1 | 4 | ГРУППА «ММК» | 273 503,30 | 16,63% | -3 526,80 | |
2 | 17 | ГРУППА ЧТПЗ | 113 970,90 | 33,45% | 496,4 | |
3 | 18 | ЕВРАЗ НИЖНЕТАГИЛЬСКИЙ МЕТАЛЛУРГИЧЕСКИЙ КОМБИНАТ | 109 327,38 | 30,32% | 7 204,37 | |
4 | 22 | ЧЕЛЯБИНСКИЙ МЕТАЛЛУРГИЧЕСКИЙ КОМБИНАТ | 99 203,16 | 4,58% | -190,35 | |
5 | 33 | УРАЛЬСКАЯ СТАЛЬ | 63 274,29 | 16,73% | -1 420,45 | |
6 | 50 | ЕВРАЗ КАЧКАНАРСКИЙ ГОРНО-ОБОГАТИТЕЛЬНЫЙ КОМБИНАТ | 37 716,78 | 55,16% | 21 493,43 | |
7 | 55 | ЧЕЛЯБИНСКИЙ ЭЛЕКТРОМЕТАЛЛУРГИЧЕСКИЙ КОМБИНАТ | 35 595,10 | 19,25% | 303 | |
8 | 58 | НИЖНЕСЕРГИНСКИЙ МЕТИЗНО-МЕТАЛЛУРГИЧЕСКИЙ ЗАВОД | 34 490,00 | 21,94% | -14 597,69 | |
9 | 66 | СЕВЕРСКИЙ ТРУБНЫЙ ЗАВОД | 30 097,00 | 1 058,59 | ||
10 | 68 | СИНАРСКИЙ ТРУБНЫЙ ЗАВОД | 27 056,42 | 23,43% | 153,68 | |
11 | 75 | ЧЕЛЯБИНСКИЙ ЗАВОД ПО ПРОИЗВОДСТВУ КОКСОХИМИЧЕСКОЙ ПРОДУКЦИИ | 23 522,25 | 14,03% | -1 551,27 | |
12 | 86 | БЕЛОРЕЦКИЙ МЕТАЛЛУРГИЧЕСКИЙ КОМБИНАТ | 19 649,21 | 16,55% | 467,95 | |
13 | 93 | АШИНСКИЙ МЕТАЛЛУРГИЧЕСКИЙ ЗАВОД | 17 292,50 | 25,46% | 113,5 | |
14 | 95 | ГРУППА «МАГНЕЗИТ» | 16 263,71 | 5,28% | 898,74 | |
15 | 97 | ЗЛАТОУСТОВСКИЙ МЕТАЛЛУРГИЧЕСКИЙ ЗАВОД | 15 857,20 | 59,79% | 26,8 | |
16 | 101 | УРАЛЬСКАЯ КУЗНИЦА | 15 148,12 | 50,49% | 1 983,39 | |
17 | 108 | СЕРОВСКИЙ ЗАВОД ФЕРРОСПЛАВОВ | 13 474,70 | 17,26% | 1 910,69 | |
18 | 120 | ИЖСТАЛЬ | 12 437,47 | 5,11% | -703,48 | |
19 | 132 | ГРУППА РОССПЕЦСПЛАВ | 10 364,42 | 62,51% | 174,92 | |
20 | ВИЗ-СТАЛЬ | 9 779,53 | 0,12% | 529,29 |
Партнеры компании ООО «Нева-МеталлТрэйд» — Северсталь, ММК, НОСТА – ведущие металлургические комбинаты России
ОАО Северсталь
Череповецкий металлургический комбинат ОАО «Северсталь» — крупнейшее предприятие металлургического комплекса Вологодской области.
ЧерМК — предприятие с полным металлургическим циклом, включающим коксохимическое, агломерационное, доменное, сталеплавильное и прокатное производства. Он является одним из самых мощных и современных предприятий мира по производству черных металлов.
Основные виды выпускаемой продукции Череповецкого металлургического комбината — арматура, катанка, круг, уголок, швеллер, шестигранник, судовая сталь, сталь для мостостроения, строительства зданий и сооружений, сталь для сосудов, работающих под давлением, электротехническая сталь, оцинкованная сталь, оцинкованная сталь с полимерным покрытием, автолист, гнутые профили, двухслойная плакированная сталь, трубная заготовка.
ОАО «Магнитогорский металлургический комбинат
ОАО «Магнитогорский металлургический комбинат» входит в число крупнейших мировых производителей стали и занимает лидирующие позиции среди предприятий черной металлургии России.
Активы компании в России представляют собой крупный металлургический комплекс с полным производственным циклом, начиная с подготовки железорудного сырья и заканчивая глубокой переработкой черных металлов.
ММК производит широкий сортамент металлопродукции с преобладающей долей продукции с высокой добавленной стоимостью.
Группа НЛМК
НЛМК – одна из крупнейших металлургических компаний в мире. Группа производит широкий спектр листового и сортового стального проката.
При производственной мощности более 12,6 миллионов тонн стали, НЛМК является ведущим поставщиком слябов и трансформаторной стали в мире и крупнейшим российским поставщиком продукции с высокой добавленной стоимостью, включая прокат с полимерным покрытием, оцинкованную и электротехническую сталь, а также сортовую металлопродукцию.
ПАО «Металлургический комбинат Азовсталь
ПАО «Металлургический комбинат «Азовсталь» входит в Дивизион стали и проката Группы Метинвест и является одним из крупнейших всемирно известных металлургических предприятий Украины. Комбинат входит в тройку лидеров металлургической отрасли страны по производству чугуна, стали и проката. Высокое качество продукции «Азовстали» признано более чем в 70 странах мира.
В состав металлургического комбината «Азовсталь» входят: коксохимическое производство, цех агломерации, доменный цех в составе пяти доменных печей, сталеплавильный комплекс в составе конвертерного, прокатный комплекс в составе толстолистового цеха, рельсобалочного цеха и входящего в него отделения крупного сорта и цеха рельсовых скреплений.
ПрАО «Донецксталь
ПрАО «Донецксталь» — металлургический завод» создано в августе 2002 года на базе доменного и мартеновского цехов Донецкого металлургического завода.
Сегодня это современное металлургическое предприятие, специализирующееся на производстве:
— литейного и передельного чугуна;
— более 100 разновидностей углеродистых, конструкционных, низколегированных, легированных обыкновенного качества, качественных и высококачественных марок стали;
— церковных колоколов из цветного высококачественного сплава;
— стальных электросварных прямошовных труб и металлических мебельных каркасов;
— стройматериалов, железосодержащих отходов, шлаковой продукции и продукции известкового производства.
Металлургия — Главная | О регионе | Экономика | Промышленность | Металлургия
В промышленном производстве области наибольший удельный вес приходится на металлургическое производство.
Металлургический комплекс области является одним из крупнейших производителей металлопродукции в России, ведущим в Северо-Западном федеральном округе.
Крупнейшие металлургические предприятия металлургии в Вологодской области — Череповецкий металлургический комбинат ПАО «Северсталь» и ОАО «Северсталь-метиз».
ПАО «Северсталь»
http://www.severstal.ruЧереповецкий металлургический комбинат – ключевой актив дивизиона «Северсталь Российская Сталь», один из крупнейших интегрированных заводов по производству стали и один из самых рентабельных металлургических предприятий в мире.
Основные виды выпускаемой предприятием продукции – арматура, катанка, круг, уголок, швеллер, шестигранник, судовая сталь, сталь для мостостроения, строительства зданий и сооружений, сталь для сосудов, работающих под давлением, электротехническая сталь, оцинкованная сталь, оцинкованная сталь с полимерным покрытием, автолист, гнутые профили, двухслойная плакированная сталь, трубная заготовка.
ОАО «Северсталь-метиз»
http://www.severstalmetiz.com«Северсталь-метиз» – группа предприятий, объединяющая метизные активы компании «Северсталь», входящая в ТОП-5 крупнейших европейских компаний в своем сегменте и имеющая стратегию развития, направленную на достижение единых общекорпоративных целей ПАО «Северсталь».
Группа предприятий «Северсталь-метиз» — это эффективно работающая компания, стремящаяся к совершенствованию своих бизнес-процессов, работающая в нишевых сегментах с высокой добавленной стоимостью (рынки, отрасли, продукты), ориентированная на создание ценности для клиента через лучший портфель «продукт-сервис».
Предприятия группы выпускают более 100 тыс. видов продукции, включая низкоуглеродистую и высокоуглеродистую проволоку, гвозди, холоднотянутую сталь, стальные канаты, сетки и крепеж.
История Череповецкого Металлургического Комбината по годам
Строительство крупного завода для снабжения Северо-Западного региона России собственным металлом стало возможным после открытия в 1930-1933 годах Кольских железных руд и печорских углей. Суровые климатические условия и территориальная удаленность делали нецелесообразным строительство металлургического комбината в непосредственной близости от залежей руды и угля. Было решено расположить предприятие около Череповца — на перекрестке потоков руды, угля и готовой продукции, в месте пересечения железнодорожной линии Вологда-Ленинград с Мариинской водной системой.
20 июня 1940 г. Совнарком СССР принял постановление «Об организации металлургической базы на Северо-Западе СССР», предусматривающее создание металлургического завода в г. Череповце. Строительство завода было отложено в связи с Великой отечественной войной и возобновлено лишь через 7 лет.
30 декабря 1947 года было решено возобновить сооружение Череповецкого металлургического завода с пересмотром его проекта в соответствии с результатами изучения проблемы и рекомендациями Академии Наук СССР.
24 августа 1955 года был получен первый череповецкий чугун на доменной печи №1. Этот день стал Днем рождения Череповецкого металлургического завода. Домна работала на привозном коксе Ново-Липецкого металлургического завода.
1 мая 1958 года, в 1 час 40 минут была получена первая череповецкая сталь. А утром еще теплый слиток провезли по городу в праздничной колонне.
В ноябре 1959 года Правительство страны поздравило строителей и металлургов с вводом в действие крупнейшего в Европе листопрокатного стана – 2800 ЛПЦ №1. Череповецкий завод стал предприятием с полным металлургическим циклом. В последующие годы вступают в строй новые металлургические мощности: доменные печи, электропечи, конвертеры, прокатные станы по производству листовой и сортовой стали.
Учитывая сложную структуру и комбинированный характер производства, Министерство черной металлургии СССР 23 июня 1983 года приняло решение о реорганизации Череповецкого металлургического завода в Череповецкий металлургический комбинат.
24 сентября 1993 года в соответствии с указом Президента Российской Федерации государственное предприятие Череповецкий металлургический комбинат зарегистрировано в мэрии города Череповца как акционерное общество «Северсталь».
Начиная с 1993 г. происходило активное развитие компании «Северсталь»: в ее состав вошли предприятия, связанные с производством метизов, труб большого диаметра, добычи угля, железной руды и других минералов.
За все время работы на предприятии было выплавлено более 400 млн тонн стали и произведено более 2 500 000 км проката.
Металлургические базы России
В зависимости от направленности металлургического комплекса, предприятия размещаются вблизи от мест добычи сырья, необходимого для обеспечения их работы. Поскольку залежи руды, или топлива для ее плавления, размещены в определенных регионах страны, то вокруг них находятся целые группы металлургических заводов и комбинатов. Данные предприятия пользуются общими сырьевыми ресурсами, и имеют одинаковое производственное направление, поэтому их условно объединяют в группы, которые называют металлургическими базами.На территории России можно выделить три большие группы:
— Центральная
— Уральская
— Сибирская.
Поскольку на этих территориях расположены разные по составу залежи руды, различная степень обеспечения топливом и другими производственными потребностями, то целевая направленность, мощность и структура баз имеет отличие. К тому же в этих регионах добыча и переработка стартовало в разное время, что существенно сказалось не только на масштабах производительной мощности, но и на истощение рудников, с которых ведется добыча.
Центральная металлургическая база
Эта группа предприятий занимается активным производством черных металлов. Ресурс данных предприятий очень большой, поскольку на близлежащих территориях имеются значительные запасы сырья в виде железной руды. Производство охватывает не только переплавку добываемой руды из месторождений Курской магнитной аномалии, но и занимается переработкой импортированного сырья и лома черного металла.
Для территории Центральной базы характерно залегание руды достаточно близко к поверхности, что позволило наладить добычу открытым способом.
Такая технология позволяет поставить большую производительность каждого рудника. Это значительно удешевляет стоимость, что положительно влияет на развитие всего металлургического комплекса Центральной базы.
Непосредственная добыча производится в Курской и Белгородской областях. Стоимость на добычу 1 тн. руды готовой для переработки, почти в два раза ниже, чем на других производственных месторождениях Украины и Казахстана. Центральная база обеспечивает 80 млн. тн. сырой руды.
Этот показатель составляет около 40 % добычи по всей стране. Удобное место расположения позволяет не только наладить экспорт своей продукции, но и импорт сырья для переработки. Эти факты позитивно влияют на себестоимость продукции, делая ее конкурентной на рынке.
Группа имеет в своем составе предприятия полного металлургического цикла, которые оснащены производственной мощностью для переработки сырья в готовую продукцию в виде металлопроката и других изделий. Среди них можно выделить: Новотульский завод, Новолипецкий металлургический комбинат, металлургический завод «Свободный Сокол», Оскольский электрометаллургический комбинат по прямому восстановлению железа. Эти предприятия обладают большой степенью самодостаточности, и играют ключевую роль в экономике России.
Центральная база включает и территорию Севера европейской части РФ. Здесь имеется залежи руды в размере 5 % от общих запасов. Непосредственная добыча металла в процентном соотношения от Всероссийской составляет 21 %. Это обеспечивает группа предприятий таких как: Череповецкий металлургический комбинат, Оленегорский, Ковдорский и Костомукшский горно-обогатительные комбинаты. Добываемая здесь руда имеет малый процент примесей, что позволяет при переработке получить из нее качественную высокоуглеродистую сталь.
Уральская металлургическая база
Имеет развитую структуру, что позволило ей стать одним из крупнейших в странах СНГ металлообрабатывающим комплексом. Ежедневно здесь выплавляется 52 % чугуна и черных металлов, 56 % стали от общей производительности по стране. На Урале налажено величайшее производство цветных металлов в РФ. Такие масштабы объясняются тем, что эти производства старейшие в России, так что имеют большую историю развития. В связи с нехваткой топлива в данном регионе, здесь налажена поставка кузнецкого угля, что позволяет полностью покрыть спрос. В связи с сильным истощением собственных залежей, предприятия перерабатывают руду из Казахстана, Карелии и Курской магнитной аномалии. Данные меры позволяют удерживать Уральской металлургии первенство по производительности.
Непосредственная добыча собственной руды активно протекает в Свердловской и Челябинской областях. Масштабное производство налажено на Качканарский горно-обогатительном комбинате и Бакальском рудоуправлении. Эти предприятия достаточно старые и имеют большую историю, и уже много лет поддерживают работу всего региона.
Самые эффективные центры черной металлургии страны находятся именно на Урале, это: Магнитогорск, Нижний Тагил, Челябинск, Серов, Екатеринбург и др. Нужно отметить, что самым масштабным предприятием по производству чугуна в Европе является Магнитогорский металлургический комбинат, который также входит в группу Уральской металлургической базы.
Для Урала характерна высокая концентрация данных предприятий. Но их деятельность не ограничивается только выплавкой, поскольку в регионе производят трубы для нефти и газопроводов, что является большим направлением требующим значительную долю от производимых металлов. Таким образом, на территории Уральской базы развита система потребления метала путем изготовления из него труб, арматуры и других изделий, которые покрывают спрос не только внутри страны, но и экспортируются.
Сибирская металлургическая база
Это сравнительно молодая группа, которая находится на этапе формирования. Несмотря на незначительную степень развития, в сравнении с уральскими предприятиями, деятельность по добыче и переработки является весьма перспективной. В земных недрах этого региона скрывается 21 % от всех запасов страны, а заводов и комбинатов по их добыванию пока не очень много. В процентном соотношении производится 15 % чугуна и готового проката. Работу предприятий обеспечивает Ангаро-Илимский бассейн, Хакасия и Горная Шория. Для выплавки используется топливо из Кузнецкого каменноугольного бассейна, который, как было замечено ранее, поддерживает и уральское производство.
Главными в регионе можно назвать Кузнецкий и Западно-Сибирский металлургические комбинаты. В связи с неполным заполнением возможностей по добыче сырья, на территории Сибирской металлургической базы существуют перспективы строительства дополнительных центров. В частности это можно сделать путем расширения Тайшетского и Барнаульского металлургических заводов.
В свете активного формирования Южно-Якутского комплекса, имеются перспективы на развитие данной деятельности на Дальнем Востоке. Отдаленность региона является препятствием для масштабной транспортировки сырья, поэтому предполагается создание полного цикла по переработки непосредственно вблизи места добычи. Это позволит снизить стоимость готовой продукции, поскольку отпадет необходимость дополнительных затрат на перевозку.
С развитием экономики, для обеспечения сбыта продукции и поставки необходимого для производства сырья с других регионов или стран, были сформированные объединения и холдинги. В их структуру входят заводы и комбинаты, которые находятся в разных металлургических базах страны. Яркими примерами такого союза являются холдинг «Металлоинвест», «Северсталь», «Евраз Групп С.А.» и др.
Решение компании Эмерсон обеспечивает надежный анализ отходящих газов на одном из крупнейших металлургических комбинатов России
Решение от Эмерсон позволяет одновременно экономить на топливе в производственном цикле и является существенным шагом вперед в реализации Государственной программы защиты окружающей среды
РОССИЯ, Челябинск (14 февраля, 2018) – Магнитогорский металлургический комбинат реализовал проект по оптимизации процессов горения и контролю газовых выбросов с воздухонагревателей одной из доменных печей с помощью решения компании Эмерсон. Решение от Эмерсон позволяет одновременно экономить на топливе в производственном цикле и является существенным шагом вперед в реализации Государственной программы защиты окружающей среды, а также задачи внедрения на промышленных предприятиях Урала систем экологического мониторинга.
Крупнейший металлургический комбинат в России имеет 8 доменных печей, в состав каждой из которых входит четыре воздухонагревателя-каупера. На каждом каупере комбината необходимо измерять состав отходящих газов, попадающих после отработки в воздух. Сложность анализа газовой смеси, которая формируется от горения смеси доменного и коксового газов, состоит в том, что смесь имеет большое количество различных механических примесей и обладает агрессивными свойствами из-за высокого содержания соединений серы, Кроме этого, переменный режим работы воздухонагревателей изменяет давление анализируемого газа от вакуума до избыточного.
Российские эксперты Эмерсон предложили внедрение решения в виде четырех систем на базе газоанализаторов для каждого из воздухонагревателей печи. Решение, смонтированное «под ключ» во всепогодном обогреваемом шкафу, обеспечило непрерывное одновременное определение содержания оксидов углерода СО, СО2 и кислорода О2.
Оптимальность спроектированных аналитических систем позволяют ММК контролировать технологические режимы подачи топлива и, как следствие, контролировать процессы горения, что снижает экологическую нагрузку на окружающую среду, обеспечить надежный непрерывный анализ выходящих газов и проводить дополнительный контроль технологического режима. Успешно внедренная и эффективно функционирующая система позволила обеспечить настройку работы воздухонагревателей по полному сгоранию газа в автоматическом режиме.
«Аналитические решения компании Эмерсон, которые проектируют российские инженеры, позволяют промышленным предприятиям страны контролировать выбросы в атмосферу, а также экономить потребление сырья в производственном цикле», – говорит Александр Моев, руководитель подразделения аналитического оборудования, директор департамента промышленного анализа и экологических разработок ООО «Эмерсон».
Дополнительная информация о решение по мониторингу выбросов от компании Эмерсон по ссылке https://www.emerson.com/documents/automation/4237466.pdf
О ПГ «Метран»
На сегодняшний день Промышленная Группа «Метран» является ведущим российским приборостроительным предприятием, с производственных линий которого выходят средства измерений давления, температуры, уровня, расхода; распределенные системы управления, клапаны и регуляторы, метрологическое оборудование. «Метран» обеспечивает все стадии жизненного цикла продукции: разработку, изготовление, техническую поддержку, продажи, сервисное обслуживание и обучение заказчиков. Это ключевой актив компании Emerson не только в России, но и СНГ. Главным шагом в стратегии локализации, последовательно реализуемой компанией в течение 10 лет, стало открытие в 2015 году нового офисно-производственного комплекса в Челябинске площадью почти в 30 тыс. кв.м. Расширение производства на территории России позволяет выпускать продукцию мирового уровня под знаком «Сделано в России».
О компании Emerson
Emerson (NYSE: EMR), Сент-Луис, штат Миссури, США – глобальная компания, объединяющая технологии и инжиниринг для создания инновационных решений для Заказчиков на рынке товаров промышленного назначения, коммерческом рынке и рынке индивидуальных потребителей. Бизнес компании Automation Solutions помогает непрерывным, гибридным и дискретным производствам производить максимум, защищать персонал и окружающую среду и оптимизировать их энергетические и эксплуатационные затраты. Бизнес Commercial and Residential Solutions помогает своим заказчикам в создании комфортной бытовой среды и охране здоровья, контроле качества и безопасности пищевых продуктов, повышении эффективности энергопотребления и строительстве функциональной инфраструктуры. Более подробная информация представлена на сайте Emerson.com.
Крупнейший металлургический комбинат Украины остановил работу — Экономика и бизнес
КИЕВ, 16 мая. /ТАСС/. Рабочие первой смены железнодорожного цеха горно-металлургического комбината «АрселорМиттал» (ранее «Криворожсталь») в Кривом Роге Днепропетровской области отказались работать на неисправной технике. Как пояснил в среду председатель первичной ячейки Независимого профсоюза горняков Украины (НПГУ) Юрий Самойлов, это фактически парализовало работу комбината.
«Сегодня с 7 часов утра на ПАО «АрселорМиттал Кривой Рог» рабочие первой смены железнодорожного цеха начали действовать по инструкциям. Они отказались работать на неисправной технике, и это фактически парализовало работу всего предприятия, поскольку ни один локомотив не сдвинулся с места», — приводит его слова пресс-служба Конфедерации свободных профсоюзов Украины.
Самойлов пояснил, что железнодорожный транспорт обслуживает все производство на предприятии. «То есть доставляет сырье и вывозит готовую продукцию, в результате уже остановились и мартеновский и конвертерный цехи. А это может привести к катастрофическим последствиям», — отметил представитель НПГУ.
Ранее, 14 марта 2018 года, работники предприятия выходили на акцию протеста с требованиями повышения зарплаты, предоставление нормальных условий труда, проверки исправности оборудования, усовершенствования конвертерного цеха, обследования зданий завода. Сотрудники в ходе мероприятия призывали не допустить несчастных случаев. Тогда же во время митинга было собрано 12 тысяч подписей работников предприятия, необходимых для созыва конференции профсоюзов, после чего у работников появились законные основания для объявления забастовки.
Деятельность предприятия «АрселорМиттал Кривой Рог» охватывает производственную цепочку от добычи железной руды до изготовления готовой металлургической продукции. Экспорт осуществляется в Россию, Центральную Азию, страны Персидского залива, также в Африку и Европу.
Осенью 2015 года металлургический комбинат «Криворожсталь» на повторном приватизационном аукционе достался Mittal Steel индийского миллиардера Лакшми Миттала за $4,8 млрд. Позже комбинат был переименован в «Арселор Миттал Кривой Рог».
Крупнейший советский сталелитейный завод будет построен в Центральной России
Доменные печи в США, как правило, меньше по размеру, самая большая из них находится на заводе Bethlehem Steel Corporation в Бернс-Харборе, штат Индиана, с рабочим объемом 86 000 кубических футов. Американские производители проявляют все больший интерес к процессу прямого восстановления, который превращает железную руду в высокообогащенное железо без доменной печи.
Новое разрабатываемое месторождение
Помимо Липецка, доменные печи объемом 175 000 кубических футов должны быть построены на Урале и в Украине, вероятно, на месте нового разрабатываемого месторождения руды недалеко от Кременчуга на Днепре. Река.Проектирование этих огромных агрегатов сейчас находится в стадии разработки. Первая печь запланирована на 1975 год, но советские промышленные проекты часто откладываются.
Решение о наращивании производственных мощностей в Липецке в центральной части России все в большей степени отражает политику размещения промышленности подальше от восточных регионов Советского Союза, особенно Сибири, которые страдали от острой нехватки трудовых ресурсов.
Во многих отраслях промышленности СССР была тенденция к развитию как можно большего количества дополнительных мощностей в европейской части страны, где сосредоточена большая часть производства и населения.Развитие Сибири, как правило, ограничивается отраслями, основанными на гидроэнергетике и некоторых минеральных ресурсах, имеющихся в изобилии в этом регионе.
Липецкий металлургический комбинат использует руду так называемой Курской магнитной аномалии, обширного железосодержащего региона между Орлом и Белгородом, где из-за огромных запасов железа под землей стрелки компаса отклоняются от магнитного поля. к северу.
Неблагоприятные условия
Развитие этого железного района замедлилось из-за неблагоприятных условий добычи, но использование современных технологий начало ускорять добычу руды.В Губкине, восточнее Курска, и в Железногорске, к югу от Орла, строятся две крупные обогатительные фабрики мощностью 15 миллионов тонн железного концентрата каждая.
Еще до начала работ по доменной печи объемом 175 000 кубических футов в Липецке будет завершена печь объемом 112 000 кубических футов, строительство которой сейчас ведется. Это будет пятая печь на заводе.
Строительство липецкого комбината, дополнившего старый металлургический завод XIX века, началось в 1934 году, но современное расширение началось только после Второй мировой войны.Электропечи и установка непрерывной разливки были открыты в 1959 году, а первый кислородный сталеплавильный цех был открыт в 1966 году.
FACTBOX: Производство стали и металлов в России
(Рейтер) — Россия, второй по величине экспортер нефти в мире после Саудовской Аравии. Аравия, поставщик четверти потребностей Европы в газе, также является одним из крупнейших мировых производителей стали и металлов.
Ниже приводится список некоторых металлов, производимых в России, и мировой рейтинг страны:
СТАЛЬ
Россия является четвертым по величине производителем стали в мире после Китая, Японии и США.
В 2007 году было произведено 72,2 миллиона тонн, или 5,3 процента от мирового производства в 1,34 миллиарда тонн.
Крупнейшими производителями стали в России являются «Северсталь», Evraz Group, Магнитогорский металлургический комбинат и Новолипецкий металлургический комбинат.
Источник: Международный институт черной металлургии
ЖЕЛЕЗНАЯ РУДА
Россия занимает пятое место в мире по добыче железной руды после Китая, Бразилии, Австралии и Индии.
В 2007 году было произведено 110 миллионов тонн, или 5,8 процента мирового производства, равного примерно 1.9 млрд тонн.
Запасы России, однако, являются крупнейшими в мире по содержанию железа: 31 миллиард тонн, или 19 процентов от мировых запасов в 160 миллиардов тонн, исходя из содержания железа.
Крупнейшим производителем железной руды в России является Металлоинвест.
Источник: Геологическая служба США
ЗОЛОТО
Россия занимает шестое место в мире по добыче золота после Китая, Южной Африки, Австралии, США и Перу. В 2007 году было произведено 169,2 тонны золота, или 6 тонн.8 процентов мирового производства золота 2476 тонн.
Однако по золотым запасам России она уступает только ЮАР. Российский союз золотопромышленников заявляет, что страна планирует увеличить добычу до 225 тонн к 2015 году, так как многие крупные рудники в Сибири и на Дальнем Востоке будут введены в эксплуатацию.
Крупнейшей золотодобывающей компанией в России является «Полюс Золото», которая производит около четверти золота в стране и является четвертой по величине золотодобывающей компанией в мире по запасам.
Источник: консультации GFMS Ltd
НИКЕЛЬ
Россия — крупнейший производитель никеля в мире.В 2007 году она произвела 278 400 тонн рафинированного никеля, или 19,3 процента от мирового производства рафинированного никеля в 1,44 миллиона тонн.
«Норильский никель» производит подавляющую часть никеля в стране.
Источник: Международная исследовательская группа по никелю
ПАЛЛАДИЙ
Россия является крупнейшим в мире производителем палладия, драгоценного металла, используемого в ювелирных изделиях и выхлопных газах автомобилей. По оценкам, в 2007 году он произвел 99 тонн, или 44 процента от мирового производства в 225 тонн. Южная Африка, занявшая второе место, произвела примерно 83 тонны, или 37 процентов от общемирового производства.
«Норильский никель» — основной производитель.
Источник: Raw Materials Group
PLATINUM
Россия является вторым по величине производителем платины в мире после Южной Африки. В 2007 году он произвел около 30 тонн, или 14 процентов от мирового производства в 215 тонн. Южная Африка произвела 171 тонну, или 79,5 процента от общемирового производства.
«Норильский никель» — основной производитель.
Источник: Raw Materials Group
АЛЮМИНИЙ
Россия является вторым по величине производителем первичного алюминия в мире после Китая. В 2007 году она произвела почти 4 миллиона тонн, или 10,5 процента от мирового производства в 37,7 миллиона тонн.
Объединенная компания РУСАЛ производит весь первичный алюминий в России и является крупнейшим производителем в мире.
Источник: Raw Materials Group.
Составлено Робином Пакстоном в Москве и Карен Нортон в Лондоне
Промышленность
ПромышленностьПромышленность в Магнитогорске
Промышленность в Магнитогорске сосредоточена вокруг крупнейшей в мире сталелитейной промышленности. фрезерно-формовочный завод.Пять заводов завода производили сталь. на половину всех танков России во время ВОВ. Это исторически военный акцент типичен для города сталинской эпохи и отмечен статуей из олицетворенный советский рабочий передает выкованный им меч Советский солдат. Это наследие производства стали живет сегодня в огромных количествах.
стали, чугуна и готовой продукции Магнитогорского производства
Металлургический завод. В 1996 году завод выпустил 7 штук.5 млн т стали, что
примерно соответствует объему производства стали в Великобритании или Канаде.
Этот подвиг еще более удивителен тем фактом, что нет естественных
происходящие ресурсы в настоящее время находятся на небольшом расстоянии от города. Однажды
богатая шахта
на Магнитной горе в настоящее время истощены, и на самом деле никогда не существовало
уголь для коксования чугуна на участке. Теперь все сырье должно
буксировать по рельсам из разных уголков России.Это
может показаться странным, что страна с чуть более чем половиной населения
Соединенных Штатов будет производить столько же стали и чугуна. Этот
Несоответствие связано с несколькими факторами. В течение
крах индустриализации сталинской эпохи
в расчете на количество товаров востребован тоннаж стали, а не
качество стали. Этот рывок был попыткой заставить СССР успокоиться.
Соединенные Штаты в промышленном потенциале. Следовательно, этот толчок потребовал
огромное количество измеримых товаров, например, тоннаж стали, и
в командной экономике то, что диктует правительство, — это то, что заводы
попытка произвести.
Второй фактор во многом объясняется неисправностью
инфраструктура в СССР. Поскольку производители знали, что их
поставки необработанной стали не приходили вовремя, они заказывали гораздо больше
чем им было нужно, и заказывали это гораздо чаще и держали огромные
запасы стали в наличии, которые из-за большого количества времени
в плохих условиях хранения ржавчина ржавеет и приходит в негодность. Таким образом,
цикл начался снова.
Условия на заводе всегда были далеко не из приятных.
В определенные моменты во время строительства фабрики травмы и смертельные случаи
в среднем более одного в день. Со временем условия улучшились, но
они все еще не дотягивают до японского или американского производства стали.
стандарты. Травмы по-прежнему встречаются чаще, чем в США, и условия
хуже. Главный фактор повышенной опасности в Магнитогорске
Металлургический завод — это состояние оборудования и помещений. В
большая часть оборудования на заводе по-прежнему основана на разработанных технологиях. в 1930-е годы, когда был построен завод и во многих местах сами машины
те же самые, что были установлены на первоначальной фабрике при ее создании.
Возраст оборудования в сочетании с чрезмерным использованием и плохими привычками к обслуживанию
привел в состояние фабрики сегодня. Многие машины
были постоянно превышены производственные мощности и не имели времени на ремонт
чтобы фабрика выполнила свою квоту. Практика «штурма»
также сказалось на машинах и рабочих. Штурм — это практика
установленный при плановой экономике конец производственного цикла.
Если завод еще не достиг своей квоты на производство стали, то
завод перейдет в режим овердрайва и произведет оставшуюся часть
квота.Это часто удваивало или утроило нормальную производительность завода.
Эта деградация техники в сочетании с ее возрастом и неэффективностью
в сочетании для действительно сложных рабочих условий. Рабочие в
сообщается, что фабрика предпочитает летние месяцы зиме, потому что
летом завод позволяет открывать крышу и световые люки,
снижает концентрацию паров.
Текущее состояние сталелитейного завода довольно неопределенное. В то время как мельница работает менее чем на треть своей обычной мощности, это по-прежнему одна из наиболее жизнеспособных отраслей в России. Страны Азии без собственных сталеплавильных комплексов были относительно нетерпеливы покупать дешевую сталь на этом российском заводе. Зарубежные продажи В результате заводчане получили доход в твердой валюте, каждый из которых платят больше, чем в среднем по стране.

Дом
Новый завод Металлоинвеста по производству ГБЖ в России будет способствовать развитию зеленой сталелитейной промышленности
Во время своего выступления на международной конференции Global Iron Ore 2021 Юрий Гаврилов, директор по стратегии и слияниям и поглощениям Металлоинвеста, ведущего российского производителя железной руды и горячебрикетированного железа. производитель заявил, что к 2030 году доля стали, произведенной в ЭДП, в общем объеме производства стали, как ожидается, вырастет с нынешних 21 процента до 37 процентов.

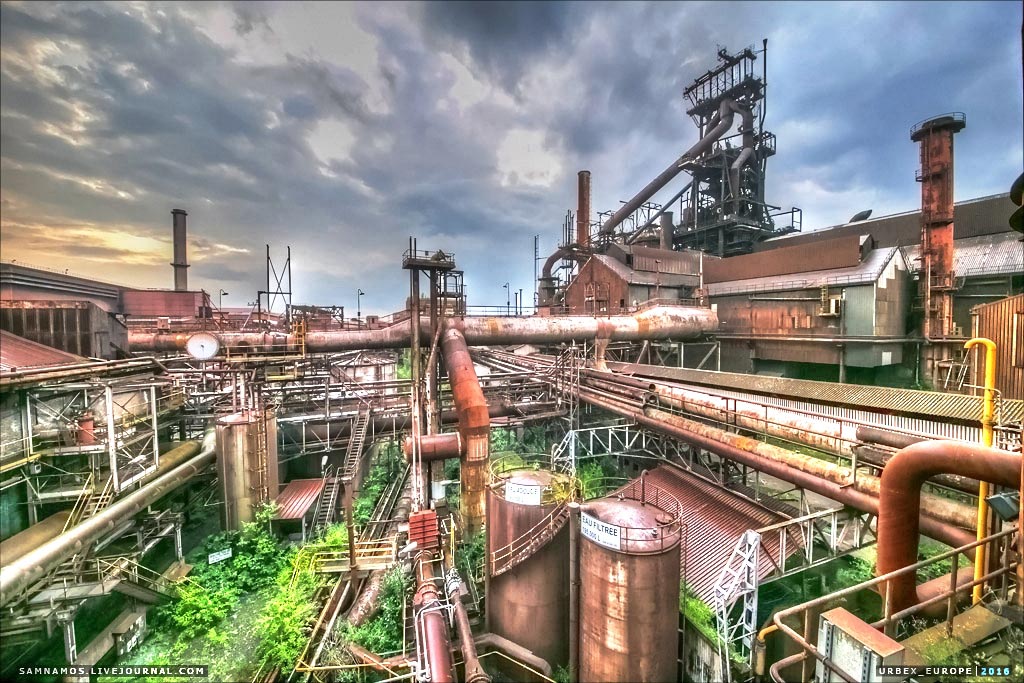
Металлоинвест продолжает работу над улучшением качества концентрата, уделяя основное внимание увеличению производства высокорентабельной продукции, а именно окатышей и ГБЖ. Компания считает, что окатыши премиум-класса, горячее брикетирование и железо прямого восстановления (ГБЖ / ПВЖ) — это будущее зеленой металлургии.
В настоящее время компания продолжает реализацию комплексной программы по повышению качества железорудной продукции на Михайловском ГОКе Андрея Варичева и, в частности, по увеличению объемов производства.В 2020 году Металлоинвест запустил производство нового товарного продукта — железорудных окатышей премиум-класса (марки DR), предназначенных для последующей металлизации. В 2022 году будет завершено строительство завода по обогащению концентрата, который будет производить до 17 млн т высококачественного концентрата в год для производства окатышей на заводе окатышей Михайловского ГОКа.
Mitsubishi Heavy построит крупнейший завод по производству стали с нулевым содержанием углерода
ТОКИО — Японская компания Mitsubishi Heavy Industries скоро завершит строительство в Австрии крупнейшего в мире сталелитейного завода, способного обеспечить нулевые выбросы углекислого газа.
Mitsubishi Heavy через британское подразделение строит опытный завод на комплексе австрийской сталелитейной компании Voestalpine. Пробная эксплуатация планируется начать в 2021 году.
Завод будет использовать водород вместо угля в процессе восстановления железной руды. Оборудование нового поколения будет производить 250 тысяч тонн металлопродукции в год.
По данным Международного энергетического агентства, в 2018 году мировая сталелитейная промышленность произвела около 2 миллиардов тонн CO2, что вдвое больше, чем в 2000 году.Доля сталелитейного сектора среди всех отраслей выросла на 5 процентных пунктов до 25%.
На сокращение выбросов железной руды приходится значительная часть выбросов CO2 при производстве стали. Японские производители стали, в том числе Nippon Steel, разрабатывают процессы восстановления, потребляющие водород, на основе традиционной конструкции доменной печи.
Завод Mitsubishi Heavy применяет процесс, называемый прямым восстановлением железа, или DRI. Новые доменные печи требуют инвестиций в триллионы иен (1 триллион иен равен 9,6 миллиардам долларов). Хотя оборудование DRI производит меньше стали, инвестиции в доменные печи оцениваются менее чем в половине.
Для достижения такого же уровня конкурентоспособности по затратам, как и у доменных печей, DRI должен иметь дешевый водород. Рыночные затраты на водород сейчас составляют около 100 иен за куб. метр, оценивает Минэкономики, торговли и промышленности.
Правительство стремится снизить затраты на водород до 30 иен за нормальный куб. метра к 2030 году, в основном за счет массового производства.
Но для того, чтобы DRI стало возможным в сталелитейной промышленности, «уровень должен быть ниже 10 иен», — сказал один из руководителей крупного производителя стали.
Немецкая компания SMS, ведущий мировой поставщик сталеплавильного оборудования, вместе с Даниэли из Италии, занявшей второе место, развивает процесс производства стали на водородном топливе. Среди производителей стали компания ArcelorMittal из Люксембурга планирует построить в 2021 году в Германии пилотный завод по производству водородной стали. Такие конкуренты, как немецкие Thyssenkrupp и Salzgitter, инвестируют в DRI.
Mitsubishi Heavy, третий по величине поставщик сталеплавильного оборудования в мире, также обеспечивает безопасность цепочки поставок водорода. В октябре компания купила долю в норвежском предприятии по производству водородного оборудования.
В другом месте Mitsubishi Heavy решила приобрести доли в производителях водорода в таких местах, как Австралия. Группа будет контролировать поставки водорода, а также строительство и проектирование оборудования.
В июле Европейский Союз объявил об инициативе инвестировать 470 миллиардов евро (572 миллиарда долларов) в водород к 2050 году. Ожидается, что заводы по производству водородной стали получат поддержку. В Европе растет число предприятий, занимающихся водородом. Mitsubishi Heavy покроет спрос металлургической промышленности на водород, чтобы компенсировать более слабые перспективы роста оборудования для тепловых электростанций.
Производство чугуна и стали в России с 1800 по 1860 год по JSTOR
Abstract Данная статья представляет собой исследование производства чугуна в России в течение первых шести десятилетий XIX века, сразу после трех предыдущих десятилетий, когда Россия была крупнейшим производителем пруткового железа в мире и незадолго до отмены крепостного права в 1861 году. показывает, что в период с 1800 по 1860 год производство пруткового железа в России увеличилось вдвое благодаря сочетанию усовершенствований ранее проверенных процессов и адаптации других зарубежных технологий с учетом имеющихся ресурсов.Хотя российские нефтеперерабатывающие заводы производили высококачественную продукцию на протяжении всего прошлого столетия, для металлургических предприятий стало важным снизить затраты на топливо, чтобы оставаться конкурентоспособными, особенно в условиях ограниченного доступа к прежним экспортным рынкам после 1800 года. Уральский регион продолжал оставаться основным металлургическим регионом страны. производителя, но уральский уголь был непригоден как для плавки, так и для очистки. Таким образом, российским металлургам стало необходимо сократить потребление древесного угля или устранить необходимость в угле.В статье рассматриваются основные примеры инноваций для достижения этих целей: более эффективный процесс оклейки Franche-Comtois (контуазский или малокричный) и метод «лужения», адаптированный для использования дров.
Чтобы удовлетворить растущий спрос на передельный чугун как в чистовых, так и в пудлинговых печах с 1800 по 1860 год, мощность доменных печей значительно увеличилась, несмотря на хрупкость древесного угля по сравнению с коксом, хотя улучшения в использовании топлива во время плавки были довольно скромными.Уральские металлурги также предпочитали постоянное использование обильных водных ресурсов для производства энергии, а не широкое распространение паровых двигателей.
ICON, основанный в 1995 году, — это журнал ICOHTEC, посвященный истории технологий. ICON, публикуемый ежегодно, включает статьи, обзорные эссе и рецензии на книги по всем аспектам и периодам технологической истории как членами, так и не членами. Он поощряет исследования транснационального характера, сфокусированные на глобальных технологиях, и стремится поощрять сотрудничество между учеными через национальные или политические границы.
Информация для издателя ICOHTEC была основана в Париже в 1968 году, когда горечь разделила народы Восточного и Западного мира. Намерение состояло в том, чтобы предоставить форум ученых, занимающихся историей технологий, по обе стороны железного занавеса.
Таганрогский металлургический комбинат
Одна из важнейших задач предприятия — коренная реконструкция и ревизия существующих мощностей.Эти меры повысят качество продукции компании и ее конкурентоспособность на внутреннем и мировом рынках.
Признание и уважение, завоеванные Компанией в деловом мире, подтверждено рейтингом ТАГМЕТа в ТОП1000 лучших предприятий России 21 века, а также многочисленными наградами, в том числе Почетным дипломом Лучшего экспортера России.
ТМК — крупнейшая холдинговая компания трубной отрасли России. Под его управлением находятся ведущие трубные предприятия России: Волжский трубный завод (в Волгоградской области), Синарский трубный завод (в Свердловской области), Северский трубный завод (в Свердловской области), Таганрогский металлургический завод (в Ростовской области).
Производственные мощности ТМК обеспечивают 45% производства труб в России. Суммарная производственная мощность ТМК составляет 5 млн тонн трубной продукции в год. Компания является крупнейшим производителем труб в России, выпускает более 42% труб в России, и входит в тройку крупнейших производителей труб в мире. ТМК также является лидером экспорта в своем секторе, поскольку более половины продаваемых за рубежом российских труб произведены ТМК. Иностранные клиенты компании находятся более чем в 60 странах мира.В 2004 году отгружено около 780 000 тонн труб.
Все торговые операции компании осуществляются ее специализированными торговыми подразделениями: TMK Trading Company, работающая в России и странах СНГ, и Sinara Trading: официальный дистрибьютор TMK за пределами бывшего Советского Союза, с собственными филиалами в Германии, Италии, Испании, Венгрии. . Филиалы и представительства ТМК в России и за рубежом, а также широкая сеть официальных дилеров во многом способствуют своевременному и эффективному принятию решений о поставках продукции компании клиентам по всему миру.
ТМК производит широкий ассортимент труб для нефтегазовой, химической и нефтехимической промышленности, энергетики, машиностроения, строительства и ЖКХ, судостроения, авиационной техники, космической и ракетной техники. Это сварные трубы диаметром от 8 мм до 2520 мм и толщиной стенки от 1 до 25 мм и бесшовные трубы диаметром от 1 мм до 426 мм и толщиной стенки от 0,1 до 60 мм, то есть весь диапазон, который востребован мировым рынком.Трубы изготавливаются из углеродистых, нержавеющих и жаропрочных сталей, титановых и никелевых сплавов, композиционных металлов и чугуна. Продукция ТМК сертифицирована в соответствии с международными стандартами API 5L, API 5CT, API 5D, ASTM, DIN и другими. Система качества на всех заводах сертифицирована на соответствие требованиям стандартов ISO 9001 и API Spec Q1.
Клиентами ТМК являются крупные российские и зарубежные компании, такие как Газпром, Транснефть, Лукойл, ЮКОС, Сургутнефтегаз, Exxon, AGIP, Mitsui, Marubeni-Itochu, Wintershall и многие другие.
Благодаря высокому качеству продукции ТМК успешно участвует во многих крупных российских и международных проектах. Среди них нефтепровод Балтийской трубопроводной системы, газопроводы Ямал-Западная Европа, Ближняя Азия-Центр и другие.
Важнейшей составляющей деятельности холдинга является постоянная и системная работа по повышению качества продукции. С этой целью компания реализует масштабную инвестиционную программу, направленную на обновление производства, обновление производственных мощностей и ввод новых мощностей. в операции.Ежегодные инвестиции составляют более 50 млн долларов США.
В 2006 году введен в эксплуатацию стан непрерывного литья под давлением — ключевое звено инвестиционной программы ТМК. В 2008 году на Таганрогском заводе в запланированные сроки введен в эксплуатацию цельнопрокатный стан Premium Quality Finishing (PQF) мощностью 600 тыс. Тонн. Сургутнефтегазу отгружена первая партия бесшовных труб PQF. Стан PQF будет производить высококачественные бесшовные трубы с внешним диаметром от 73 до 273 мм и толщиной стенки до 25 мм. Стан был спроектирован, изготовлен и поставлен немецкой компанией SMS Meer, ведущим поставщиком трубопрокатного оборудования. Помимо увеличения доли продукции премиум-класса, применяемая на комбинате современная трехвалковая технология повысит выход продукции на 6–17%.
Читать пресс-релизы ТАГМЕТа и финансовые отчеты на TaganrogCity.Com:
8 апреля 2015 г.
25 октября 2014 г.
8 ноября 2013 г.
25 марта 2013 г.
26 ноября 2010 г.
1 октября 2008 г.
17 августа 2008 г.
14 июля 2006 г.
24 января 2006 г.
25 ноября 2005 г.
4 октября 2005 г.
29 сентября 2005 г.
24 июня 2005 г.
16 декабря 2004 г.
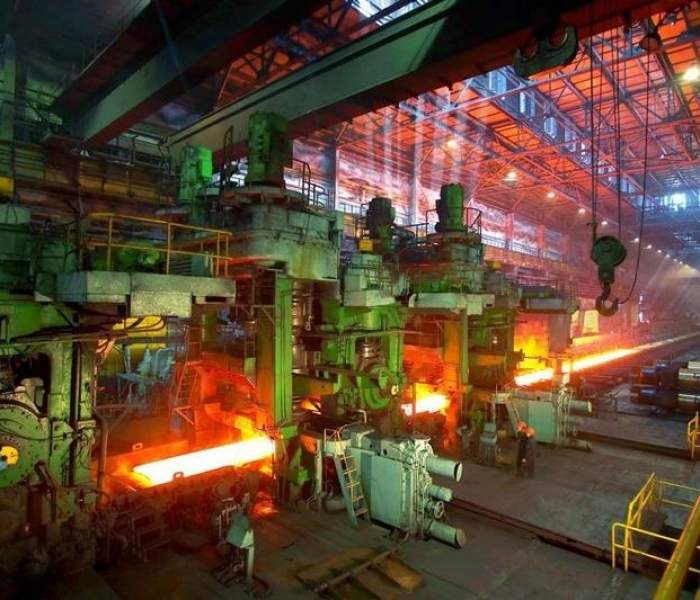