Производство газосиликатных блоков
Технология производства
Оборудование для производства стройматериалов сегодня играет важную роль, ведь от него зависит качество, надежность и долговечность сооружений. Рассмотрим полный цикл по производству газосиликатных блоков на заводе в Московской области.
Производство газосиликатных блоков основано на добавлении газообразователя в специально подготовленную смесь из молотого кварцевого песка, извести, небольшой части цемента. При взаимодействии газообразователя с известью структура смеси становится пористой. Процесс перемешивания происходит в смесеприготовительном цехе завода в специальных газобетоносмесителях.
Далее смесь поступает в формовочно-резательный цех, где происходит её заливка в формы и вспучивание. После вспучивания смеси она выдерживается на постах для того, чтобы материал приобрёл пластическую прочность сырца (0,15 – 0,04 МПа). Затем газосиликатные блоки производство переходит на резательный комплекс, где массивы разрезаются в поперечном и продольном направлениях.
Разрезанные массивы отправляются на пост комплектации, где они устанавливаются на специальные тележки и поступают в автоклав. После погрузки происходит тепловлажностная обработка материала, которая является заключительным этапом изготовления.
Область применения
Этот материал в основном применяется в малоэтажном строительстве. Газосиликатные блоки используются при возведении внутренних и наружных стен домов и подвалов, различных перегородок, при заполнении каркасных строительных конструкций. Поэтому оборудование для изготовления газобетона сильно востребовано на сегодняшний день.
Преимущества
Высокотехнологичное производство газосиликатных блоков обеспечивает строительный материал некоторыми преимуществами. Он хорошо поглощает звук и не горит. Кроме данных характеристик стройматериал имеет высокую прочность, показательную геометрию (т.е. линейные размеры стабильны не только конкретно в одной партии, но и в типоразмере всей продукции), низкие вес и теплопроводность.
Идентичные друг другу геометрические параметры блоков упрощают процесс кладки материала на клеевой состав при строительстве различных объектов. Их не нужно будет подгонять друг к другу. За счёт ровной поверхности газосиликатных блоков можно существенно экономить на строительных материалах. Помимо прочего, они просты в обработке (легко режутся, пилятся, строгаются, сверлятся).
Также этот материал не требует особого ухода. В экологическом плане он уступает дереву, но в отличие от него не гниёт и не горит.
Купить оборудование для производства блоков уже сегодня? С компанией МЕТЕМ это реально. А на все интересующие вас вопросы о цене наши специалисты подробно ответят вам по телефону.
Технические характеристики
- Масса – 400-600 кг/м3
- Показатель прочности – 10-50 кг/см3
- Теплопроводность – 0,12-0,14 Вт/м°C
- Морозостойкость – 25-35 циклов
Производство газосиликатных блоков: технология, оборудование (станок)
Для тех, кто ищет способ создать бизнес на дому, производство газосиликатных блоков станет выгодным решением. Сегодня вы познакомитесь с особенностями изготовления газосиликата и узнаете, как открыть такой бизнес.
Коды ОКВЭД, требуемые при регистрации ИП по данному виду деятельности: 26.61: Производство изделий из бетона для использования в строительстве; 26.66: Производство прочих изделий из бетона, гипса и цемента; 51.53: Оптовая торговля лесоматериалами, строительными материалами и санитарно-техническим оборудованием.
Содержание статьи:
Технические характеристики материала
Газосиликатные блоки – высококачественный строительный материал. Они отличаются низкой себестоимостью, экологически чистым производством и небольшим весом. Эти качества позволили материалу получить широкую популярность в строительной промышленности.
Блоки имеют высокую прочность, а благодаря ячеистой структуре, газосиликат может обладать плотностью от 300кг/м³ до 700кг/м³, равномерно распределенной по всему блоку, что так же увеличивает популярность этого товара среди строительных компаний.
Требования к производственному помещению
Помещение, отведенное под производство газосиликатных блоков своими руками, должно отвечать некоторым требованиям. Для хранения сырья и готовой продукции, понадобится специально отведенное место. Высота помещения должна составлять не менее трех метров.
Так же, тех. процесс предусматривает наличие электросетей напряжением 380В и 220В, водопровода и подъездных путей. Само помещение должно быть утепленным и очищенным от грязи и мусора.
Производство газосиликата считается безотходным, поэтому в канализации на территории мини-завода нет необходимости.
Оборудование для производства газосиликатных блоков
Чтобы организовать мини-завод в гараже или небольшом арендованном помещении, вам понадобятся следующие станки для производства газосиликатных блоков:
- Вибросито
- Автоклав промышленный;
- Формы для блоков;
- Шаровая мельница;
- Бункер-дозатор;
- Бетоносмеситель.
Цена оборудования
Где и по какой цене можно купить хорошее оборудование для производства газосиликата? Остановимся на этом вопросе поподробнее:
- Вибросито для просеивания песка. Подойдут недорогие варианты, занимающие мало места, такие как: вибросито ВО-1, производства Авер-Иркутск, мощностью 0,25 кВт – 320$, вибросито ВО-01, ООО «Строительное оборудование» — 370 долл., вибростол ВС-250, Строймашсервис-Дон – 575$, вариант без вибратора, Стройтехнополис – 125 долларов, машина от Элси-строй – 520$, ВИБРОМАШ ВО-1, Дельта-инжиниринг – 450 долларов;
- Шаровая мельница. Уралмаш МШЦ-210*3000 – 1740 долларов, Уралмаш МСЦ-3600*4500 – 1740$, мельница шаровая МШМП-0.8 – до 5750 долл., мельница от ЗАО Паритет сухого помола – 3710 долларов; ЗАО Паритет мокрого помола – 3310$;
- Дозаторы. Бункер — дозатор БД-30 от Златоустовского завода бетоносмесительного оборудования – 5750 долл., Бункер дозатор для бетоносмесителя от НПО КСК – 1130 долларов;
- Бетоносмеситель.
Варианты от компаний: Комплект-ЮГ – 90$, Б 130 «Энтузиаст» — 180 долл., Афалина Челябинск – 225 долларов, TOR 46л. От Торгового дома ТОР – 125$;
Формы. Металлические кассетные формы для ячеистого бетона из Красноярска, компания ГК ТСК – 185 долларов, Металлическая кассетная форма Строй механика Киров – 315$, форма «Стандарт-1», на 36 блоков – 350$;- Автоклав. Машина производства «УралЦентрКомплект» Аг-1200 тз – 43 550$, автоклав проходной АП 1,2 – 2*17, производства «Стройкомплекс Брик» — 26 135 долларов.
Чтобы купить качественный станок для производства газосиликатных блоков, придется тщательно выбирать подходящий именно вам вариант и сопоставлять их мощность и производительность.
Для сравнения цен и технических характеристик производственных машин, рекомендуется изучить и зарубежный рынок.
Особое внимание советуем обратить на технику из Китая. Такое оборудование для производства газосиликата отличает широкий ассортимент и доступная цена.
Технология производства газосиликатных блоков
Для производства, помимо оборудования, вам понадобится знание технологии изготовления и пропорции сырья.
Процесс производства газосиликатных блоков
Процесс довольно прост в исполнении. При соблюдении пропорций и правильном выполнении технологии, будет получен качественный продукт.
- С помощью вибросита отделить сыпучий материал от лишних фрагментов;
- Измельчить сырьё для производства газосиликатных блоков в шаровой мельнице;
- Соблюдая пропорции, смешать все сыпучие составляющие, кроме алюминиевой суспензии;
- Произвести повторное просеивание;
- Добавить алюминиевую пудру и воду, тщательно перемешать;
- Наполнить формы смесью на ½ от общего объема каждой из них;
- Оставить формы с массой при температуре не менее 40° на 2 часа;
- Обработать блоки с помощью автоклава;
- Оставить на 3 часа для завершения химических процессов и набора прочности.
Если вы хотите производить гозобетонные блоки в соответствии с межгосударственными стандартами, то ознакомьтесь с положениями ГОСТ 31360-2007, 21520-89, 25485–89, 31359, где описаны требования к стеновым неармированным изделиям из ячеистого бетона автоклавного твердения.
В продаже можно найти различные размеры газосиликатных блоков, но согласно ГОСТу 31360, размер каждого блока должен соответствовать следующим нормам: длинна – 625мм, ширина – 500 мм, высота – 500мм.
Пропорции ингредиентов для изготовления смеси
Рассмотрим, из чего делают газосиликатные блоки. Для производства 1 куб.м газосиликатной смеси понадобятся ингредиенты в следующих пропорциях: вода – около 450л., цемент – 60кг (от 8% до 10%), кварцевый песок – 450 кг (до 70%), гипс – 0,5 кг (до 2%), известь – 120 кг (процент извести вот 12% до 20%), а так же алюминиевая пудра – 0,5 кг (до 2%).
Чтобы достичь наибольшего показателя плотности материала, доля пор должна составлять не более 38%, такой строительный блок подходит для капитального строительства.
При среднем показателе плотности, газосиликат представляет собой материал, с долей пор не более 52%.
Наибольшая допустимая пористость легкого ячеистого материала составит до 92%. В последнем случае, применение газосиликатных блоков допустимо только для теплоизоляции.
Производство газосиликатных блоков в домашних условиях
Такое производство возможно, при наличии помещения, отвечающего соответствующим требованиям.
Блоки, изготовленные в домашних условиях, уступают по качеству товару, выпущенному на производственной линии.
Прежде всего, это обусловлено техническими характеристиками используемой техники. Но следует заметить, что газосиликат, произведенный небольшим частным заводом, пользуется не меньшим спросом, чем заводской, благодаря доступной цене и небольшой разнице в качестве строительного материала.
Подсчет рентабельности
Подсчитаем сроки окупаемости и прибыльность небольшого домашнего завода по производству газосиликатных строительных блоков.
Инвестиции
Вибросито – 450 долларов;
Шаровая мельница – 5 750$;
Бункер-дозатор для бетоносмесителя – 1 130 долл.;
Бетоносмеситель – 225 долларов;
Формы – 350$;
Автоклав – 26 135 долларов.
Итого: 34 040 долл.
Затраты на 1 кубометр сырья
Вода – 450л. – 0,6$;
Цемент – 60кг – 2,5 долл.;
Кварцевый песок – 450кг – 7,8 долларов;
Гипс – 0,5кг – 0,1$;
Известь – 120кг — 6,2 долл.;
Алюминиевая пудра – 0,5кг – 0,1$.
Итого: 17,3 долларов/1 куб. м.
Объем производства на нашем мини-заводе составит 1500 куб. м. в месяц, продажная цена 1м³ — 45$. При полной реализации, ежемесячный доход составит 67 500 долларов. Чистая прибыль – 24 250$ в месяц. С учетом сопровождающих изготовление и реализацию товара факторов, вложения в небольшой частный завод окупятся за 3 месяца работы.
Подведем итоги. Анализируя объем прибыли и срок окупаемости инвестиций, можно сказать, что газосиликатные блоки как бизнес, являются доходным предприятием с высоким коэффициентом рентабельности.
Понравилась статья? Поделитесь с друзьями:
производство и изготовление газобетонных блоков в Москве
Производственные мощности предприятия Bonolit располагаются на территории небольшого города Старая Купавна, находящегося в 22 км от Москвы. Производство современных строительных материалов из газобетона осуществляется на высокотехнологичном оборудовании компании HESS AAC Systems B.V. Автоклавный газобетон изготавливается по уникальной технологии, не имеющей аналогов у других российских производителей. Все технологические процессы производства автоматизированы и контролируются специалистами с высокой квалификацией.
Технология изготовления
При производстве газобетон проходит автоклавную обработку. Перед тем как поместить «зеленый массив» в автоклавы, блоки обязательно проходят специальное разделение, то есть в автоклав поступают уже разделенные, а не слипшиеся блоки. Такой метод позволяет избежать появления сколов и трещин на готовом газобетоне. Метод «разделения зеленого массива» обеспечивает равномерный процесс пропаривания материала, благодаря чему он получает однородность структуры и высокие механические характеристики. Поверхность изделий Bonolit хорошо контактирует с любыми отделочными материалами. Завершающей стадией при производстве газобетона является его упаковка в специальную пленку Stretch-hood, которая способствует сохранению целостности готовых изделий при хранении и транспортировке и обеспечивает дополнительное удобство при перевозке.
Виды газобетонных блоков
Вы можете выбрать и купить газоблоки для устройства различных конструкций.
Для несущих стен. Газобетон высокой прочности, имеющий плотность 300, 400 и 500 кг/м3, применяется для возведения несущих конструкций. Имея стандартные длину и высоту (600 и 2500 мм соответственно), блоки могут изготавливаться с различной шириной – от 200 до 500 мм. Стены из таких газобетонных блоков имеют хорошую несущую способность, качественную тепло- и звукоизоляцию и высокий коэффициент паропроницаемости.
Для внутренних перегородок. Для возведения перегородок можно использовать газобетон плотностью 500 и 600 кг/м3. Длина и высота изделий составляет 600 и 250 мм соответственно, а ширина находится в диапазоне от 500 до 175 мм. Перегородки из газосиликатных блоков имеют высокие звуко- и теплоизоляционные показатели, отличаются огнестойкостью.
Для арок.Для организации арочных проемов используют газобетонные блоки плотностью 500 и 600 кг/м3. Благодаря легкости обработки блоков из газобетона можно изготавливать арки различного радиуса.
Для перемычек. Усиление оконных и дверных проемов возможно с помощью газосиликатных П-образных блоков производства компании Bonolit с плотностью 500 кг/м3.
Для навесных фасадов. Для устройства вентилируемых фасадов компания Bonolit осуществляет производство газобетона плотностью 600 кг/м3, которые не подвергаются разрушению от воздействия влаги и перепадов температур, а также отличаются повышенной прочностью на вырыв. Размеры таких газосиликатных блоков – 600х250х200–500 мм.
Преимущества газоблоков Bonolit
Точность геометрии. Предельные отклонения в габаритах изделий, изготовленных на резательных линиях HESS, составляют не более +-1 мм.
Экологическая чистота. При изготовлении газобетона используются исключительно натуральные компоненты (гипс, песок, известь, цемент и вода) в соответствии с передовыми стандартами в области экологии. Компания Bonolit осуществляет безотходное производство. Цикл использования газобетона позволяет применять выделяемый пар для остальных рабочих процессов производства газобетона.
Высокий уровень качества. Контроль продукции Bonolit осуществляется на всех этапах ее изготовления – начиная от закупки качественного сырья и заканчивая высококачественной упаковкой. Производитель имеет собственную сертифицированную лабораторию, оснащенную современным оборудованием, для измерения и испытания газобетона Bonolit.
Долгий срок службы. При соблюдении требований к возведению домов из газосиликатных блоков срок их службы превышает 100 лет даже без дополнительной облицовки фасада.
Высокая теплоизоляция. Стены зданий, построенных из газосиликатных блоков от производителя Bonolit, обладают высокими способностями теплосбережения. Газобетон Bonolit 40 (плотностью 400 кг/м3 и шириной 400 мм) позволяет возводить дом в один ряд без дополнительного утепления.
Плотность (кг/м3) | 300 | 400 | 500 | 600 |
Класс прочности | B 1,5 | В 2,5 | В 3,5 | В 5 |
Теплопроводность (Вт/м*С) | 0,08 | 0,096 | 0,12 | 0,14 |
Паропроницаемость (мг/м*ч*Па) | 0,26 | 0,23 | 0,20 | 0,16 |
Морозостойкость | F75 | F75 | F75 | F75 |
Усадка при высыхании (мм/м) | 0,24 | 0,24 | 0,24 | 0,225 |
Огнестойкость | REI 240 |
Видеоролик о производстве газобетона на нашем сайте позволит Вам получить более полное представление о работе предприятия и наших технологиях. Чтобы купить газосиликатные блоки от производителя, можно оформить заказ на сайте либо связаться с нами по телефонам в Москве: +7 (495) 660-06-50, +7 (495) 660-06-51.
Как делают газосиликатные блоки
Сама технология изготовления газосиликатного блока была разработана достаточно давно — еще в начале прошлого века, в Швеции. Но лишь спустя десятилетия — ближе к концу 70-х, она получила широкое распространение благодаря набору уникальных свойств и характеристик, делающих данный материал востребованным на многих строительных площадках. При небольшом весе, газосиликат, поставляемый нашей компанией ООО СтройКА+, обладает одним из самых низких коэффициентов теплопроводности и исключительной экологической чистотой, что позволяет с успехом использовать его в строительстве любых типов помещений.
Состав материала
Основными компонентами для производства газосиликатных блоков служит известь, песок, цемент, алюминиевая пудра и вода. Данный состав отличается отменной экологической чистотой, так все составляющие являются чистыми природными материалами.
При смешивании всех компонентов образуется раствор, целиком состоящий практически из силикатной пены. Алюминиевая пудра запускает процесс пенообразования. Затем данный раствор в виде пены поступает в автоклавы, где под действием высокой температуры, пара и давления, он становится прочным. На выходе из автоклава образуется большой «брусок» готового газосиликата, который впоследствии нарезается на блоки определенной величины при помощи специального оборудования.
Непосредственно сам процесс производства блоков практически полностью автоматизирован. Высокотехнологичная линия управляет всеми этапами изготовления и следит за соотношением сырья, от которого в конечном итоге будет зависеть плотность газосиликатных блоков и их коэффициент теплопроводности. Например, при помощи специального оборудования на этой линии, можно легко регулировать величину получаемых пор и таким образом получать материал, имеющий различные свойства. Автоматизированный подход к производству исключающий «человеческий фактор» позволяет выпускать газосиликат всегда неизменно высокого качества.
При строительстве домов, львиная доля экономических затрат приходится на возведение стен и перегородок, а также на их утепление. Использование же газосиликатных блоков в качестве материала для стен — отличное решение особенно для индивидуального строительства, дающее значительную экономию, так как стены из газосиликата нужно лишь защитить от атмосферных воздействий без всякого утепления. Сделать это можно при помощи достаточно недорогих облицовок, например, таких как виниловый или металлический сайдинг, а также при помощи обыкновенной штукатурки. При таком подходе экономический эффект будет заметно ощутим, а кроме этого, благодаря большому размеру блоков — значительно сокращается время на строительство.
Производство газосиликатных блоков: оборудование, цены
Все большую популярность в качестве строительного материала в наши дни набирают газосиликатные блоки. Выбор в их пользу делают как частные лица, так и строительные компании. Основными причинами такого необыкновенного спроса являются надежность этого материала и экономическая выгода, обусловленная крайне низкой ценой на газосиликатные блоки и, весьма небольшими затратами при его использовании для строительства зданий. Кроме этого, они позволяют быстро и качественно организовать строительство дома из газосиликатных блоков своими руками.
Стоит отметить, что для разных случаев применения используются различные виды силикатных блоков:
- В качестве утеплителя используются блоки, плотность которых составляет 350 кг/м.
- Для строительства домов с тремя и менее этажами применяются блоки плотностью 400 кг/м.
- Выше трех этажей – 500 кг/м.
- Высокоэтажные сооружения строятся из блоков, плотность которых составляет 700 кг/м.
Фото: дом из газосиликатных блоков
Процесс изготовления блоков в заводских условиях
Газосиликатные блоки изготавливают в заводских условиях. Самые крупные и известные компании, выпускающие эти изделия, применяют самое совершенное оборудование для производства газосиликатных блоков, произведенное в Германии. Данные линии способны контролировать каждую стадию процесса изготовления блоков, начиная с самых первых этапов и заканчивая проверкой теплоизоляционных свойств готового изделия.
Что касается технологии, то здесь используются известь, вода, цемент и кварцевый песок, смешанные в строго определенных пропорциях. Кроме этого, для создания пористой структуры в смесь добавляется алюминиевая пудра, которая является образователем газа. Во время перемешивания происходит химическая реакция, приводящая к вспениванию смеси. Технологичная аппаратура способна даже регулировать диаметр этих пузырьков для получения пор нужного размера.
Производство газосиликатных блоков полностью автоматизировано, позволяет получать изделия максимально высокого качества с минимальным количеством брака.
Весь процесс изготовления газосиликатных блоков состоит из ряда последовательных этапов, для каждого из которых используется свое оборудование.
Система измельчения и дробления сыпучих материалов
В данной системе используется больше всего различного оборудования:
- Бункер для песка.
- Элеватор.
- Бункер для хранения извести.
- Хранилище для извести.
- Шаровая мельница.
- Электронные приборы для взвешивания порошка.
- Ленточный конвейер.
- Автоматический смеситель.
- Дробилка.
На данном этапе происходит перемешивание песка и воды до состояния жидкой смеси. Полученное вещество направляется в смесительное отделение. Там в него добавляются и остальные компоненты смеси в строго определенной пропорции и последовательности. После тщательного перемешивания добавляется алюминиевая суспензия и снова происходит перемешивание, которое контролируется электронными системами.
Заливка и дозирование
В этой системе используется следующее оборудование:
- Заливочная платформа.
- Система газораспределения.
- Заливочный смеситель.
Здесь происходит заливка смеси в формы и транспортировка в зону созревания. В течение нескольких часов происходит бурная реакция с выделением водорода и появляется необходимая пористая структура.
Резка и группировка
Используются:
- Захват для переворачивания.
- Машина для резки.
Полученный массив газосиликата разрезается с получением системы гребень-паз. Применяемое оборудование позволяет производить нарезку практически с ювелирной точностью. Самое интересное, что полученные после нарезки отходы можно отправлять на переработку и использовать в получении новой смеси. Это делает производство газосиликатов безотходным.
Набор прочности в автоклаве
Оборудование:
- Паровой котел.
- Рельсы.
- Автоклав.
В автоклаве нарезанные блоки набирают прочность путем постепенного выпаривания при высоком давлении. После этого давление уменьшается и блоки выезжают с платформы.
Упаковка
Используется следующее оборудование:
- Кран.
- Колодки.
- Приборы, замеряющие точность нарезки.
- Упаковочная линия.
С помощью крана происходит захват ряда блоков и выкладывание для дальнейшего остывания. Затем на автоматической линии происходит упаковка блоков. Одновременно с упаковкой происходит выписка документов, содержащих всю необходимую информацию об изделии.
В качестве примера можно сказать, что цена линии для изготовления газосиликатных блоков, производительностью 300 тыс. м3/год составляет примерно 900 тысяч долларов.
Конечно, можно изготавливать блоки и на более простом оборудовании, которое стоит дешевле, но и себестоимость такого производства будет значительно выше, что в некоторых случая попросту нецелесообразно.
Видео
Технология производства и срок службы газосиликатных блоков
Когда обычный рядовой житель большого города решает построить дом на своем участке и принимается за изучение вопросов, связанных с выбором строительных материалов, разновидностей фундамента, утепления стен и прочих немало важных нюансов – голова его идет кругом от всех тонкостей строительства, о которых новоиспеченный владелец будущего дома ни разу до этого и не задумывался. Не будучи профессионалом или, как минимум, не обратившись за помощью к профессионалу, сложно будет определиться с проектом дома, стройматериалом для его возведения, да и вообще лучшим местом на участке, предназначенном для строительства. Поэтому не стоит переоценивать свои возможности, считая, что все можно сделать самому, своими руками и при этом не хуже, чем любой другой строитель. Не стоит экономить на знаниях и опыте специалистов в своем деле, которые помогут воплотить в жизнь все Вами задуманное, при этом сделают это профессионально, качественно и довольно быстро. И тогда довольны будут все: и Вы, что теперь у Вас есть дом Вашей мечты, в котором с удовольствием хочется проводить как можно больше времени, и строительная фирма, за помощью к которой Вы обратились, будет удовлетворена своими результатами. Конечно, в интернете, да и во многих других источниках можно найти много полезной информации, различных статей о строительстве и многое другое. Но этого не достаточно для начала самостоятельного строительства, к примеру, дома.
Можно принять к сведению полезные советы по выбору строительных материалов или перенять опыт других строителей, которые зачастую делятся своими успехами на специализированных форумах. Но это только малая часть того, что вообще надо знать для того, чтобы что-то построить. Итак, в этой статье рассмотрим положительные качества такого строительного материала как газосиликатный блок. Начнем с того, что срок службы газосиликатных блоков сравним со сроком службы кирпича, а это, как минимум, заявленные 80 лет. Но если не нарушена технология кладки газосиликатных блоков и их последующая эксплуатация, то можно сказать, что они очень долговечны. Такой материал, как газосиликатные блоки, можно отнести к очень эффективным стройматериалам. Изначально технология производства газосиликатных блоков была открыта в Швеции, а затем, благодаря удачному сочетанию хороших качеств, газосиликатные блоки стали производить по всему миру. Процесс производства блоков уже давно поставлен на конвейер и человеческий фактор тут исключен.
Благодаря своим уникальным качествах и техническим характеристикам газосиликатный блок можно считать идеальным материалом для возведения различных построек. Теплопроводность газосиликатных блоков давно известна всем и благодаря этому свойству блоки плотностью до 500 кг/м3 успешно используют в качестве утеплителя.
Наша компания предлагает на Ваш выбор газосиликатные блоки разной плотности отечественного и импортного производства для использования в различных целях. У нас широкий диапазон типоразмеров по доступным ценам!
Производство газосиликатных блоков | Бизнес и оборудование
Усовершенствование строительных технологий и постоянная работа над улучшением свойств материала, позволили создать газосиликатную продукцию, которая имеет невысокую стоимость и пользуется высокой популярностью среди застройщиков.
Основной особенностью продукции, является размер блоков, они
существенно больше обычного размера шлакоблочного изделия, именно это позволяет
ускорить стройку.
Для производства газосиликатных блоков применяется:
- негашеная известь;
- портландцемент с кварцевым песком;
- алюминиевая пудра;
- вода;
- обязательным является добавление специальных модифицированных добавок, армирующих волокон и хлорида кальция. Эти компоненты ускоряют процессы затвердения.
Основным компонентом в производстве блоков, является использование алюминиевой пудры, провоцирующей возникновение химической реакции и приводящей к появлению силикатной пены.
Технология производства газосиликатных блоков:
- Просеивание заготовленного материала.
- Загрузка компонентов в смеситель. Добавление определенной части цемента, песка, извести, алюминиевой пудры и воды.
- Выполнение процесса смешивания.
- Разлив сырья по формам.
- Удаление излишков раствора.
- Сушка в автоклаве.
- Порезка материала на блоки.
Процесс производства
газосиликатных блоков заключается в смешивании сухих компонентов с водой до
получения однородного цвета. Пудра и негашеная известь, являются основными
элементами химической реакции, в результате которой образовываются пузырьки с
воздухом. Они делают материал пористым, снижая при этом удельный вес изделия.
После, готовый раствор распределяют по формам, именно здесь он продолжает увеличиваться в размере, за счет химической реакции. По истечению некоторого времени, излишки сырья срезают металлической струной, формы отправляют в автоклав.
Автоклавный метод сушки позволит улучшить свойства строительного материала за счет воздействия высоких температур и давления. Использование устройства позволяет добиться необходимого уровня влажности для создания однородной структуры.
Активная обработка продукции способствует образованию ячеистой структуры и повышению прочности материала. Газосиликатная продукция отличается от газобетона легкостью, плотностью, ровной формой изделия и лучшей экологичностью.
Допустимо твердение смеси в естественных условиях, но это
негативно скажется на эксплуатационных свойствах материала. Обеспечить максимальную
прочность способен только автоклав.
Виды готовой продукции:
- конструкционные блоки, используются для строительства капитальных конструкций;
- теплоизоляционно-конструкционный материал, предназначен для закладки перегородочных стен;
- теплоизоляционная продукция, необходима для утепления построек.
Оборудование для производства газосиликатных блоков:
- шаровые дробильные механизмы, дозаторы, дробилки, вибросито, бетоносмеситель и весы, необходимы для измельчения и очистки сырья;
- заливочный смеситель, разъемная опалубка, газораспределительная система, набор форм, нужны для замеса и распределения сырья;
- режущая рама и захваты, позволяют осуществить нарезку материала;
- автоклавы, предают прочности изделию;
- для упаковки продукции используется кран, устройство, определяющее габариты и несколько гидравлических колодок.
Чтобы организовать производство газосиликатных блоков в домашних условиях, нужно использовать специальное оборудование:
- смеситель, для качественного смешивания компонентов;
- формы, способные предать правильных геометрических размеров;
- металлическая струна, для устранения излишков смеси;
- автоклав.
Основными функциями смесителя, является автоматическое дозирование и смешивание компонентов. Он самостоятельно изготавливает раствор, существенно упростив и облегчив процесс производства.
Преимущества использования газосиликатной продукции:
- легкость материала;
- экологичность;
- высокая звукоизоляция и паропроницаемость;
- морозоустойчивость и теплоаккумулирование;
- обладание теплоизоляционными свойствами;
- увеличенные размеры материала;
- простота обработки, материал легко поддается нарезке.
Для создания мини-производства по изготовлению газосиликатной продукции, необходимо составить бизнес-план и приобрести специальное оборудование. При наличии постоянных клиентов, получится не только окупить производство в короткий срок, но и существенно расширить масштабы поставок для увеличения прибыли.
Republished by Blog Post Promoter
Пеносиликатный блок в современном домостроении.
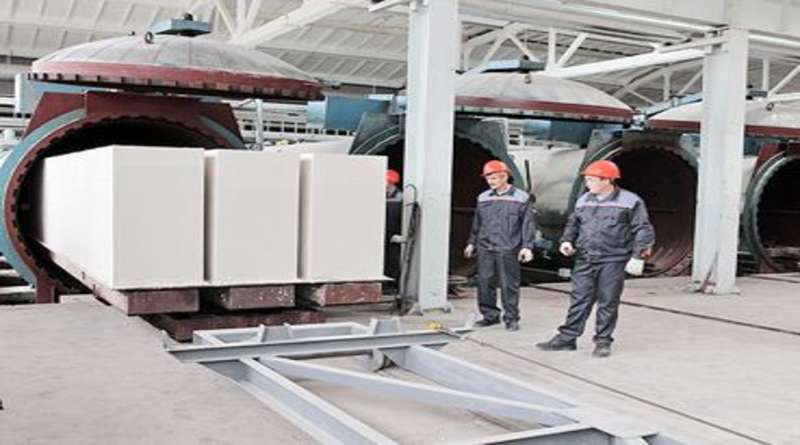
Что делать, если вы выбрали план дома из газобетонного блока? Вам необходимо иметь представление о материалах, из которых построен такой дом. Учтите все характеристики и свойства. Так дом будет теплоэффективным и прочным на долгие годы эксплуатации.
Газобетонные блоки различной формы
Заводы по производству газосиликатов оснащены высокотехнологичными линиями. Там все процессы автоматизированы и контролируются.Благодаря этому газоблок имеет точные параметры и характеристики
Тщательно перемешанная тестовая масса состоит из воды, цемента, кварцевого песка, извести, гипса и алюминиевой пудры. Эту массу разливают в большие формы для изготовления блоков.
Блоки выдерживают в специальных камерах 3-4 часа при 35 ° C. Здесь происходит реакция алюминия с известью. Эта реакция напоминает процесс брожения. Во время этого процесса масса выделяет водород, создавая пористую структуру.В процессе созревания объем блока увеличивается и приобретает прочность.
Автоклавная сушка пенобетона
Автоклавная сушка пенобетона
После разложения материал поступает на линию резки и боковой обработки. (если у будущего агрегата должна быть щелевая система захоронения). Очищается от бетонной крошки с помощью сжатого воздуха. Наш массив поступает в камеру автоклава. Он будет оставаться там в течение 12 часов под воздействием пара 180 ° C и давлением не менее 12 атмосфер.Готовые блоки через установленный срок отправляются в цех упаковки. Там их готовят к дальнейшему использованию.
Хочу отметить, что мелкие производители стеновых блоков не могут себе позволить такое производство. Так что качество газосиликатного блока неодинаково для всех производителей. Вам необходимо проверить сертификаты выбранного производителя и рекомендации по применению. Вы должны знать, какой клей наносить, по каким критериям прочности и влагопоглощения.
Хочу предостеречь от неповоротливости строителей при строительстве. Газовый блок хрупкий и требует осторожного обращения.
Подводя итог, дома из таких блоков достаточно теплые, но имеют свои нюансы. Например, при кладке нужно сделать арматуру. Фундамент должен быть коническим, с идеально ровной поверхностью. Его основание должно быть ниже глубины промерзания. Все внешние стены фасадными системами следует защищать от влаги и атмосферных осадков.
Если следовать рекомендациям по газоблочной технологии, ваш дом прослужит долго.При дальнейшем использовании проблем не возникнет.
Произошла ошибка при настройке пользовательского файла cookie
Этот сайт использует файлы cookie для повышения производительности. Если ваш браузер не принимает файлы cookie, вы не можете просматривать этот сайт.
Настройка вашего браузера для приема файлов cookie
Существует множество причин, по которым cookie не может быть установлен правильно. Ниже приведены наиболее частые причины:
- В вашем браузере отключены файлы cookie.
Вам необходимо сбросить настройки вашего браузера, чтобы он принимал файлы cookie, или чтобы спросить вас, хотите ли вы принимать файлы cookie.
- Ваш браузер спрашивает вас, хотите ли вы принимать файлы cookie, и вы отказались. Чтобы принять файлы cookie с этого сайта, используйте кнопку «Назад» и примите файлы cookie.
- Ваш браузер не поддерживает файлы cookie. Если вы подозреваете это, попробуйте другой браузер.
- Дата на вашем компьютере в прошлом. Если часы вашего компьютера показывают дату до 1 января 1970 г., браузер автоматически забудет файл cookie.Чтобы исправить это, установите правильное время и дату на своем компьютере.
- Вы установили приложение, которое отслеживает или блокирует установку файлов cookie. Вы должны отключить приложение при входе в систему или проконсультироваться с системным администратором.
Почему этому сайту требуются файлы cookie?
Этот сайт использует файлы cookie для повышения производительности, запоминая, что вы вошли в систему, когда переходите со страницы на страницу. Чтобы предоставить доступ без файлов cookie
потребует, чтобы сайт создавал новый сеанс для каждой посещаемой страницы, что замедляет работу системы до неприемлемого уровня.
Что сохраняется в файле cookie?
Этот сайт не хранит ничего, кроме автоматически сгенерированного идентификатора сеанса в cookie; никакая другая информация не фиксируется.
Как правило, в файлах cookie может храниться только информация, которую вы предоставляете, или выбор, который вы делаете при посещении веб-сайта. Например, сайт не может определить ваше имя электронной почты, пока вы не введете его. Разрешение веб-сайту создавать файлы cookie не дает этому или любому другому сайту доступа к остальной части вашего компьютера, и только сайт, который создал файл cookie, может его прочитать.
Произошла ошибка при настройке пользовательского файла cookie
Этот сайт использует файлы cookie для повышения производительности. Если ваш браузер не принимает файлы cookie, вы не можете просматривать этот сайт.
Настройка вашего браузера для приема файлов cookie
Существует множество причин, по которым cookie не может быть установлен правильно. Ниже приведены наиболее частые причины:
- В вашем браузере отключены файлы cookie. Вам необходимо сбросить настройки вашего браузера, чтобы он принимал файлы cookie, или чтобы спросить вас, хотите ли вы принимать файлы cookie.
- Ваш браузер спрашивает вас, хотите ли вы принимать файлы cookie, и вы отказались. Чтобы принять файлы cookie с этого сайта, используйте кнопку «Назад» и примите файлы cookie.
- Ваш браузер не поддерживает файлы cookie. Если вы подозреваете это, попробуйте другой браузер.
- Дата на вашем компьютере в прошлом. Если часы вашего компьютера показывают дату до 1 января 1970 г.,
браузер автоматически забудет файл cookie. Чтобы исправить это, установите правильное время и дату на своем компьютере.
- Вы установили приложение, которое отслеживает или блокирует установку файлов cookie. Вы должны отключить приложение при входе в систему или проконсультироваться с системным администратором.
Почему этому сайту требуются файлы cookie?
Этот сайт использует файлы cookie для повышения производительности, запоминая, что вы вошли в систему, когда переходите со страницы на страницу. Чтобы предоставить доступ без файлов cookie потребует, чтобы сайт создавал новый сеанс для каждой посещаемой страницы, что замедляет работу системы до неприемлемого уровня.
Что сохраняется в файле cookie?
Этот сайт не хранит ничего, кроме автоматически сгенерированного идентификатора сеанса в cookie; никакая другая информация не фиксируется.
Как правило, в файлах cookie может храниться только информация, которую вы предоставляете, или выбор, который вы делаете при посещении веб-сайта. Например, сайт
не может определить ваше имя электронной почты, пока вы не введете его. Разрешение веб-сайту создавать файлы cookie не дает этому или любому другому сайту доступа к
остальной части вашего компьютера, и только сайт, который создал файл cookie, может его прочитать.
Возможность сделать каждый блок на счету — Masonry Magazine
Технология в кладке
Скотт Биггар и Челси Код-Макнил
Технологический прогресс не ограничен — проведение исследований и разработок неизбежно ведет к открытиям, продвигающим вперед инновации. Компания CarbonCure Technologies не новичок в этом цикле. Технология компании началась, когда их генеральный директор Роберт Нивен начал исследовать химическую реакцию между углекислым газом (CO2), цементом и водой, когда получил степень магистра в Университете Макгилла в Монреале, Канада.
Это исследование позже стало основой для разработки CarbonCure в течение следующих восьми лет и превратилось в то, что сейчас является жизнеспособным решением для производителей бетона по переработке отработанного CO2 в их бетонных смесях.
Двуокись углерода, известный парниковый газ и способствующий изменению климата, быстро становится главной темой для строительной отрасли. Архитекторы и застройщики на протяжении десятилетий совершенствовали строительные системы и методы, чтобы снизить выбросы CO2, связанные с их зданиями.Однако этот подход затрагивает только один конец дымовой трубы, и разрабатываются новые технологии, позволяющие использовать CO2 для производства новых строительных материалов.
В основе технологии CarbonCure лежит химическая реакция, называемая минерализацией. Реакция происходит, когда CO2 вводится в процессе производства бетонных блоков (CMU). Газ CO2 вступает в реакцию с ионами кальция, содержащимися в цементе, и подвергается обратной реакции обжига (рис. 1), в результате чего образуется минерал карбонат кальция (известняк).
CMU, который поступает на объект, изготовленный с использованием технологии CarbonCure, имеет точно такие же физические свойства и внешний вид, что и традиционный CMU. Разница в том, что CMU CarbonCure забрал CO2 и удержал его внутри, откуда он больше не может быть выпущен. Поскольку газ был преобразован в карбонат кальция, он больше не влияет на изменение климата.
Дизайнеров и архитекторов постоянно просят приоритизировать свойства материалов, чтобы функционально оставаться верными мотивам своих клиентов.При рассмотрении использования КМУ в проекте в пользу материалов складывается множество свойств: долговечность, прочность, огнестойкость и тепловая масса. Все эти свойства материалов способствуют устойчивости здания, и с появлением стандарта LEED v4 вводятся новые меры для поощрения материалов, способных противостоять климатическим воздействиям.
Несмотря на материальные преимущества кирпичной кладки, в CMU есть один ингредиент, который несет значительный углеродный след: цемент. Строительная промышленность уже много лет знает о выбросах CO2 при производстве цемента и подталкивает производителей к поиску решений для уменьшения этого воздействия.
Там, где некоторые видят проблему в выбросе углекислого газа из бетона, CarbonCure рассматривает его как возможность для адаптивного повторного использования. Каждый блок — это возможность сохранить небольшое количество углерода, шанс сократить некоторые выбросы цементной промышленности и вернуть их в бетон.
Brampton Brick, производитель кирпичной кладки, ведущий свою деятельность на юге Онтарио, был одним из первых, кто применил технологию CarbonCure в Северной Америке, впервые заключив партнерские отношения с компанией в 2013 году. В сентябре 2015 года Brampton принял решение установить технологию еще на двух заводах. свои заводы, ссылаясь на желание начать производство всей своей продукции с переработанным CO2.
«Все, что мы производим сегодня, содержит CO2, — сказал Дэйв Картер, генеральный директор Brampton Brick. Он указывает на стандарты зеленого строительства, такие как LEED, как на движущие силы тенденции.
Рис. 2 — Пакетный оператор, использующий интерфейс HMI CarbonCure.
(любезно предоставлено CarbonCure Technologies)
Использование CMU в качестве емкости для хранения углерода не сильно увеличило общие затраты Brampton Brick и не изменило их производственную практику. Но Картер не рекламирует блоки с впрыском CO2 своей компании как серебряную пулю для бетонной промышленности.
«Это всего лишь часть головоломки», — сказал он, указав также на растущее использование в цементной и бетонной промышленности альтернативных видов топлива и материалов.
Добавление CarbonCure в состав смеси не влияет на вес, цвет и требования ASTM. С 2013 года CarbonCure установила свою технологию на 22 заводах в США и Канаде.
Разработчики и архитекторы из США начинают узнавать о перспективах хранения углерода в бетонных блоках. Kimco Realty, крупнейший в Северной Америке владелец и оператор торговых центров под открытым небом, недавно построила первый проект в Орегоне, в котором используется блок CarbonCure.Блок был изготовлен и поставлен компанией Mutual Materials, недавним партнером CarbonCure.
Рис. 3 — Строящаяся торговая точка Kimco. (Предоставлено Kimco Realty) |
Рис. 4 — CMU CarbonCure, предоставленный Mutual Materials. (Предоставлено Kimco Realty) |
«Добавление CarbonCure в наш проект Sunset Mall было довольно простым делом», — сказал Тим Хаманн, директор по строительству Kimco Realty.
В новом торговом центре разместятся два ресторана и магазин розничной торговли, строительство которых будет осуществлять компания Lanphere Construction and Development.
«У нашего генерального подрядчика и каменщиков не было никаких проблем с блоком», — сказал Хаманн. «Проект был выполнен так же, как и обычная кладка. Рециркуляция CO2 в этом проекте была как раз тем, что соответствовало целям Kimco в области устойчивого развития ».
Интеграция технологии CarbonCure в блочную установку также очень проста.После того, как производитель наладил поставку промышленного CO2 местного производства, инженеры CarbonCure устанавливают его оборудование и работают с группой контроля качества завода, чтобы интегрировать CO2 в свои бетонные смеси.
В эпоху, когда инновации имеют решающее значение как для окружающей среды, так и для устойчивости отрасли, производители бетона ищут способы улучшить как свои производственные процессы, так и брендинг своей компании. Добавление технологии CarbonCure обеспечивает небольшую, но новаторскую настройку существующих производственных операций, помогая ответить на глобальный призыв к решениям для хранения углерода.
Для получения дополнительной информации о технологии CarbonCure свяжитесь с Кристи Гэмбл, директором по продажам и маркетингу, по адресу [email protected].
Скотт Биггар — менеджер по устойчивому развитию, а Chelsea Code-McNeil — координатор по устойчивому развитию в компании CarbonCure Technologies.
Полезное использование диоксида углерода в производстве сборных железобетонных изделий (Технический отчет)
Шао, Исинь. Выгодное использование диоксида углерода в производстве сборных железобетонных изделий .
США: Н. П., 2014.
Интернет. DOI: 10,2172 / 1155035.
Шао, Исинь. Выгодное использование диоксида углерода в производстве сборных железобетонных изделий . Соединенные Штаты. https://doi.org/10.2172/1155035
Шао, Исинь.Чт.
«Полезное использование диоксида углерода в производстве сборных железобетонных изделий». Соединенные Штаты. https://doi.org/10.2172/1155035. https://www.osti.gov/servlets/purl/1155035.
@article {osti_1155035,
title = {Выгодное использование диоксида углерода в производстве сборного железобетона},
author = {Shao, Yixin},
abstractNote = {Изучена возможность использования углекислого газа в качестве сырья при производстве сборного железобетона. Двуокись углерода реагирует с соединениями кальция в бетоне, образуя твердые карбонаты кальция в связующей матрице. Два типичных сборных железобетона проверяются на их способность удерживать углекислый газ во время производства. Это бетонные блоки и фиброцементные панели. Эти два продукта в настоящее время производятся серийно и обрабатываются паром. Двуокись углерода можно использовать для замены пара в процессе отверждения для ускорения ранней прочности, повышения долговечности и снижения энергии и выбросов. Для реакции в течение 24-часового технологического окна теоретически максимально возможное поглощение углерода бетоном составляет 29% в расчете на массу цемента в продукте.Для достижения максимального поглощения разработан специальный процесс, повышающий эффективность реакции до 60-80% при 4-часовом отверждении диоксидом углерода и улучшающий устойчивость к циклическому замораживанию-оттаиванию и воздействию сульфат-ионов. Процесс также оптимизирован для достижения проектной цели по использованию углерода в размере 10 долларов за тонну CO2.
Используя самоконцентрирующуюся абсорбционную технологию, можно производить CO2 высокой чистоты по цене ниже 40 долларов за тонну. При использовании недорогих технологий улавливания и утилизации CO2 можно создать сеть для улавливания и утилизации углерода вблизи источников углерода.Если бы все блочные производители и производители панелей в Соединенных Штатах могли внедрить в свое производство углекислый газ вместо пара, использование углерода только на этих двух рынках могло бы потреблять более 2 Мт CO2 в год. Этот процесс улавливания и утилизации может быть распространен на большее количество сборных железобетонных изделий и будет продолжаться еще долгие годы.},
doi = {10.2172 / 1155035},
url = {https://www.osti.gov/biblio/1155035},
journal = {},
number =,
объем =,
place = {United States},
год = {2014},
месяц = {6}
}
во главе с профессором Калифорнийского университета в Лос-Анджелесе выигрывает 7 долларов.

Группа инженеров UCLA стала первой университетской командой, выигравшей главный приз в глобальном конкурсе NRG COSIA Carbon XPRIZE. Снижая углеродный след бетона, изобретение команды может в конечном итоге стать важным шагом в глобальной борьбе с изменением климата.
Команда CarbonBuilt из Калифорнийского университета в Лос-Анджелесе, возглавляемая Гауравом Сэнтом, профессором гражданской и экологической инженерии инженерной школы Самуэли Калифорнийского университета в Лос-Анджелесе, выиграла 7,5 миллионов долларов в конкурсе на технологии, связанные с выработкой электроэнергии на угле.
Технология-победитель представляет собой первый в своем роде экологически безопасный подход к улавливанию выбросов углекислого газа непосредственно от электростанций и других промышленных объектов — выбросов, которые в противном случае попадали бы в атмосферу — и внедрения их в новый тип бетона изобретена командой. По мере того, как он затвердевает и набирает прочность, специально разработанный бетон надолго поглощает и улавливает парниковые газы.
Благодаря обширным исследованиям в Калифорнийском университете в Лос-Анджелесе и испытаниям в Интегрированном испытательном центре, расположенном за пределами Джиллетта, штат Вайоминг, исследователи продемонстрировали, что их процесс снижает углеродный след бетона более чем на 50%, производя бетон, столь же прочный и долговечный традиционный материал.
В каждом бетонном блоке CarbonBuilt хранится около трех четвертей фунта углекислого газа — значительное количество, учитывая, что к 2027 году ежегодно будет производиться около 1 триллиона бетонных блоков.
Сант присоединился к преподавателям Калифорнийского университета в Лос-Анджелесе в 2010 году. Он и группа научных сотрудников, докторантов и докторантов начали исследования, которые привели к получению награды в 2014 году.
«Я очень рад, что CarbonBuilt выиграл NRG COSIA Carbon XPRIZE», — сказал Сант, который руководит Институтом углеродного менеджмента Калифорнийского университета в Лос-Анджелесе и занимает должность преподавателя в отделе материаловедения и инженерии Калифорнийского университета в Лос-Анджелесе.«Как инженер-строитель в третьем поколении, я был очарован той ролью, которую строительство сыграло в решении социальных проблем. Потратить последнее десятилетие на разработку решения по уменьшению углеродного следа бетона с феноменальной командой и выиграть NRG COSIA Carbon XPRIZE, сделав то, чем я увлечен, — это величайшая мечта ».
Конкурс NRG COSIA Carbon XPRIZE стоимостью 20 миллионов долларов, спонсируемый NRG Energy и Канадским альянсом по инновациям в нефтеносных песках, был объявлен в сентябре 2015 года, чтобы найти способы с пользой использовать выбросы диоксида углерода.Некоммерческая организация XPRIZE Foundation поставила перед мировым сообществом специалистов по решению проблем задачу разработать технологии для превращения углекислого газа из выбросов угольных и газовых электростанций в ценные продукты. Канадская команда под названием CarbonCure выиграла другой конкурс — производство электроэнергии на основе природного газа.
UCLA была одной из 47 заявок, поданных 38 командами из семи стран. CarbonBuilt, ранее известный как CO 2 Concrete, был назван одним из 10 финалистов в октябре 2017 года.
Сант сказал, что оригинальное вдохновение для технологии победы пришло из невероятного источника: морских ракушек.
«Ракушки сделаны из карбоната кальция, который является природным цементирующим веществом», — сказал он. «Нас действительно вдохновила идея того, как ракушки держатся вместе. Вот как мы на самом деле приступили к превращению углекислого газа в бетон ».
Столкнувшись с вызовом экспертов из академических кругов и промышленности, которые заявили, что это невозможно, Сант и его команда провели следующие семь лет, пытаясь доказать свою неправоту.
Инженерная школа имени Самуэли Калифорнийского университета в Лос-Анджелесе
Бетонные блоки CarbonBuilt сходят с производственной линии. Каждый бетонный блок CarbonBuilt хранит около трех четвертей фунта углекислого газа.
Сначала исследователи Калифорнийского университета в Лос-Анджелесе разработали новую формулу цемента, который является связующим веществом в бетоне. Они использовали гашеную известь или портландит, который может быстро поглощать углекислый газ, чтобы заменить традиционный силикатный цемент кальция, известный как обычный портландцемент.Затем команда разработала метод, при котором углекислый газ, взятый непосредственно из дымовых газов, быстро поглощается портландитом по мере затвердевания бетона.
В дополнение к абсорбции углекислого газа в бетон, процесс Reversa компании CarbonBuilt снижает количество обычного портландцемента, необходимого для производства бетона, на 60-90%. Процесс также происходит при обычных температурах и давлениях. В результате бетон CarbonBuilt имеет гораздо меньший углеродный след, чем обычный бетон.Это может иметь большое значение для сокращения выбросов парниковых газов в мире, поскольку производство традиционного цемента, используемого в бетоне, является причиной почти 9% мировых выбросов углекислого газа.
Еще одно неоспоримое преимущество новой технологии — ее экономичность. В отличие от других технологий снижения выбросов углерода, которые требуют дорогостоящей установки для улавливания выбросов углекислого газа или их очистки, процесс CarbonBuilt позволяет напрямую использовать углекислый газ в дымовых газах электростанций и промышленных предприятий и преобразовывать их у источника без этих дополнительных шагов.
«Это революционный момент для Калифорнийского университета в Лос-Анджелесе, а также для науки и техники», — сказал Джаяти Мурти, Рональд и Валери Шугар, декан UCLA Engineering. «Благодаря упорству и решимости Гаурав и его команда смогли превратить исследовательский проект в инновационную технологию, которая может решить реальную социальную проблему и привести к позитивным изменениям в мире».
Чтобы выйти в финал, исследователи Калифорнийского университета в Лос-Анджелесе продемонстрировали, что их технология может потреблять 135 килограммов (около 297 фунтов) углекислого газа за 24 часа. В 2017 году команда должна была соответствовать определенным техническим требованиям, подлежащим проверке независимой фирмой. Затем эти результаты были оценены группой экспертов-судей из академических кругов и промышленности, которые оценили количество углекислого газа, которое было преобразовано в бетон, изготовленный из углеродного волокна, а также инженерную, экологическую и экономическую ценность строительного материала.
Первоначально запланированный на февраль 2020 года финальный раунд конкурса был отложен из-за пандемии COVID-19.В июне 2020 года команда Калифорнийского университета в Лос-Анджелесе прибыла в Комплексный испытательный центр, чтобы продемонстрировать свою систему в промышленных масштабах. Демонстрация длилась четыре месяца и произвела почти 150 метрических тонн (более 330 000 фунтов) бетонных блоков CarbonBuilt. Некоторые из бетонных блоков были пожертвованы племени восточных шошонов для строительства жилья в резервации Винд Ривер в Форт Вашаки, штат Вайоминг.
Средства от награды NRG COSIA Carbon XPRIZE будут поддерживать инновационные исследования по снижению выбросов углерода и разработку технологий в UCLA Engineering.CarbonBuilt, частная компания, основанная Сэнтом, получила права на патентный портфель проекта, принадлежащий Калифорнийскому университету в Лос-Анджелесе, с целью коммерциализации технологии.
Инженерная школа имени Самуэли Калифорнийского университета в Лос-Анджелесе
Гаурав Сант: «Потратить последнее десятилетие на разработку решения по уменьшению углеродного следа бетона с феноменальной командой и выиграть NRG COSIA Carbon XPRIZE, сделав то, что я страстно увлечен, — это величайшая мечта».
Перед тем, как выиграть главный приз, команда собрала 10 миллионов долларов на разработку технологии CarbonBuilt.В дополнение к награде в размере долларов США в размере 500000 долларов США от фонда XPRIZE Foundation в 2018 году за выход в финал Сант получил грант в размере 1,8 миллиона долларов США в 2019 году от Министерства энергетики. (Дополнительное тестирование для завершения гранта Министерства энергетики США, недавно заключенного в Национальном центре улавливания углерода в Уилсонвилле, штат Алабама.) А Семейный фонд Энтони и Жанны Притцкер внес 1,5 миллиона долларов в 2017 году.
Многие преподаватели UCLA внесли свой вклад в успех команды, в том числе Данте Симонетти, доцент кафедры химической и биомолекулярной инженерии; Дж.Р. ДеШазо, профессор государственной политики, гражданского строительства и охраны окружающей среды и директор Центра инноваций UCLA Luskin; Лоран Пилон, профессор машиностроения, аэрокосмической техники и биоинженерии; Ричард Канер, выдающийся профессор химии и биохимии, материаловедения и инженерии; и Матье Боши, доцент кафедры гражданского строительства и охраны окружающей среды.
В состав дополнительных членов группы входят нынешние и бывшие ученые проекта UCLA Engineering Дейл Прентис, Габриэль Фальцоне, Иман Мехдипур и Бу Ван; Хюкмин Квеон, бывший научный сотрудник Калифорнийского университета в Лос-Анджелесе; Чжэньхуа Вэй, бывший докторант в области гражданского строительства и защиты окружающей среды; Камли Тран, исполнительный директор Института углеродного менеджмента; и опытных отраслевых консультантов, включая Эдварда Мюллера, Стивена Рааба и генерального директора CarbonBuilt Рахула Шендуре.
Силикат кальция — обзор
15.5 Гидравлические цементы
Портландцемент — это гидравлический цемент, получаемый путем измельчения клинкера, состоящего в основном из гидравлических силикатов кальция с сульфатом кальция (гипсом) в качестве добавки в грунт. Клинкер получают путем нагревания глинистых материалов с известью при высоких температурах (> 1500 ° C) с образованием конкреций (диаметром 5–25 мм). Низкая стоимость и широкая доступность известняка и природных источников кремнезема делают портландцемент одним из самых дешевых материалов, используемых во всем мире.Производство и состав портландцементов, процессы гидратации, а также химические и физические свойства цемента были тщательно изучены.
Портландцемент состоит в основном из извести (60–65 мас.% CaO), кремнезема (21–24 мас.% SiO 2 ), глинозема (3–8 мас.% Al 2 O 3 ) и оксид железа (3–8 мас.% Fe 2 O 3 ), но также содержит небольшие количества магнезии (0–2 мас. % MgO), триоксид серы (1–4 мас.% SO 3 ) и другие оксиды, представленные в виде примесей из сырья, используемого при его производстве.
Основными фазами, присутствующими в негидратированном портландцементе, являются алит (Ca 3 SiO 5 -силикат трикальция), белит (Ca 2 SiO 4 — β-дикальций силикат), алюминат (Ca 3 Al 2 O 6 — алюминат трикальция), феррит (Ca 4 (Al, Fe) 2 O 7 — алюмоферрит тетракальция).
В таблице 15.1 показаны составы и сокращения этих соединений.
Таблица 15.1. Основные соединения в портландцементе
Соединение | Оксидный состав | Аббревиатура | ||||||
---|---|---|---|---|---|---|---|---|
Силикат трикальция | 3CaO · SiO 2 | 9014 901 C D 9014 901 C D 9014 90 C · SiO 2C 2 S | ||||||
Алюминат трикальция | 3CaO · Al 2 O 3 | C 3 A | AlO4C6 | AlO-Alcrite | AlO2O4 O 3 · Fe 2 O 3 | C 4 AF |
Ранняя гидратация цемента в основном контролируется количеством и активностью C 3 A, сбалансированной количеством и вид сульфатной грунтовки с цементом. C 3 A быстро гидратирует и влияет на характеристики раннего склеивания. Аномальная гидратация C 3 A и плохой контроль его гидратации сульфатом могут привести к таким проблемам, как схватывание, потеря осадки и несовместимость цемент-добавка. На основе этой информации был разработан ряд цементов с различной прочностью или высокой начальной прочностью. Пять признанных типов портландцемента перечислены в Таблице 15.2. Типичные составы коммерческих портландцементов приведены в Таблице 15.3.
Таблица 15.2. Типы портландцемента и их применение
Тип цемента | Использование |
---|---|
I | Цемент общего назначения при отсутствии смягчающих условий |
II | Вспомогательные вещества, обеспечивающие умеренную устойчивость к сульфатам |
III | Когда требуется высокая и ранняя прочность |
IV | Когда требуется низкая теплота гидратации (в массивных конструкциях) |
V | Когда требуется высокая сульфатостойкость |
Таблица 15. 3. Состав (мас.%) Коммерческих портландцементов
Тип цемента | C 3 S | C 2 S | C 3 A | C 4 AF 90s325 | ||||
---|---|---|---|---|---|---|---|---|
I | 50 | 24 | 11 | 8 | 7 | |||
II | 42 | 33 | 5 | 13 | 13 | 9 | 8 | 10 |
IV | 26 | 50 | 5 | 12 | 7 | |||
V | 9014 9014409 | 7 |
Тип I, называемый нормальным портландцементом или обычным портландцементом (OPC), наиболее часто используется, когда особые свойства других типов не требуются, например Например, когда он не подвержен сульфатному воздействию отходов или когда тепло, выделяемое при гидратации цемента, не вызывает неприемлемого повышения температуры. Цементы типа I обычно имеют прочность на сжатие (раздавливание) через 7 дней> 19 МПа, измеренную на 50-миллиметровых кубиках раствора.
Тип II, модифицированный портландцемент с пониженным содержанием C 3 S и C 3 A, имеет более низкую скорость гидратации, чем тип I, и медленнее выделяет тепло. Он также обладает повышенной устойчивостью к воздействию сульфатов и предназначен для использования там, где важны дополнительные меры предосторожности против умеренного воздействия сульфатов.
Тип III, высокопрочный цемент с высоким содержанием C 3 S и более низким уровнем C 2 S, быстро набирает прочность благодаря высокому содержанию трикальцийалюмината и трикальцийсиликата.Однако такое быстрое нарастание прочности сопровождается высокой скоростью выделения тепла, что может препятствовать использованию цемента типа III для массивных монолитов из отходов / цемента.
Тип IV, низкотемпературный цемент с низким содержанием C 3 S и C 3 A и, следовательно, высоким уровнем C 2 S, может использоваться в первую очередь для массивных отходов / цементных монолитов. Низкая скорость тепловыделения в этом типе цемента объясняется высоким содержанием силиката дикальция и соответствующим низким содержанием силиката трикальция и алюмината трикальция.
Тип V — сульфатостойкий цемент из-за низкого содержания трикальцийалюмината. Это специальный цемент, предназначенный для использования в монолитах, подвергающихся сильному воздействию сульфатов. Он имеет более медленную скорость набора прочности, чем обычный портландцемент.
Портландцемент типов I, II и III обычно используется для иммобилизации радиоактивных отходов. В то время как тип II обладает повышенной устойчивостью к воздействию сульфата, растворы сульфата натрия успешно затвердевают, причем все три типа имеют примерно одинаковые нагрузки.Водные отходы, содержащие борную кислоту, могут затвердеть, если в цемент добавить щелочной материал (например, гашеную известь или NaOH) или силикат натрия, а также при увеличении щелочности раствора до pH 8–12. Было показано, что типы I, II и III работают с такими добавками.