Деревообрабатывающий станок — Википедия
Материал из Википедии — свободной энциклопедии
У этого термина существуют и другие значения, см. Станок.Дéревообрабатывающий станóк — станок, применяемый для механической обработки древесины (пиления, строгания и др.), с помощью режущего инструмента или давления. На деревообрабатывающих станках из древесного сырья получают пиломатериалы, заготовки и полуфабрикаты (брусья, брёвна, бруски, доски, стружку, шпон и прочее), детали изделий и конструкций (для мебели, вагонов, судов и т. д.), а также готовые изделия в виде одной детали, паркет, детали перекрытия к зданиям, тару, лыжи, детали музыкальных инструментов, канцелярские принадлежности и др.
- Рабочие машины, производящие работу методом давления, называются прессами.
- Рабочие машины, выполняющие рабочие операции без изменения формы, размеров и качества объекта труда, называются просто машинами (сортировочные, пакето-формирующие, транспортирующие и др.).
- Рабочие машины, осуществляющие физико-химическое воздействие на обрабатываемый объект, называются аппаратами.
Рабочая машина представляет собой механизм или сочетание нескольких механизмов, осуществляющих определённые целесообразные движения для выполнения полезной работы.
ru.wikipedia.org
Где используют лазерные станки
Лазерные станки с программным обеспечением завоевывают огромную популярность и используются для выпуска очень разных изделий. Кстати, если хотите лазерный станок купить переходите на сайт mclaser.ru. Обладая большой скоростью, точностью и аккуратностью обработки, лазерные машины активно теснят собственных «собратьев» даже в тех областях, где прежде применялось лишь оборудование контактной обработки механическим способом (например, фрезерное или токарное). Это, например, относится к подобной операции, как раскрой большеформатных заготовок.
Как все знают, для изготовления любого изделия необходим материал. Единую (цельную) часть материала, подвергаемую отделке для получения готового изделия, называют заготовкой. Форма и размеры заготовки должна максимально подходить виду готового изделия. В данном случае комплект операций по отделке заготовки (по существу, срезанию «избыточного» материала на случай контактной обработки механическим способом, или парообразование – для бесконтактной обработки термическим способом лазером) будет очень маленьким. Что, естественно, приведёт к уменьшению себестоимости и упрощению выпуска продукции. Однако заготовки из разного материала поставляются в виде сортамента с традиционными размерами (самые разные прутья, швеллера, материал листового типа для сталей, плиты конкретной формы для древесины, пластика либо стекла и т.д.). Такие заготовки всегда имеют внушительные размеры.
Стало быть, ранним этапом производства любого изделия считается получение «собственной», нужного размера заготовки. Практически всегда это выполняется путём разрезания листов большого формата. Для этого есть специализированные «отрезные» станки. Однако самые новые модели станков с числовым программным управлением в превосходной степени справляются с подобной операцией – если их письменный стол может поместить «первичную» заготовку большого формата. Во время использования многофункционального станка для лазерной резки с высокой рабочей областью нет необходимости в наличии особого «раскроечного» оборудования. Это существенно облегчает тех. процесс и понижает расходы на оборудование. Но лишь тогда, когда станок с числовым программным управлением может не только раскроить, но и качественно обработать заготовку – аж до 100% готового изделия.
Что такое «большеформатный лазерный станок с числовым программным управлением»
Под станком «большого формата» понимается лазерное оборудование с ЧПУ, имеющее область для работы с размерами более 2000 х 3000 мм. В основном, такой письменный стол не может быть закрыт крышкой (она вышла бы очень большой и тяжёлой), благодаря этому «большие лазеры» получаются своего рода «открытыми». Это налаживает конкретные требования на систему вытяжки отходов (см. ниже) и охранную систему от излучения лазером.
В отличии от фрезеровочных «большеформатников», станок для лазерной резки хотя и имеет широкий инструментальный портал (соответствующей ширине стола для работы), но его вес относительно небольшой – ведь лазерная головка излучателя имеет намного меньшую массу, чем тяжёлый мощный шпиндель. Благодаря этому требования к электрическим двигателям инструментального портала сравнительно «мягкие». Все таки, для динамичного перемещения на любую дистанцию и точного позиционирования излучателя над заготовкой, привод инструментального портала выполняется при помощи серводвигателей.
Для убирания отходов (во время обработки лазером появляются лишь газообразные отходы от испаряемого лучом высокой энергии материала заготовки) станки для лазерной резки большого формата имеют специализированную вытяжку под решётчатым столом. Мощные электрические вентиляторы (в основном, как минимум несколько) убирают газ, засасывая его сквозь промежутки между ячейками или решётками стола для работы.
Другие системы станка имеют те же конструктивные схемы, что и для оборудования «нормального» размера. Все таки, работа большеформатного станка для лазерной резки с ЧПУ имеет принципиальные специфики.
sxteh.ru
Список токарной группы станков — Википедия
Материал из Википедии — свободной энциклопедии
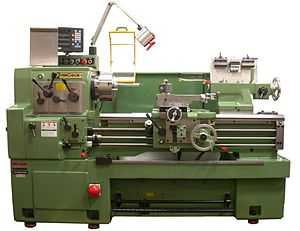
Тока́рный стано́к
— станок для обработки резанием (точением) заготовок из металлов, древесины и других материалов в виде тел вращения. На токарных станках выполняют черновое и чистовое точение цилиндрических, конических и фасонных поверхностей, нарезание резьбы, подрезку и обработку торцов, сверление, зенкерование и развёртывание отверстий и т. д. Заготовка получает вращение от шпинделя, резец — режущий инструмент — перемещается вместе с салазками суппорта от ходового вала или ходового винта, получающих вращение от механизма подачи.Значительную долю станочного парка составляют станки токарной группы. Она включает, согласно классификации Экспериментального НИИ металлорежущих станков, девять типов станков, отличающихся по назначению, конструктивной компоновке, степени автоматизации и другим признакам.
Применение на станках дополнительных специальных устройств (для
История изобретения токарного станка | Великие открытия человечества
Согласно дошедших до нас сведений токарный станок был изобретен примерно в середине седьмого столетия до нашей эры. Между двумя соосно установленными центрами зажималась заготовка из кости или дерева. Подмастерье вращал заготовку, а мастер прижимал резец к заготовке в нужном месте и снимал стружку, пока заготовка не приобретала требуемую форму. Позже заготовку приводили в движение с помощью лука с провисающей тетивой. Ее оборачивали петлей вокруг заготовки. Когда лук начинали двигать, словно пилу при распилке бревен, заготовка начинала вращаться вокруг своей оси то в одну, то в другую сторону. В XIV — XV веках получили распространение токарные станки, имевшие ножной привод. Упругая жердь (очеп) крепилась консольно над станком. На конец жерди крепили бечевку, обернутую на один оборот вокруг заготовки. Нижний конец бечевки крепили к педали. Когда на педаль нажимали, натягивалась бечевка и заготовка делала 1-2 оборота, а жердь сгибалась. Если педаль отпускали, жердь выпрямлялась и подтягивала бечевку вверх, заготовка совершала 1-2 оборота, но в другую сторону.
К 1430 году очеп заменили механизмом, состоящим их педали, кривошипа и шатуна. Получился привод, аналогичный ножному приводу в швейной машинке XX-го столетия. Теперь заготовка в течение всего процесса не совершала колебательного движения, как раньше, а вращалась в одну сторону. В 1500 г. на станке уже были стальные центры и люнет, позволившие обрабатывать достаточно сложные детали. Однако маломощный привод и недостаточная сила в руке рабочего делали обработку металла малоэффективной. Появление водяных приводов оказало большое влияние на повышение эффективности в металлообработке. В середине XVI века был изобретен токарный станок для нарезки конических и цилиндрических винтов. Его изобрел Жак Бессон.
Со временем токарные станки стали часто использовать для нарезки металлов, а не дерева. Возникла необходимость в жестком креплении резца и механизированного передвижения его по обрабатываемой поверхности. Проблема самоходного суппорта разрешилась с изобретением А. К. Нартовым в 1712 году токарно-копировального станка. Во второй половине XVIII века значительно расширилась сфера использования металлорежущих станков, начались усиленные поиски универсального токарного станка. Проблема механизированного передвижения резца стала особенно острой, когда приходилось нарезать резьбу, изготавливать зубчатые колеса, наносить на предметы роскоши сложные узоры. А. К. Нартов успешно решил вопрос механизации операции. Копировальный палец и суппорт двигались благодаря одному ходовому винту, но шаг нарезки под копиром и резцом были разные. Соответственно была решена проблема автоматического передвижения суппорта вдоль оси заготовки. Поперечная подача пока отсутствовала, ее заменило качание системы «копир-заготовка».
Над созданием совершенного суппорта трудились многие изобретатели, наиболее удачную конструкцию изобрел англичанин Г. Модсли. В 1798 году он улучшил конструкцию суппорта и изобрел универсальный токарный станок. В 1800 году станок был усовершенствован и создан новый вариант, включавший все детали, имеющиеся на токарно-винторезных станках и сегодня. Модсли впервые применил стандартизацию резьб на гайках и винтах и стал выпускать наборы плашек и метчиков для нарезания резьбы. Ученик изобретателя Р. Робертс установил ходовой винт перед станиной, на переднюю панель станка вынес ручки управления, добавил зубчатый перебор, улучшив тем самым токарный станок. Еще один сотрудник Модсли — Клемент изобрел лоботокарный станок, позволивший обрабатывать детали с большим диаметром. Д. Витворт изобрел в 1835 г. в поперечном направлении автоматическую подачу, связанную с механизмом продольной подачи. На этом принципиальное совершенствование токарного станка было завершено. Наступил период автоматизации токарных станков.
mirnovogo.ru
Где используются металлорежущие станки
Металл – один из наиболее часто используемых материалов. Наиболее часто он используется в строительстве и машиностроении. Но для полноценного использования, первоначальный материал, должен быть обработан на соответствующем оборудовании.
Задача металлорежущих станков – придать металлу необходимую форму, размер и вес. Металлорежущие станки, являются сложными машинами. Изделия получаемые в результате их работы имеют высокое качество. Подавляющее число механизмов изготовлены на металлорежущих станках. Есть много видов оборудования для производств и заводов, вот, например, несколько вариантов, но особое место, отведено металлорежущих станкам, которые способны работать не только с металлом, но и другими материалами.
Металлорежущих станки – основные группы
В зависимости от области применения, эту обширную группу станков можно поделить на несколько групп:
- токарные;
- фрезерные;
- шлифовальные;
- металлорежущий инструмент;
- прочие инструменты и устройства.
Токарные станки
Токарные станки необходимы для обработки и создания деталей, обладающих формой вращения. В зависимости от сферы применения, такие станки могут быть небольшими. Например, малогабаритные, мини-токарные, микро-токарные, миниатюрные. Любой из этих станков можно свободно разместить на обычном столе. Бывают также тяжелые промышленные станки, которые имеются на большинстве промышленных предприятий.
На токарных станках можно изготовить цилиндрические, конические детали. Подрезать торцы. Просверлить отверстия. Сделать резьбу. А также множество других полезных операций. Основным критерием для характеристики данного оборудования является диапазон оборотов. Который в свою очередь влияет на выбор оснастки. Это может быть быстрорежущая сталь, а также металлокерамика. Большинство токарных станков являются универсальными. Обработка заготовок происходит за счёт снятия стружки или путём деформации.
Фрезерные станки
Этот вид станков обрабатывает металл с помощью фрезы. Фрезерные станки имеют различное предназначение и делятся на:
- универсальные;
- горизонтальные;
- вертикальные;
- продольные;
На этом перечень видов фрезерных станков не заканчивается. Вся эта группа станков имеет жесткую конструкцию, которая необходима для проведения фрезерно-сверлильных работ.
Такие станки имеют несколько режимов работы. Фрезы имеют разную форму, начиная от цилиндрических до дисковых. Эти станки обеспечивают высокую точность обработки, при условии, что станок правильно установлен. Также должен соблюдаться определённый микроклимат в цеху, а рядом со станком нет источников тепла и вибрации. Перечень работ, производимых этим станком весьма широк. Это сверление, рассверливание, долбление.
Металлообрабатывающие станки могут резать и другие материалы, такие как дерево, текстолит, капрон. При современном уровне развития средств производства, уходят в прошлое механизмы, полностью управляемые человеком. Всё чаще на производстве можно встретить станки с ЧПУ. Они позволяют полностью исключить вероятность ошибки, так как вмешательство человека минимально.
bilsh.com
Самодельный станок, где колоть дрова и щепу
В этой статье, я собираюсь показать вам, как я сделал стационарный станок, где колоть дрова, который можно использовать для колки дров или щепы для розжига. Щепание лучины для розжига — это то, что мне было нужно, а использование для этого стационарного станка намного безопаснее, чем попытка разрубить древесину тесаком или топором. Наверху есть квадратная клетка, чтобы предохранить молоток или руку от касания лезвия во время использования.
Станок работает просто, установив полено на лезвие где колоть дрова, ударить по нему молотком, топором или другим куском дерева. Для тех из вас, кто не может размахивать молотком или не чувствует себя комфортно, размахивая топором, вы можете использовать деревянный молоток или подходящее полено.
Шаг 1: Материалы и инструменты
Для изготовления станка, где колоть дрова, нужно очень мало материалов, но требуется сварщик.
Материалы:
• Арматура длиной 10 футов разрезается на:
4 штуки длиной 8″
5 штук длиной 7 1/16″
2 штуки длиной 12″
4 штуки длиной 5 «
• 7&3/4″ x 1,5″ x 1/4″ стальная пластина
Инструменты:
• Сварка
• Угловая шлифовальная машина с режущим диском и шлифовальным диском
• Ручная или механическая ленточная пила (опция)
• Сварочные магниты (дополнительно)
Шаг 2: Видео
Это видео показывает, как работает станок, где колоть дрова
Шаг 3: Дизайн и сборка
Дизайн очень простой, но эффективный, я получил вдохновение от фотографий, где колют дрова, которые я видел в Интернете.
Рама:
• Сделайте 8-дюймовый квадрат из двух 8-дюймовых кусков и двух 7&1/16″ частей арматуры, сделайте это дважды, чтобы было два квадрата;
• Закрепить сварные квадраты для удержания;
• Используя сварочные магниты, выровняйте 12-дюймовую арматуру перпендикулярно одной стороне одного из квадратов, а затем закрепите на месте сваркой;
• Повторите с другой стороны;
• Сварите второй квадрат, который будет вершиной клетки.
Лезвие:
• Лезвие изготовлено из куска листовой стали толщиной 7&3/4″ x 1,5″ x 1/4″, вырезанной полукругом, как лезвие топора;
• Лезвие приварено к арматуре 7&1/16″;
• Кромка была заточена в подобие ножа с помощью угловой шлифовальной машинки и шлифовального диска. Режущая кромка не должна быть слишком острой, но достаточной, чтобы разделять древесину.
Сборка:
• Узел лезвия был приварен между двумя вертикальными частями арматуры длиной 12 дюймов, что удерживает лезвие достаточно высоко, поэтому, когда дерево раскалывается, есть место для щепок. В то же время расстояние не позволяет вам ударить по верхней части клетки ручкой молотка;
• Используйте 5-дюймовые детали арматуры, которые надо отрезать под углом, чтобы их можно было сварить между нижним квадратом и вертикальными прутами 12-дюймовой арматуры в качестве опорных стержней;
• Перед окончательной сваркой все сварные швы были предварительно приварены прихватками.
Шаг 4: Как пользоваться станком, где колоть дрова
Использовать станок очень легко, просто держите кусок дерева над лезвием и ударяйте по нему молотком или другим куском дерева. Вы можете разделить полено на очень мелкие кусочки, и вы никогда не коснётесь лезвия. Щепание небольших кусков дерева и лучины стало очень простым.
Опционально, вы можете сварить из нескольких кусков плоского металла раму, просверлить в ней несколько отверстий, чтобы станок, где колоть дрова, можно было прикрутить на колоду, чтобы он оставался устойчивым при использовании. Это было бы особенно хорошо, если вы захотите колоть большие поленья.
Примечание. Исходя из некоторых ваших комментариев: лезвие расположено достаточно высоко, так что рукоятка молотка никогда не коснётся его, по крайней мере, у меня таких случаев не было. Я думаю, что если вы раскалываете большие бревна, вы можете ударить ручкой об ограждающий каркас. Но в этом случае, вы могли бы защитить верхнюю направляющую куском пены или резины.
По материалам www.instructables.com
tnn-garden.ru
Строгальный станок по дереву своими руками: чертежи
Строгальные станки используются для обработки ровных и фасонных поверхностей: наклонных, угловых, горизонтальных и вертикальных. Самодельные устройства чаще всего объединяют на одном валу циркулярную пилу и строгальное устройство. Это очень опасный вариант, поэтому предпочтительнее затратить больше усилий и установить два различных вала. Но сначала следует подробнее ознакомиться с устройством строгального аппарата по дереву для дома.
Функции и принцип работы строгальных станков
самодельный строгальный станок
Простругивание линейчатых и фасонных деталей из дерева не единственная функция станка. На нем доводят до гладкости пазы, выемки, канавки и уступы, обрабатывают изделия по замкнутому контуру. Назначение механизма в доведении детали по толщине и гладкости.
Существуют двухсторонние станки, которые за один проход обрабатывают две поверхности. Наиболее широко используются они при производстве паркета для дома, мебельной доски из массива. После распиловки заготовки подаются на строгальный станок, где доводятся до необходимой гладкости. Для обработки твердых пород дерева устанавливают специальные ножи.
Рабочая поверхность самодельного станка двигается возвратно-поступательно. На ней фиксируют доску. В суппорты своими руками устанавливают резцы. Заготовка протягивается между резцами, удаляется верхний слой. Обработка производится циклично до достижения необходимой толщины детали.
Продольно-строгальные устройства содержат механизм, создающий возвратно-поступательное перемещение столешницы и передвижение рабочего органа вертикально или горизонтально.
Управляется станок своими руками с помощью ручек и кнопок. Их размещение должно быть максимально удобным, это следует предусмотреть в чертежах самодельного аппарата.
В оборудовании устанавливается электромотор, наиболее совершенные модели оснащаются коробкой скоростей с плавным изменением скоростей. Строгальный станок является основой для универсальных шлифовальных и фуговальных аппаратов с растачиванием.
Устройство строгальных станков
Главные элементы строгального станка:
- электромотор;
- ножевой вал;
- вальцы;
- рабочая поверхность.
Рабочая поверхность состоит из двух параллельных половин, между которыми установлен вал ножей, назначение которого в удалении верхнего слоя заготовки. Доска подается на резку вручную или автоматически. Фиксируется доска на рабочей поверхности вальцами.
Станок позволяет своими руками дома выставлять толщину снимаемого слоя. Для этого предусмотрен специальный высокоточный механизм.
Основание — самодельная станина выполняется из металлического уголка 50х50 мм. Ширина основания определяется промежутком между подшипниками вала (опорными). На станину болтами крепится корпус. В качестве самодельных поперечин выступают металлические пруты.
Своими руками рабочую поверхность выполняют из двух частей: зафиксированной и подвижной. Обе части накладываются на сварную раму из металлического уголка 25 х 25 мм. Длина рам должна быть на 5 см меньше, чем длина рабочей поверхности. Ширина совпадает с шириной стола. Рабочая поверхность выполняется из листа металла толщиной 3 мм.
Фиксированная рамка стола своими руками приваривается на стойки из трубы прямоугольного сечения 40 х 10 мм. Монтаж неподвижной части столешницы осуществляют в следующем порядке:
- при помощи клиньев он выставляется параллельно основанию и валу;
- стойка сваркой крепится к основанию.
Мобильная часть столешницы выполняется в форме прямоугольного треугольника в сечении. Чтобы относительно вала поднять или опустить стол, предусматривают винтовое соединение (талреп).
К раме столешница крепится потайными винтами на прокладках. На фиксированном уголке прикрепляется шплинт, который не позволяет изменение высоты больше чем на 3 мм.
Для упора обрабатываемых деталей предусматривается линейка, которая дает возможность изменять наклон опоры.
Самодельный строгальный станок
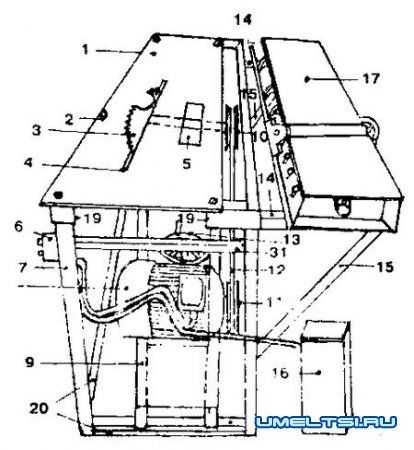
Вид станка с торца: 1 — плита 110х5х1 см; 2 — крепежные болты; 3 — пила; 4 — паз для пилы; 5 — отверстие для фрезы; 6 — автомат ПИВ кнопочный; 7 — ножки; 8 — двигатель; 9 — нижняя рама; 10 — шкив пильного вала; 11 — шкив электромотора; 12 — ремень клиновидный; 13 — колесо механизма натяжения; 14, 15 — фиксаторы рубанка во время простоя; 16 — конденсаторы рабочие и пусковые; 17 — рубанок; 18 — вал для подъемной рамы; 19 — выемка в уголке для рубанка во время работы; 20 — уголки нижние; 21 — уголок для фиксации рубанка
Представленная конструкция для безопасности своими руками оснащена двумя электромоторами и парой валов. Мощность двигателей 5,5 и 3,5 кВт, выдают до 3000 оборотов в минуту. На первый вал надевается фрезерный барабан, на второй — циркулярка. За счет того, что двигатель может перемещаться в пазах, рабочий орган поднимается и опускается.
На таком станке можно работать по дереву дома с кругами до 50 см в диаметре, достигая скорости до 4500 оборотов в минуту. Некоторые умельцы «разгоняют» мотор и до 6000. Однако предварительно следует тщательно выточить вал рубанка, обработать фрезой и отбалансировать. В противном случае вал будет «бить». Обрабатываются детали длиной до 6 метров, шириной до 2,5 м.
Детали конструкции. Валы можно своими руками менять местами. Чтобы установить фрезерный вал снимать раму не нужно. Пила поднимается на максимальную высоту с помощью ключа. Для фиксации рамы на эксцентрике используется пара болтов. Пила и рама поднимаются эксцентриками. Рама, на которой установлен пильный диск жестко фиксируются болтами.
К нижней части электродвигателя крепится плита, перемещающаяся в предусмотренных для этого пазах. Плита приводится в движение колесом, которое изменяет степень натяжения ремня. Это полезно, например, для замены валов. Строгальный рубанок устанавливается на держателе, который фиксируется болтами.
Габариты. Ширина станка 50 см, высота 80 см, длина — 110 см компактный аппарат легко разместить дома. Для устойчивости своими руками из уголка привариваются распорки снизу и металлического уголка 35 х 35 мм.
Видеоролик демонстрирует работу самодельного деревообрабатывающего станка:
stanokgid.ru