Как сделать деталь, напечатанную на 3D-принтере, более прочной
Как нам всем хорошо известно, детали, напечатанные на обычном домашнем 3D-принтере, получаются не такими прочными и служат не так долго, как оригинальные. Мы подумали, что было бы здорово научиться как-нибудь укреплять напечатанные детали, и немного над этой идеей поработали.
Такие более прочные детали позволят нам использовать их в реальном деле, при высокой нагрузке. Тогда, вместо того чтобы искать оригинальные детали на замену сломавшимся в гаджетах, роботах, машинах, механических игрушках или для любого разрабатываемого проекта, мы сможем просто напечатать их.
Необходимость в разработке такого руководства возникла у автора тогда, когда он купил на eBay велосипедные подвесные сумки. Одну для подруги, другую для себя. Крепление сумок подразумевало, что руль имеет толщину в один дюйм (2,54 см), и едва подходило к женскому велику. Руль же мужского велосипеда имел диаметр 3,15 мм, и на него крепление не налезало.
Поэтому появилась мысль изготовить деталь по размеру соответствующего крепления, напечатав ее на 3D-принтере.
Шаг 1. Требующаяся деталь
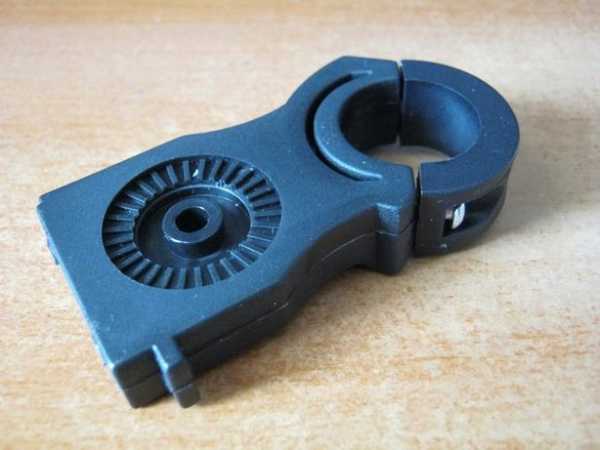

Вот узел, который нужно воспроизвести на 3D-принтере.
Чтобы что-то напечатать, для начала требуются файлы 3D-модели. Их, соответственно, нужно найти и скачать в интернете или же разработать самостоятельно. Второй вариант представлялся единственно возможным, поскольку готовых 3D-моделей для такой специфической детали найти невозможно, и нужно было модифицировать ту, которая имелась, так, чтобы она налезала на руль.
Однако всем прекрасно известно, что напечатанные на 3D-принтере детали прочностью не отличаются. Напечатанный обычным способом данный узел получился бы не настолько прочным, чтобы надежно держать тяжелую сумку на тряской дороге. Тогда возникла мысль как-то укрепить эту деталь, придав ей достаточно прочности.
Автор несколько лет занимался судомоделированием и имел возможность убедиться, насколько слои стекловолокна и эпоксидки делают более крепкими даже тонкие фанерные детали, в результате чего они без проблем выдерживают высокие нагрузки.
Поэтому и в данной работе было решено задействовать стекловолокно и эпоксидный клей-смолу.
Первоначально планировалось снять чертеж детали, внести необходимые изменения по размерам и покрыть все стекловолоконной тканью с эпоксидным клеем. Итак, приступим к моделированию.
Шаг 2. Проект первый
Деталь должна быть такой. Все размеры подогнаны, всё в целом увеличено и утолщено. Увеличены и поверхности, чтобы на них можно было наклеить стекловолокно.
Кроме того, на каждой из сторон предусмотрены желобки, чтобы заполнить их эпоксидкой для придания еще большей прочности. Смоделированы также сквозные отверстия, чтобы части узла было проще соединять друг с другом и чтобы стекловолокно и смола соединяли их изнутри.
Деталь напечатана на принтере Up и проверена на предмет того, подходит ли она по размерам.
Тип заполнения выбран решетчатый, что позволило оставить достаточно пустого пространства внутри детали. В обычной ситуации это уменьшает прочность, но сделано это было сознательно. В детали просверлено еще несколько отверстий, чтобы позволить эпоксидному клею проникнуть внутрь и укрепить ее.
Шаг 3. Нанесение стекловолокна и эпоксидного клея на первый проект
Это самая грязная часть работы. С эпоксидкой и стекловолокном работать сложно. Всё везде липнет так, что потом почти не отмоешь.
Сначала полоски стекловолоконной ткани были наклеены на обе половинки детали, чтобы они лучше скреплялись.
Затем всё было выложено на кусок нейлона, поскольку эпоксидная смола, к счастью, к нейлону прилипает не так смертельно. После этого эпоксидка была нанесена на поверхность детали, вырезан соответствующей формы и размера кусок стекловолоконной ткани, поверх которой был опять-таки нанесен эпоксидный клей. Клея было столько, что стекловолокно стало прозрачным.
Вся эта процедура повторилась для другой стороны детали, после чего смола день застывала. Даже немного больше, чтобы всё скрепилось намертво.
Шаг 4. Еще эпоксидки для дополнительного укрепления с боков
Решено было также добавить еще эпоксидного клея в специально предусмотренные для этого торцевые бороздки.
Шаг 5. Проект второй
При разработке первого проекта имелось в виду, что деталь через просверленные в ней дополнительные отверстия будет частично заполнена эпоксидной смолой, а снаружи ее будет держать пропитанное эпоксидкой стекловолокно. В процессе печати первой детали родилась идея смоделировать только ее оболочку, а внутри все вообще сделать только из эпоксидного клея и стекловолокна.
И вот, пока первый проект застывал, решено было приступить к моделированию второго. Хотелось сравнить оба варианта в плане прочности и легкости в изготовлении. Во втором проекте в заполнении двух фрагментов детали (для крепления нужно две части) был использован различный подход.
На фото видно, что второй проект – это пустая оболочка со стенками в 1 мм толщиной. Округлый фрагмент отделен от большего, чтобы упростить процесс заполнения. Его нужно потом, когда эпоксидка будет застывать, закрепить винтами.
Шаг 6. Заполнение второго проекта эпоксидкой и оптоволокном
Для начала было мелкими кусочками нарезано стекловолокно, и получившимися клочьями обе части детали заполнены чуть больше, чем наполовину. Затем нужно по каплям добавлять эпоксидный клей и немного придавливать обрезки, чтобы они хорошо пропитывались.
Шаг 7. Заполняем дальше проект 2. Фрагмент 1
Продолжаем капать и утаптывать, пока вся стеклоткань не пропитается, после чего добавляем еще обрезков стеклоткани, повторяя этот шаг до окончательного заполнения детали. Теперь закрепим винтами второй фрагмент детали. В конце концов уровень смеси эпоксидки и стекловолокна должен быть до краев.
Почти то же самое для меньшего, округлого фрагмента.
Шаг 8. Заполняем проект 2. Фрагмент 2
Для этого фрагмента применен несколько другой подход: деталь не заполнялась с самого начала наполовину. На дно был уложен только один слой стеклоткани, затем еще один – с перехлестом на края. Эти слои пропитывались эпоксидкой до тех пор, пока не стали полностью прозрачными, после чего на них один за другим укладывались и придавливались, чтобы впитали клей, следующие слои. Немного эпоксидки добавлялось через каждые 2-3 слоя.
Первый способ давал нам деталь, внутри которой больше эпоксидной смолы и чуть меньше стекловолоконной ткани. При втором способе в детали больше стекловолокна и меньше эпоксидки между слоями.
Шаг 9. Теперь всё должно застыть
Периодически детали проверялись, в образующиеся при впитывания смолы пустоты добавлялось еще смолы. Где надо, добавлялось стекловолокна. На полное застывание ушел примерно день. В продаже есть эпоксидные клеи, которые застывают быстрее, можно также добавить больше отвердителя, чтобы ускорить процесс. Мы, однако, этого не рекомендуем, потому что это только осложнит работу и будет мешать клею проникнуть во все углы.
Шаг 10. Сборка готового узла
Шаг 11. Удаляем пластиковые части
Этот шаг на самом деле не предусматривался. Предполагалось просто использовать напечатанные на 3D-принтере и укрепленные детали. Но когда дело дошло до ошкуривания, напечатанная «кожица» просто стала отламываться по углам, остальное тоже снималось без проблем. «Кожица» эта никакой дополнительной прочности не давала, поэтому и была практически полностью снята, и деталь стала композитной эпоксидно-стекловолоконной.
Шаг 12. Итоги
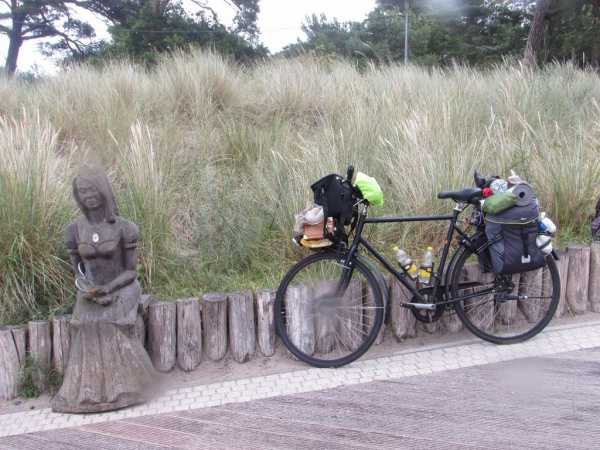
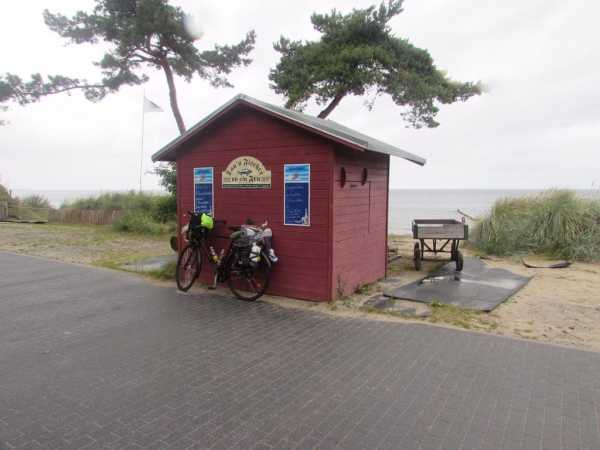
Деталь без проблем продержалась во время 20-дневной поездки по Швеции, Польше, Германии и Дании. Передняя сумка было все время до отказа заполнена едой, было пройдено немало ухабистых дорог. Детали прослужили на отлично и по-прежнему крепче камня.
Вот еще несколько полезных замечаний.
- Интересно, что эпоксидка не очень хорошо прилипает к ABS. Именно поэтому дополнительные отверстия, через которые она будет проникать внутрь и скреплять конструкцию, просто обязательны.
- Укреплять деталь снаружи гораздо сложнее, чем заполнять ее. Времени на первый вариант уходит масса, но заполненная деталь получается легче. Бесспорно, укрепленная деталь значительно прочнее, чем просто напечатанная и не укрепленная. Это легко проверить, если испытать на скручивание укрепленную и не укрепленную детали. Укрепленная подобна камню, обычная легко меняет форму.
- Второй метод укрепления гораздо проще и дает гораздо более опрятный результат. После застывания смолы почти ничего не надо чистить. А то, что получилось, имеет крепость гранита!
- Оба варианта заполнения при различных количествах стекловолокна дают одинаковое ощущение прочности и массивности. Однако тот, где волокна больше, теоретически и почти без сомнений должен выдерживать больший вес.
- По второму проекту узел получается более тяжелым, поскольку внутри он полностью состоит из стекловолокна и эпоксидной смолы. Вес немного уменьшается после удаления окружающего пластика. При этом, впрочем, изменятся и размеры детали. Поэтому о размерах нужно подумать заблаговременно и учесть снятие пластика при моделировании.
- Во втором проекте тоже можно предусмотреть желобки-бороздки и пустоты, тогда вес удастся снизить.
Перевод статьи Strengthening a 3D Printed Part с сайта Instructables.com
3dpt.ru
Как производится печать деталей на 3d принтере
Технология 3D печати была разработана еще в прошлом столетии. Однако до настоящего времени она применялась лишь в промышленности. 3D принтер может воссоздать любой трехмерный объект, детали и даже целое здание, дом. Первый дом созданный по этой технологии находиться в Дубае. Дом строится менее чем за сутки по данной технологии. Принтер с каждым годом совершенствуются, и разрабатываются такие модели, которые могли бы воссоздать органы, имплантаты и протезы, а также еду.
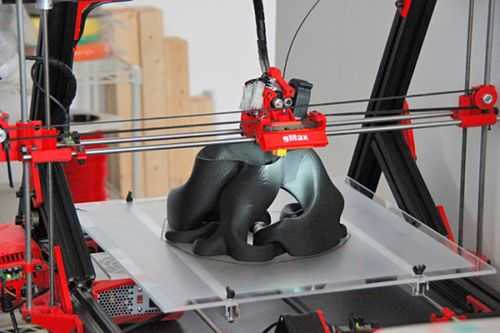
Технология 3D печати FDM
О чём пойдет речь:
Процедура проектирования и печати
Для начала необходимо спроектировать 3d модели для печати на 3d принтере. Есть специальная программа, с помощью которой можно спроектировать любой объект, любой формы и цвета. Затем нужно переходить к обработке модели, то есть к преобразованию ее в цифровой код, с помощью генератора G-кода. Именно с такого кода принтер считывает информацию о том, как распределить материал. Цифровой код представляет собой изображение, состоящее из многочисленных горизонтальных линий или штрихов. Как показано на фото. Далее осуществляется печать обработанной модели.
Принципы осуществления печати общие для всех моделей 3D принтера, но особенности печати у разных моделей 3D принтера могут отличаться. Принцип работы заключается в том, что головка осуществляющий печать перемещается по плоскости и наносит материал согласно созданной в программе модели. После нанесения одного слоя, платформа, на которой создается объект, снижается на толщину первого слоя, после этого наносится следующий слой, и платформа снова снижается на величину равную толщине слоя, и так продолжается до создания полноценной трехмерной модели.
Особенности печати
Для каждого принтера существуют определенные технологии печати. Самыми популярными методами печати являются FDM и SLA.
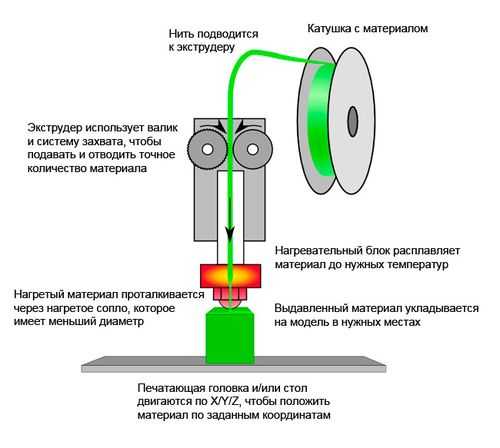
FDM печать
Первый метод основан на технологии плавления специальной нити. Осуществляется следующим образом, по контуру модели накладывается специальная нить и плавиться, создавая нужную форму. Для этой технологии печати используются синтетические материалы как пластик, полиамид, нейлон поликарбонат и другую синтетику. Эти материалы выпускаются в виде катушек нити.
Кстати, при изготовлении пластиковых бутылок используется эта же технология. Приобрести материалы для принтера можно онлайн через компании, предоставляющие услуги по поставке.
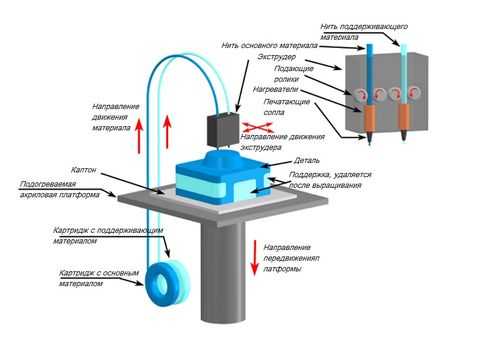
Схема технологии FDM
3D принтер, осуществляющий печать по такой технологии работает по принципу и алгоритму. Нить помешается в специальный контейнер, в котором она плавиться под воздействием температуры.
А затем выдавливается на платформу. Контейнер с нитью перемещается по определенной траектории, надавливая слой за слоем. Если модель сложная используются два материала, один для основы, другой для модели. Первый предназначен для опоры, при создании объектов с отдельными или повисшими элементами. То есть, принтер сначала создает основу, а затем на ней воссоздает отдельные детали.
Второй метод основан на использовании для печати, в качестве основного материала фотополимерные смолы. Изначально они находятся в жидком состоянии, но затем застывают под воздействием лазера. Эта технология позволяет создать объекты с очень маленькой толщиной. Печать формируется следующим образом. Если в первом методе платформа снижалась на толщину одного слоя, то здесь предусмотрена немного другая процедура.
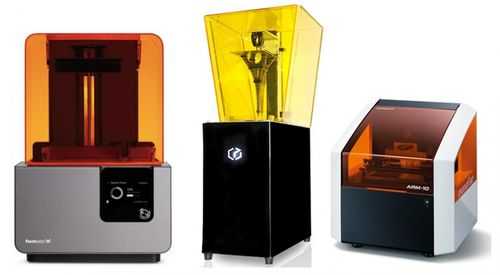
SLA печать
То есть, платформа погружается в контейнер с жидкой фотополимерной смолой, после каждого слоя на величину равную толщине. Затем с помощью лазера вырезается объект. И после завершения объект погружают в специальные растворы, чтобы очистить от пыли и остатков.
Печать деталей из металла и пластика
Как уже было упомянуто выше, технологии печати 3D применяются для изготовления деталей из любых доступных материалов, в том числе пластика и металла. Чтобы осуществить печать деталей на 3d принтере, помимо самого принтера и материалов необходимы определенные навыки, и ознакомиться с технологией.
Но если нет возможности сделать это самостоятельно, то можно обратиться в специальные фирмы, которые предоставляют услуги по изготовлению металлических или пластиковых деталей. Практически все фирмы реализуют свои услуги через Интернет, и таким образом можно заказать необходимую деталь или запчасти, не выходя из дома. В анкете указываются все данные о будущем объекте, а услуги оплачиваются любым удобным способом.
Для ознакомления с технологией 3d печати можно посмотреть видео, или пошаговую инструкцию с фото.
3d печать металлом
Технология 3d печати стремительно набирает популярность не только среди юридических лиц, осуществляющих массовое производство деталей, но и рядовых потребителей. Они приобретают принтер для себя, чтобы создавать объекты для дома, личного пользования, игрушек, сувениров и других целей, не исключено и создание малого бизнеса по изготовлению деталей по заказу. Почему люди стремятся приобрести принтер, использующие металл для создания объектов?
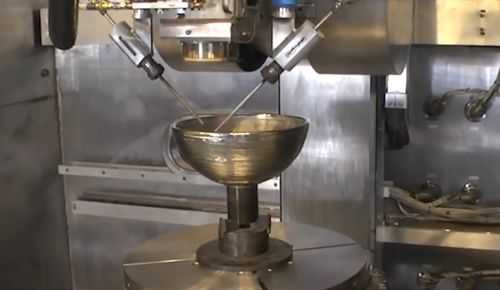
Печать металлом
Печать металлом на 3d принтере может сэкономить расходы и время на приобретение, и поиск нужной детали или запчасти для авто, или имплантатов, а также многое другое.
Металл, который применяется в 3D принтерах, уступает настоящему только прочностью. То есть, детали из металла имеют свойство подвергаться коррозии до определенной степени. Однако обычное железо при этом может заржаветь полностью, а этот нет. Металл для 3d принтера применяется в виде порошка. Технология печати металлом также осуществляется по слоям. Некоторые производители вело запчастей, также применяют 3d технологии, и оказывают услуги по их реализации.
Применение 3d принтера и печать деталей из пластика
Каждый человек может сделать 3d печать дома на 3d принтере. Технология очень простая, программа для проектирования модели доступна всем без исключения.
Применить 3d технологию можно в целях создания макетов, или копий реальных зданий или оригинальных архитектурных сооружений или оказывать услуги.
Что касается стоимости принтеров, принтеры которые осуществляют печать из пластика, может приобрести любой человек. Пластик самый доступный и дешевый материал, а изготовить из него можно практически все, начиная от игрушек и кончая посудой. Более того, пластик можно декорировать и покрасить при желании, или же подобрать по текстуре и цвету из широкого разнообразия, в отличие, например, от других материалов как металл.
printergid.ru
Печать автозапчастей на 3D принтере как бизнес: пошаговое руковдство
Добавлено в закладки: 0
Как открыть печать автозапчастей на 3D принтере
Еще недавно 3D принтер казался фантастикой. А сегодня им активно пользуются во всем мире. Существует множество технологий печати с использованием различных материалов. 3D принтер нашел свое применение в самых различных областях: от печати протезов и имплантов до производства самых различных конструкторских элементов и деталей разного размера и сложности. 3D печать активно используется автоконцерном Ford для изготовления как песчано-полимерных литейных форм, так таких сложных изделий как головка блока цилиндров или впускных и выпускных систем. Давайте рассмотрим печать автозапчастей на 3D принтере как выгодный современный бизнес.
На видео: Печать автозапчастей на 3D принтере
Печать автозапчастей на 3D принтере позволяет достичь высокой точности изготовления изделий, при этом сам процесс относительно не сложный. А именно это необходимо при производстве автозапчастей. Производство деталей с помощью такого принтера требует наличие знаний технологий производства и всех принципов работы продукта, а также необходимого программного обеспечения. Помимо этого необходимы квалифицированные специалисты.
Давайте же подробнее разберемся, что такое 3D печать, какие существуют технологии и как наладить производство автомобильных запчастей на 3D принтере.
Какие существуют технологии 3D печати?
На сегодняшний день существует достаточно много технологий, позволяющих изготавливать изделия на 3D принтере. Все они построены на принципе послойного создания объекта.
Технологии производства запасных частей на авто с помощью 3D печати
Лазерная стереолитография
Изделие формируется из о жидкого фотополимера,который твердеет под воздействием излучения, которое формирует объект слой за слоем. Селективное лазерное спекание. При использовании этой технологии объект создается из порошкового материала (это может быть пластик или металл), который плавится под воздействием лазера, а сам процесс протекает в бескислородной среде.
Электронно-лучевая плавка
В этом случае электронным лучом плавится металлический порошок, а процесс проходит в вакууме. Эту технологию используют для создания крупногабаритных моделей из тугоплавких металлов.
Моделирование методом наплавления
Для формирования объекта послойно укладывают нити из пластика, металла или воска.
Метод многоструйного моделирования
Используется струйная печать.
Изготовление объектов с использованием ламинирования
Изделие формируется путем послойного склеивания пленочного материала, каждый слой которого режут лазером или лезвием.
3D Printing (3DP)
Технология похожа на технологию селективного лазерного спекания, но в этом случае плавление не используется, а объект создается путём склеивания из порошкового материала, при использовании струйной печати. Данная технология используется при цветном моделировании – при печати в клей добавляют краситель.
Материалы, с которыми работает 3D принтер
Приняв решение о производстве автомобильных деталей, вы должны определиться, из каких материалов будете их создавать. В настоящее время на рынке существует множество устройств, печатающих изделия из различных материалов. На схеме представлены виды сырья и их свойства, а также сфера применения.
Самое сложное в 3D печати – создание компьютерной модели детали. А принтер сам воссоздаст изделие по эскизу из имеющегося сырья.
Преимущества и недостатки 3D печати автозапчастей
Как и в любом деле, здесь существуют проблемы и трудности, которые стоит учитывать:
- Не любое изделие вы можете напечатать. И материалы подходят не для всех деталей. Прием посетителей всегда должен вести грамотный специалист-консультант. Иногда вам все-таки придется отказывать клиенту.
- Небольшие «домашние» 3D принтеры могут иметь недостаточное расширение. Часто изделие будет пребывать дополнительной доработки.
- Технология цветной печати изделий пока не находится на должном уровне. Цвета не всегда яркие и точные. Но ведь это не главное в автозапчастях?
- Достаточно высокая стоимость как самого принтера, так и чернил. Также необходимо будет иметь на производстве дополнительные инструменты для некоторой корректировки – их вам тоже придется включить в себестоимость производства.
Однако, если вы настроены серьезно, трудности вас не испугают. Ведь печать автозапчастей на 3D принтере дело интересное и перспективное. Время идет, наука развивается. Создаются и совершенствуются технологии. А это значит, что со временем вы получите еще больше возможностей для развития своего бизнеса.
На видео: Бизнес на печати запчастей на принтере 3D
Изготовление автозапчастей на 3D принтере
Если вы решили создать мастерскую по печати 3D принтере, то рекомендуем вам попробовать печатать автозапчасти. В нашей стране огромное количество автомобилей. И практически каждый автолюбитель сталкивался с ситуацией, когда нужную деталь необходимо заказывать и долго ждать, даже если деталь достаточно простая.
Производство изделия состоит из двух фаз:
- создание макета
- сама печать.
Макет создается в специальной программе, а со временем, макеты накопятся и эту фазу вы будет все чаще пропускать. Преимуществом 3D печати изделий является точность, простота и универсальность. Ведь можно печатать самые разные детали, а также фрагменты корпуса.
biznes-prost.ru
Как сделать деталь, напечатанную на 3D-принтере, более прочной: 3d_tutorials
Как нам всем хорошо известно, детали, напечатанные на обычном домашнем 3D-принтере, получаются не такими прочными и служат не так долго, как оригинальные. Мы подумали, что было бы здорово научиться как-нибудь укреплять напечатанные детали, и немного над этой идеей поработали.
Такие более прочные детали позволят нам использовать их в реальном деле, при высокой нагрузке. Тогда, вместо того чтобы искать оригинальные детали на замену сломавшимся в гаджетах, роботах, машинах, механических игрушках или для любого разрабатываемого проекта, мы сможем просто напечатать их.
Необходимость в разработке такого руководства возникла у автора тогда, когда он купил на eBay велосипедные подвесные сумки. Одну для подруги, другую для себя. Крепление сумок подразумевало, что руль имеет толщину в один дюйм (2,54 см), и едва подходило к женскому велику. Руль же мужского велосипеда имел диаметр 3,15 мм, и на него крепление не налезало.
Поэтому появилась мысль изготовить деталь по размеру соответствующего крепления, напечатав ее на 3D-принтере.
Шаг 1. Требующаяся деталь
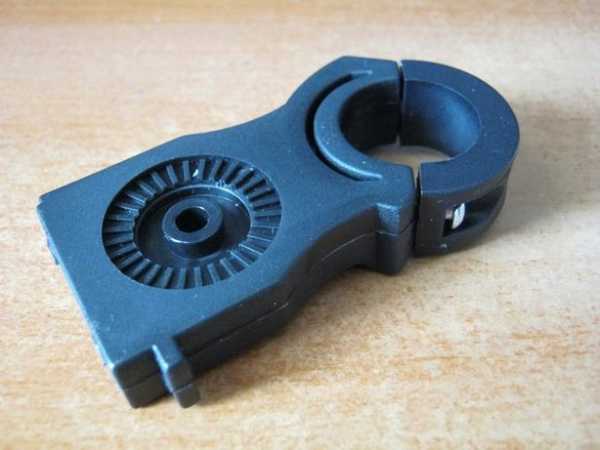
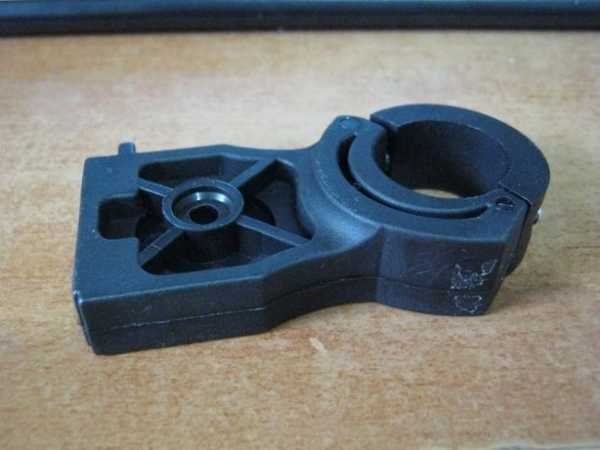
Вот узел, который нужно воспроизвести на 3D-принтере.
Чтобы что-то напечатать, для начала требуются файлы 3D-модели. Их, соответственно, нужно найти и скачать в интернете или же разработать самостоятельно. Второй вариант представлялся единственно возможным, поскольку готовых 3D-моделей для такой специфической детали найти невозможно, и нужно было модифицировать ту, которая имелась, так, чтобы она налезала на руль.
Однако всем прекрасно известно, что напечатанные на 3D-принтере детали прочностью не отличаются. Напечатанный обычным способом данный узел получился бы не настолько прочным, чтобы надежно держать тяжелую сумку на тряской дороге. Тогда возникла мысль как-то укрепить эту деталь, придав ей достаточно прочности.
Автор несколько лет занимался судомоделированием и имел возможность убедиться, насколько слои стекловолокна и эпоксидки делают более крепкими даже тонкие фанерные детали, в результате чего они без проблем выдерживают высокие нагрузки.
Поэтому и в данной работе было решено задействовать стекловолокно и эпоксидный клей-смолу.
Первоначально планировалось снять чертеж детали, внести необходимые изменения по размерам и покрыть все стекловолоконной тканью с эпоксидным клеем. Итак, приступим к моделированию.
Шаг 2. Проект первый
Деталь должна быть такой. Все размеры подогнаны, всё в целом увеличено и утолщено. Увеличены и поверхности, чтобы на них можно было наклеить стекловолокно.
Кроме того, на каждой из сторон предусмотрены желобки, чтобы заполнить их эпоксидкой для придания еще большей прочности. Смоделированы также сквозные отверстия, чтобы части узла было проще соединять друг с другом и чтобы стекловолокно и смола соединяли их изнутри.
Деталь напечатана на принтере Up и проверена на предмет того, подходит ли она по размерам.
Тип заполнения выбран решетчатый, что позволило оставить достаточно пустого пространства внутри детали. В обычной ситуации это уменьшает прочность, но сделано это было сознательно. В детали просверлено еще несколько отверстий, чтобы позволить эпоксидному клею проникнуть внутрь и укрепить ее.
Шаг 3. Нанесение стекловолокна и эпоксидного клея на первый проект
Это самая грязная часть работы. С эпоксидкой и стекловолокном работать сложно. Всё везде липнет так, что потом почти не отмоешь.
Сначала полоски стекловолоконной ткани были наклеены на обе половинки детали, чтобы они лучше скреплялись.
Затем всё было выложено на кусок нейлона, поскольку эпоксидная смола, к счастью, к нейлону прилипает не так смертельно. После этого эпоксидка была нанесена на поверхность детали, вырезан соответствующей формы и размера кусок стекловолоконной ткани, поверх которой был опять-таки нанесен эпоксидный клей. Клея было столько, что стекловолокно стало прозрачным.
Вся эта процедура повторилась для другой стороны детали, после чего смола день застывала. Даже немного больше, чтобы всё скрепилось намертво.
Шаг 4. Еще эпоксидки для дополнительного укрепления с боков
Решено было также добавить еще эпоксидного клея в специально предусмотренные для этого торцевые бороздки.
Шаг 5. Проект второй
При разработке первого проекта имелось в виду, что деталь через просверленные в ней дополнительные отверстия будет частично заполнена эпоксидной смолой, а снаружи ее будет держать пропитанное эпоксидкой стекловолокно. В процессе печати первой детали родилась идея смоделировать только ее оболочку, а внутри все вообще сделать только из эпоксидного клея и стекловолокна.
И вот, пока первый проект застывал, решено было приступить к моделированию второго. Хотелось сравнить оба варианта в плане прочности и легкости в изготовлении. Во втором проекте в заполнении двух фрагментов детали (для крепления нужно две части) был использован различный подход.
На фото видно, что второй проект – это пустая оболочка со стенками в 1 мм толщиной. Округлый фрагмент отделен от большего, чтобы упростить процесс заполнения. Его нужно потом, когда эпоксидка будет застывать, закрепить винтами.
Шаг 6. Заполнение второго проекта эпоксидкой и оптоволокном
Для начала было мелкими кусочками нарезано стекловолокно, и получившимися клочьями обе части детали заполнены чуть больше, чем наполовину. Затем нужно по каплям добавлять эпоксидный клей и немного придавливать обрезки, чтобы они хорошо пропитывались.
Шаг 7. Заполняем дальше проект 2. Фрагмент 1
Продолжаем капать и утаптывать, пока вся стеклоткань не пропитается, после чего добавляем еще обрезков стеклоткани, повторяя этот шаг до окончательного заполнения детали. Теперь закрепим винтами второй фрагмент детали. В конце концов уровень смеси эпоксидки и стекловолокна должен быть до краев.
Почти то же самое для меньшего, округлого фрагмента.
Шаг 8. Заполняем проект 2. Фрагмент 2
Для этого фрагмента применен несколько другой подход: деталь не заполнялась с самого начала наполовину. На дно был уложен только один слой стеклоткани, затем еще один – с перехлестом на края. Эти слои пропитывались эпоксидкой до тех пор, пока не стали полностью прозрачными, после чего на них один за другим укладывались и придавливались, чтобы впитали клей, следующие слои. Немного эпоксидки добавлялось через каждые 2-3 слоя.
Первый способ давал нам деталь, внутри которой больше эпоксидной смолы и чуть меньше стекловолоконной ткани. При втором способе в детали больше стекловолокна и меньше эпоксидки между слоями.
Шаг 9. Теперь всё должно застыть
Периодически детали проверялись, в образующиеся при впитывания смолы пустоты добавлялось еще смолы. Где надо, добавлялось стекловолокна. На полное застывание ушел примерно день. В продаже есть эпоксидные клеи, которые застывают быстрее, можно также добавить больше отвердителя, чтобы ускорить процесс. Мы, однако, этого не рекомендуем, потому что это только осложнит работу и будет мешать клею проникнуть во все углы.
Шаг 10. Сборка готового узла
Детали получились довольно неплохими, особенно по второму проекту. Крепление их на сумку прошло без проблем. Подошли отлично. Теперь нужно закрепить сумку на велосипед.
Шаг 11. Удаляем пластиковые части
Этот шаг на самом деле не предусматривался. Предполагалось просто использовать напечатанные на 3D-принтере и укрепленные детали. Но когда дело дошло до ошкуривания, напечатанная «кожица» просто стала отламываться по углам, остальное тоже снималось без проблем. «Кожица» эта никакой дополнительной прочности не давала, поэтому и была практически полностью снята, и деталь стала композитной эпоксидно-стекловолоконной.
Шаг 12. Итоги
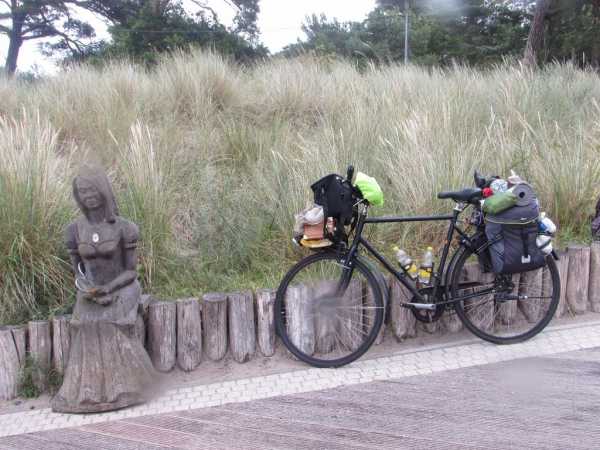
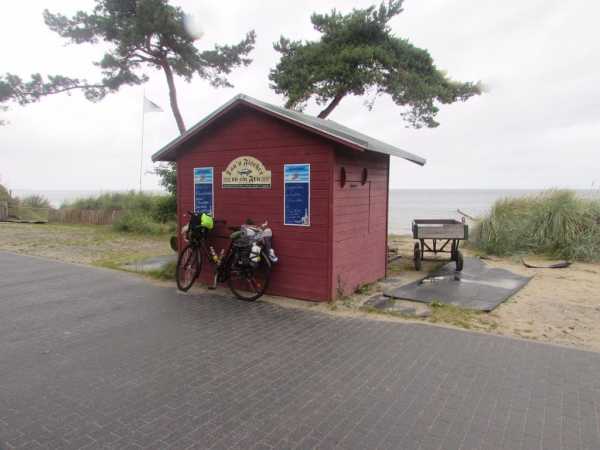
Деталь без проблем продержалась во время 20-дневной поездки по Швеции, Польше, Германии и Дании. Передняя сумка было все время до отказа заполнена едой, было пройдено немало ухабистых дорог. Детали прослужили на отлично и по-прежнему крепче камня.
Вот еще несколько полезных замечаний.
- Интересно, что эпоксидка не очень хорошо прилипает к ABS. Именно поэтому дополнительные отверстия, через которые она будет проникать внутрь и скреплять конструкцию, просто обязательны.
- Укреплять деталь снаружи гораздо сложнее, чем заполнять ее. Времени на первый вариант уходит масса, но заполненная деталь получается легче. Бесспорно, укрепленная деталь значительно прочнее, чем просто напечатанная и не укрепленная. Это легко проверить, если испытать на скручивание укрепленную и не укрепленную детали. Укрепленная подобна камню, обычная легко меняет форму.
- Второй метод укрепления гораздо проще и дает гораздо более опрятный результат. После застывания смолы почти ничего не надо чистить. А то, что получилось, имеет крепость гранита!
- Оба варианта заполнения при различных количествах стекловолокна дают одинаковое ощущение прочности и массивности. Однако тот, где волокна больше, теоретически и почти без сомнений должен выдерживать больший вес.
- По второму проекту узел получается более тяжелым, поскольку внутри он полностью состоит из стекловолокна и эпоксидной смолы. Вес немного уменьшается после удаления окружающего пластика. При этом, впрочем, изменятся и размеры детали. Поэтому о размерах нужно подумать заблаговременно и учесть снятие пластика при моделировании.
- Во втором проекте тоже можно предусмотреть желобки-бороздки и пустоты, тогда вес удастся снизить.
Перевод статьи Strengthening a 3D Printed Part с сайта Instructables.com
3d-tutorials.livejournal.com
Печать на 3D принтере сложных деталей из пластиков ABS и PLA с большим количеством поддержки
Доброго времени суток с вами компания 3Dtool! Часто возникают ситуации, когда необходимо напечатать геометрически сложную деталь на 3D принтере с одним экструдером например Hercules Strong, которую как не крути, а без поддержек не напечатать. Вариант – порезать на части и склеить в контексте этого поста рассматривать не будем.У одного из наших заказчиков возникли сложности в подготовке, печати и постобработке детали (см. ниже). Сверху на картинке –лицевая сторона, внутренняя сторона (вторая картинка) печатается с поддержками.
Сложность 3D печати заключается в том, что поддержки с черновой стороны детали удалить практически невозможно, они либо удаляются с кусками детали, либо первые слои детали провисают над поддержками и печатаются не ровно.
Загружаем деталь в Slic3r.
Располагаем деталь таким образом для того, чтобы верхняя часть панели получилась в хорошем качестве. Также нам важно качество боковых внешних стенок. Внутренняя часть панели — черновая, поэтому выстраиваем поддержки во внутренней части.
Идем в Print settings → Support materials и включаем поддержки.
Получается, что вся деталь держится на поддержках, и удалить их будет очень сложно. На фото результат печати нашего заказчика. Именно он подкинул нам эту интересную задачу. Время печати 4,5 часа.
Отделить поддержки удалось с большим трудом плоскогубцами. Внутренняя поверхность в очень плохом качестве, обработать ее невозможно.
Стандартные настройки в данном случае с задачей не справились. Поэтому будем настраивать Slic3r вручную.
Для того, чтобы поддержки легко удалились и внутренняя часть панели получилась в допустимом качестве, нужно изменить некоторые параметры:
Заходим в раздел Support Material
1. Уменьшить ширину экструзии на поддержках. Сетка поддержки будет печататься тонкими нитями, похожими на паутину. Их легко удалить руками и в то же время их прочности вполне хватает, чтобы удержать первые слои детали.
Меняем настройки в Advanced → Extrusion width → Support material–0.35 мм.
2. Для того, чтобы нити первого слоя детали, который будет печататься над поддержкой, не провисли, нам нужно, чтобы сетка поддержки была плотной, т. е. шаг необходимо сделать минимум 1 мм. Этот параметр называется Pattern Spacing. Это расстояние в миллиметрах между нитями поддержки. Если мы укажем там небольшое расстояние, печать поддержек займет очень много времени. Поэтому мы сделаем таким образом: будем печатать поддержку с шагом в 3 мм, а последние 2 слоя поддержки напечатаем с нужным нам шагом в 1 мм, эти слои будут поддерживать первые слои детали и шаг в 1 мм не даст нитям провиснуть. Это существенно сэкономит время. Меняем настройки:
Pattern spacing –3 mm -печатаем поддержку с шагом в 3 мм
Interface layers –2, Interface pattern spacing–1 mm – задаем двум слоям между деталью и поддержкой печатать линии с шагом в 1 мм.
3. Contact Z distance укажем 0. Первый слой детали будет печататься вплотную к поддержке, поэтому он будет ровнее. А уменьшение ширины экструзии позволит нам без проблем удалить поддержку с поверхности детали.
4. Идем в раздел Speed. Для того, чтобы нити поддержки из-за сниженной экструзии не обрывались, снижаем скорость для Support material до 40 мм/с и Interface support material до 30 мм/с.
Скорость для сплошных слоев, тех самых, которые будут печататься поверх поддержки, снижаем до 50%. Делаем это для того, чтобы слои на поддержку легли ровнее и нить не обрывалась.
Speed → Solid Infill – 50%
Сохраняем G-code и печатаем.
Смотрим результат.
Зеленый PLA Esun и кремовый ABS Esun. Печаталось на Hercules Strong соплом 0,5 мм, высота слоя 0,2 мм. Время печати 6,5 часа PLA и почти 7 часов ABS.
Основная часть поддержки легко отделилась руками, нити двух слоев между деталью и поддержкой мы удалили канцелярским ножом и тонкой плоской отверткой. Поверхности над поддержками получились ровные, без обрывов и провисаний нитей.
Данный метод позволяет печатать сложные детали с большим количеством поддержки. Время печати будет увеличиваться в зависимости от настроек Slic3r-а, которые в свою очередь будут зависеть от сложности детали, типа пластика и желаемого результата. В нашем случае время печати увеличилось почти на 40%.
Как показали эксперименты, ширину экструзии на поддержке возможно уменьшать до 40% от диаметра сопла, чем меньше это значение, тем легче будет отделить поддержку, но тем больше вероятность, что экструзия будет срываться и первые слои детали лягут неровно или не удержатся на поддержке. Также не стоит забывать о физических свойствах пластика: для ABS пластика мы уменьшали скорость печати поддержки до 30 мм/с, иначе экструзия срывалась. PLA пластик хорошо тянется, в отличии от ABS, и печатался на скорости 40мм/с без срывов. Поэтому все перечисленные параметры могут варьироваться в каждом конкретном случае.
Каталог 3D принтеров
Не забывайте подписываться на наш YouTube канал (новые ролики выходят каждую неделю).
habr.com
Технология 3d печати больших деталей
Нашел интересную статью о том, как печатать ABS пластиком большие детали без изгиба и отлипания детали. Основная проблема при печати больших деталей в том, что они изгибаются. Происходит это из-за того, что напечатав первый слой, проходит относительно много времени, прежде чем принтер преступит к печати второго слоя. Это приводит к остыванию первого слоя. Пластик немного сжимается в размерах, но этого недостаточно для искривления всей детали и отлипания от подложки.
Затем, принтер печатает второй слой по «усохшемуся» первому слою. Это приводит к еще большему напряжению первого слоя. Далее печатается третий слой по «усохшемуся» второму слою. Каждый последующий слой добавляет напряжение в детали. И как результат — она изгибается дугой и отлипает.
Далее, я расскажу, как автор статьи решил эту проблему:
Он сделал очень простую вещь — основание детали представляет собой полоски длиной и шириной порядка 1-2см, не более, и высотой пару миллиметров. Т.е. деталь как бы стоит на сваях
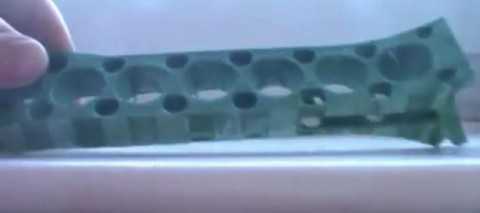
3d печать без изгиба детали
Во всей детали он делает отверстия таким образом, что бы самый длинный слой оказался длиной 1-2см. Вот как это выглядит:
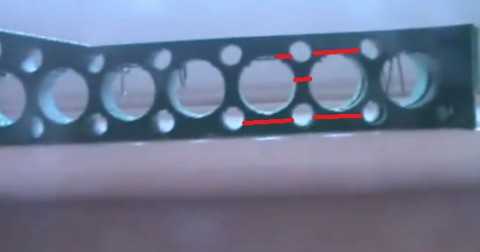
Деталь без искривлений
Красными линиями я показал, что любой слой, так или иначе прерывается специальными отверстиями.
Здесь кажется, что основание детали цельное, но это не так. Посмотрите видео и вы все поймете:
Результаты впечатляют.
Да, не везде можно применить такой метод. Но самое главное — это рабочая технология 🙂
diylife.ru
Основы 3D-моделирования для 3D-печати / Habr
3D-модель, которая в дальнейшем будет распечатана на 3D-принтере отличается от 3D-модели, разработанной для литья или фрезерования. Связано это с техническими особенностями 3D-принтера, из которых нужно либо выжать максимум пользы, либо подстроиться под недостатки печати.Из оговорок, отмечу, что данные рекомендации относятся в основном к методу 3D-печати FDM(FFF), при котором пластиковый пруток топится подвижным экструдером, формирующим деталь слой за слоем.
Разработка 3D-модели начинается с создания эскиза. Это может быть рисунок на бумаге, материальный прототип, мысленный образ и пр. На что важно обратить внимание при создании такого эскиза и самой модели разберем подробно.
Прочность детали
Здесь и дальше по тексту есть несколько подпунктов, которые необходимо учитывать одновременно, держать в голове с самого начала.
- Помнить про слоистость или анизотропность материала: сломать деталь по слоям гораздо проще, чем поперек. Это нужно учитывать заранее, задавшись расположением 3D-модели на столе 3D-принтера.
- Добавлять скругления. Ножка табуретки и столешница в месте стыка должны иметь скругленный угол. При этом, чем больше радиус скругления, тем прочнее ножка будет закреплена на столешнице. Аналогично для различных корпусных деталей. Моделируем коробку? Все прямые углы скругляем. При этом неважно, в какой они плоскости. Даже там, где нужен прямой угол, делаем радиус 0,5 мм. Принтер легче пройдет такой участок, чем нескругленный, не будет удара от резкой остановки экструдера, деталь не покачнется и прочие плюсы.
- Толщина стенок и заполнение. Максимальная прочность при 100% заполнении — это факт, но если нужно облегчить деталь или сэкономить пластик, можно сделать в настройках печати гораздо большую толщину стенки, при этом заполнение выставить гораздо ниже. Это работает с деталями, имеющими отверстия под крепеж. При создании машинного кода для принтера абсолютно все внешние стенки толстые, поэтому крепеж будет окружен надежным толстым слоем пластика вашей детали.
- Поддержка. Данный элемент влияет на прочность тем, что не всегда слои, опирающиеся на поддержку, идеальны по структуре. Это можно решать увеличением толщины стенки, заполнением, но лучше поддержку вообще не делать. Поддержка добавляется слайсером в зависимости от угла между стенкой детали и плоскостью стола. Часто по умолчанию стоит 60 градусов, иногда 45. Этот параметр подбирается экспериментально для каждого 3D-принтера. Проверить это можно с помощью специальных тестовых деталей. Например, https://www.thingiverse.com/thing:2806295 — не забудьте выключить поддержку, чтобы проверить реальное качество 3D-печати в её отсутствии. Например, вам нужно напечатать Т-образный соединитель для трубок. Литые изделия делают Т-образной формы. 3D-печать заставляет делать изделие L или даже Λ-образным. Во втором случае можно даже избежать поддержки, а деталь будет прочнее из-за слоев, расположенных под углом 45 градусов к трубкам. Мы, в мастерской настроили слайсеры для каждой машины и спрашиваем клиента о прочностных требованиях, и, в зависимости от этого, выбираем 3D-принтер для печати.
Геометрические ограничения
- Толщина стенки ограничивается снизу размером сопла 3D-принтера. Его диаметр постоянный и в подавляющем большинстве случаев равен 0,4 мм. Меньшая толщина — долгая 3D-печать для большинства деталей. Больше сопло — менее прочны связи между слоями, сильнее видны ступеньки между слоями. И вообще, толщина стенки должна быть кратна 0,4 мм, тогда 3D-принтер сможет аккуратно сделать стенку за два прохода (0,8мм), за 3 прохода (1,2 мм) и т.д. Другие толщины заставят 3D-принтер оставить пробел или перелив, что негативно влияет на прочность и внешний вид напечатанной детали.
- 3D-Печать тонких цилиндров и «иголок». Для 3D-печати таких изделий нужны особые настройки 3D-принтера: низкая скорость 3D-печати, давать время на остывание, иначе такая структура будет гнуться. Вертикально стоящих тонких элементов лучше избегать всеми силами. Даже если они будут напечатаны, то будут очень хрупкими. Их имеет смысл оставлять только для декоративных целей, но надо быть готовым, что их качество будет хуже качества других элементов 3D-детали.
- 3D-Печать отверстий. Замечу, что если отверстие прямое и сквозное, то его можно рассверлить, если оно изогнутое и требует поддержки, то может получиться так, что достать поддержку будет невозможно.
- При 3D-моделировании важно учитывать габаритные размеры 3D-принтера. Мы используем удобные 3D-принтеры, стол 250х250 мм, диагональ 353 мм. Вот сюда и нужно вписывать габариты, по возможности. Иначе надо заказывать либо промышленный 3D-принтер с большой зоной печати, либо использовать склейку, но лучше сборку, так процесс сборки будет контролируем разработчиком, а не мастером 3D-печати.
- Большая площадь основания может повлечь за собой отклеивающиеся от стола края. Мы используем специальный клей, но и это не всегда помогает. К нам периодически обращаются с жалобой на коллег по цеху, что для них такие «мелкие» дефекты, как загнутый край не является причиной для перезапуска 3D-печати, забирайте как есть. Но инженер, который 3D-моделирует деталь, может и сам это учитывать в работе, и делать либо сборки, либо тонкостенные плоские 3D-детали, у которых «не хватит сил» сжать внешний контур и поднять, как следствие, край.
- Высокие и тонкие «башни» могут плохо получаться из-за вибраций, возникающих при работе 3D-принтера ближе к вершине, также возможны сдвиги слоев.
Размеростабильность, точность
- Точная 3D-печать — довольно редкая птица. Не хочу тут говорить инженерным языком, но вероятность того, что сложная составная конструкция соберется с первого раза очень низкая. Тут скорее нужно учитывать то, что можно потом механически доработать детали.
- Отверстия под крепеж лучше делать с запасом 0,5 мм по диаметру. Прочности это не убавит, болтаться крепеж тоже не будет из-за сил затяжки, но вот если сделать без запаса, однозначно придется рассверливать. Уменьшить размер большого вала, >10мм шкуркой гораздо проще, чем обрабатывать отверстие, под которое требуется огромное сверло, врезающееся в пластиковые стенки и ломающее деталь, или застревающие в нем. Также важно учесть, что при сверлении пластик расплавляется и сверло может в него вплавиться так, что извлечь невозможно. Бывали случаи.
- Термоусадка не всегда компенсируется, точнее, её очень сложно поймать, она неодинакова по разным направлениям, поэтому учитывать её крайне сложно. Проще напечатать пробный вариант, а потом внести коррективы.
Если важен внешний вид
- Думайте о том, как мастер будет ориентировать деталь на столе 3D-принтера. 3D-печать идет по слоям, что ярко проявляется при печати поверхностей, отстоящих от горизонтали стола на небольшой угол. Шкурить придется долго и мучительно, потому что придется срезать эту «лестницу» до самых глубоких впадин «ступенек». Лучше располагать такие поверхности или горизонтально, например, положить на стол, или увеличивать угол. В ряде случаев, даже добавление поддержки, портящей изнаночную ненужную сторону, позволяет сэкономить время и силы на постобработку.
- Поддержка. Во-первых, поверхность, которую она поддерживает, имеет значительно больше дефектов, чем без нее. Во-вторых, тонкая и высокая поддержка — слабая, шаткая, что приводит к тому, что поддерживающая деталь может иметь серьезные дефекты, либо не получиться вовсе.
- Улучшение качества первого слоя. Нужно добавить фаску. Даже там, где не нужен острый угол рекомендую добавить фаску 0,5 мм. Она не будет явно видна, однако кромка получится аккуратной.
О чем надо знать, чтобы не ошибиться при заказе 3D-печати
Если важен внешний вид
- Расположение детали на столе. Помним про анизотропию.
- Толщина стенки и заполнение. На что тут можно напороться: заполнение — клеточки 20%, которые либо видно сквозь тонкую внешнюю стенку, либо заполнение незначительно утягивает внешнюю стенку при усадке, но при этом визуально легко определить, что внутри есть поддержка. Тут помогает в первую очередь увеличение толщины внешней стенки, либо увеличение плотности заполнения. Учитывайте это при заказе.
Постобработка
Устранение ступенчатости достигается механическим и химическим методом. Возможно использование шпаклевки. Доступна окраска акриловыми красками. Если деталь имеет сложную цветовую структуру, то мы используем принтер ProJet 4500, работающий по другой технологии. Он склеивает частички порошка клеем с цветными чернилами. Получается неплохо.
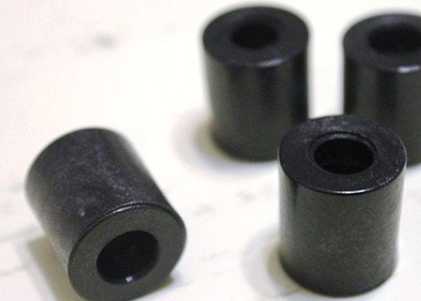
Мораль
В заключение хочется отметить, что указанные рекомендации и наработанный опыт позволит производить детали методом 3D-печати, которые по своим свойствам не будут уступать литым, что позволяет при наличии настроенного принтера и небольших объемах производства экономить значительные средства. По своему опыту отмечу, что возиться с принтером, отлаживать его, знать «все трещинки» — отдельная тема, о которой поведаю позднее. А в завершении я бы хотел попросить читателя выссказать мнение в опросе.
habr.com