов устойчивого развития и продолжает инвестировать время, деньги и ресурсы для дальнейшего улучшения своей деятельности в этой важной области. Хотя бетон вносит небольшой чистый вклад в глобальное потепление, на него приходится лишь 2,6% выбросов CO2 в Великобритании в 2006 году, он продолжает продвигать использование материалов и технологий, которые еще больше снизят его воздействие на общество (5).
МИКС ДИЗАЙН
Чтобы извлечь максимальную пользу из вышеперечисленных разработок, необходимо, чтобы технолог по бетону разработал конструкцию смеси в соответствии с требованиями специалиста, и это подчеркивается здесь путем рассмотрения трех приложений, которые были разработаны в результате достижений в области бетонных технологий:
Бетон высокопрочный
Указанная прочность бетона неуклонно растет в течение последних 30 лет.За этот период средняя прочность выросла примерно на 10 Н / мм2, и все большее количество всего бетона определяется прочностными характеристиками.
Более значительный рост наблюдается в производстве высокопрочных бетонов. В то время как C50 когда-то считался высокопрочным, теперь обычным явлением является то, что бетон C80 обычно производится, а на некоторых заводах по производству товарного бетона производятся бетоны с прочностью до C130.
Эти преимущества возможны только при тщательном выборе и сочетании сырья, а также при использовании высокодисперсных водоредуцирующих добавок в сочетании с отобранными вяжущими компонентами, такими как PFA и микрокремнезем.Теория упаковки частиц и реологическое поведение бетона становятся важными частями процесса разработки смесей в этих приложениях.
Границы высокопрочного бетона были расширены с разработкой и производством сверхвысокопрочных бетонов, где прочность может превышать 200 Н / мм2, хотя на сегодняшний день применение и производство таких материалов ограничено.
Самоуплотняющийся бетон
Самоуплотняющийся бетон (SCC) быстро развивается с тех пор, как он был впервые продемонстрирован в Японии в конце 1980-х годов.Развитие технологии добавок и лучшее понимание реологических характеристик SCC позволило производителям надежно производить материалы, которые можно размещать без вибрации, что приводит к преимуществам за счет повышения эффективности на месте, снижения воздействия на окружающую среду и улучшения качества поверхности.
Однако конструкция SCC является сложной, часто включающей несколько комбинаций порошка и примеси, чтобы гарантировать достижение желаемых свойств, и требуются дальнейшие исследования и разработки для обеспечения большей надежности конструкции смеси.
Устойчивое проектирование
Использование вторичных вяжущих компонентов является обычным явлением в промышленности, и использование таких материалов может снизить выброс CO2 в бетон до 40%.
Водоредуцирующие добавки обычно используются для снижения содержания воды и, таким образом, предоставляют возможности для удовлетворения заданных требований к прочности при более низком содержании цемента.
Использование оборотной воды и устранение отходов смыва в настоящее время является эталоном в отрасли, и более крупные производственные предприятия будут иметь установки для регенерации материалов из любого возвращенного бетона.
Использование переработанных заполнителей часто рассматривается как логический способ снижения воздействия бетона на окружающую среду. Однако использование переработанного заполнителя (RA) или переработанного заполнителя для бетона (RCA) требует тщательного рассмотрения, поскольку их использование может значительно увеличить содержание цемента.
Требуется подробное рассмотрение общих преимуществ для устойчивости от использования RA или RCA, чтобы гарантировать полное понимание воздействия на устойчивость, поскольку часто бывает, что природный заполнитель местного производства является более устойчивым решением, чем импорт переработанных материалов.
ТЕХНОЛОГИЯ ПРОИЗВОДСТВА
Основные требования для производства бетона сегодня немного отличаются от того, когда эта отрасль зародилась почти 80 лет назад — однородное смешивание цемента, заполнителей и воды для производства материала, который можно транспортировать до 2 часов и при этом использовать при строительстве. сайт.
Однако мир изменился, и развитие цементных и бетонных технологий привело к появлению все более сложных смесей, требующих все более сложных методов смешивания и контроля для удовлетворения требований современных методов строительства.
Компьютеризация, прогресс в измерении материалов и доступность передовых добавок позволяют производителю товарного бетона проектировать и производить огромное количество сложных, технически сложных бетонов, которые были просто недостижимы даже 10 лет назад.
Повышение экологической осведомленности привело к значительным изменениям в конструкции современных бетонных заводов: новые заводы были полностью закрыты, и никакие отходы никогда не покидали территорию, поскольку бетонные и водооборотные установки становятся нормой.
Снаружи современный завод по производству бетона может не сильно отличаться от построенного 60 лет назад, но технологии и сложность современного завода и производимые на нем материалы — это световые годы по сравнению с первым заводом, построенным в Великобритании в 1930 году.
ВЫВОДЫ
За последние 30 лет произошло множество инноваций в области бетонных технологий, в частности, касающихся разработки альтернативных вяжущих компонентов и еще более мощных и гибких систем добавок, способных изменять свойства свежего и затвердевшего бетона.
В последнее время акцент на экологические проблемы и концепция устойчивого развития привели к изменениям в способах производства и использования сырья для производства бетона. Увеличилось использование переработанных и альтернативных материалов, которые вместе могут снизить воздействие бетона на окружающую среду, и ожидается дальнейшее развитие в этой области.
Эти разработки были приняты промышленностью товарного бетона, и характер продукции, производимой в этой отрасли, значительно изменился.Производственные подразделения стали более сложными и имеют более широкий ассортимент цементов, добавок и заполнителей, что позволяет производить широкий спектр бетонов с высокими техническими характеристиками, разработанных для удовлетворения самых требовательных применений.
ССЫЛКИ
- SCRIVENER, K.L., and R.J. КИРКПАТРИК: «Инновации в использовании и исследования вяжущих материалов», Cement and Concrete Research 38 (2008), стр. 128-136.
- BAMFORTH, P.B .: «Повышение прочности железобетона», Технический отчет Concrete Society No.61, 2004.
- Руководство по использованию макробетона, армированного синтетическим волокном, Технический отчет № 65, 2007 г.
- Руководство по «Устойчивому проектированию и системам оценки бетона», Британская ассоциация товарного бетона, 2008 г.
- MEYER, C .: «Озеленение бетонной промышленности», Цемент и бетонные композиты, 2009.
Этот документ был представлен на 37-м ежегодном техническом симпозиуме Института технологии бетона (ИКТ) в апреле 2009 года и впоследствии опубликован в выпуске Ежегодника ИКТ за 2009/10 год.Он воспроизведен здесь с любезного разрешения ICT.
5 Лучшие устойчивые решения для производства бетона
Опережать технологические новшества означает укреплять ваше конкурентное преимущество. Вот почему мы даем вам аналитическую информацию об инновациях в обрабатывающей промышленности на основе данных. На этот раз вы познакомитесь с 5 тщательно подобранными стартапами, разрабатывающими экологически безопасные решения для производства бетона.
Глобальная тепловая карта стартапов: 5 лучших решений для производства бетона из 98
Выводы этого анализа на основе данных основаны на платформе StartUs Insights Discovery на базе больших данных и искусственного интеллекта, охватывающей 1.379 000+ стартапов и масштабных проектов по всему миру. Платформа дает вам исчерпывающий обзор новых технологий и соответствующих стартапов в определенной области всего за несколько кликов.
Глобальная тепловая карта стартапов, представленная ниже, показывает распределение 98 образцовых стартапов и масштабных проектов, которые мы проанализировали в рамках этого исследования. Кроме того, в нем выделяются 5 производственных стартапов, которые мы выбрали на основе таких критериев, как год основания, местоположение, объем привлеченного финансирования и т. Д. В этом отчете вы узнаете о решениях этих 5 стартапов и масштабных проектов.Свяжитесь с нами, чтобы получить информацию об остальных 93 экологически безопасных решениях для производства бетона.
Нажмите, чтобы загрузить
Заинтересованы в изучении всех более чем 90 экологически безопасных решений для производства бетона?
Nanotek Materials предлагает Nanocement
Производство цемента вызывает одни из самых больших выбросов парниковых газов (ПГ) в мире. Для решения этой проблемы существует тенденция к созданию умных и экологически безопасных строительных материалов, а также альтернативных процессов производства цемента.Стартапы используют достижения нанотехнологий для разработки экологически безопасного заменителя вяжущих материалов. Наноцемент обеспечивает улучшение физических и механических характеристик и снижает воздействие углерода в промышленности.
Канадский стартап Nanotek Materials разрабатывает наноцемент. В процессе стартапа портландцемент сочетается с нанооболочкой на основе суперпластификатора. Он также включает нанодобавки, которые обеспечивают более высокую плотность и прочность при меньшей пористости. Заменяя большую часть клинкера кварцевым песком, промышленными отходами и золой, решение стартапа снижает выбросы парниковых газов до 65%.
FLEXOFibers создает стальную фибру для армирования бетона
Добавление стальных волокон к цементным материалам делает бетон более прочным и долговечным. Он обеспечивает такую же гибкость при использовании более тонких плит и упрощает строительство. Однако производство стали загрязняет окружающую среду, а отходы бетона превращаются в отходы стальной фибры. Вот почему стартапы работают над решениями по армированию бетона, в которых используется переработанная сталь.
Испанский стартап FLEXOFibers производит стальную фибру из восстановленного металла.В 100% переработанном металлическом волокне стартапа используется высококачественная стальная проволока небольшого диаметра. FLEXOFiber Micro имеет большое количество волокон на единицу веса и обеспечивает лучшее распределение по бетонной массе. Армирующее средство для бетона дает те же преимущества, что и синтетические волокна.
AGMA Geopolymers разрабатывает геополимер
Производство цемента — энергоемкий процесс. Вот почему строительные стартапы ищут более эффективные производственные процессы и низкоуглеродные источники.Геополимеры утилизируют промышленные отходы и другие потоки отходов, отводя их от свалок. Следовательно, геополимеры предлагают низкоуглеродистую альтернативу цементу, а также обеспечивают лучшую теплоизоляцию.
AGMA Geopolymers — это итальянский стартап, разрабатывающий экологически устойчивые решения для строительства. Он превращает промышленные отходы в геополимер, тем самым снижая затраты на сырье. Производственный процесс стартапа включает смешивание алюмосиликатного порошка со щелочными инактиваторами с последующей реакцией с основным водным раствором.Продукт стартапа также снижает затраты на энергию при производстве вяжущих материалов, а также снижает выбросы углекислого газа (CO2).
Hyperion Robotics предоставляет роботизированную 3D-печать
Строительная промышленность производит большое количество отходов и уже применяет технологию 3D-печати для решения этой проблемы. Например, 3D-печать позволяет производителям сократить свои цепочки поставок и уменьшить отходы материалов. Это также позволяет разрабатывать готовые панели и плиты для модульного строительства, что еще больше способствует устойчивости.
Hyperion Robotics — финский стартап, который использует роботизированную 3D-печать для обеспечения устойчивости строительства. Комплексное решение стартапа включает в себя головку экструдера, роботизированный манипулятор и смеситель-насос. Наряду с программным решением стартап занимается прототипированием и печатью железобетонных элементов. Он использует структурную оптимизацию, чтобы максимизировать высоту печати при минимальном использовании материала. Таким образом решения Hyperion Robotics позволяют производить зеленый бетон.
neustark позволяет улавливать атмосферный углерод
Производство цемента вносит значительный вклад в антропогенный выброс углекислого газа в атмосферу.Технологии улавливания углерода, которые перенаправляют этот углерод в производство цемента, снижают общий углеродный след отрасли. Вот почему стартапы и компании разрабатывают инновационные решения, которые удерживают атмосферный углерод в бетоне, где он может оставаться в течение длительного времени.
Швейцарский стартап neustark удаляет углекислый газ из атмосферы и хранит его в переработанном бетоне. Он применяет принципы естественной минерализации, ускоряя ее для более эффективного улавливания углерода.Он также оптимизирует использование бетона, чтобы свести к минимуму использование цемента при производстве бетона. Бетон для стартапа соответствует всем стандартным критериям качества по удобоукладываемости, прочности на сжатие, модулю упругости и долговечности.
Узнайте больше Производственные стартапы
Производственные стартапы, такие как примеры, приведенные в этом отчете, сосредоточены на инновационных материалах, робототехнике, автоматизации, а также аддитивном производстве. Хотя все эти технологии играют важную роль в развитии отрасли, они представляют собой лишь верхушку айсберга.Чтобы узнать больше о производственных технологиях, просто свяжитесь с нами, и мы рассмотрим ваши области интересов. Чтобы получить более общий обзор, вы можете загрузить наш бесплатный отчет о производственных инновациях, чтобы сэкономить время и улучшить процесс принятия стратегических решений.
Бетонные инновации | Журнал гражданского и строительного инженера
Лайонел Лемей, PE, SE, LEED AP. Исполнительный вице-президент по конструкциям и устойчивому развитию, Национальная ассоциация товарного бетона
Брайан Лемей, младший научный сотрудник, Национальная ассоциация товарных бетонных смесей
Кредит: 1 LU / HSW
Номер курса: ZG082019CS
Спонсор:
Build with Strength, коалиция Национальной ассоциации готовых бетонных смесей, знакомит строителей и дизайнеров и политиков с преимуществами бетона и поощряет его использование в качестве строительного материала.Ни один другой материал не может повторить преимущества бетона с точки зрения прочности, долговечности, безопасности и простоты использования.Обзор курса:
Бетон — это материал, который выбирают для самых высоких зданий в мире и инфраструктуры, рассчитанной на века. Чтобы удовлетворить потребности в этих передовых проектах, бетон должен быть прочнее, долговечнее и удобнее, чем когда-либо прежде. В этой статье рассказывается, как с помощью новых продуктов, методов производства и исследований разрабатываются инновационные бетоны для решения этих новых задач.Гибкий бетон, бетон, поедающий смог, и улавливание углерода — это лишь несколько примеров новых технологий, улучшающих продукт, разработка которого ведется почти 5000 лет.
Цели обучения:
1. Понимание новых технологий, используемых в производстве бетона
2. Узнайте, как инновационные бетонные изделия могут повысить эффективность проекта
3. Узнайте, как внедрять новейшие бетонные инновации в проекты строительства и инфраструктуры
4.Продемонстрировать важность внедрения новых технологий для повышения устойчивости и устойчивости искусственной среды
Юбилейная церковь. Фото: Элио Ломбардо, Alamy Stock Photo Пантеон. Фото: Hercules Milas, Alamy Stock PhotoВведение
Что общего между Юбилейной церковью и Пантеоном? Оба они являются культовыми сооружениями в Риме. Но, кроме того, они оба построены из инновационного бетона. Римляне освоили использование бетона 2000 лет назад, чтобы построить одни из самых знаковых построек из когда-либо построенных.Римский бетон, хотя и отличается от современного бетона, использовал те же принципы, сочетая заполнитель с гидравлическим вяжущим. Агрегат включал в себя куски камня, керамической плитки и кирпичного щебня, часто перерабатываемого в снесенных зданиях. Вулканический пепел, называемый пуццоланом, был излюбленным связующим там, где он был доступен. В качестве связующих также использовались гипс и негашеная известь. И даже 3000 лет назад египтяне использовали бетонную форму, сделанную из грязи и соломы, для строительства пирамид. Сегодня, конечно, большая часть бетона производится из портландцемента, изобретенного в 1824 году, в сочетании с высококачественным заполнителем.Большинство современных бетонов дополнены инновационными продуктами и добавками для улучшения пластических и затвердевших свойств.
Инновационные дополнительные вяжущие материалы (SCM), такие как летучая зола, шлаковый цемент и микрокремнезем, используются для повышения прочности, долговечности и удобоукладываемости. Химические добавки влияют на время схватывания, морозостойкость и текучесть. Крошечные волокна добавляются для увеличения пластичности и контроля растрескивания. Двуокись углерода вводится в бетон для повышения прочности и улавливания парниковых газов.Некоторые усовершенствования фактически удаляют загрязняющие вещества с поверхности бетона и из окружающей атмосферы, что и делает бетон Юбилейной церкви таким инновационным. Наружные изогнутые поверхности покрыты цементом из диоксида титана (TiO 2 ), который разъедает смог, помогая поддерживать чистоту поверхности.
Бетон — это наиболее широко используемый строительный продукт в мире. В основном его делают на месте из местных материалов. Он экономичен, доступен повсюду, прочен и долговечен.Хотя обычный бетон может справиться с большинством работ, он также является предпочтительным материалом для самых высоких зданий в мире и инфраструктуры, рассчитанной на века. Хотя бетон не всегда является синонимом инноваций, новые продукты и методы производства улучшают характеристики бетона для решения современных проблем. В этой статье рассматриваются некоторые из этих последних нововведений.
Самоочищающийся бетон
Представьте себе бетон, который может очищать себя и даже окружающий воздух от вредных загрязняющих веществ.Именно на это способен бетон, изготовленный из диоксида титана (TiO 2 ). Цемент TiO 2 предназначен для разрушения вредных загрязняющих веществ в воздухе посредством реакции, катализируемой светом, или фотокатализа из-за диоксида титана, который добавляется в цемент во время его производства. Эта способность цементов TiO 2 была вдохновлена способностью определенных микробов расщеплять вредные химические вещества, изменяя их степень окисления, в том числе посредством фотокатализа. Однако в фотокатилитических цементах реакция осуществляется титаном, тогда как микробы полагаются на естественные ферменты.Цемент разрушает как органические, так и неорганические загрязнители, и он предназначен для использования в проектах в городских центрах, где загрязнение воздуха и плохое качество воздуха наиболее выражены.
Пример того, как цемент TiO 2 разрушает загрязняющие вещества, можно увидеть в его преобразовании диоксида азота (NO 2 ), вредного соединения, которое в основном образуется при сжигании топлива в легковых и грузовых автомобилях. Двуокись азота — одно из соединений, вызывающих кислотные дожди, смог, респираторные проблемы и окрашивание зданий и тротуаров.В результате реакции с солнечным светом образуются гидроксильные радикалы, которые реагируют с NO 2 с образованием NO 3 , который растворяется водой после реакции с поверхностью цемента.
Данные исследования TX Active®, цемента TiO 2 , продаваемого Lehigh Hanson (подразделение HeidelbergCement Group) в США, показывают, что «до 50% этих атмосферных загрязнителей можно было бы сократить в некоторых городах, если бы только 15%. зданий и дорог были покрыты цементом TX Active®.«TX Active® был впервые использован для изогнутых панелей Юбилейной церкви (также известной как Dives in Misericordia Church) в Риме, в которой использовались фотокаталитические цементные панели в качестве стилистических оболочек. С тех пор Italcementi (подразделение HeidelbergCement Group) посвятила десятилетия исследованиям фотокаталитических цементных продуктов. Этот цемент имеет многообещающий потенциал для значительного улучшения городской жизни и окружающей среды.
Пример: Юбилейная церковь, Рим, Италия
Фото: Эдмунд Самнер-ВИД, Алами Стоковое ФотоПо словам архитекторов Ричарда Мейера и его партнеров, Юбилейная церковь в Риме «была задумана как часть инициативы тысячелетия Папы Иоанна Павла II по обновлению приходской жизни в Италии.«Проект состоит из самой церкви, а также светского жилья и жилья для духовенства. Церковь легче всего отличить по трем большим бетонным корпусам, которые символизируют Святую Троицу. Учитывая символическое значение ракушек, их внешний вид является безусловным приоритетом. Таким образом, из-за того, что оболочки должны оставаться в первозданном состоянии, было вполне естественным использовать «самоочищающийся» фотокаталитический бетон TX Active®, чтобы гарантировать, что на оболочках не будут накапливаться пятна из-за смога.Фотокаталитические оболочки, построенные в 2003 году, заметно остались чистыми и белыми, постоянно выполняя самообслуживание.
Гибкий бетон
Гибкий бетон в 300-500 раз пластичнее обычного. Фото: Victor C. LiГибкий бетон представляет собой эффективную альтернативу, прежде всего, при строительстве и обслуживании инфраструктуры, где бетон подвержен суровым погодным условиям и экстремальным нагрузкам. Конструкция, которая дает изгибаемый бетон или инженерный цементный композит (ECC), его впечатляющая пластичность основана на перламутре, веществе, которое покрывает внутреннюю часть раковин морского ушка.Перламутр состоит из небольших пластинок арагонита, которые удерживаются вместе природными полимерами, что делает его твердым и гибким, поскольку пластинки могут свободно скользить из стороны в сторону под воздействием нагрузки. Этот эффект имитируется в гибком бетоне за счет рассеивания крошечных волокон по всей поверхности. Виктор К. Ли из Мичиганского университета, где впервые была исследована и изобретена система ECC, утверждает, что изгибаемый бетон «может деформироваться до 3-5 процентов при растяжении до того, как он разрушится, что дает ему в 300-500 раз большую способность к деформации при растяжении, чем обычно. конкретный».Конечно, именно эта невероятная способность выдерживать растягивающую деформацию делает изгибаемый бетон уникальным.
Столь значительное увеличение пластичности предполагает различные потенциальные области применения. Во-первых, на дорогах, а также на других покрытиях с твердым покрытием, которые должны выдерживать многократную нагрузку тяжелых транспортных средств, изгибаемый бетон будет реже трескаться, предотвращая дальнейшее выветривание, главным образом из-за дорожных солей, которые разъедают стальную арматуру. Кроме того, благодаря способности ECC поглощать большее количество энергии без повреждений, его можно использовать для изготовления усиливающих элементов, таких как демпферы на обходном виадуке Сейшо в Японии, протяженность которого составляет примерно 28 километров.Доктор Ли также заявляет, что система ECC использовалась для защиты от землетрясений в высотных зданиях в Токио и Осаке, и далее предполагает, что ECC может быть полезен при подземном строительстве, а также при строительстве водной инфраструктуры.
Однако, прежде чем его можно будет более широко коммерциализировать для таких крупномасштабных проектов, изгибаемый бетон должен стать более доступным. Чтобы быть экономически жизнеспособным, он должен поставляться эффективно и не чрезмерно использоваться в проектах. Но крайне важно, чтобы профессионалы в области проектирования были осведомлены о продукте и его потенциале, поскольку в противном случае они могли бы упустить из виду перспективный бетонный вариант для конструкций, которые требуют способности выдерживать значительные растягивающие напряжения.
Гибкий бетон также обладает способностью к самовосстановлению. Поскольку изгибаемый бетон сохраняет трещины относительно небольшими, естественные реакции в затвердевшем бетоне создают «исцеляющие» продукты за счет минерализации углерода и постоянной гидратации, которые устраняют трещины и восстанавливают долговечность бетона. Гибкий бетон — перспективная технология, которая уже зарекомендовала себя благодаря коммерциализации нескольких компаний.
На самом деле, фибробетон не новость.Многие компании поставляют волокна для использования в бетоне с целью улучшения прочности и долговечности бетона. В бетоне, армированном волокном, это достигается за счет включения волокон из стали, стекла или органических полимеров (пластмасс). Иногда также используются натуральные волокна, такие как сизаль и джут. Эти волокна в основном используются для борьбы с пластической усадкой и усадкой при высыхании, которые в противном случае могут привести к растрескиванию и повреждению бетона. Это сопротивление усадке и последующему растрескиванию является ключом к продлению срока службы бетона, уменьшая частоту дорогостоящих ремонтов.Волокна также препятствуют расширению существующих трещин и дальнейшему повреждению бетона, когда они действительно появляются. А в последнее время стальная фибра используется в конструкциях, чтобы уменьшить количество традиционных стальных арматурных стержней, сэкономив время и труд.
Фото: Bluestone Organization
Пример: 42 Broad, Fleetwood, New York
42 Broad — это 16-этажный комплекс смешанного использования недалеко от Нью-Йорка, построенный с использованием изоляционной бетонной формы (ICF). Строительство ICF становится все более популярным с тысячами проектов, построенных в США, но по-прежнему многими считается инновационным.ICF размещает железобетонную стену между формами из жесткого пенополистирола, которые остаются на месте после затвердевания бетона. В Канаде есть несколько более высоких зданий ICF, но 16-этажное здание 42 Broad будет самым высоким в США.
Фото: ICF Panels, Inc.Настоящим нововведением в этом проекте является облицовка блоков Amvic ICF панелями и использование армирования стальным волокном HelixTM. ICF собираются за пределами строительной площадки на ближайшем заводе и прибывают на рабочую площадку в виде индивидуальных панелей длиной до 50 футов, что приводит к экономии труда и времени на строительной площадке, а это означает, что владелец может занять здание раньше.Частью того, что делает возможным этот процесс, является использование стальных волокон в готовом смешанном бетоне для замены горизонтальной арматуры, что устраняет дорогостоящие горизонтальные срезы арматуры.
LafargeHolcim — одна из первых компаний, которые начали коммерциализацию гибкого бетона с продуктом под названием Ductal®. Ductal® — это бетон со сверхвысокими характеристиками (UHPC), который включает волокна в бетонную смесь для повышения прочности и пластичности, а также множества других преимуществ.LafargeHolcim распределяет порошок премикса, волокна и добавки, необходимые для производства Ductal®, своим партнерам, которые затем смешивают его с бетоном. LafargeHolcim заявляет, что они используют «высокоуглеродистые металлические волокна, нержавеющие волокна, волокна поливинилового спирта (ПВС) или стекловолокна», чтобы повысить способность бетона выдерживать растягивающие нагрузки и деформации.
Ductal® также менее пористый, чем обычный бетон, что делает его более устойчивым к хлоридам, кислотам и сульфатам. Кроме того, он, как правило, более непроницаем для воды, что делает его идеальным для кровли.Кроме того, Ductal® обладает самовосстанавливающимися свойствами. Этот гибкий бетон был тщательно исследован и продается.
Пример: Художественный музей Переса, Майами, Флорида
Фото: Ян Дагналл, Алами Стоковое ФотоХудожественный музей Переса в центре Майами примечателен главным образом применением сверхвысокопроизводительного бетона Ductal® (UHPC). В музее находится около 200 000 квадратных футов внутреннего и внешнего пространства для презентации современного искусства.Однако это свойство сопряжено с одной серьезной проблемой. Музей построен в заливе Бискейн, где он подвержен воздействию морского воздуха и соли. Кроме того, он подвержен риску тропических штормов и ураганов и, следовательно, должен противостоять силам, связанным с этими экстремальными погодными явлениями. Ductal® был использован для производства около 100 стоек длиной 16 футов для поддержки самого большого в мире ударопрочного окна во время его строительства в 2013 году. Бетонные стойки были сделаны тонкими, что обеспечивало максимальную видимость, а также соответствовало строительным нормам Флориды. для сопротивления ураганам.
Графеновый бетон — это бетон, армированный графеном. Графен представляет собой одинарный слой атомов углерода, прочно связанных в гексагональную сотовую решетку. Слои графена, наложенные друг на друга, образуют графит, естественную кристаллическую форму углерода, наиболее часто используемую в карандашах и смазках. Отдельные слои графена в графите можно разделить на листы толщиной всего в один атом. Графен — это самое тонкое соединение, известное человечеству, самый легкий из известных материалов и самое сильное из обнаруженных соединений, более чем в 100 раз прочнее стали.Графеновый бетон получают путем суспендирования хлопьев графена в воде, а затем смешивания этой воды с традиционными ингредиентами бетона, такими как цемент и заполнитель.
Сильная сторона этой технологии во многом заключается в ее доступности, поскольку она недорогая и совместима с современными крупномасштабными производственными требованиями. Согласно исследовательской статье, опубликованной в журнале Advanced Functional Materials, озаглавленной «Сверхвысокопроизводительные нанотехнологические композиты из графена и бетона для многофункциональных приложений», графеновый бетон впечатляюще демонстрирует «увеличение прочности на сжатие на 146 процентов по сравнению с обычным бетоном — 79.5-процентное увеличение прочности на изгиб и снижение водопроницаемости почти на 400 процентов ». В дополнение к своей повышенной прочности, графеновый бетон также более экологичен, поскольку для него требуется меньше цемента, чем обычно требуется для производства бетона с заданной прочностью. В качестве альтернативы можно использовать более прочный графеновый бетон для изготовления более мелких структурных элементов, что снижает количество используемого материала.
Улавливание углерода
Как и большинство искусственных материалов, бетон считается источником выбросов углекислого газа (CO 2 ), в основном из-за процесса производства цемента.Но что, если бы вы могли повернуть этот процесс вспять и улавливать или улавливать CO 2 в бетоне с помощью естественных процессов или технологий улавливания углерода.
Карбонизация — это естественный процесс, при котором диоксид углерода (CO 2 ) проникает через поверхность затвердевшего бетона и вступает в химическую реакцию с продуктами гидратации цемента с образованием карбонатов. Для эксплуатационного бетона карбонизация — медленный процесс со многими зависимыми переменными. Скорость снижается со временем. Это связано с тем, что карбонизация снижает проницаемость, и карбонизация происходит от поверхности внутрь, создавая более плотную матрицу на поверхности, затрудняя дальнейшую диффузию CO 2 в бетон.Хотя процесс карбонизации медленный, он все же приводит к поглощению некоторого количества CO 2 , выделяемого при производстве цемента, — химический процесс, называемый кальцинированием. Теоретически, при наличии достаточного времени и идеальных условий весь CO 2 , выделяемый при прокаливании, может быть изолирован посредством карбонизации. Однако условия реального мира обычно далеки от идеальных.
Скорость поглощения CO 2 зависит от воздействия воздуха, ориентации поверхности, отношения поверхности к объему, компонентов связующего, обработки поверхности, пористости, прочности, влажности, температуры и концентрации CO 2 в окружающей среде.Предсказать, сколько CO 2 абсорбируется монолитным бетоном, сложно. Что известно, так это то, что скорость поглощения CO 2 является наибольшей, когда отношение поверхности к объему высокое, например, когда бетон был раздроблен и подвергался воздействию воздуха.
В одном из наиболее всеобъемлющих исследований Си и др. Опубликовали краткое изложение своего исследования в статье «Существенное глобальное поглощение углерода за счет карбонизации цемента» в журнале Nature Geoscience, ноябрь 2016 года. процесс прокаливания — карбонизация.Используя аналитическое моделирование химии карбонизации, они смогли оценить региональное и глобальное поглощение CO 2 в период с 1930 по 2013 год. По их оценкам, кумулятивное количество CO 2 , изолированного в бетоне, составляет 4,5 Гт за этот период. Это компенсирует 43% выбросов CO 2 от производства цемента, вызванных процессом обжига. Они пришли к выводу, что карбонизация цементных продуктов представляет собой значительный сток углерода.
Две области исследований и коммерциализации предлагают значительные улучшения в этом процессе поглощения CO 2 .Самый простой подход — усиленная карбонизация в условиях окончания и вторичного использования бетона. Это нельзя считать инновационным, поскольку это просто означало бы изменение способа сбора и обработки разрушенного бетона перед повторным использованием. Если условия подходящие, а размер частиц небольшой, дробленый бетон потенциально может поглотить значительные количества CO 2 за небольшой период, например, один или два года, и, таким образом, оставляя измельченный бетон открытым для воздуха перед повторным использованием, было бы полезно.
Другие коммерчески жизнеспособные технологии ускоряют карбонизацию. Это достигается либо введением CO 2 в бетон, выдержкой бетона в CO 2 или созданием искусственных заполнителей известняка с использованием CO 2 .
Компания под названием CarbonCure использует CO 2 , улавливаемый промышленными выбросами, который затем очищается, сжижается и доставляется на бетонные заводы-партнеры в резервуарах под давлением. Затем он вводится в бетон во время его перемешивания, что превращает CO 2 в твердый минерал внутри бетона.Образовавшиеся минералы увеличивают прочность на сжатие.
Этот процесс снижает выбросы CO 2 двумя способами — за счет прямого связывания CO 2 , вводимого в бетонную смесь, и за счет снижения потребности в цементе, поскольку бетон CarbonCure требует меньше цемента для производства бетона с заданной прочностью.
Экономическая жизнеспособность этого бетона также делает его особенно привлекательной инновацией. Стоимость оборудования и лицензирования компенсируется снижением цен на цемент.Компания CarbonCure установила свою технологию на более чем 100 заводах по всей Северной Америке, которые поставили более двух миллионов кубических ярдов бетона. Этот продукт достаточно доступен, чтобы его можно было использовать сейчас, и уже был использован с большим успехом во многих проектах.
Фото: любезно предоставлено CarbonCure
Пример использования: 725 Ponce, Atlanta, Georgia
Завершенное в 2018 году офисное здание по адресу 725 Ponce De Leon Avenue было построено с использованием 48000 кубических ярдов бетона CarbonCure.Благодаря их сотрудничеству инженер-конструктор Uzun + Case и поставщик бетона Thomas Concrete смогли значительно сократить углеродный след этого проекта. Бетон CarbonCure поглощает 680 метрических тонн, или 1,5 миллиона фунтов, CO 2 , что примерно равно количеству CO 2 , поглощаемому 800 акрами леса в США каждый год. Тот факт, что выбросы, вредные для окружающей среды, могут быть сокращены таким значительным фактором в этом большом проекте, который обеспечивает 360 000 квадратных футов офисных площадей, является прекрасным примером жизнеспособности улавливания и связывания углерода в качестве устойчивого варианта для бетонного строительства.
Solidia Technologies предлагает еще одну технологию улавливания углерода. Он сочетает в себе специально разработанный цемент с отверждением CO 2 для производства бетона, в первую очередь для производства сборных железобетонных изделий. Цемент Solidia примерно такой же по стоимости, как портландцемент, но значительно снижает выбросы CO 2 за счет снижения производственной энергии. В первую очередь это связано с тем, что в цементе Solidia используются все те же материалы, которые используются для производства портландцемента, но в другом соотношении.
ЦементSolidia использует меньше известняка, чем портландцемент, что позволяет обжигать его при более низких температурах в тех же вращающихся печах, в которых в настоящее время производится обычный портландцемент. Эти более низкие температуры горения потребляют меньше энергии, а также производят на 30% меньше парниковых газов и других загрязняющих веществ. Кроме того, вместо отверждения в воде, как у обычного бетона, бетон Solidia отверждается при контакте с атмосферой, содержащей CO 2 . Это не только обеспечивает большую точность во время процесса отверждения, но и во время отверждения, бетон Solidia изолирует CO 2 , равный 5% от его веса.Solidia утверждает, что за счет сочетания более низких материальных затрат, более низких затрат на топливо и секвестрации CO 2 в процессе отверждения углеродный след бетона снижается на 70%.
БетонSolidia также предлагает другие практические преимущества, помимо экологической безопасности. Например, Solidia заявляет, что их бетон подвержен уменьшению высолов, а это означает, что солевые пятна будут проявляться менее серьезно и реже на поверхности, когда она подвергается воздействию воды. Кроме того, снижается водопоглощение бетона, составляющее менее 2%.Его прочность на сжатие составляет около 10 000 фунтов на квадратный дюйм. Для окрашивания требуется меньше пигмента. И, наконец, Solidia Concrete совместим с нетрадиционными заполнителями и переработанным стеклом. Это позволяет дополнительно снизить материальные затраты и экологические преимущества.
Другой компанией, использующей технологию улавливания углерода, является Blue Planet Ltd. Они предлагают продукт, который «сочетает в себе неочищенный CO 2 , поглощенный непосредственно из дымовых газов электростанции или других промышленных источников выбросов CO 2 , с оксидами металлов для производства известняка, используемого для покрытия субстрат, делающий СО 2 -секвестрированный строительный заполнитель.Известняковое покрытие представляет собой 44 процента по массе постоянно поглощенных отходов CO 2 ». Подложка обычно представляет собой мелкие частицы камня или даже переработанный бетон.
Частицы переработанного бетона покрыты синтетическим известняком, образуя покрытие, которое содержит 44% по массе CO2. Фотографии: Blue Planet Ltd.Blue Planet заявляет, что углерод-отрицательный бетон достижим, используя их искусственный известняк в бетоне. Они подсчитали, что при замене обычного заполнителя на один кубический ярд бетона, обычно стоимостью 3000 фунтов, 44% его веса будет состоять из секвестрированного CO 2 , примерно 1320 фунтов.Это компенсировало бы больше, чем количество CO 2 , обычно производимое таким же количеством обычного бетона, сделанного с портландцементом, которое составляет примерно 600 фунтов на кубический ярд. Легкий заполнитель Blue Planet с известняковым покрытием был указан для временной зоны посадки B в международном аэропорту Сан-Франциско в 2016 году. Испытания бетона показали, что бетон Blue Planet соответствует всем необходимым спецификациям.
Технология улавливания и связывания углерода — многообещающее решение для уменьшения углеродного следа цемента и бетона при одновременном повышении производительности.Возможность значительно сократить выбросы CO 2 , связанные с производством бетона, или даже выйти за их пределы за счет связывания большего количества CO 2 , чем образуется в процессе производства цемента, является заманчивой. Многие технологии улавливания и связывания углерода уже коммерчески жизнеспособны и в настоящее время используются в строительстве, поскольку их можно удобно производить на существующем оборудовании или путем модернизации существующих заводов. В целом, улавливание углерода представляет собой простое, но очень многообещающее решение для уменьшения воздействия бетона на окружающую среду.
Самоуплотняющийся бетон
Самоуплотняющийся бетон (SCC) — это высокотекучий, не расслаивающийся бетон, который может течь на место, заполнять опалубку и инкапсулировать арматуру без какой-либо механической вибрации. SCC основан на сочетании высокой доли мелкозернистого заполнителя и добавок, называемых суперпластификаторами и модификаторами вязкости, для получения стабильного и высокотекучего бетона.
Повышенная простота использования и эффективность SCC во время строительства — основа многих его основных преимуществ.Во-первых, его можно укладывать быстрее, чем обычный бетон, при этом требуется меньшая отделка и отсутствие механической вибрации. Он также улучшает однородность бетона на месте, а также однородность поверхностей, уменьшая или устраняя необходимость в поверхностных работах.
Кроме того, использование SCC позволяет сэкономить трудозатраты, а также повысить безопасность на рабочем месте, поскольку не требует от рабочих перемещаться по поверхности плит или верху стен для механической вибрации бетона. SCC экономит время во время строительства, что приводит к снижению затрат, а также улучшает прокачиваемость бетона и время оборачиваемости автобетононасосов.
SCC был впервые разработан в 1986 году профессором Окамура из Университета Оучи, Япония, для решения проблемы нехватки квалифицированной рабочей силы. Сначала SCC использовался в узкоспециализированных проектах, таких как ремонтные работы или в труднодоступных местах из-за высокой стоимости производства и необходимости высокого контроля качества. Первое массовое использование SCC было в сборных железобетонных изделиях, где бетон производился и размещался в контролируемых условиях. В товарных бетонных смесях SCC использовался в основном для сильно армированных секций, где механическая вибрация была затруднена.В последнее время SCC используется в архитектурном бетоне, поскольку он обеспечивает более качественную обработку поверхности, чем у обычного бетона. SCC по-прежнему имеет относительно высокую стоимость, но набирает популярность там, где не хватает рабочей силы или где требуется гладкий открытый бетон.
Одно из самых популярных применений SCC — это проекты высотных зданий, что доказывает его коммерческую жизнеспособность и успех в практических приложениях. Некоторые соображения, которые следует учитывать в отношении этого бетона, связаны с тем фактом, что он зависит от текучести, которая может снижаться из-за жаркой погоды, больших расстояний или задержек на стройплощадке.Технические характеристики, необходимые для данной работы, такие как текучесть и растекание, могут варьироваться, но смеси могут быть испытаны с помощью методов, включая испытание на оседающую текучесть, чтобы определить степень пластических свойств бетона, чтобы гарантировать, что бетон, поступающий на рабочую площадку, соответствует стандартам, специфичным для сам проект. SCC полностью коммерциализирован и используется во всем мире.
Пример использования: 432 Park Avenue, New York
Фото: Дэвид Перейрас, Shutterstock432 Парк-авеню в Нью-Йорке в настоящее время является самым высоким жилым строением в США.Это эстетически простое здание с открытыми белыми бетонными колоннами, которые структурно укрепляют здание, а также придают ему наиболее характерные стилистические атрибуты. Здание очень тонкое для своей высоты, его ширина и длина составляет 93,5 фута, а высота — 1396 футов. Согласно статье в журнале STRUCTURE, июль 2018 года, для достижения «минимального смещения, ускорения и вибрации для соответствия самым строгим стандартам» использовались многочисленные инновационные структурные методы.К ним относятся: «пять выносных опор, каждая из которых занимает более двух этажей, были разработаны по всей высоте башни, чтобы служить положительной связью между внутренним ядром и периметром, что улучшило общие характеристики конструкции».
Более жесткий бетон с более высокой прочностью на сжатие использовался на этажах выше 38-го этажа для дальнейшего увеличения сопротивления движению в верхних этажах. Кроме того, весь бетонный бетон для 432 Park Avenue был спроектирован с учетом повышенной прочности за счет сведения к минимуму отношения воды к вяжущим материалам до нуля.25, и бетон должен был быть перекачиваемым, самоуплотняющимся и иметь низкую теплоту гидратации, чтобы облегчить строительство и внешний вид открытых структурных элементов.
От отходов к стоимости
Дополнительные вяжущие материалы (SCM), такие как летучая зола, шлаковый цемент и микрокремнезем, являются ключевыми для получения высокоэффективных бетонов. Что делает эти материалы настолько инновационными, так это то, что большинство из них получают из отходов — побочных продуктов производственного процесса, которые в противном случае оказались бы на свалках.Но когда эти отходы смешиваются с портландцементом в бетоне, они вступают в реакцию с определенными химическими соединениями с образованием большего количества связующего. В результате эти материалы чрезвычайно ценны как SCM.
Пример: Trump Tower Chicago
Фото: ghornephoto, iStockChicago Trump Tower and Hotel — это 92-этажное здание, полностью построенное из железобетона. В проекте было использовано 194 000 кубических ярдов бетона. Архитектор / инженер Skidmore, Owings & Merrill указал поставщика высококачественного бетона и бетона Prairie Materials, который разработал смеси.Колонны и стены требовали 12000 фунтов на квадратный дюйм в течение 90 дней до уровня 51 с некоторыми боковыми элементами сопротивления до 16000 фунтов на квадратный дюйм. SCC был указан для многих элементов конструкции из-за перегрузки арматуры. Чтобы уменьшить теплоту гидратации, большие объемы SCM были определены для основы мата, которая включала комбинацию шлакового цемента, летучей золы и микрокремнезема. Во время строительства фундамент площадью 5000 кубических ярдов был крупнейшим размещением SCC в Северной Америке.
Высокопроизводительная система железобетона помогла минимизировать толщину пола, создав более высокие потолки.Жилые этажи также имеют открытые пролеты до 30 футов, не требующие перемычки по периметру, позволяющие открывать панорамные виды на Чикаго и озеро Мичиган. Сочетание нескольких инновационных бетонных технологий позволило быстро и эффективно построить, а также открыло новые возможности, недоступные для обычного бетона.
Пары кремнезема — это побочный продукт переработки кварца в кремний или железо-кремниевые металлы в электродуговой печи. Пары кремнезема состоят из сверхмелкозернистых сферических частиц, которые в сочетании с цементом значительно увеличивают прочность и долговечность бетона.Из трех основных SCM у микрокремнезема самый низкий запас и самая высокая стоимость, обычно как минимум в три раза дороже портландцемента. Он используется в приложениях, где требуется чрезвычайно высокая прочность, например, в колоннах в высотных зданиях или там, где требуется чрезвычайно низкая проницаемость для долговечности, например, настилы мостов и настилы парковок. Обычно его комбинируют с другими модулями SCM для оптимизации производительности и затрат.
Доменный шлак — побочный продукт производства чугуна. После закалки и измельчения доменный шлак приобретает гораздо более высокую ценность, чем SCM для бетона.Доменный шлак используется в качестве частичной замены цемента, чтобы придать бетону дополнительную прочность и долговечность. Некоторое количество шлака используется для изготовления легкого заполнителя для бетона. В США было произведено около 16 миллионов тонн шлака, но менее половины из них было использовано в бетоне в качестве SCM. Шлаковый цемент стоит примерно столько же или немного больше, чем цемент, в зависимости от качества и местоположения.
Угольная зола является побочным продуктом сжигания угля на электростанциях. Летучая зола, обычный SCM, используемый в бетоне, является одним из компонентов угольной золы.По данным Американской ассоциации угольной золы (ACAA), в 2017 году было произведено 111,4 миллиона тонн угольной золы, из которых 38,2 миллиона тонн — летучая зола. Угольная зола и летучая зола имеют множество применений, от использования в бетоне в качестве SCM до синтетического гипса для стеновых панелей и горнодобывающей промышленности. Из 38,2 миллиона тонн производимой летучей золы только 14,1 миллиона тонн используются в бетоне.
Летучая зола — самый распространенный из всех СКМ, и ее стоимость составляет примерно половину стоимости портландцемента. Однако из-за ужесточения правил выбросов на угольных электростанциях производится не так много высококачественной летучей золы, как в прошлом.Кроме того, с переходом к возобновляемым источникам энергии и природному газу угольные электростанции закрываются, и поэтому многие рентабельные поставки сокращаются.
Пример: 102 Ривония, Йоханнесбург, Южная Африка
Фото: Грег Бальфур Эванс, Алами Стоковое ФотоРивония-Роуд 102 состоит из двух основных зданий с соединенными переходами между ними, чтобы создать ощущение единства и стимулировать сотрудничество между различными зонами офиса. Оно было спроектировано с учетом экологических требований, поскольку оно на 50% более устойчиво, чем среднее офисное здание с 4-звездочным рейтингом Green Star SA (Южная Африка).Чиллеры с воздушным охлаждением и противопожарная система, рециркулирующая использованную воду, также внесли свой вклад в энергоэффективность проекта. Примечательно, что использование летучей золы в бетоне снизило общее использование материалов в рамках проекта на 30%, что также в значительной степени способствовало уменьшению углеродного следа проекта.
Поскольку производство электроэнергии на угле началось в США в начале 1900-х годов, но использование летучей золы в бетоне в значительных объемах началось только в конце 1900-х годов, по оценкам, около 1.5 миллиардов тонн угольной золы было отправлено на свалки, часть из которых — летучая зола. И вот тут-то и появляется инновация. Некоторые компании, понимая, что спрос на летучую золу в бетоне, вероятно, возрастет, начали собирать летучую золу со свалок и обрабатывать ее с помощью процесса, называемого обогащением.
Обогащение просто означает извлечение угольной золы со свалок и ее переработку, чтобы она соответствовала необходимым стандартам полезного использования. Для летучей золы это обычно означает уменьшение количества несгоревшего углерода в золе.Углерод имеет свойство абсорбировать, что препятствует улавливанию воздуха и добавкам, уменьшающим воду. Есть также другие химические вещества, такие как аммиак, в некоторых отложениях угольной золы, которые необходимо уменьшить перед использованием в бетоне.
Несколько компаний разработали процессы для сбора золы со свалок и уменьшения количества несгоревшего углерода и аммиака, кальция, серы и других примесей. Самый простой процесс — сжечь излишки углерода. В других методах используется химическая обработка для смягчения воздействия углерода и аммиака, а одна компания использует низкочастотный звук, чтобы уменьшить размер частиц и сделать их более однородными, что является желаемой характеристикой летучей золы.Компании включают Boral Resources, Waste Management / Fly Ash Direct, SEFA Group, SonoAsh LLC и Charah Solutions, согласно статье «Копаем в прошлом: сбор унаследованных месторождений золы для удовлетворения будущего спроса», написанной Рафиком Минкарой и опубликованной в Выпуске 1 за 2019 год. журнала Ash at Work.
Минкара заключает: «Несмотря на то, что в настоящее время существует множество технологий для обогащения золы, содержащейся на суше и в накопителях, их стоимость и сложность могут оказаться весьма значительными». Он продолжает: «Процессы обогащения могут быть столь же простыми, как использование стандартного оборудования, или включать разработку индивидуальных решений с высокими требованиями к капитальным затратам.«В конце концов, это будет зависеть от спроса на летучую золу. Поскольку запасы недорогих материалов со временем уменьшаются, спрос, вероятно, будет удовлетворен за счет сбора и обогащения огромных запасов угольной золы на свалках.
Бетон без цемента
Хотя мы, вероятно, находимся далеко от широкой коммерциализации, одной из наиболее интересных областей исследований и разработок является геополимерный бетон, в котором вместо портландцемента в качестве связующего используется летучая зола и / или шлак и химические активаторы.Геополимерный бетон изготавливается с использованием источника кремния и алюминия, обычно летучей золы или шлака, и объединения его со щелочным активирующим раствором, который полимеризует эти материалы в молекулярные цепочки для создания затвердевшего связующего. Наиболее распространенные активирующие растворы включают гидроксид натрия или гидроксид калия, которые высвобождают кремний и алюминий.
Прочность на сжатие геополимерного бетона сравнима с прочностью портландцементного бетона или выше, и увеличение прочности обычно происходит быстрее при прочности 3500 фунтов на квадратный дюйм или выше за 24 часа.Прочность на сжатие через 28 дней составляет от 8000 до 10000 фунтов на квадратный дюйм. Исследования показывают, что геополимерный бетон имеет меньшую усадку при высыхании, меньшую теплоту гидратации, улучшенную проницаемость для хлоридов и более устойчив к кислотам. И его огнестойкость значительно выше, чем у портландцементного бетона, который уже обладает высокой огнестойкостью, что делает геополимерные бетоны идеальными для специальных применений при высоких температурах.
На сегодняшний день развитие большинства этих продуктов не вышло за пределы стадии исследований и разработок.Одна компания, Ceratech, запустила геополимерный бетон в 2002 году, но позже закрылась. Продукт под названием Pyrament® был выпущен на рынок в 1980-х годах, но не был успешно коммерциализирован. Некоторые из недостатков включают высокую стоимость и энергию для производства химического активатора, трудности и проблемы безопасности при работе с сильно щелочным раствором и необходимость контроля температуры во время процесса отверждения. Кроме того, утверждение строительных норм всегда является препятствием. В настоящее время наиболее многообещающими приложениями являются приложения в суровых условиях окружающей среды, такие как сборные железобетонные мосты, или другие специальные приложения, такие как среда с высокой кислотностью или высокой температурой, или для быстрого ремонта.
Фото: commons.wikimedia.org
Пример из практики: Институт глобальных изменений, Брисбен, Австралия
Институт глобальных изменений при Квинслендском университете, первое в Австралии здание с нейтральным выбросом углерода, был спроектирован с учетом высочайшего уровня устойчивости. Это одно из первых зданий, зарегистрированных для участия в конкурсе Living Building Challenge. Некоторые из особенностей зеленого здания включают в себя работающую солнцезащитную шторку, биоудерживающий бассейн, локальную систему серой воды, солнечную энергию и тепловую трубу.И это первое здание, в котором используется сборный железобетон из структурного геополимера, что значительно снижает углеродный след строительных материалов.
Ключом к коммерциализации геополимерного бетона будет разработка недорогих, простых в использовании активаторов. Одна многообещающая разработка находится в Университете Райса, где инженеры разработали геополимерный бетон, для которого требуется лишь небольшая часть активирующих химикатов на основе натрия, используемых в других геополимерных бетонах. По словам исследователей, они использовали сложные статистические методы для оптимизации стратегий смешивания ингредиентов.Это привело к оптимальному балансу летучей золы, богатой кальцием, нанокремнезема и оксида кальция с менее чем 5% традиционного активатора на основе натрия.
Заключение
Ежегодно в мире производится более 20 миллиардов тонн бетона. В результате на бетонные конструкции приходится около 5% мировых выбросов CO 2 , в основном за счет процесса производства цемента. Спрос на бетон, вероятно, будет продолжать расти по мере роста населения.Кроме того, требования к прочности, долговечности и технологичности будут продолжать расти. Сочетание традиционных и передовых технологий поможет удовлетворить эти новые требования. Такие технологии, как цемент TiO 2 , SCC, SCM и волокна, теперь используются в различной степени с выдающимися результатами. Улавливание и связывание углерода находятся в зачаточном состоянии, но имеют большие перспективы. Обогащение летучей золой поможет удовлетворить спрос на доступные, высокоэффективные бетоны, а геополимерные бетоны могут однажды помочь сделать бетон углеродно-нейтральным без ущерба для характеристик.
Пройдите тест и получите сертификат.