Производство магнитов (процесс производства ферритовых)
Уважаемые клиенты!
Расскажем, об еще одном интересном магнитом факте. На этот раз речь пойдет о ферритовых магнитах. Это магниты черного цвета, более привычные Вам из курса физики.
СПОСОБ ИЗГОТОВЛЕНИЯ АНИЗОТРОПНЫХ ФЕРРИТОВЫХ МАГНИТОВ
Сущность изобретения: ферритовой порошок подвергают мокрому измельчению, сушат, и затем подвергают дезагрегации до получения порошка с насыпной плотностью 0,6 -0,8 г/см3 , прессуют его в магнитном поле, после чего спекают.
ОПИСАНИЕ ИЗОБРЕТЕНИЯ
Изобретение относится к порошковой металлургии, в частности к способу изготовления постоянных магнитов из порошков магнитотвердых ферритов. Известен способ получения анизотропных магнитов, включающий мокрый помол порошков ферритов, их сушку, прессование в магнитном поле и спекание. При этом способе магнитные параметры изделий невысоки, так как при сушке мелкодисперсные частицы образуют конгломераты, вследствие чего затруднено ориентирование частиц в магнитном поле при прессовании. Также известен способ получения анизотропных ферритовых магнитов, включающий мокрое измельчение ферритовых порошков и смешение их со связующим, ориентацию полученной смеси в магнитном поле с одновременным обезвоживанием смеси до влажности 5-10 мас.%, сушку, измельчение высушенных блоков, прессование и спекание. К недостаткам последнего следует отнести высокую трудоемкость, низкую степень ориентации состоящих из большого количества частиц гранул в магнитном поле при прессовании и, как следствие, низкая степень текстуры и относительно невысокие магнитные параметры изделий.
По достигаемому результату наиболее близким аналогичным решением является способ, при котором во время подготовки порошка к прессованию обеспечивают разделение самопроизвольно образующихся при сушке и хранении конгломератов частиц, наименьшую насыпную плотность порошков. К недостаткам этого способа следует отнести невысокую точность размеров магнитов, большое время цикла прессования. Целью предлагаемого способа является повышение точности размеров получаемых магнитов, увеличение производительности способа. Поставленная цель достигается тем, что в известном способе, включающем разделение самопроизвольно образующихся при сушке и хранении конгломератов частиц, обеспечение наименьшей насыпной плотности порошков, порошок после мокрого помола и сушки подвергают дезагрегации до насыпной плотности 0,6-0,8 г/см3.
По сравнению с прототипом заявляемое техническое решение имеет следующие отличительные признаки: дезагрегация порошка производится до значения насыпной плотности 0,6-0,8 г/см3, осуществляется контроль и поддерживается стабильность значений насыпной плотности порошков после дезагрегации в указанных пределах.
Известно техническое решение, в котором также контролируют насыпную плотность порошков. Однако при этом насыпная плотность контролируется с целью определения размеров транспортирующих и запасных емкостей для порошка, высоты подъема пуансонов, пригодности различных порошков для шликерного литья и спекания свободно насыпанных порошков. В заявленном техническом решении контроль и неизменность в указанных пределах насыпной плотности вводится с целью повышения точности размеров получаемых магнитов и увеличения производительности способа. По остальным признакам других известных технических решений не выявлено.
Предлагаемое техническое решение основано на экспериментально выявленных зависимостях времени дезагрегации, длительности цикла прессования, точности получаемых размеров магнитов от значений насыпной плотности порошков.
Порошки бариевых или стронциевых магнитотвердых ферритов, имеющих после дезагрегации насыпную плотность 0,6-0,8 г/см3, обладают необходимой текучестью, хорошо ориентируются в магнитном поле и прессуются. Это позволяет сократить длительность цикла прессования, применить многогнездное прессование, получить прессовки с высокой точностью линейных размеров. Изготовленные из таких порошков магниты имеют высокие магнитные параметры и высокую точность линейных размеров.
Порошки с насыпной плотностью более 0,8 г/см3 также хорошо прессуются. Однако вследствие того, что они содержат большое количество неразделенных при дезагрегации частиц, они плохо ориентируются в магнитном поле. Получающиеся из них анизотропные магниты имеют сравнительно низкие магнитные параметры. По этой причине использовать такие порошки нецелесообразно.
Порошки с насыпной плотностью ниже 0,6 г/см3 хорошо ориентируются в магнитном поле, но обладают рядом существующих недостатков. Для достижения такой насыпной плотности в 2-3 раза увеличивается время дезагрегации. Вследствие низкой текучести, возрастает время загрузки пресс-формы, особенно для тонкостенных малогабаритных прессовок. Уменьшаются скорости рабочих ходов пресса, так как необходимо время на удаление воздуха при прессовании. При загрузке частицы образуют арки и мостики, что приводит к неконтролируемому изменению массы загружаемого порошка от цикла к циклу и от гнезда к гнезду при многоместном прессовании. Это в свою очередь приводит к разбросу значений плотности и размеров прессовок. Кроме того, при прессовании порошка с насыпной плотностью менее 0,6 г/см3 на заготовках появляются трещины, снижающие выход годных изделий.
Способ осуществляли следующим образом. В качестве исходных сырьевых материалов ученые взяли бариевый ферритовый порошок и стронциевый ферритовый порошок. Измельчение порошков проводилось в вибромельнице при соотношении массы шаров, порошка и воды 10:1:0,5, соответственно. Время помола для бариевых порошков составляло 6 ч, а для стронциевых — 10 ч. Затем порошки сушили до влажности 1-2 мас.% и подвергали дезагрегации в высокоскоростном смесителе в течение 5, 10, 20, 40, 50, 80, 120 мин. После этого проводили замеры насыпной плотности по ГОСТу «Порошки металлические. Определение насыпной плотности». Полученные таким образом порошки в 2-местной пресс-форме прессовали на прессе в магнитном поле напряженностью 720 кА/м при удельном давлении 0,85 т/см2, цилиндрические образцы диаметром 20 мм и высотой 15 мм. Время засыпки порошков в пресс-форму и скорости рабочих ходов прессы устанавливались такими, чтобы, во-первых, обеспечить полную и постоянную от цикла к циклу высоту засыпки, во-вторых, необходимую плотность прессовок и, в-третьих, отсутствие видимых трещин и сколов после спекания. Производительность операции прессования оценивали путем определения количества циклов в минуту. Затем прессовки спекались в проходной туннельной электрической печи. Для бариевого феррита максимальная температура спекания составила 1180оС, для стронциевого феррита — 1240оС. На спеченных магнитах измеряли высоту с точностью до 0,01 мм. Анализируя все данные, сделали следующие выводы:
1) из порошков насыпной плотностью более 0,8 г/см3 получаются образцы с высокой точностью размеров и хорошей производительностью, но они обладают низкими магнитными параметрами;
2) для получения бездефектных образцов из порошков с насыпной плотностью менее 0,6 г/см3 необходимо значительно увеличить цикл прессования и время дезагрегации. Однако при этом увеличение магнитных параметров не происходит. Кроме того, значительно ухудшается точность размеров спеченных магнитов;
3) порошки с насыпной плотностью в интервале 0,6-0,8 г/см3 обеспечивают как высокие магнитные параметры, так и производительность прессования. Одновременно размеры магнитов имеют высокую точность.
Следовательно, порошки бариевых и стронциевых магнитотвердых ферритов с насыпной плотностью 0,6-0,8 г/см3 позволяют увеличить производительность способа, повысить точность размеров получаемых магнитов при сохранении высоких магнитных параметров спеченных образцов.
ПРОЦЕСС ПРОИЗВОДСТВА ФЕРРИТОВЫХ МАГНИТОВ
Приоткроем завесу нашего производства, и покажем весь процесс поэтапно:
1. Подготовка сырья
2. Процесс прессования: придаем будующему магниту необходимую форму (диск, пластина, кольцо, сектор)
3. Спекание заготовок в печи при высокой температуре более 1100оС, по времени — 24, 48 и более часов
4. Шлифовка багнитных заготовок на станке
5. Промывка
6. И , наконец, сам процесс намагничивания готового изделия, а также проверка всех параметров
Обратившись, в нашу компанию, Вы можете подобрать ферритовый магнит в форме диска, кольца или пластины необходимого размера из имеющегося ассортимента. Если ваш необходим магнит другой формы или размера, мы изготовим ферритовый магнит по Вашим чертежам.
Полный ассортимент феррита можно посмотреть здесь.
Следите за новостями!
В статье взяты материалы из независимый научно-технического портала: http://www.ntpo.com/patents_electronics/electronics_10/electronics_27.shtml
Производство неодимовых магнитов. Лучшие цены в Статьи о магнитах
МЫ ПРОДАЁМ МАГНИТЫ ТОЛЬКО —
ТОЧНЫЙ РАЗМЕР
Способы оплаты
Распечатать страницу
Главная \ О Магнитах \ Производство неодимовых магнитов
« Назад Производство неодимовых магнитов. Неодимовые магниты — это класс редкоземельного материала, который используется в нескольких отраслях промышленности, как в машиностроении, в производстве компьютеров, так и на более бытовом уровне. Когда неодимовые магниты появились в продаже, этот вид магнитов заменил собой другие — ферритовые и кобальтовые. «Магазин Магнитов» — компания, которая предлагает клиентам приобрести целую партию этих магнитов в любых объемах и лучшего качества. Система заказа очень удобная, к тому же мы предлагаем вам воспользоваться комплексными консультациями, благодаря которым вы сможете определиться с верным выбором. Неодимовые магниты, свойства и особенности Свойства этого магнита превышают в десятки раз ферритный сплав, также они конкурируют с кобальтовыми магнитами. Они отличаются высокой остаточностью уровня намагниченности, поэтому их можно использовать как в сфере промышленности, так и в других сферах, где нужно использовать процесс омагничивания жидкостей. Сплавы неодимовые имеют отличный высокий потенциал эксплуатации. Показатель потери уровня намагниченности — около 2% на протяжении 10 лет, это очень мало. Такой низкий показатель является недостижимым для остальных типов магнитов. Магнит устойчив к воздействию низких температур, низкая температура не сказывается на работоспособности неодимового сплава. Неодимовые магниты, производство, его процесс Чтобы создать неодимовые магниты, используется сырье, которое расплавляется в печах и отливается в формах. После того, как слитки охлаждаются, их размалывают до тех пор, пока они не превращаться в мелкий порошок. Завершающий процесс — обработка термического типа, выравнивание, а также процесс намагничивания. В конечном итоге получается слиток с ровными краями, который внешне похож на металл. При выборе магнита неодимового, обратите внимание на то, какой марки сплав. Благодаря этой характеристике вы узнаете о том, какая максимальная энергия магнита. Чаще всего выделяют несколько моделей начиная N-32 и до N-52. Чем будет выше указанное число, тем сильнее свойства неодимового сплава. Если вы собираетесь применять магнит при высокой температуре, обратите внимание на те буквы, которые идут сразу после обозначения марки: Например: Буква М обозначает температуру Кюри, которая составляет 100 С. Более подробные данные о характеристиках представленных магнитов, а также об их основных свойствах вы сможете подробнее узнать у специалистов компании «Магазин Магнитов, для этого Вам нужно позвонить к нам. Наши менеджеры с удовольствием помогут вам выбрать подходящий вид неодимового магнита и сразу же оформят ваш заказ максимально быстро, поэтому вы получите свой товар в течение одного-двух дней. Мы уверены, что вы будете удовлетворены качеством нашего сервиса и конечно же товара. Чтобы клиентам не пришлось думать о вывозе магнитов самостоятельно, специально для вас работает служба доставки по всей России — приоритет отдаём «Почте России». Если вам все-таки удобнее вывезти самостоятельно, вы можете приехать сами и забрать заказанную партию. |
Как изготавливаются неодимовые магниты
Как изготавливаются неодимовые магниты? Неодимовые магниты изготавливаются с помощью сложного процесса, который включает в себя несколько очень высокотехнологичных металлургических методов, включая порошковую металлургию и передовую металлургию.

Для изготовления неодимовых магнитов, также известных как NdFeB, для химических символов неодима, железа и бора необходимо очень точно выполнить десятки технологических операций.
Варианты процесса используются для достижения свойств, необходимых для различных марок. Эти вариации включают различия в составе, морфологические различия (форма кристаллов) и различия в процессах.
Ниже мы рассмотрим многие основные этапы обработки.
Этапы производственного процесса неодимовых магнитов
Рассмотрим этапы обработки. Производство неодимовых магнитов зависит от передовых материалов и технологий. Вот основные этапы:
Этапы процесса:
- Открыта и добыта редкоземельная руда.
- Руда перерабатывается и очищается
- В рафинированный металл добавляются элементы для создания редкоземельного сплава
- Плавка (сырья) и разливка ленты
- Водородная декрепитация
- Струйное измельчение
- Прессование во внешнем магнитном поле
- Холодное изостатическое прессование
- Спекание
- Отжиг
- Механическая обработка и шлифовка
- Гальваническое покрытие/покрытие
- Намагничивание
- Упаковка и отгрузка
Этапы обработки неодимовых магнитов
Производство высококачественных высокотехнологичных неодимовых магнитов состоит из множества основных производственных операций, а также множества подэтапов. Каждый шаг очень важен, и каждый шаг является неотъемлемой частью очень тонкой операции.
Вот основные шаги.
- Этап №1 Добыча редкоземельной руды
Сначала обнаруживают, а затем добывают редкоземельную руду. Большинство редкоземельных рудников открыты, поэтому руда удаляется с помощью крупного оборудования после удаления любой вскрышной породы.
Фото: Карьер РЗЭ | Ecomerge.blogspot.com
- Шаг № 2 Переработка и очистка руды
Затем редкоземельная руда дробится и измельчается. Затем руда проходит процесс флотации, где она смешивается с водой и специальными реагентами для отделения редкоземельных элементов от хвостов. В зависимости от источника руды концентрат также может подвергаться электролитическому рафинированию. Редкоземельные металлы могут быть очищены и извлечены электрохимически, дистилляцией, ионным обменом или другими методами. Концентрат (очищенная руда) затем плавится. Это означает, что он нагревается до очень высоких температур (~ 1500 ° C), поэтому ценные металлы могут быть отделены от непригодных материалов в руде.Редкоземельные элементы часто встречаются с другими ценными металлами, такими как драгоценные металлы, и даже со значительными количествами неблагородных металлов, таких как медь и никель, поэтому для их разделения предпринимаются многочисленные шаги.
Извлечение редкоземельных элементов затруднено, поскольку многие из них имеют очень похожие свойства, что затрудняет их очистку. Это один из факторов стоимости; потому что методы очистки требуют использования дорогостоящих химикатов и трудоемких процессов.Например, малоизвестно, но около 20-30% неодима в неодимовых магнитах на самом деле является празеодимом. На самом деле сплав, используемый для изготовления магнитов, называется PrNd, потому что эти два элемента химически настолько похожи, что они не только слишком похожи, чтобы их можно было легко разделить, но они также настолько похожи, что это будет иметь лишь небольшую разницу в качестве материала. магнит.
- Этап №3 Легирование
В процессе легирования в сплав NdFeB вносятся небольшие добавки других металлов для улучшения и модификации микроструктуры конечного продукта, улучшения его магнитных свойств и усиления воздействия других процессы.
- Этап №4. Отливка полосы
Легированный NdFeB теперь готов к плавке и отливке полосы. Он нагревается в вакуумной печи, и поток расплавленного металла под давлением нагнетается на охлаждаемый барабан, где он быстро охлаждается со скоростью примерно 100 000 градусов в секунду. Высокая скорость охлаждения приводит к образованию очень мелких зерен металла, которые упрощают и усиливают эффект последующей обработки. Кроме того, мелкие зерна являются важной частью производства высококачественных магнитов.
Вакуумная печь для литья полос быстро затвердевает магнитный материал NdFeB с образованием очень мелких зерен
- Этап № 5 Декрепитация водородом
Несмотря на то, что зерна при литье полос очень малы, материал от литья полос выходит из разливочной машины в виде листов которые должны быть превращены в порошок, чтобы сделать магниты. Следующим шагом после этого является водородная декрепитация — процесс, который вводит водород для преднамеренного разрушения материала магнита.Металл теперь достаточно хрупок, чтобы его можно было легко разбить на более мелкие части, поэтому это называется водородным растрескиванием. При обработке большинства металлов переработчики избегают введения в них водорода.
Водородное охрупчивание может быть серьезной проблемой для многих металлов. В этом случае водород специально вводится для того, чтобы заставить материал распадаться. Тогда его легко измельчить еще мельче при последующей операции. Ветхий материал теперь готов к следующему шагу.
Декрепитация водородом — это технологический этап, используемый в производстве неодимовых магнитов для создания очень мелких зерен в материале.
Струйная мельница — очень чистый и эффективный способ измельчения металла NdFeB до порошка
- Этап № 7. Прессование во внешнем магнитном поле
Порошок хранится в атмосфере инертного газа и обрабатывается в перчаточных боксах перед отправкой на автоматический пресс. Порошок поступает в форму и сжимается между пластинами под действием сильного магнитного поля, образуя блок материала.Магнитное поле ориентирует зерна так, что магнитные домены остаются выровненными в заданном направлении на всех последующих этапах обработки.
Магнитное поле может быть ориентировано двумя способами: 1) на одной линии с блоком или 2) перпендикулярно блоку. Спеченные неодимовые магниты обычно прижимаются перпендикулярно блоку для достижения наибольшей анизотропии (самая сильная намагниченность север-юг)
Как изготавливают неодимовые магниты
Прессование в перпендикулярном магнитном поле
- Этап №8 Холодное изостатическое прессование
Блок материала помещается в мешок и погружается в холодный изостатический пресс (C ИП) под большим давлением. Это устраняет любые оставшиеся воздушные зазоры в блоке, который выходит из этого пресса немного меньше, чем он был при входе.
- Шаг #9 Спекание
Спрессованный блок вынимается из пакета и спекается. Спекание – это процесс, при котором блоки помещают в печь при очень высокой температуре чуть ниже точки плавления металла.При этой температуре >1000 o C отдельные атомы совершают большое движение, что позволяет блокам полностью развивать свои магнитные и механические свойства.
Магнитные домены сохраняют ту же ориентацию, что и до спекания. При этой температуре достигается полная плотность, и блоки сжимаются до своего окончательного размера.
Материал неодимового магнита достигает полной плотности в печи для спекания
- Этап №10 Отжиг
После спекания в металле остаются сдерживаемые напряжения от всех перемещений во время спекания, поэтому блоки снова подвергают термообработке ступенчатым образом при более низких температурах для снижения напряжений.
Блоки нагреваются до высокой температуры выдержки в течение заданного времени, а затем снижаются до более низкой температуры выдержки. По истечении времени выдержки теперь свободные от напряжения блоки медленно охлаждают до комнатной температуры.
- Этап №11 Резка, механическая обработка и шлифовка
Магниты NdFeB к настоящему времени получили большую добавленную стоимость благодаря всем предыдущим этапам.Резка, механическая обработка и шлифовка выполняются в соответствии со строгим планом контроля, а отходы сведены к минимуму.
Резка проволокой выполняется очень тонкой проволокой, чтобы свести к минимуму потери на пропил. Механическая обработка и шлифовка сведены к минимуму за счет строгого контроля на протяжении предыдущих процессов. Отходы повторно используются и перерабатываются.
Станки для резки проволоки используются для точной и экономичной резки магнитов.
- Этап №12 Обработка поверхности
Большинство неодимовых магнитов теперь проходят окончательную обработку поверхности перед отправкой с завода. Базовая обработка представляет собой гальваническое покрытие никель-медь-никель, которое защищает магнит от коррозии в большинстве типичных условий эксплуатации.
Некоторые конечные пользователи по разным причинам не указывают никакого покрытия. Другие определяют покрытия с большей защитой, чем может предложить Ni-Cu-Ni.Алюминий-цинк предлагает гораздо большую защиту, чем NiCuNi. Алюминий IVD — еще один выбор, указанный конечными пользователями. Эпоксидное покрытие является очень хорошим покрытием для интенсивных сред и рекомендуется конечными пользователями в тех случаях, когда магниты могут подвергаться воздействию соляного тумана.
BJMT наносит антикоррозионные покрытия для всех типов сред. Это линия непрерывного распыления алюминиево-цинкового покрытия.
- Этап 13. Тестирование
Тестирование и оценка магнитного материала выполняются почти на каждом этапе процесса, и ведется запись каждой точки данных. При таких интенсивных требованиях к тестированию BJMT имеет значительный запас испытательного оборудования для поддержания и улучшения качества продукции, эффективности производства и затрат.
Тщательное тестирование гарантирует, что покупателю отгружаются только высококачественные продукты
- Шаг №14 Намагничивание
Одним из последних этапов является намагничивание.Материал помещают внутрь электрической катушки, на которую подается напряжение для создания очень сильного магнитного поля в течение короткого времени. После того, как катушка обесточена, магнитное поле в магните сохраняется.
Различия в составе и обработке NdFeB
Высокотемпературные неодимовые магниты обычно требуют добавления тяжелых редкоземельных элементов (HREE), таких как диспрозий и тербий. HREE улучшают сопротивление магнита размагничиванию при высоких температурах и в присутствии противоположных магнитных полей.
Относительная редкость HREE побудила несколько ведущих компаний NdFeB разработать методы и процессы для снижения или устранения потребности в HREE в высокотемпературных магнитах NdFeB.
Зернограничная диффузия
В последние годы несколько ведущих производителей магнитов NdFeB создали высокотемпературные магниты NdFeB с более высокой коэрцитивной силой без HREE (или со значительно сниженным содержанием HREE) за счет улучшения контроля размера и формы зерна, а также за счет использования зернограничной диффузии.
Диффузия по границам зерен (GBD) — это метод выборочного введения HREE в зернограничную фазу магнита. ГБД создает высокую коэрцитивную силу при значительном снижении количества тяжелых РЗЭ, таких как диспрозий и тербий, что снижает опасения по поводу использования этих редких и дорогих тяжелых РЗЭ.
Форма и размер кристаллов
Во многих металлургических системах на свойства материала влияет форма отдельных кристаллов или зерен в металлической структуре, а также средняя форма и размер зерен по всей микроструктуре. . Жесткий контроль над процессами может привести к улучшению магнитных свойств при высоких температурах при одновременном снижении потребности в тяжелых РЗЭ.
Каждый производственный процесс должен тщательно контролироваться, чтобы убедиться, что каждый шаг выполняется с точностью для достижения качества, производительности и экономичности.
Производство магнитов NdFeB требует больших капиталовложений
Эти процессы требуют больших капиталовложений в оборудование. Например, вакуумные ленточные разливочные машины, оборудование для водородной декрепитации, оборудование для струйной мельницы, магнитные ориентирующие прессы, холодные изостатические прессы, печи для спекания и отжига требуются только для изготовления магнитных блоков. Каждый из них является основным капитальным вложением.
Очень точное оборудование для резки, механической обработки и шлифовки делает блоки магнитов нужными. Поскольку магнитный материал изготавливается с помощью процесса порошковой металлургии и других процессов, к тому времени, когда детали переходят к процессам механической обработки и шлифования, они приобретают значительную ценность.
Резка спланирована очень тщательно. Резка проволоки выполняется очень тонкой проволокой, чтобы свести к минимуму потери на пропил. При необходимости используется измельчение, но оно хорошо спланировано, чтобы свести потери материала к минимуму.
Гальваника и другие операции по нанесению покрытий требуют значительных капиталовложений для производства высококачественной продукции экономичным и экологически безопасным способом.
Неодимовые магниты используются для большего количества приложений
Неодимовые магниты питают так много устройств, что легко потерять их все. Почти каждый гибридный и электрический автомобиль зависит от неодимовых магнитов. Ветряные турбины, морские силовые установки, кондиционеры, мобильные телефоны, аудиоустройства и многие другие приложения зависят от неодимовых магнитов для достижения гладких форм-факторов, которые обеспечивают экономию во многих новых системах.
Промышленные двигатели, изготовленные с использованием магнитов NdFeB, рассчитанные на длительное время безотказной работы с эффективностью более 95%, позволяют экономить электроэнергию и сохранять природные ресурсы. Неодимовые (NdFeB) магниты создают больше возможностей в меньшем пространстве и большем количестве приложений, чем когда-либо прежде.
Магниты NdFeB обеспечивают высочайшую производительность при наименьшем объеме материала, что делает их очень привлекательным выбором для разработчиков все большего числа требовательных приложений.
Неодимовые магниты используются в наиболее динамично развивающихся областях энергетики и автомобилестроения
Цена за единицу веса – это еще не все
Простой расчет цены за кг не дает полной картины при оценке высокотехнологичного материала, такого как NdFeB. Многие выигрышные конструкции учитывают стоимость на единицу напряженности магнитного поля, что дает волновой эффект снижения стоимости системы во всей системе.
Например, если инженер разрабатывает систему на основе постоянных магнитов, которая требует высокой мощности в сочетании с ограничениями по размеру или пространству, существует большая вероятность того, что в системе будут использоваться неодимовые магниты. Неодимовые магниты предлагают почти в 20 раз больше магнитного поля на единицу объема, чем ферритовые магниты, и они делают это почти на 1/10 веса, поэтому конструкция, в которой используются магниты NdFeB, потенциально создаст волновой эффект, который уменьшит размер магнита. вся система.
Конечно, у каждого типа магнита есть свое место, и есть много удачных дизайнов, в которых используются разные типы магнитов.
Вы когда-нибудь хотели посетить завод по производству неодима?
Щелкните ниже, чтобы просмотреть полный тур по заводу BJMT.
Производство магнитов | Magnet-Lexicon / Глоссарий
- Материал магнита
- Магнитная энергия
В этом посте вы узнаете все шаги, необходимые для изготовления магнитов . Это показывает, что именно для этого необходимо и почему производство должно происходить на магнитной фабрике. Самостоятельно сделать магниты в домашних условиях невозможно, но создать магнитные эффекты вполне можно. Например, когда вы создаете магнитное поле с помощью железного гвоздя и железного магнита.
Производство магнитов может осуществляться различными способами. Порошковая металлургия очень распространена.
Так работает производство магнита
Производителям магнитов необходимы определенные сырье и техническое оборудование в виде машин.
Знаете ли вы это? Упомянутое сырье также называется магнитными материалами . Благодаря своим магнитным свойствам их можно использовать для изготовления магнитов. Это, например, железо с алюминием, а также кобальт и никель. Железо с неодимом и бором подходят для большей силы сцепления. Магнитные материалы делятся на две категории. 1. Магнитно-мягкий : легко намагничивается. 2. Магнитно-твердый : Постоянные магниты.
Этапы процесса изготовления магнита
1. Сначала необходимо изменить форму материалов.
Так работает намагничивание магнита
После первого шага магнит почти готов стать магнитом, но у него еще нет сцепления. Для этого его нужно предварительно поместить под большой магнит так, чтобы все магнитные частицы ориентировались в одном направлении = магнетизм .
Краткий экскурс в физику объясняет, как именно работает магнетизм:
✓ Каждое вещество состоит из атома, который, в свою очередь, имеет атомное ядро, вокруг которого вращаются электроны.
Так производится неодимовый магнит
Как и производство обычного магнита, процесс производства неодимового магнита состоит из нескольких этапов:
1. Сырье плавится в специальной печи. 2. Расплавленную смесь заливают в форму для затвердевания. 3. Закаленный металл измельчают в порошок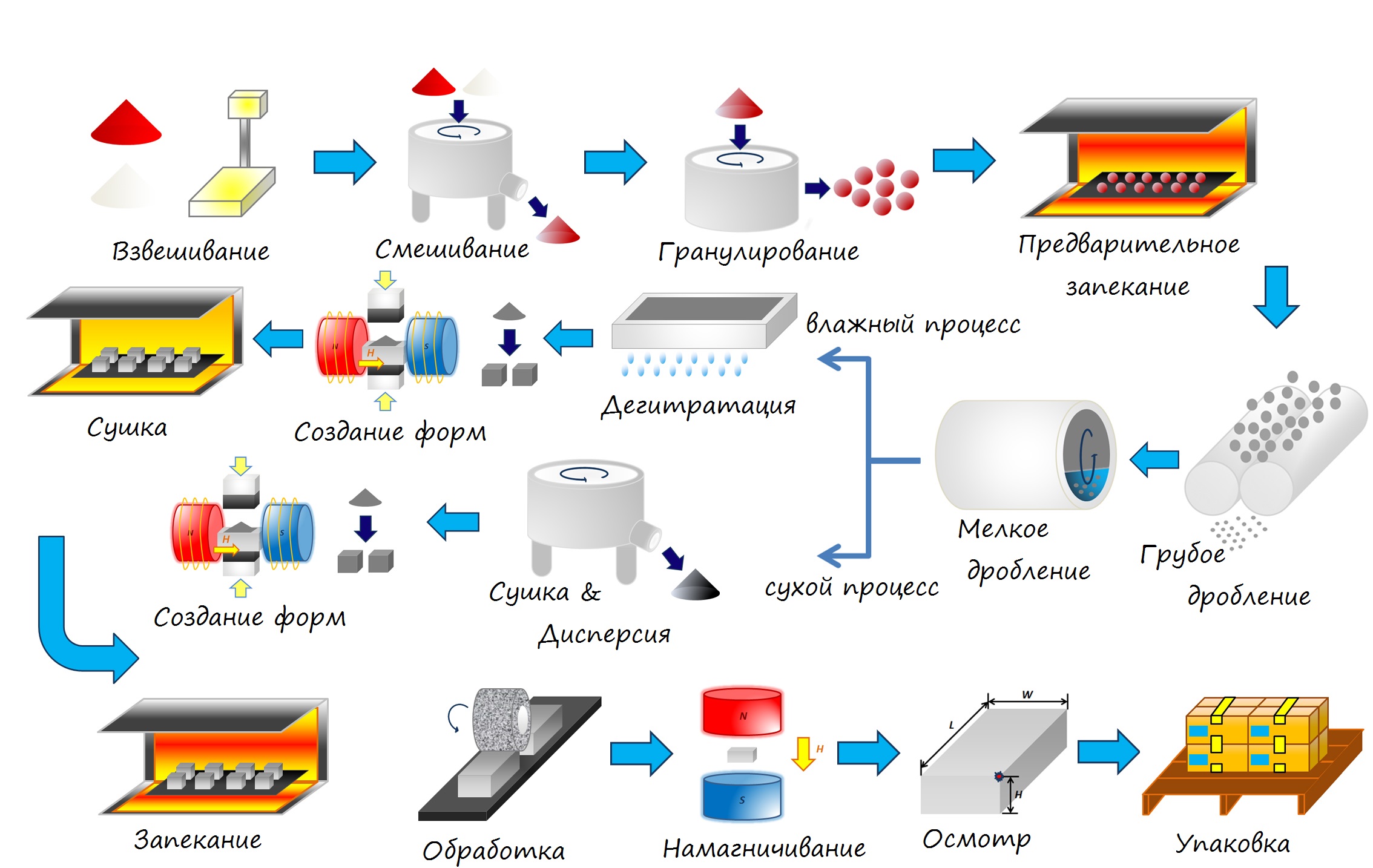